A team of Greek and German PERI engineers have developed a comprehensive formwork and scaffolding solution for the T4 bridge on the A7 motorway in Greece. The 160km long A7 connects Kalamata in the south to Corinth in the northwest of the Peloponnese peninsula. On one stretch of the motorway a 390m long arched bridge – known as T4 – is being used to close the gap between Paradisia and Tsakona. Set for completion in early 2014, two-thirds of the 22m wide bridge superstructure will be suspended on a steel arc
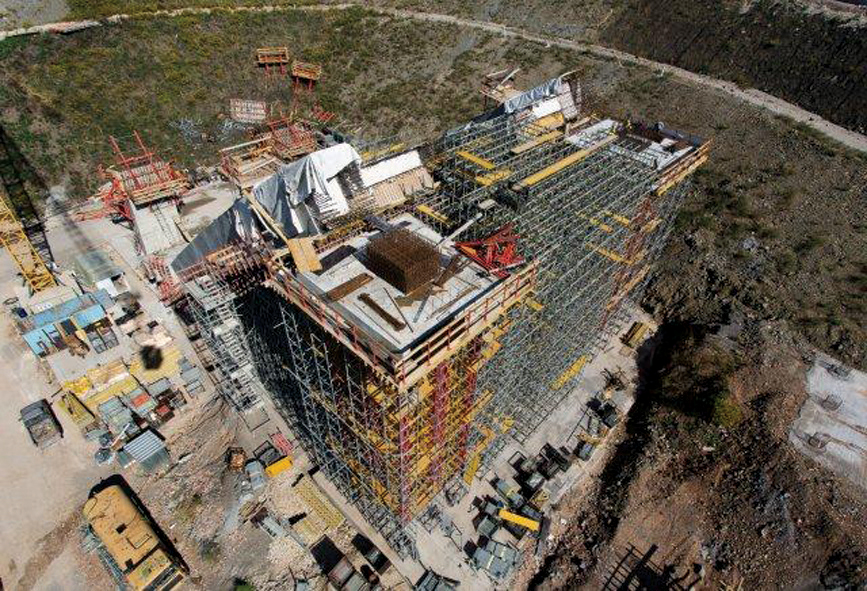
The VARIOKIT heavy-duty shoring towers being used on the T4 bridge on the A7 motorway in Greece are transferring a combined 2,400tonnes load
A team of Greek and German 298 PERI engineers have developed a comprehensive formwork and scaffolding solution for the T4 bridge on the A7 motorway in Greece.
The 160km long A7 connects Kalamata in the south to Corinth in the northwest of the Peloponnese peninsula. On one stretch of the motorway a 390m long arched bridge – known as T4 – is being used to close the gap between Paradisia and Tsakona. Set for completion in early 2014, two-thirds of the 22m wide bridge superstructure will be suspended on a steel arch and realised using the steel composite construction method. For the northern bridge section, a pre-stressed concrete superstructure variant was selected which features a twin-cell hollow box cross-section.
The supporting element of the motorway bridge is a huge, almost 30m high inclined twin-pillar pier with an asymmetric V-shape. This serves as an intermediate support for the in-situ concreted carriageway. It also serves as a support and starter section for the steel arch. Engineers from PERI and Greek colleagues devised a cost-effective plan for constructing the pier structure, the reinforced concrete superstructure and the temporary support for the bridge during the entire building project
The chosen two modular construction systems combine with each other to transfer the high loads safely into the ground. With help of the PERI UP Rosett Flex modular scaffold system, forming a spatial load-bearing structure for the piers and superstructure formwork, a gradual increasing up to the total support height of over 20m was achieved to the rear and upwards respectively. By means of 25, 50 and 75cm long ledgers, the 150cm basic grid is said by PERI to have been adapted to suit the geometric and static requirements extremely flexibly. This allowed the polygonal 32° to 36° shallow pitched inclined piers on both sides of the bridge to be constructed in eight segments, each 4.5m long.
In addition to the PERI UP scaffold construction being used, the VARIOKIT engineering construction kit, in particular, is said to offer standardised system solutions for tunnel, bridge and civil engineering projects. Thus, trusses consisting of rentable standard elements support the obliquely-positioned VARIO GT 24 girder formwork and transfer the formwork and concreting loads of the inclined piers safely into the scaffolding.
The VARIOKIT modular construction system also forms the basis for the heavy-duty shoring. In the connecting area between the cast-in-place bridge and steel arch, two 17m high, 42-leg VARIOKIT heavy-duty shoring towers are used to accommodate the high loads – throughout the entire construction period until the inherent load-bearing capacity is reached. Each of the two towers has to carry loads of 1,200tonnes and, due to the long utilisation time, has to cater for high earthquake-induced as well as horizontal loads. Here, PERI engineers combined four standard towers, each with a 2m by 2m axis dimension, by means of several bundled 37.5cm additional frames (number depended on the load concentration) to form two power packages. Only rentable system components and construction-compliant, type-tested connection means were said by PERI to be used for this.
The 160km long A7 connects Kalamata in the south to Corinth in the northwest of the Peloponnese peninsula. On one stretch of the motorway a 390m long arched bridge – known as T4 – is being used to close the gap between Paradisia and Tsakona. Set for completion in early 2014, two-thirds of the 22m wide bridge superstructure will be suspended on a steel arch and realised using the steel composite construction method. For the northern bridge section, a pre-stressed concrete superstructure variant was selected which features a twin-cell hollow box cross-section.
The supporting element of the motorway bridge is a huge, almost 30m high inclined twin-pillar pier with an asymmetric V-shape. This serves as an intermediate support for the in-situ concreted carriageway. It also serves as a support and starter section for the steel arch. Engineers from PERI and Greek colleagues devised a cost-effective plan for constructing the pier structure, the reinforced concrete superstructure and the temporary support for the bridge during the entire building project
The chosen two modular construction systems combine with each other to transfer the high loads safely into the ground. With help of the PERI UP Rosett Flex modular scaffold system, forming a spatial load-bearing structure for the piers and superstructure formwork, a gradual increasing up to the total support height of over 20m was achieved to the rear and upwards respectively. By means of 25, 50 and 75cm long ledgers, the 150cm basic grid is said by PERI to have been adapted to suit the geometric and static requirements extremely flexibly. This allowed the polygonal 32° to 36° shallow pitched inclined piers on both sides of the bridge to be constructed in eight segments, each 4.5m long.
In addition to the PERI UP scaffold construction being used, the VARIOKIT engineering construction kit, in particular, is said to offer standardised system solutions for tunnel, bridge and civil engineering projects. Thus, trusses consisting of rentable standard elements support the obliquely-positioned VARIO GT 24 girder formwork and transfer the formwork and concreting loads of the inclined piers safely into the scaffolding.
The VARIOKIT modular construction system also forms the basis for the heavy-duty shoring. In the connecting area between the cast-in-place bridge and steel arch, two 17m high, 42-leg VARIOKIT heavy-duty shoring towers are used to accommodate the high loads – throughout the entire construction period until the inherent load-bearing capacity is reached. Each of the two towers has to carry loads of 1,200tonnes and, due to the long utilisation time, has to cater for high earthquake-induced as well as horizontal loads. Here, PERI engineers combined four standard towers, each with a 2m by 2m axis dimension, by means of several bundled 37.5cm additional frames (number depended on the load concentration) to form two power packages. Only rentable system components and construction-compliant, type-tested connection means were said by PERI to be used for this.