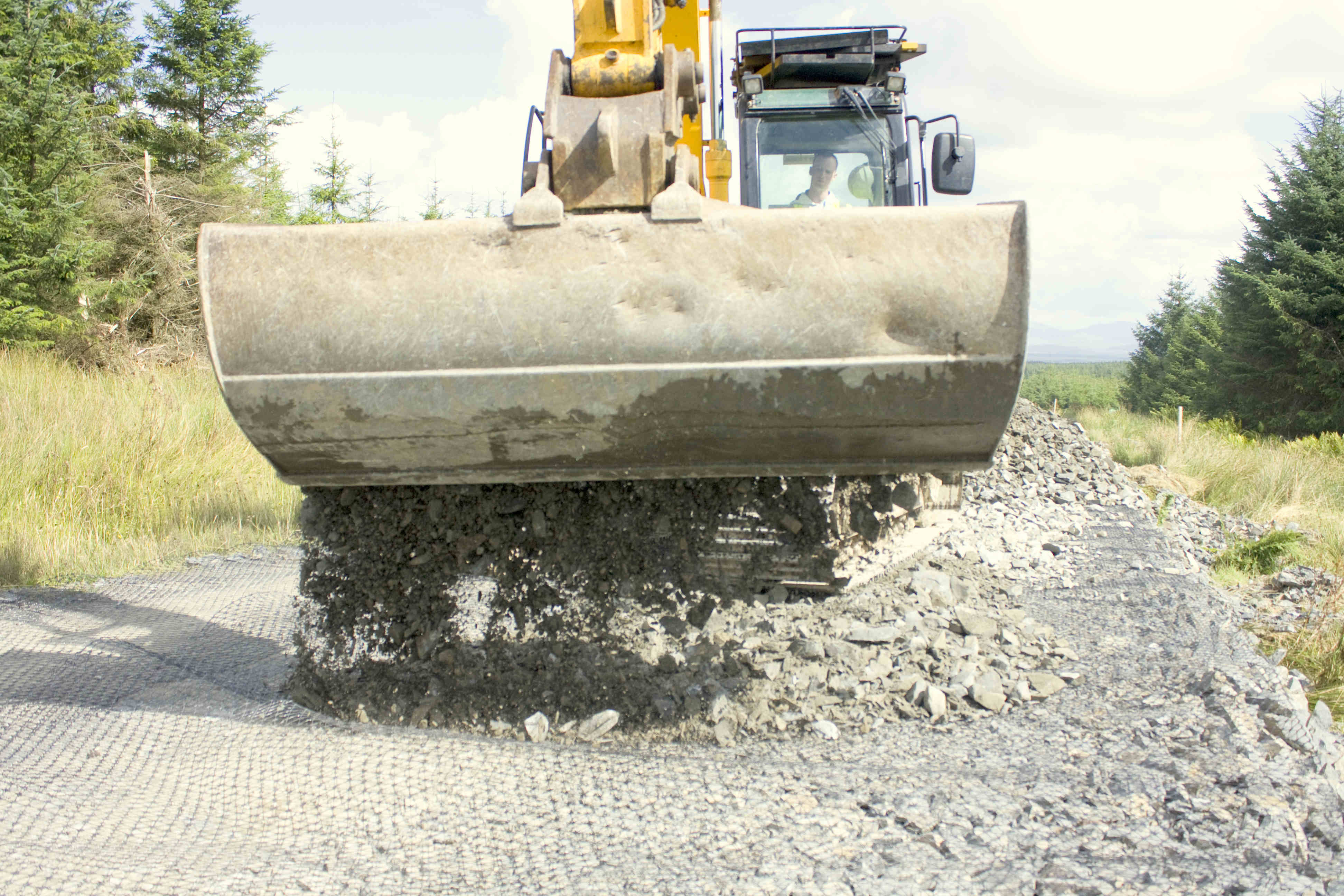
With geosynthetics sales set to grow rapidly in the next three years, manufacturers are preparing for the demand. Patrick Smith reports
Global demand for geosynthetics is projected to increase 5.3% annually to 4.7 billion m² in 2013 with countries such as China, India and Russia expected to post the strongest gains through the forecast period.All are building large-scale infrastructure developments and face evolving environmental protection regulations and strict building construction codes.
While growth in geosynthetics demand is expected to be substantial in nearly every region, the underlying reasons for that growth can vary.
These trends are presented in World Geosynthetics, a new study from The
The Asia/Pacific region accounted for nearly 45% of global geosynthetics sales in 2008. Advances in this market are primarily driven by China, which itself accounted for over 75% of regional sales in 2008. It is also projected to account for nearly 60% of new global demand for geosynthetics generated between 2008 and 2013 due to its amount of available land, its ongoing development of large-scale infrastructure projects, and its need for erosion control. Similarly, India is expected to post double-digit annual growth through the forecast period with gains driven by its ongoing development of transportation and erosion protection.
North America was the second largest regional market in 2008, accounting for nearly a 25% of global sales. Advances in the US market are expected to be aided in the near term by government spending initiatives on roads, bridges and other public works projects.
Western Europe and Japan are fairly comparable to the US in terms of the level of maturity of their respective geosynthetics markets, as well as the type of regulatory environment.
An example of the use of these special reinforcements can be found in Ochtrup (northwest of the Münster region in Germany). Rosenstrasse runs east of the town and leads directly to the border crossing to the Netherlands.
A bypass, completed in 2005, aimed at reducing heavy goods traffic in the town. On completion the former District Road 57 was downgraded to a municipal road, although people still use the shorter route along the Rosenstrasse as an alternative to the bypass.
Damage to the road (map cracking) was established along the entire width of the road before repair work on Rosenstrasse started in 1996. The plan to repair the road included removal and replacement of the 50mm layer of asphalt wearing course, and this revealed extreme cracking in the binder and base courses, which were in a very poor condition.
To renew just the wearing course would have quickly allowed cracks from the binder course to progress through to the top layer, making further repairs necessary; a total prolonged closure of Rosenstrasse was not desirable, and renewal of the entire upper structure would have caused considerable additional costs.
To keep repair costs low, extend the time between repairs and to allow the repaired road to be maintained at a high level for longer, it was decided to employ the HaTelit asphalt-reinforcement system (initially as a short-term measure). This would prevent cracks in the binder course progressing to the top layer.
After removal of the wearing course it was sprayed with bitumen emulsion: the
Six years after the work, HUESKER asked the Steinfurt District's chief executive for a condition report on the Rosenstrasse.
The response was: "...I'm happy to inform you that the repairs at the time to Kreisstrasse 57, Rosenstrasse, using HaTelit 30/13 have fully stood the test of time. The use of the asphalt-reinforcement system under the 0/11 asphalt layer has meant that, to this day, no cracks have appeared in the asphalt-concrete surface. This method was chosen at the time to avoid the necessity of the additional work required for the binder and base course..." In April, 2009, further inspection revealed that "...no map cracking has appeared in the asphalt-concrete surface to this day," while in August/September, 2009, HUESKER commissioned TÜV Rheinland LGA Bautechnik to record the cracking and assess the condition of Rosenstrasse along the length repaired in 1996.
The appraisal also compared the current condition with the condition that existed before repairs were carried out in 1996. This permitted conclusions to be drawn about whether the use of the HaTelit asphalt-reinforcement system is able to delay the occurrence of cracks propagated from the lower courses, says HUESKER.
In August, a visual inspection was undertaken by the
The LGA used the image documentation of the construction measures prepared in May 1996 as the basis for its assessment. The construction supervisor employed by the Steinfurt District at the time also provided additional necessary information.
After 13 years of use, the cracking condition value (ZWRIS) for the section of the road repaired with HaTelit in 1996 was determined as being "excellent." According to the LGA, visual inspection of the road surface revealed almost no damage to the substance. Two repair sites were recorded (due to drainage work), and a few lateral cracks were discovered at one point on the outer edge of the built-up road along with small cracks at a few other points on the outer edges. Photographs documenting the condition of the site in 1996 show that the distance between the HaTelit system and the road edge was always around 150-300mm.
TÜV Rheinland LGA Bautechnik also confirmed: "The entire remaining road area is free of cracks."
Floating on TriAx
The site in a managed forest is extensively covered with moorland peat which is unable to bear the load of heavy construction plant, and to stabilise 65km of access roads at the Arecleoch site, civil engineering contractors
As well as construction traffic, access for turbine maintenance is required throughout the windfarm's 25-year operational life, so a site-wide road network was necessary. Extensive excavation to provide a conventional load-bearing road was not acceptable, and instead consulting engineers Grontmij proposed a geogrid-based floating road construction over the peat for maximum ecological sensitivity. This would mechanically stabilise the aggregate fill minimising the thickness required to withstand loading from the 45tonne construction vehicles.
The floating road, comprising layers of geogrid and site-sourced greywacke stone, minimises disturbance of the peat and can be removed at the end of the site's life.
Tensar's TriAx geogrid, based on a triangular shaped aperture, stiff polymer grid, was selected after an on site performance trial.
Following this, 20km of 6m wide main access roads and 45km of 5m wide ancillary access roads were constructed or widened around the site.
"In most areas, two layers of geogrid with 450mm of compacted well graded fill with a maximum particle size of 75mm were sufficient to distribute the traffic loading, although some deeper contours required more fill to maintain the shallow gradient," said Mike Horton, area civil engineer for Tensar.
Pavement construction
Developments in pavement reinforcement and how simple techniques can enhance the design life of pavement construction have been examined by David Crowther, technical manager ofIn a case study, part of a fuller report, he looks at the rural road network of Sutherland in the Highlands of Scotland, much of which is single track and built on very weak ground, mainly peat, which is unsuitable for use by heavy vehicles serving the local timber extraction industry.
To reinforce the roadways and bring them up to useable standard without importing huge quantities of stone road-base materials,
"Bituminous overlays incorporating Maccaferri Roadmesh pavement reinforcement mesh were applied to each in a long-term trial to assess their viability. This mesh causes the pavement construction to work as a cohesive mass, absorbing the horizontal tensile stresses and spreading the imposed traffic loadings over a wider footprint, reducing its damaging effect and helping the more heavily trafficked pavement to effectively 'float' on the weak underlying ground," says Crowther.
The Sutherland trials are being undertaken as a partnership agreement between Forest
'Innovative' Enkadrain
In 2009, Colbond introduced a new method of controlling the overburden pore water resulting from the installation of prefabricated vertical drains (PVDs).On the A63 highway known as the La Côte des Basques, between Bayonne and Biarritz in south-west France, PVDs were installed to prepare the marshy soil for building new highway sections. To manage the run-off of the resulting overburden pore water, an innovative choice was made. Colbond's Enkadrain 5006H/5-2S/T110PP was used as a geosynthetic drainage layer replacing a 1m layer of permeable sand to collect the overburden water from the vertical drains (traditionally, the sand layer combines two functions: drainage of water and acting as a foundation for the installation rigs).
The expensive sand was not required as a locally available C1B3 type of stiff clay with big boulders could be recycled from elsewhere on site to provide the foundation, while, as this type of soil lacks sufficient permeability, Enkadrain solved the drainage problem. Savings were made in the supply of permeable sand.
The 1m thick type C1B3 non-draining fill material was installed first, after which the PVDs were inserted down to 22m depth to achieve a planned 600mm settlement. The 5m wide Enkadrain was then placed and directly backfilled. No special connections between PVD and Enkadrain were required.
The final embankment fill on the Enkadrain was a maximum of 4m high, giving a ground pressure of (4m x 20) = 80kPa.
An additional surcharge of 10kPa was also taken into account so the pressure on Enkadrain equalled 90kPa.
Under a pressure of 90kPa and a hydraulic gradient of 0.6% (a slope of 0.6% or horizontal with a hydraulic pressure of 6cm of water column) the discharge capacity of Enkadrain 5006H/5-2S/T110PP is equivalent to 1m of sand.
The surface area was 54,500m², and the region's roads authority ASF (Autoroutes du Sud de la France) and the consultant
Detecting problems with GeoDetect
The system has already been used in Europe for a few years, and its North American launch will enable the company's global marketing efforts in the field of geotechnology to be coordinated and the continued development of the system to be intensified.
TenCate GeoDetect intelligent geotextile is a system that will provide detail about the properties of embankments, slopes, tunnels, walls, levees, roads, rails and other earth structures with real-time monitoring of "every square metre of land for ground movement, soil erosion, settlement and other changes." The system is developed by Roctest (through its subsidiary SMARTEC), the world's largest manufacturer of fibre optic sensors for civil engineering applications, and TenCate Geosynthetics.
Wilson Harvie, director of corporate business development at TenCate Geosynthetics North America, said: "By combining proven optical fibre technology with the characteristics of our geotextiles, TenCate Geosynthetics offers an accurate, customisable and profitable monitoring system."
In Europe the required experience has already been gained with TenCate GeoDetect in pilot projects, including one in France for the construction of the embankment for the rails of SNCF's (French Railways) high-speed line, and another in The Netherlands.
"The future of TenCate Geosynthetics is less about products and more about providing solutions for geotechnical challenges through a systems approach. Coupling our application expertise with Roctest's sensoring technology gives an innovative and differentiated approach to detecting potential failures and/or problems for civil engineers," said Dave Clarke, group director for TenCate Geosynthetics.