Upgrading a key route through Florida – novel construction techniques are helping widen a road in difficult geological conditions – Lucio Garofalo reports. A major road widening project underway in Florida is due for completion soon. The work will improve an important section of road, reducing congestion at peak period and cutting travel times for drivers. The US 331/SR83 highway runs for some 79km and provides an important link in Florida’s Panhandle area, as it connects with Route 98.
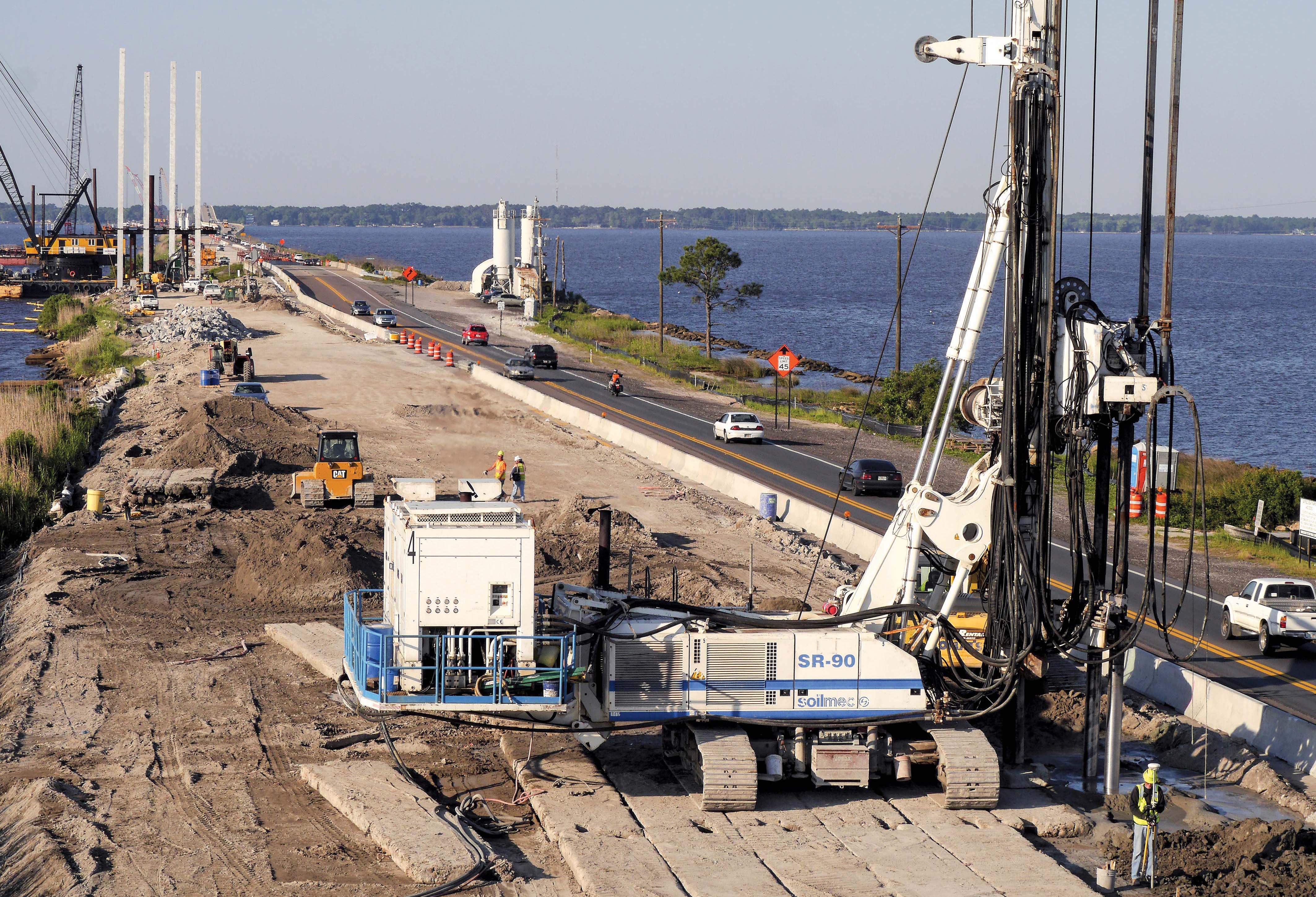
The causeway was originally constructed in the 1930s
Upgrading a key route through Florida – novel construction techniques are helping widen a road in difficult geological conditions – Lucio Garofalo reports
A major road widening project underway in Florida is due for completion soon. The work will improve an important section of road, reducing congestion at peak period and cutting travel times for drivers. The US 331/SR83 highway runs for some 79km and provides an important link in Florida’s Panhandle area, as it connects with Route 98.
Route 98 crosses a highly populated area noted as a tourist destination, whereas to the north it joins up with I-10, a highway that connects the Atlantic to the Pacific, the most southerly of the several coast-to-coast routes across the US. A key section of the US 331/SR83 route that needs to be improved is the 6.4km stretch crossing the Choctawhatchee Bay. The Choctawhatchee Bay extends for around 65km, covering an area of 334km2 and forms part of the Emerald Coast region, which is located on the Florida Panhandle in the north-western part of the state. This road is critical, especially for local transport, because it is one of the main road links to the Emerald Coast. However, it has to carry heavy traffic volumes of both commercial and private vehicles at present and congestion can be severe at times, resulting in delays for drivers. The route was first opened to drivers in the 1950s and vehicle numbers and distances driven have risen enormously since then, so the road is understandably having to cope with
traffic volumes that far exceed its capacity at peak periods.
US 331, which features only two lanes for the 6.4km stretch crossing the Choctawhatchee Bay, also has an important function as an emergency route. In case of evacuation due to a hurricane alert, it is the only major escape route by road from the Santa Rosa Beach area to points north.
The area is densely populated and especially during the high season when tourists or those with second homes in the area tend to be in residence. However, this is when there is a risk of hurricanes and storms and as a result, when the road is likely to have to cope with huge numbers of vehicles leaving the area in a hurry. As a result, the2697 Florida Department of Transportation included US 331/SR 83 on the priority list, and for this specific project it applied for and received financial support from the federal government in Washington through the Tiger II program (Transport Investing Generating Economy Recovery).
The upgrade project called for two new lanes to be added to the current 6.4km section comprising the causeway and bridge. The work has also included a new bridge to the east of the 3.7km-long Clyde B Wells Bridge. The widened four lane causeway will carry traffic to and from the bridges, and from both south and north sides. The road widening project also includes that ground be prepared for a park and recreation area at the very end of the embankment on the south side. When the construction work is completed, the new bridge and widened causeway will be used to handle the traffic driving northwards, while the existing causeway and bridge will carry the traffic heading south.
The US$118.5 million design-build project was won by a joint venture team comprising2296 Skanska and 2693 Parsons Brinckerhoff. The two partners are directly overseeing construction of the new bridge as well as the four lanes of the causeway. The partners are also carrying out all the temporary works to ensure that traffic flow remains steady during the construction phases.
The project to widen this 6.4km stretch is not without its challenges however. Because the water table is high, the ground conditions are difficult and require extensive preparation to ensure the roadway can be constructed properly. For this portion of the project, a specialist firm was brought in to handle the work by the joint venture partners. Italian company Treviicos, through a subsidiary, Treviicos South (TIS), is handling this important link in the chain and carrying out the necessary road foundation improvement work for the upgraded road connection.
Treviicos was subcontracted to handle the ground stabilisation work for the foundations below the embankments. The less than ideal geological conditions meant that this crucial aspect of the project had to be carried out by a specialised ground engineering contractor with experience of this type of work. Treviicos was selected due to its extensive experience from working with all types of foundations in loose soil.
Over the years, the causeway embankments had shown clear signs of settlement as a result of insufficient bearing capacity. The embankments were suffering from the combined effect of increased traffic volumes as well as the poor quality of fill used at the time of the original construction in the late 1930s, and before the opening of the current US 331 in 1953. Construction engineering has improved since that time, although it is a testament to the original work that the causeway embankments have lasted so long.
The bearing capacity of the two causeways leading to the bridge from the north and south had been provided by a 13.7m thickness of consolidated sands, silty sands and clayey sands that had only been lightly loaded. This arrangement offered a limited bearing capacity given that differential settlements visible on the surface had long been evident. To verify if there were deeper bearing layers susceptible to high settlement potential, extensive bore samples were taken down to a depth of 61m, using dynamic penetration (SPT) tests that were carried out in the south and central embankments. The tests revealed that at a depth of approximately 12m, there were very loose to dense clean sands within layers of silty and clayey sands.
However no limestone layer was hit until 45.7m down, although at depths of 45.7-61m, very dense sandy layers were encountered leading to "refusal" SPT-N values. In the upper layers the surveys indicated weak clays and silt-sandy layers. A number of further surveys were carried out as precautionary measures in the external (eastern) part of the central embankment and these yielded similar results, demonstrating that no well-defined bearing layer existed. This geological situation led engineers at Skanska and Parsons Brinkerhoff and Treviicos to utilise a solution that would guarantee the bearing capacity and durability required by the principal, also in the event of a destructive hurricane occurring once every 100 years.
The solution was to create columns using the shallow mixing method (SMM) and deep mixing method (DMM) techniques. Both of these methods were carried out by Treviicos which used its TreviTurboMix system. This novel type of soil mixing has been developed jointly by Trevi and2959 Soilmec, the manufacturer of piling rigs which is also a part of the 978 Trevi Group.
This method is said to allow fast and cost-effective construction of columns that can also comply with strict quality standards. The system can be applied to a wide range of soil types, from cohesive with a soft consistency to loose and cohesionless with a medium consistency. TreviTurboMix technology includes a tool that combines the jet effect at a high kinetic energy, with mechanical mixing due to the action of the blades. These are angled to achieve maximum effectiveness. This technology is considered a wet system as the fluid grout type binder is injected through outlets in the blades.
Injection takes place only when the tool is in its down-stroke phase, whereas mixing is carried out both during the down-stroke and up-stroke. One of the key advantages of the TreviTurboMix method according to the firm is that the geometric characteristics of the columns do not depend on soil characteristics as with traditional mixing. Instead geometric characteristics of the columns remain constant for the whole length, which is said to provide a high quality solution as well as durability. With the TreviTurboMix system the stabilising agent is inserted into the ground during drilling in the form of a stable mix of water and cement to which additives can be included should this be required for the mix.
The technology has been well-proven in a number of projects, both in the US and elsewhere, which was why Treviicos was confident that the system would suit the tricky conditions in Florida. In the US TreviTurboMix was used to reinforce the LPV 111 levee in New Orleans, the largest project of this kind ever undertaken in the US, and among the most important ever performed in the world. And as in Florida, the ground conditions around New Orleans are poor while the water table is high, showing just how suitable the TreviTurboMix method would be for the US 331 highway project.
After examining the SPT results, engineers came to a solution based on a soil mixing design that would deliver the necessary bearing capacity. This involved constructing no less than 1,500 double columns, each with a length of 13.7m so as to reach the bearing layer. The design also called for the construction of a further 8,400 double columns each with a length of 3.04m and arranged in a tight mesh so as to provide a supporting platform covering around 95% of the causeway surface.
Using this technique delivered a dual benefit, providing the advantages of a deep foundation as well as a shallow foundation. The shallow foundation is important as this acts as a support for the roadway and ensures that the bearing capacity of the ground is sufficient to support the static and dynamic loads generated by vehicle traffic. In terms of ground stabilisation meanwhile, this system allows the longer and deeper columns (DMM), with a compressive strength of 1034.2KNm², to transfer the loads of the platform columns (SSM) towards the deeper layers, which have a greater bearing capacity. This is achievable because the columns of the platform (SSM) have a compressive strength of 517.1KNm². This system also makes the more superficial layers resistant to erosion, which also helps to ensure long-term durability in the conditions.
The specifications for settlement tolerances were stringent so as to ensure long-term stability. These allowed for a maximum of 50mm of settlement for every 300m. To monitor the degree of settlement two different methods were used, one preliminary in the early stage of the project, and one permanent.
The preliminary method consisted of setting concentrated loads on a sample section which reproduced the features of the highest embankment section. The testing ensured that the performance of the stabilisation method met requirements. The process verified to what extent the platform would transfer the loads to the longer elements below. Data were collected for three months (and continue to be collected for a long-term analysis) and confirmed that the transfer of the loads took place as expected and within the indicated project values.
By contrast, the permanent monitoring system consists in positioning, every 300m in the deeper elements, extensometers and transducers (DMM) for measuring pore water pressure. This arrangement ensures that the Florida DOT can constantly (and over an extended time) monitor the behavior of the foundation system on which the road embankment rests.
The piling task has been assigned to a Soilmec SR-90 TTM (TreviTurboMix) drilling rig that can produce a double column by overlapping two elements, which is similar to the layout of secant piles. During some stages of the work, a second machine has been used in tandem with the first to speed up operations and also to help minimise the impact on traffic. To allow production of two columns at a time, the SR-90 in the TTM (TreviTurboMix) version is fitted with twin injection systems and features two shafts driven by two rotary heads delivering a torque of 179kN. The machines are also equipped with a control system that regulates the flow and quantity of injected material arriving from the mixing plant. The SR-90 also features the DMS system, which enables monitoring of functions such as rotation speed, torque and depth, and the principal mechanical and hydraulic components of the machine. This helps the contractor monitor working performance and ensures that the work complies as required with all the various parameters and project specifications. The drilling position system (DPS) meanwhile delivers correct positioning of the columns on three axes to guarantee their verticality.
Once the stabilisation work is complete, the two SR-90 TTM rigs will have treated 172,025m3 of material. And once the work on the US 331 highway is complete, drivers will benefit from reduced delays at peak periods, while residents will also be assured of a much safer emergency route in the event of a hurricane.
A major road widening project underway in Florida is due for completion soon. The work will improve an important section of road, reducing congestion at peak period and cutting travel times for drivers. The US 331/SR83 highway runs for some 79km and provides an important link in Florida’s Panhandle area, as it connects with Route 98.
Route 98 crosses a highly populated area noted as a tourist destination, whereas to the north it joins up with I-10, a highway that connects the Atlantic to the Pacific, the most southerly of the several coast-to-coast routes across the US. A key section of the US 331/SR83 route that needs to be improved is the 6.4km stretch crossing the Choctawhatchee Bay. The Choctawhatchee Bay extends for around 65km, covering an area of 334km2 and forms part of the Emerald Coast region, which is located on the Florida Panhandle in the north-western part of the state. This road is critical, especially for local transport, because it is one of the main road links to the Emerald Coast. However, it has to carry heavy traffic volumes of both commercial and private vehicles at present and congestion can be severe at times, resulting in delays for drivers. The route was first opened to drivers in the 1950s and vehicle numbers and distances driven have risen enormously since then, so the road is understandably having to cope with
traffic volumes that far exceed its capacity at peak periods.
US 331, which features only two lanes for the 6.4km stretch crossing the Choctawhatchee Bay, also has an important function as an emergency route. In case of evacuation due to a hurricane alert, it is the only major escape route by road from the Santa Rosa Beach area to points north.
The area is densely populated and especially during the high season when tourists or those with second homes in the area tend to be in residence. However, this is when there is a risk of hurricanes and storms and as a result, when the road is likely to have to cope with huge numbers of vehicles leaving the area in a hurry. As a result, the
The upgrade project called for two new lanes to be added to the current 6.4km section comprising the causeway and bridge. The work has also included a new bridge to the east of the 3.7km-long Clyde B Wells Bridge. The widened four lane causeway will carry traffic to and from the bridges, and from both south and north sides. The road widening project also includes that ground be prepared for a park and recreation area at the very end of the embankment on the south side. When the construction work is completed, the new bridge and widened causeway will be used to handle the traffic driving northwards, while the existing causeway and bridge will carry the traffic heading south.
The US$118.5 million design-build project was won by a joint venture team comprising
The project to widen this 6.4km stretch is not without its challenges however. Because the water table is high, the ground conditions are difficult and require extensive preparation to ensure the roadway can be constructed properly. For this portion of the project, a specialist firm was brought in to handle the work by the joint venture partners. Italian company Treviicos, through a subsidiary, Treviicos South (TIS), is handling this important link in the chain and carrying out the necessary road foundation improvement work for the upgraded road connection.
Treviicos was subcontracted to handle the ground stabilisation work for the foundations below the embankments. The less than ideal geological conditions meant that this crucial aspect of the project had to be carried out by a specialised ground engineering contractor with experience of this type of work. Treviicos was selected due to its extensive experience from working with all types of foundations in loose soil.
Over the years, the causeway embankments had shown clear signs of settlement as a result of insufficient bearing capacity. The embankments were suffering from the combined effect of increased traffic volumes as well as the poor quality of fill used at the time of the original construction in the late 1930s, and before the opening of the current US 331 in 1953. Construction engineering has improved since that time, although it is a testament to the original work that the causeway embankments have lasted so long.
The bearing capacity of the two causeways leading to the bridge from the north and south had been provided by a 13.7m thickness of consolidated sands, silty sands and clayey sands that had only been lightly loaded. This arrangement offered a limited bearing capacity given that differential settlements visible on the surface had long been evident. To verify if there were deeper bearing layers susceptible to high settlement potential, extensive bore samples were taken down to a depth of 61m, using dynamic penetration (SPT) tests that were carried out in the south and central embankments. The tests revealed that at a depth of approximately 12m, there were very loose to dense clean sands within layers of silty and clayey sands.
However no limestone layer was hit until 45.7m down, although at depths of 45.7-61m, very dense sandy layers were encountered leading to "refusal" SPT-N values. In the upper layers the surveys indicated weak clays and silt-sandy layers. A number of further surveys were carried out as precautionary measures in the external (eastern) part of the central embankment and these yielded similar results, demonstrating that no well-defined bearing layer existed. This geological situation led engineers at Skanska and Parsons Brinkerhoff and Treviicos to utilise a solution that would guarantee the bearing capacity and durability required by the principal, also in the event of a destructive hurricane occurring once every 100 years.
The solution was to create columns using the shallow mixing method (SMM) and deep mixing method (DMM) techniques. Both of these methods were carried out by Treviicos which used its TreviTurboMix system. This novel type of soil mixing has been developed jointly by Trevi and
This method is said to allow fast and cost-effective construction of columns that can also comply with strict quality standards. The system can be applied to a wide range of soil types, from cohesive with a soft consistency to loose and cohesionless with a medium consistency. TreviTurboMix technology includes a tool that combines the jet effect at a high kinetic energy, with mechanical mixing due to the action of the blades. These are angled to achieve maximum effectiveness. This technology is considered a wet system as the fluid grout type binder is injected through outlets in the blades.
Injection takes place only when the tool is in its down-stroke phase, whereas mixing is carried out both during the down-stroke and up-stroke. One of the key advantages of the TreviTurboMix method according to the firm is that the geometric characteristics of the columns do not depend on soil characteristics as with traditional mixing. Instead geometric characteristics of the columns remain constant for the whole length, which is said to provide a high quality solution as well as durability. With the TreviTurboMix system the stabilising agent is inserted into the ground during drilling in the form of a stable mix of water and cement to which additives can be included should this be required for the mix.
The technology has been well-proven in a number of projects, both in the US and elsewhere, which was why Treviicos was confident that the system would suit the tricky conditions in Florida. In the US TreviTurboMix was used to reinforce the LPV 111 levee in New Orleans, the largest project of this kind ever undertaken in the US, and among the most important ever performed in the world. And as in Florida, the ground conditions around New Orleans are poor while the water table is high, showing just how suitable the TreviTurboMix method would be for the US 331 highway project.
After examining the SPT results, engineers came to a solution based on a soil mixing design that would deliver the necessary bearing capacity. This involved constructing no less than 1,500 double columns, each with a length of 13.7m so as to reach the bearing layer. The design also called for the construction of a further 8,400 double columns each with a length of 3.04m and arranged in a tight mesh so as to provide a supporting platform covering around 95% of the causeway surface.
Using this technique delivered a dual benefit, providing the advantages of a deep foundation as well as a shallow foundation. The shallow foundation is important as this acts as a support for the roadway and ensures that the bearing capacity of the ground is sufficient to support the static and dynamic loads generated by vehicle traffic. In terms of ground stabilisation meanwhile, this system allows the longer and deeper columns (DMM), with a compressive strength of 1034.2KNm², to transfer the loads of the platform columns (SSM) towards the deeper layers, which have a greater bearing capacity. This is achievable because the columns of the platform (SSM) have a compressive strength of 517.1KNm². This system also makes the more superficial layers resistant to erosion, which also helps to ensure long-term durability in the conditions.
The specifications for settlement tolerances were stringent so as to ensure long-term stability. These allowed for a maximum of 50mm of settlement for every 300m. To monitor the degree of settlement two different methods were used, one preliminary in the early stage of the project, and one permanent.
The preliminary method consisted of setting concentrated loads on a sample section which reproduced the features of the highest embankment section. The testing ensured that the performance of the stabilisation method met requirements. The process verified to what extent the platform would transfer the loads to the longer elements below. Data were collected for three months (and continue to be collected for a long-term analysis) and confirmed that the transfer of the loads took place as expected and within the indicated project values.
By contrast, the permanent monitoring system consists in positioning, every 300m in the deeper elements, extensometers and transducers (DMM) for measuring pore water pressure. This arrangement ensures that the Florida DOT can constantly (and over an extended time) monitor the behavior of the foundation system on which the road embankment rests.
The piling task has been assigned to a Soilmec SR-90 TTM (TreviTurboMix) drilling rig that can produce a double column by overlapping two elements, which is similar to the layout of secant piles. During some stages of the work, a second machine has been used in tandem with the first to speed up operations and also to help minimise the impact on traffic. To allow production of two columns at a time, the SR-90 in the TTM (TreviTurboMix) version is fitted with twin injection systems and features two shafts driven by two rotary heads delivering a torque of 179kN. The machines are also equipped with a control system that regulates the flow and quantity of injected material arriving from the mixing plant. The SR-90 also features the DMS system, which enables monitoring of functions such as rotation speed, torque and depth, and the principal mechanical and hydraulic components of the machine. This helps the contractor monitor working performance and ensures that the work complies as required with all the various parameters and project specifications. The drilling position system (DPS) meanwhile delivers correct positioning of the columns on three axes to guarantee their verticality.
Once the stabilisation work is complete, the two SR-90 TTM rigs will have treated 172,025m3 of material. And once the work on the US 331 highway is complete, drivers will benefit from reduced delays at peak periods, while residents will also be assured of a much safer emergency route in the event of a hurricane.