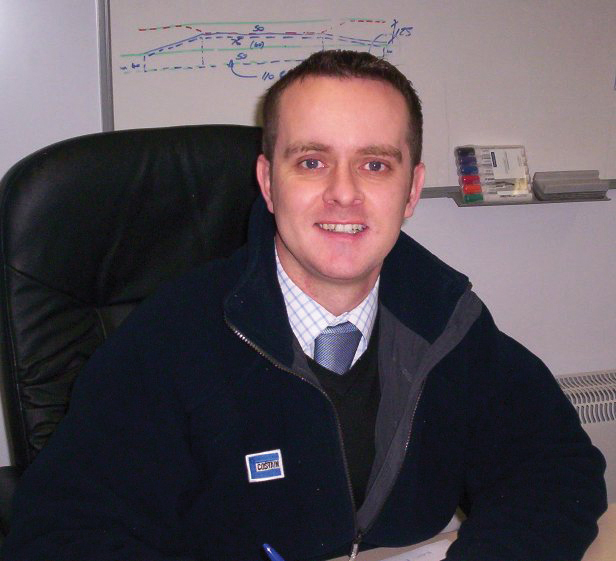
The latest drainage technology and products are being used to provide crucial drainage solutions to ambitious major transport projects, while innovative geosynthetic products and the people behind them remain in demand worldwide as Guy Woodford reports
An innovative solution to providing vital, low-impact surface water control for one of Britain’s largest local authority road schemes is said to have been recently achieved usingThe new 7km bypass built by
“One important problem with a new road like a bypass is the potential disruption to surface water ow in the area,” says Costain’s Church Village project manager, John Lee.
“I had not used the Hydro Drop Shaft technique before, but it seemed a simple and non-disruptive solution which avoided much greater expense.”
Simon Edwards, principal engineer, water and environment, for
“From there, the water had to descend around four metres to a small local stream bed and then into the River Taff,” he explains. “Uncontrolled, this drop of water would have scoured away the stream bed, and caused unacceptable environmental damage.”
To achieve the required water control, the Hydro Vortex Drop Shaft system was used. A single-shaft self-activating system with no moving parts, the product is designed to quietly and safely drop water or sewerage from heights while being ergonomically sound.
“The maximum design ow was 1m3/sec through a 600mm pipe reducing to 450mm,” says Edwards. “By inducing a vortex at the lower end of the drop, the Hydro Vortex Drop shaft provided the energy dissipation which prevents excess flow force at the discharge.”
An alternative solution to the Hydro Drop Shaft had been to build a cascade to take the ow down over successive weirs. However, Lee points out this would have involved “considerable and expensive” earthworks through the rail embankment.
“Additionally, cutting into old rail ground structures could have created all sorts of trouble,” he continues. “No-one knew what was in there as all the records had disappeared. It was much simpler to install the Drop Shaft, and with less visual impact too.”
Equal care was also said to have been paid during the Church Village project to other environmental factors, from the planting of 117,000 new trees and shrubs and using 300,000 tyres as part of the land ll, to building three connecting bridges across the road for the use of local dormice, an endangered species.
Rhondda Cynon Taff Council granted planning permission for the bypass in 2006. Funded by a US$142.4million (£90million) grant from the Welsh Assembly Government, the road was opened to traf c in autumn 2010.
As well as seeing its products used successfully in recent major highways projects, HI has launched a new worldwide engineering consultancy for ood risk assessment and stormwater management. The consultancy’s UK work will, according to the company, respond to the growing need for expert technical support in both the public and private sectors following water and planning reforms.
Led by respected industry experts David Scho eld and Alan Corner, who have joined HI to establish the new team, Hydro Consultancy (HC) will provide technical professional services, design and hydraulic modelling support to a range of clients from local authorities and developers, to landscape architects and operating bodies.
“The requirements of the Flood and Water Management Act, and changing planning laws, are challenging engineers in the public and private sector alike at a time when budgetary constraints have never been tougher,” says Corner, HC’s recently appointed associate director.
“Hydro has responded by providing highlevel engineering consultancy that can rival any in the UK, whilst offering a much more agile and value-for-money service.”
HC’s services will encompass Flood Risk Management and Assessment, SuDS design and implementation, planning support, drainage design support for formal Water Company agreements, operating authority consents, BREEAM and Code for Sustainable Homes assessments. The consultancy team are said to be retaining an independent ‘arms-length’ stance, while calling on the depth of knowledge, experience and R&D resources of HI’s global operations.
YouTube may not have historically been a source for large scale drainage solution knowledge, but that’s just what
Mike Rawlings, soil and drain marketing manager at Saint- Gobain PAM UK, said: “Optimising our online presence is key to our business development strategy. We believe visitors to our YouTube channel will and the videos both Tangier to Saïda in northern Morocco has involved the installation of 35 geogrid reinforced earthwalls up to 31 metres high. Moroccan authorities used Enkagrid PRO geogrid from Netherlands-based
The bypass is seen as an integral part of the Moroccan Government’s northern region development policy, aimed at opening up the Mediterranean coast while improving the infrastructure of the region and access to it. It is also seen as key to boosting the region’s economic potential, particularly tourism and maritime activities.
Earth walls reinforced with geogrids were chosen by Moroccan authorities for phase 2 of the project, as the Rif region shows the highest level of seismicity in Morocco and experiences the largest number of earthquakes in the country. Four earthquakes between enlightening and practical.” The ongoing construction of a Mediterranean bypass linking 1910 and 1926 caused substantial damage to Melilla, an exclave on the north coast of Morocco. However, 21 January, 1909 was the date of the country’s most severe earthquake to date, with a measurement of 6.2 on the Richter scale, which occurred in the Tétouan region. In his report to the world renowned Geosynthetics Middle East conference held last October, Colbond product manager Alain Hérault highlighted how seismicity is a “… disturbing factor in the equilibrium and stability of embankments, slopes and mountainsides, demanding the selection of highly exible support techniques to withstand earthquakes”.
The 35 earthwalls used in phase 2 of the bypass project required the installation of 1.5million m² of reinforcing geogrids. All facings are inclined at 63° (1H/2V) and consist of 1metre x1metre x1metre gabions lled on site. Enkadrain 5004C/5-2s/T110PP ensured the drainage of the excavated embankments behind the walls. This product ful ls the requirements of the external French certi cation quality system (Asqual).
Colbond says the geogrid reinforced earthwalls were designed in accordance with Eurocode 7 which, since 2010, has been the standardised geotechnical calculation of structures used by
TenCate Geosynthetics recently introduced
The US company’s MiraSlope design solutions software is said to be based on state of the practice design methods, and can determine the optimal reinforcement con guration for simple geometries using what is described as its interactive approach. The designer or engineer may select the appropriate TenCate reinforcement geosynthetic and facing system to use in their design, and analyse the potential failure modes for the design cross section.
The design standards that the MiraSlope can use in North America are FHWA and BS8006- 95, in Europe, EBGEO 2010 based on EC7 and BS8006-95 and in Asia, FHWA and BS8006-95.
"The introduction of TenCate MiraSlope design solutions software allows engineers to quickly and accurately design MSE structures with the most extensive geosynthetic reinforcement product line available,” says John Henderson, senior vice president of TenCate Geosynthetics Americas.
“In addition, the flexibility to select either FHWA or European design standards will further assist engineers in meeting the end user's requirements. We are excited about adding this powerful tool to our growing package of software design solutions."
In the UK, Tensar’s Tensartech TR2 Wall solution was used on the Dishforth to Leeming section of the North Yorkshire A1 upgrade, which is seeing new carriageways built adjacent to the in-use existing highway. The TR2 Wall was deployed as a temporary structure during the raising of a below grade section. Joint venture contractors
The existing 150metre section of the A1 either side of the Butcher House Bridge is up to 10 metres below the final required grade of the new motorway. An earth retaining structure with a near vertical face was required to support the new carriageways, which would allow the traffic to be switched to them while the old section was filled in to complete a new dual three-lane motorway.
Tensar says a conventional technique using extensive sheet piling along the embankment and for bridge abutments to relieve lateral thrust would have been time consuming, and access for the installation plant could have disrupted traffic flow. In addition, the sheet piling would have been buried when the existing carriageway was filled in for the completed motorway, making a very expensive loss of material.
“Tensar developed a reinforced earth solution which was quick to install, with minimal disturbance to vehicles by temporarily supporting the new south bound embankment, bridge wing walls and abutments,” says the joint venture senior engineer, Kevin Wilcock.
“As a temporary sacrificial structure, the TR2 was by far the best option and less expensive than other methods available.”
The Tensartech TR2 Wall comprised compacted fill reinforced with layers of Tensar’s uniaxial geogrid, securely connected to steel mesh facing units to form a 100metre length of the 85° earth retaining structure up to 3metres high. Site won fill was used for the project. For the bridge abutments and wing walls a 26metre length of vertical faced TR2 face, using imported 6N/6P granular fill and uniaxial geogrids, was built up to 9.5metres. At either end of the embankment, a 45° slope was constructed using the Tensartech.
The North Yorkshire A1 upgrade, which started in 2009 and is due for completion this summer, will see the A1’s existing dual twolane carriageway become a dual three-lane motorway. Local traffic access points are being made safer, while agricultural traffic will be excluded from the completed motorway.
Huesker Synthetic recently hosted a special conference in Düsseldorf to mark the German geosynthetic company’s 150th anniversary. Representatives of subsidiaries, numerous national and international business associates and partners of the firm, as well as representatives of engineering companies, testing institutes, authorities and universities attended the two-day event.
The main focus of the conference was on geotechnical engineering but special attention was also given to geosynthetic engineering solutions ensuring sustainability and quality management, while also helping to tackle outstanding projects.
In his welcome speech, Dr Dimiter Alexiew, technical director of Huesker, described how competition from abroad in the post-Second World War years, particularly in the field of high-quality textiles, led to a change of commercial emphasis by Huesker from the 1960s onwards.
It saw the firm concentrate on the manufacturing and sales of products made of synthetic fibres and materials for hydraulic engineering applications and other civil engineering fields where the term ‘geosynthetic textiles’ is now used. “We were able to build on this solid basis throughout the years which set the stage for our sustained growth today,” said Alexiew. Picture left to right: Sven Schröer; Dr Michael Schmalz; Andreas Elsing; Professor Jorge G. Zornberg; Markus Wilke; Christian Kortboyer; Martin Hawkswood; Professor Tom Schanz; Dr Dimiter Alexiew.