Warsaw’s General Stefan Rowecki Bridge, or the Grota Bridge, is the second largest in the Polish capital and, as part of the Trasa Toruska expressway, it is the busiest. The structure, which opened in 1981, handles 150,000 cars daily, so repairs were always going to be tricky if minimal disruption to traffic was to occur. The steel orthotropic deck consists of two structurally independent parts – each with four traffic lanes. This meant that pedestrians and cyclists were restricted to two very narrow track
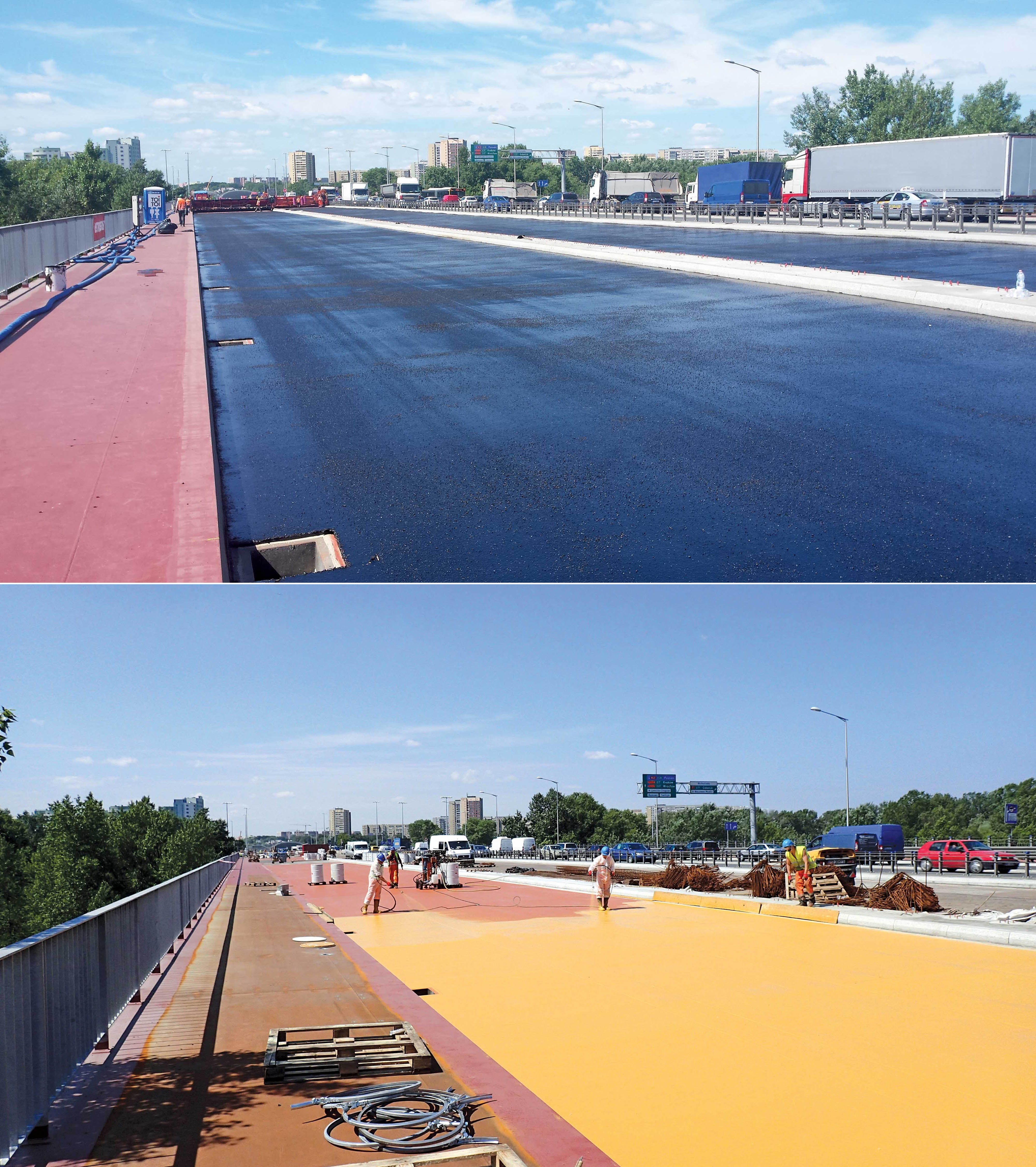
Colour contract made quality inspections easier
Warsaw’s General Stefan Rowecki Bridge, or the Grota Bridge, is the second largest in the Polish capital and, as part of the Trasa Toruska expressway, it is the busiest
The structure, which opened in 1981, handles 150,000 cars daily, so repairs were always going to be tricky if minimal disruption to traffic was to occur. The steel orthotropic deck consists of two structurally independent parts – each with four traffic lanes. This meant that pedestrians and cyclists were restricted to two very narrow tracks, each separated from the road by traffic barriers, which made the bridge inaccessible to many people.
As a result, repair work to the bridge included widening to incorporate an extra two lanes in each direction for through-traffic, three lanes for local traffic and separate cycle and pedestrian paths.
Extreme weather conditions dictated that a high level of protection was needed. It was also important to ensure minimum maintenance in the future. Also, part of the bridge had to remain open during the work, to minimise traffic disruption.
Contractor B7 did reconstruction work on the 645m long x 40m wide bridge, while ZBM Inwestor Zastpczy was the lead engineering firm. They found that, once exposed, the deck had many irregularities including protrusions from the steel mesh.
After trialling several waterproofing solutions from different suppliers on the uneven deck profile, the contractors selected2314 Stirling Lloyd’s Eliminator system, said Ned Birley, export general manager at Stirling Lloyd Polychem.
Stirling Lloyd’s authorised contractor, DWD Service prepared the deck and applied the waterproofing coat in phases based around reconstruction work.
The first phase was applying the Eliminator system to the pedestrian areas in July 2014. The second phase – consisting of waterproofing the main and new deck – was completed between April and June this year.
For both phases, the deck was prepared by shot-blasting metallic grit, followed by an independent assessment of the work that included measurement of the surface profile, dust assessment and ionic contamination. This was essential to ensure a strong bond between the substrate and the waterproofing, vital to the long-term performance of any membrane.
Adhesion pull-off tests confirmed a bond of between 3MPa and 4 MPa, more than the specified 2 MPa.
The Eliminator system comprised an initial anti-corrosive primer, ZED S94, to protect the newly exposed steel deck and enhance the bond between the deck and membrane. Once this had dried, the Eliminator system was sprayed on in two coats of contrasting colour – aiding on-site quality control and helping to ensure complete waterproofing integrity.
A final Tack Coat No. 2 was then applied. The thin film ‘hot melt’ adhesive ensures a strong bond between the membrane and surface. This adhesion between the deck, Eliminator and surfacing enables all elements to act as a composite, particularly important on a busy orthotropic steel deck. In turn, this helps to extend the life of both the surfacing and the structure. DWD was able to apply 1000m2 of the full bridge deck waterproofing system per day and which dried in less than an hour.
“Service and application conditions for the waterproofing were also extreme,” said Marcin Szwed, technical manager at Stirling Lloyd Polychem.
“Due to the phased nature of the work, the waterproofing system was applied and exposed to hot and cold weather conditions, with the deck temperature reaching up to 70°C at its peak. Using a system that can be applied in a wide range of temperatures and climatic conditions means that waterproofing installation can be carried out throughout the year, an essential feature for a large, phased project.”
Stirling Lloyd recently announced that Eliminator has gained European Technical Assessment (ETA) certification from the European Organisation for Technical Approvals (EOTA) through the British Board of Agrément (BBA). The ETA is based on the testing requirements in the European Technical Approval Guideline (ETAG) 033. Eliminator is the first UK manufactured system to achieve this level of accreditation.
The structure, which opened in 1981, handles 150,000 cars daily, so repairs were always going to be tricky if minimal disruption to traffic was to occur. The steel orthotropic deck consists of two structurally independent parts – each with four traffic lanes. This meant that pedestrians and cyclists were restricted to two very narrow tracks, each separated from the road by traffic barriers, which made the bridge inaccessible to many people.
As a result, repair work to the bridge included widening to incorporate an extra two lanes in each direction for through-traffic, three lanes for local traffic and separate cycle and pedestrian paths.
Extreme weather conditions dictated that a high level of protection was needed. It was also important to ensure minimum maintenance in the future. Also, part of the bridge had to remain open during the work, to minimise traffic disruption.
Contractor B7 did reconstruction work on the 645m long x 40m wide bridge, while ZBM Inwestor Zastpczy was the lead engineering firm. They found that, once exposed, the deck had many irregularities including protrusions from the steel mesh.
After trialling several waterproofing solutions from different suppliers on the uneven deck profile, the contractors selected
Stirling Lloyd’s authorised contractor, DWD Service prepared the deck and applied the waterproofing coat in phases based around reconstruction work.
The first phase was applying the Eliminator system to the pedestrian areas in July 2014. The second phase – consisting of waterproofing the main and new deck – was completed between April and June this year.
For both phases, the deck was prepared by shot-blasting metallic grit, followed by an independent assessment of the work that included measurement of the surface profile, dust assessment and ionic contamination. This was essential to ensure a strong bond between the substrate and the waterproofing, vital to the long-term performance of any membrane.
Adhesion pull-off tests confirmed a bond of between 3MPa and 4 MPa, more than the specified 2 MPa.
The Eliminator system comprised an initial anti-corrosive primer, ZED S94, to protect the newly exposed steel deck and enhance the bond between the deck and membrane. Once this had dried, the Eliminator system was sprayed on in two coats of contrasting colour – aiding on-site quality control and helping to ensure complete waterproofing integrity.
A final Tack Coat No. 2 was then applied. The thin film ‘hot melt’ adhesive ensures a strong bond between the membrane and surface. This adhesion between the deck, Eliminator and surfacing enables all elements to act as a composite, particularly important on a busy orthotropic steel deck. In turn, this helps to extend the life of both the surfacing and the structure. DWD was able to apply 1000m2 of the full bridge deck waterproofing system per day and which dried in less than an hour.
“Service and application conditions for the waterproofing were also extreme,” said Marcin Szwed, technical manager at Stirling Lloyd Polychem.
“Due to the phased nature of the work, the waterproofing system was applied and exposed to hot and cold weather conditions, with the deck temperature reaching up to 70°C at its peak. Using a system that can be applied in a wide range of temperatures and climatic conditions means that waterproofing installation can be carried out throughout the year, an essential feature for a large, phased project.”
Stirling Lloyd recently announced that Eliminator has gained European Technical Assessment (ETA) certification from the European Organisation for Technical Approvals (EOTA) through the British Board of Agrément (BBA). The ETA is based on the testing requirements in the European Technical Approval Guideline (ETAG) 033. Eliminator is the first UK manufactured system to achieve this level of accreditation.