The Swiss, well-known for their tunnel constructions, have enhanced their reputation with the recent Gotthard Tunnel breakthrough which has created the world's longest tunnel. And in Bern, a roundabout is being re-positioned almost 10m under the ground, which will transform a somewhat dismal road intersection into an attractive gateway to the country's capital.
PERI provided a comprehensive formwork solution for the realisation of the massive beams, reinforced concrete slab along with the conically-sh
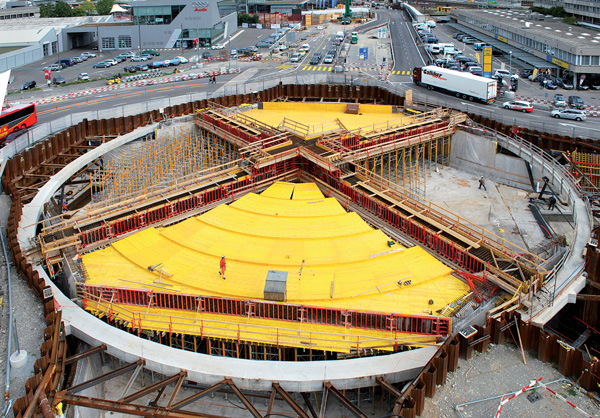
In Bern, Switzerland, PERI provided a comprehensive formwork solution to help construct an underground roundabout
The Swiss, well-known for their tunnel constructions, have enhanced their reputation with the recent Gotthard Tunnel breakthrough which has created the world's longest tunnel.
And in Bern, a roundabout is being re-positioned almost 10m under the ground, which will transform a somewhat dismal road intersection into an attractive gateway to the country's capital.
298 PERI provided a comprehensive formwork solution for the realisation of the massive beams, reinforced concrete slab along with the conically-shaped roundabout walls, which are to be formed in architectural concrete.
Over 65,000 vehicles pass through the junction on a daily basis, and being located near the motorway, traffic is reduced to a snail's pace, resulting in long waiting times for drivers; a negative impact on the environment and badly affecting the public transport system.
The Wankdorfplatz is being transformed into a two-storey structure, meaning a project from an ideas competition is fast becoming a reality.
From 2012 onwards, the underground roundabout with a 50m diameter will accelerate the flow of traffic and create space for pedestrians and cyclists above ground as well as greatly improving bus and tram connections.
For the pre-stressed beams and reinforced concrete slab as well as for the conically-shaped walls in architectural concrete quality, PERI's Swiss engineers developed various formwork solutions using mainly rentable system equipment which matched the requirements of the contractor.
The customised wall formwork elements for the curved external walls of the roundabout area were prefabricated by PERI on the basis of the VARIO GT 24 girder wall formwork system. For this project, the radii range from 30m to 45m with a wall inclination of 10:1.
The construction of the 1.8m wide, pre-stressed beams with varying heights of between 1.15m and 2.7m took place on a combined load-bearing and working level which angled upwards to the centre of the roundabout. This was formed using the flexible MULTIFLEX girder slab formwork system with the help of GT 24 lattice girders as very high load-bearing twin main beams and VT 20 cross beams.
The MULTIPROP system served as support with towers comprising MRK frames connected to MULTIPROP aluminium slab props.
"Thanks to the free-running collar and the integrated measuring tape, these could be easily adjusted to suit the varying heights of between 5m and 6m. TRIO panel formwork also found use as the side formwork. By means of the double thickness formlining excellent concrete surfaces could be achieved," says PERI.
"Following this, four slab segments were to be constructed and connected to the crosswise-arranged beams. The extremely tight construction schedule meant that sufficient formwork materials were to be available on site for the complete slab area of some 1,400m². The up-to 1.2m thick reinforced concrete slab runs in a truncated cone-shaped manner with an approximate 3% gradient on the upper side. In addition, the underside of the slab features five height offsets and a number of different inclinations. In close cooperation with the contractor, PERI created a formwork concept for this which allowed safe and accurate positioning of the required additional special elements." MULTIPROP towers were again used as shoring. The MULTIFLEX girder slab formwork system formed a level intermediate platform which covered the entire area. In contrast to the beam solution with VT 20 cross girders, the use of GT 24 girders as radially-positioned cross beams proved to be the more cost-effective variant in order to reliably transfer the loads via GT 24 double main beams and MULTIPROP props. From this working level, the construction crew was able to quickly install the pre-fabricated special elements which had been put together in the PERI assembly hall.
Due to limited on site storage, PERI Switzerland delivered the formwork elements on a just-in-time basis.
And in Bern, a roundabout is being re-positioned almost 10m under the ground, which will transform a somewhat dismal road intersection into an attractive gateway to the country's capital.
Over 65,000 vehicles pass through the junction on a daily basis, and being located near the motorway, traffic is reduced to a snail's pace, resulting in long waiting times for drivers; a negative impact on the environment and badly affecting the public transport system.
The Wankdorfplatz is being transformed into a two-storey structure, meaning a project from an ideas competition is fast becoming a reality.
From 2012 onwards, the underground roundabout with a 50m diameter will accelerate the flow of traffic and create space for pedestrians and cyclists above ground as well as greatly improving bus and tram connections.
For the pre-stressed beams and reinforced concrete slab as well as for the conically-shaped walls in architectural concrete quality, PERI's Swiss engineers developed various formwork solutions using mainly rentable system equipment which matched the requirements of the contractor.
The customised wall formwork elements for the curved external walls of the roundabout area were prefabricated by PERI on the basis of the VARIO GT 24 girder wall formwork system. For this project, the radii range from 30m to 45m with a wall inclination of 10:1.
The construction of the 1.8m wide, pre-stressed beams with varying heights of between 1.15m and 2.7m took place on a combined load-bearing and working level which angled upwards to the centre of the roundabout. This was formed using the flexible MULTIFLEX girder slab formwork system with the help of GT 24 lattice girders as very high load-bearing twin main beams and VT 20 cross beams.
The MULTIPROP system served as support with towers comprising MRK frames connected to MULTIPROP aluminium slab props.
"Thanks to the free-running collar and the integrated measuring tape, these could be easily adjusted to suit the varying heights of between 5m and 6m. TRIO panel formwork also found use as the side formwork. By means of the double thickness formlining excellent concrete surfaces could be achieved," says PERI.
"Following this, four slab segments were to be constructed and connected to the crosswise-arranged beams. The extremely tight construction schedule meant that sufficient formwork materials were to be available on site for the complete slab area of some 1,400m². The up-to 1.2m thick reinforced concrete slab runs in a truncated cone-shaped manner with an approximate 3% gradient on the upper side. In addition, the underside of the slab features five height offsets and a number of different inclinations. In close cooperation with the contractor, PERI created a formwork concept for this which allowed safe and accurate positioning of the required additional special elements." MULTIPROP towers were again used as shoring. The MULTIFLEX girder slab formwork system formed a level intermediate platform which covered the entire area. In contrast to the beam solution with VT 20 cross girders, the use of GT 24 girders as radially-positioned cross beams proved to be the more cost-effective variant in order to reliably transfer the loads via GT 24 double main beams and MULTIPROP props. From this working level, the construction crew was able to quickly install the pre-fabricated special elements which had been put together in the PERI assembly hall.
Due to limited on site storage, PERI Switzerland delivered the formwork elements on a just-in-time basis.