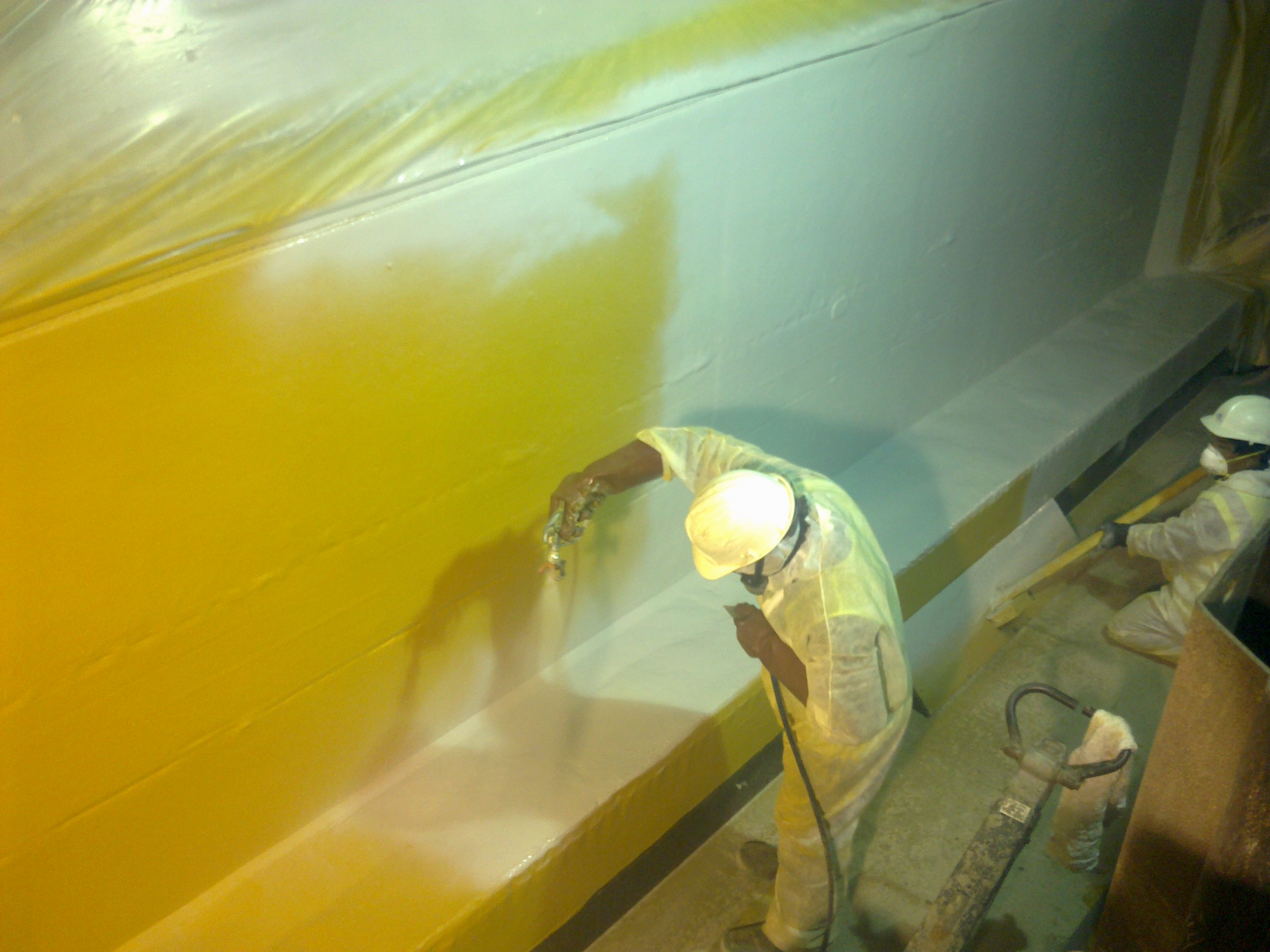
The construction of the tunnel is a major project as it forms part of a new US$30 billion integrated transportation system in Qatar. The new
The tunnel is unusual in that it is designed to carry both road traffic and light rail. To ensure that it remains watertight,
The overall Lusail City Development, located 15km north of Doha, covers a 38km2 site, which includes 25,000 residential units, housing 175,000 people, all of whom will benefit from the Lusail Tunnel project. The development is set to generate significant economic diversification as it is set to strengthen Qatar’s tourism sector.
However, the construction of this new underground infrastructure faced challenging ground conditions and fast track construction programmes due to an aggressive and high water table.
Following a number of projects where un-bonded waterproofing systems had leaked on other Lusail sites, the client LREDC was focused on pushing the boundaries and performance of waterproofing to set new standards on their projects.
Past tunnel projects within
To meet tight deadlines and the challenging onsite conditions, speed and ease of application were key for the project. The fact that Integritank can be sprayed to verticals and up to 60m from the mixing head meant that no scaffolding was required when applying to the tunnel walls, greatly reducing the time required for the application and removing an unnecessary cost.
In addition, the membranes' puncture resistance and durability meant no additional protection boards or screeds were required, further saving time and money.
Coordination between the designers, supervision consultants and authorised contractor Intertectra Qatar, as well as Stirling Lloyd’s technical input and onsite technical presence also ensured quality assurance.
Adhesion pull-off tests confirmed the strong bond achieved by the Integritank system, removing the threat of numerous leaks through water tracking. Watertightness and puncture resistance testing before backfilling also served to further reassure all parties involved of the effectiveness of the system. The same tests conducted after backfilling confirmed that the system had performed as expected and fulfilled its potential.
Stirling Lloyd claims that due to the challenging ground conditions and fast track construction programme, the fact that the Integritank material could be applied speedily to provide a fully bonded, seamless waterproofing system was crucial to the success of the project.
Forming part of a $30bn integrated transportation system, the