A new causeway, crossing the Bay of Kuwait, is under construction and providing a major engineering challenge - Mike Woof reports.
The new Sheikh Jaber Al-Ahmad Al-Sabah Causeway Project being built across the Bay of Kuwait is a massive engineering project that is costing around US$3 billion in all. This highly complex project involves the design, build, completion and maintenance of the causeway, which spans Kuwait Bay between Kuwait City and the Subiyah area. The 36km Sheikh Jaber Al-Ahmad Al-Sabah Cau
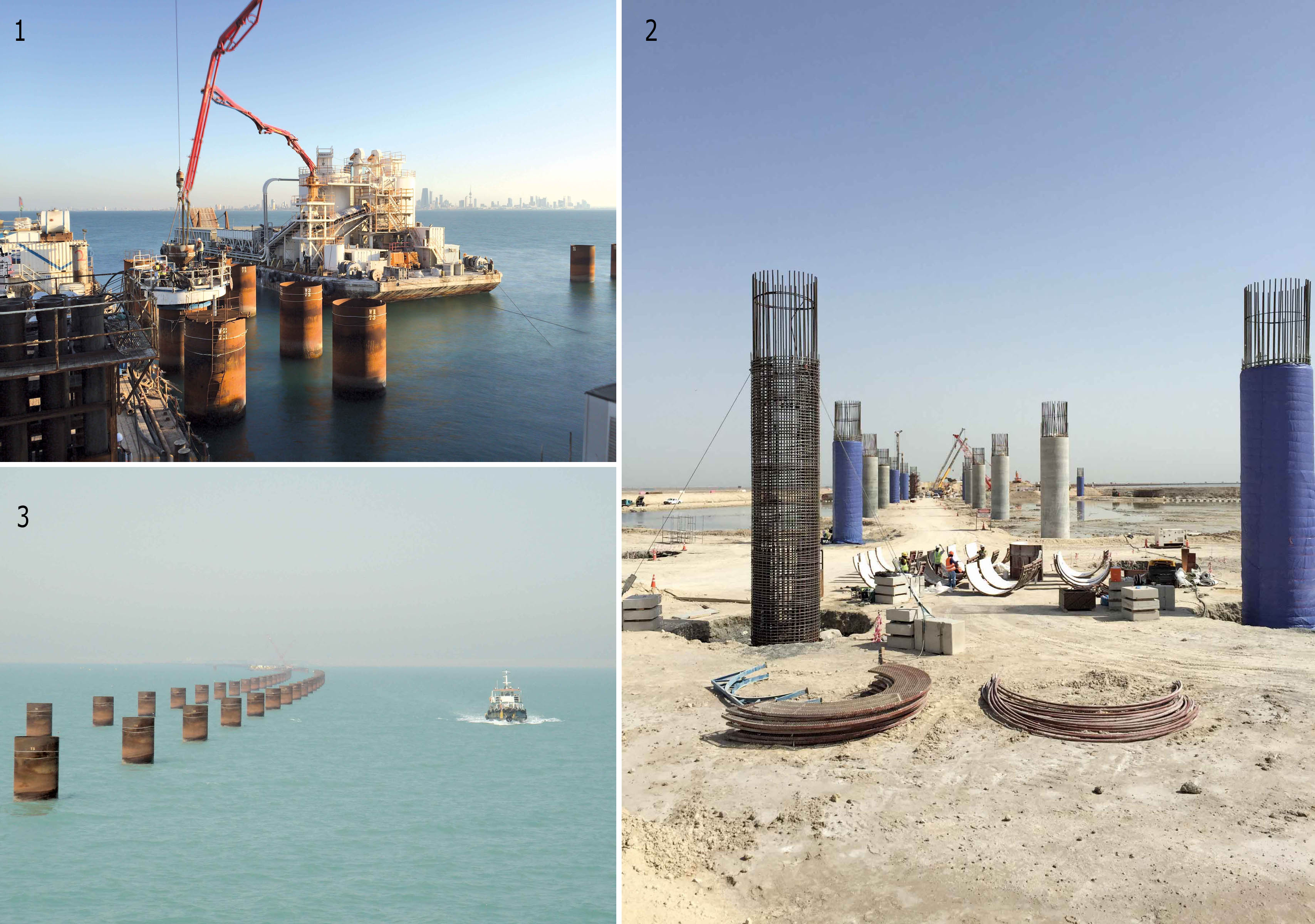
1. Materials are supplied from a barge lying alongside the piling barge 2. The onshore piling operation has been rather less complex 3. Constructing the piles offshore has required a complex working schedule
A new causeway, crossing the Bay of Kuwait, is under construction and providing a major engineering challenge - Mike Woof reports.
The new Sheikh Jaber Al-Ahmad Al-Sabah Causeway Project being built across the Bay of Kuwait is a massive engineering project that is costing around US$3 billion in all. This highly complex project involves the design, build, completion and maintenance of the causeway, which spans Kuwait Bay between Kuwait City and the Subiyah area. The 36km Sheikh Jaber Al-Ahmad Al-Sabah Causeway Project (SJSC) is one of the largest and most challenging transport infrastructure projects in Kuwait, as well as the entire Middle East region.
The overall aim of the project is to reduce the travel distance between Kuwait City and Subiyah area from 104-36km, which will cut the journey time from 90 minutes at present to less than 30 minutes.
Building the causeway will provide a new strategic highway route that will help planned development work located to the north of Kuwait City, as it will connect Shuwaikh Port with the Subiya New Town Development. And it will help to integrate the northern areas of the country with more the densely populated central and southern regions, while also helping lower traffic congestion in the surrounding roads.
The client for the project is the Ministry of Public Works (MPW), State of Kuwait, while the link was designed by5549 SYSTRA, with 1397 AECOM handling the ICE role. The consultants involved are Dar Al-Handasah Consultants (Shair and Partners), SSH and 3355 TY Lin International. Korean contractor 5739 Hyundai Engineering & Construction is the main contractor for the project, while Italian contractor TREVI is playing a vital role, providing a significant number of the foundations for this 36km causeway.
The project is extensive and includes the construction of a 27km low-level bridge across the bay, a main bridge with a span of 200m, an elevated road, and a 5km approach road onshore in Subiya. The causeway crosses two artificial islands on its route, Bay Island North and Bay Island South, with project completion expected in 2018. There is also an additional 13km marine bridge connecting with Doha, on the southern side of the bay.
This is a megaproject in any sense of the term and providing stable foundations for the offshore section is essential for the project to be successful, as well as being one of the most challenging aspects of the work. Only with the proper foundations will the causeway be able to cope with the necessary structural loads of the roadway, as well as the surrounding offshore environment and any climactic conditions.
An important first step for the piling work was a highly accurate soil investigation, which was carried out in compliance with recognised geotechnical standards and guidelines to ensure the quality standards required. This investigation was vital to determine the most suitable method of bored piling for the foundations. The recovered data was also used as the basis for a more complex plan for each of the planned phases of the work, as well as including related information to aid in the design of the foundations for the proposed construction.
A drill log was generated for each stage of the investigation, providing important information such as a description of the soil, the location, the elevation, the date of the investigation and the depth. At the Shuwaikh Port end of the route, the ground investigation operation found large quantities of sand in very loose, medium dense and very dense conditions. Meanwhile close to the planned Subiya New Town, the ground investigation showed that there was a combination of very dense sand and very soft to medium clay. Using this data, the engineering team was able to establish what type of bored piles would suit the job.
Trevi Foundations Kuwait is handling much of the offshore piling and onshore piling activities, using specialist equipment from the2959 Soilmec range as well as other more conventional items of construction machinery.
The onshore piles are subject to lower stresses and have been designed with diameters of 2.5m. However the offshore piles have to cope with greater loads and as a result, have diameters of 3m, while also reaching greater depths.
The offshore piling operation has faced particular challenges, having to cope with hydrostatic pressure and buoyancy, underwater currents and waves and swells. The length of the causeway means that the pile furthest from shore is 17km out to sea, while there have been other significant challenges also. The tidal variation is very large around Kuwait’s shores and wind speeds can be high, while storms can also be very powerful. Luckily, cyclones are comparatively rare events for Kuwait and there is also comparatively little shipping using the area close to the route of the causeway.
The project features some 1,200 piles in all, with TREVI boring around 230 offshore and these featuring diameters of 3m and reaching depths of 84m. This piling work has been handled from a barge belonging to236 Hyundai and which sits on four spud legs, with four anchors helping to secure it in position when driving the piles. To further optimise stability, the barge features 13 large water tanks underneath its deck, each with a capacity of 55m3. These also help prevent the barge from moving during the piling work and ensure the piles are bored vertically.
The barge is not a self-elevating jack-up type though and once each pile has been bored, it has to be moved to the next location using the anchor boat and a tug. A Soilmec SC-120 rig has been used for constructing the piles, with assistance from a2200 Kobelco crawler crane to lift in the necessary materials, as well as a conventional crawler excavator for general materials rehandling duties.
In addition to the piling barge carrying the Soilmec rig, the excavator and the Kobelco crawler crane, TREVI is also using a disposal barge, a service barge and a rebar cage barge. The disposal barge plays an important role during the drilling phase, as it is loaded with all of the material removed during excavation. Meanwhile the service barge plays a support role for the piling operations, storing all the necessary tools such as the second bucket, the cleaning bucket and hanging bar. As its name suggests, the rebar cage barge is used to store the rebar and this has to be located next to the piling barge.
The piling work involves seven main tasks; driving the casing, excavating, cleaning, placing the reinforcement, flushing, pumping the concrete and installing the pile head. TREVI says it has been careful to ensure quality throughout each of these stages, using a special polymer mud to support the pile sides during excavation and until the casting portion is carried out for example.
To ensure the polymer works effectively, the level has to be kept 3.05m above the piezometric surface at all times. The slurry is also placed in the borehole prior to the piezometric level being reached as this prevent sloughing or ravelling. TREVI says it has used advanced polymeric technologies, as these limit filtration losses. At the same time, care is being taken to maintain a positive fluid pressure on the borehole sidewalls, providing the essential sidewall stability. When the polymer slurry is pumped into the excavation, there is an initial fluid loss into the formation. It is this penetration of the polymer slurry into the porous formation that allows interaction with the soil particles through chemical adhesion, providing the necessary bonding effect and improving the stability of the pile sidewalls. The strength of adhesion however varies between polymer types and can also be affected by the use of different additives, with a wide performance range depending on the combination used.
TREVI says that to ensure that the polymer slurry meets quality needs, clean water is required with pH values ranging from 10-11. Mixing should be homogenous to avoid agglomerates of polymer powders forming, while the fresh slurry should also meet the necessary target for viscosity. The polymer slurry has to be recirculated without the use of centrifugal pumps and recovered from the pile using progressive cavity pumps, while a filtration tank is employed to minimise the sand content. While excavation work is ongoing, the engineering team also have to maintain constant checks on the viscosity, pH value, density and sand content of the slurry so as to ensure quality is optimised. In addition, there are also strict rules on the handling and disposal of polymer slurries as these are subject to environmental regulations.
Most of the casings measure some 40m long, with these being spaced in pairs 10m apart, at a distance of 60m between each pair. TREVI has been installing one pair at a time; first the pile on the east and then the pile on the west, before moving the barge to its next location.
Once each casing is ready and has been checked for position accuracy by a surveyor, the excavation work is carried out. The configuration of the Soilmec rig allows the 2.96m diameter bucket to be rotated in either direction. The bucket design is crucial to the operation as it has lateral openings that allow the polymer slurry to escape as it fills with the excavated material.
Another important piece of equipment that TREVI is using is the polymer compensation tank, which allows the polymer level to be controlled accurately in the casing. This ensures that the pressure is optimised and helps the stability of the pile when it is open.
The spoil from the bucket is dumped into an empty tank, with the excavator then being used to offload the material into the disposal barge alongside. At the end of each separate piling cycle, the disposal barge carries the excavated material to the jetty for recycling. So far the firm is taking around 15 hours for each of the 65m-deep piles.
Once the excavation work has been carried out, TREVI verifies the pile stability using a Koden test. This uses ultrasonic testing, a well proven technology that can determine if there are any collapsed areas or cavities.
Once the pile has been excavated and checked for quality, TREVI then uses a cleaning bucket with no teeth to remove any material from the bottom before installing the rebar cage.
The firm uses different segments, depending on the depth of the pile, though for most three are sufficient. These have to be installed in a very limited space and TREVI says that this stage is extremely tricky. Logistically complex, the position of the components has to be carefully arranged on the rebar barge and with the lightest segment furthest from the crane for this stage to be carried out correctly. And if the segments measure up to 23m as used for the deeper piles, then two cranes are required to lower the rebar cage into place.
The segments themselves are joined using special couplers but the spacing is critical, as the sections cannot be more than 5mm apart. Cleaning of the pile is also critical, using high-pressure compressed air to flush out debris, particularly at the base of the bore. Ensuring that the toe of the pile is clean is highly important as otherwise the structure would not be able to cope with the necessary loads. This flushing is carried out at seven points inside the bore, with each of these stages taking 20 minutes. A hollow pipe is positioned inside the pile, with a side pipe then connected at the end to allow the air to flow. The upper end of the tube then connects to a discharge tank that holds fluid from the pile base. Because the compressed air mixes with the fluid, this becomes lighter and is forced upwards by hydrostatic pressure into the discharge tanks.
Only once the flushing has been carried out fully and the sand content checked, can the concreting process be initiated for the casting process. A special 1.2m diameter cleaning bucket is also used that fits inside the 2.8m diameter rebar cage. This special bucket is able to slip down inside the cage without touching the sides and is used to remove the extra concrete, which is placed inside a special container and transported back to the main contractor.
With the cleaning process complete, a personnel basket is lowered into the pile so that the inside of the pile can be cleaned and the inner surface of the concrete smoothed over. Using this complex process in the challenging offshore environment, TREVI has been able to install three piles/week on average but the firm hopes to increase productivity as it refines the operation further.
All images provided courtesy of978 TREVI Group
Kuwait geography
The State of Kuwait is situated at the north-eastern corner of the Arabian Peninsula. It comprises an area of approximately 17,800km2. Kuwait has a hot and dry climate. The summer in Kuwait is very hot, especially in July and August and the mean temperature during this period varies from 30-50°C. The winter is cool however, especially in January when the mean temperature is 12°C.
Rainfall in Kuwait totals just 110mm/year while another prevailing climatological characteristic is the frequent dust storm. The contribution of dust sedimentation of the north-western part of the Arabian Gulf is some 1mm/year. The same thickness of deposition is assumed to be taking place throughout the coastal areas of Kuwait.
Pronounced variations in humidity are also common in Kuwait. Relative humidity varies from 60.9% in January to 21.5% in June. On the other hand, evaporation is very high and is variable within location and seasons, allowing a mean amount of evaporation of 10.3mm/day.
Kuwait lies on the eastern edge of the deep sedimentary basin that forms the Arabian Peninsula and is underlain by a considerable thickness of sedimentary rocks. In the south of Kuwait, relatively young deposits of the Dibdibba formation, which are Upper Miocene to Pleistocene Epochs approximately 2-10 million years old, outcrop at the surface. These deposits are underlain at depth by the Dammam formation of the Upper Eocene Epoch, which are approximately 38-42 million years old. However the normally intervening deposits of the Fars formation are absent except in Northern Kuwait.
The Dibdibba formation typically consists of siliceous sands and gravels, with varying amounts of silt and some thin clay and gypsum bands. Cementation is only partial and relatively poor, consisting of calcium carbonate and gypsum.
In South Kuwait the recent deposits overlying the Dibdibba formation consist chiefly of windblown sand forming sheets and low dune structures. Adjacent to the shoreline, calcareous deposits are present and these generally consist of oolitic and bioclastic sands.
The low seasonal rainfall mostly evaporates or percolates into the ground, so very little runoff drains out to the sea. The influence of evaporation predominates, and the general movement of groundwater is upward. This leads to high concentrations of soluble material near the ground surface, such as calcium carbonate and gypsum. In North Kuwait gypsum predominates, whereas in the South high concentrations of calcium carbonates are encountered near the ground surface.
The new Sheikh Jaber Al-Ahmad Al-Sabah Causeway Project being built across the Bay of Kuwait is a massive engineering project that is costing around US$3 billion in all. This highly complex project involves the design, build, completion and maintenance of the causeway, which spans Kuwait Bay between Kuwait City and the Subiyah area. The 36km Sheikh Jaber Al-Ahmad Al-Sabah Causeway Project (SJSC) is one of the largest and most challenging transport infrastructure projects in Kuwait, as well as the entire Middle East region.
The overall aim of the project is to reduce the travel distance between Kuwait City and Subiyah area from 104-36km, which will cut the journey time from 90 minutes at present to less than 30 minutes.
Building the causeway will provide a new strategic highway route that will help planned development work located to the north of Kuwait City, as it will connect Shuwaikh Port with the Subiya New Town Development. And it will help to integrate the northern areas of the country with more the densely populated central and southern regions, while also helping lower traffic congestion in the surrounding roads.
The client for the project is the Ministry of Public Works (MPW), State of Kuwait, while the link was designed by
The project is extensive and includes the construction of a 27km low-level bridge across the bay, a main bridge with a span of 200m, an elevated road, and a 5km approach road onshore in Subiya. The causeway crosses two artificial islands on its route, Bay Island North and Bay Island South, with project completion expected in 2018. There is also an additional 13km marine bridge connecting with Doha, on the southern side of the bay.
This is a megaproject in any sense of the term and providing stable foundations for the offshore section is essential for the project to be successful, as well as being one of the most challenging aspects of the work. Only with the proper foundations will the causeway be able to cope with the necessary structural loads of the roadway, as well as the surrounding offshore environment and any climactic conditions.
An important first step for the piling work was a highly accurate soil investigation, which was carried out in compliance with recognised geotechnical standards and guidelines to ensure the quality standards required. This investigation was vital to determine the most suitable method of bored piling for the foundations. The recovered data was also used as the basis for a more complex plan for each of the planned phases of the work, as well as including related information to aid in the design of the foundations for the proposed construction.
A drill log was generated for each stage of the investigation, providing important information such as a description of the soil, the location, the elevation, the date of the investigation and the depth. At the Shuwaikh Port end of the route, the ground investigation operation found large quantities of sand in very loose, medium dense and very dense conditions. Meanwhile close to the planned Subiya New Town, the ground investigation showed that there was a combination of very dense sand and very soft to medium clay. Using this data, the engineering team was able to establish what type of bored piles would suit the job.
Trevi Foundations Kuwait is handling much of the offshore piling and onshore piling activities, using specialist equipment from the
The onshore piles are subject to lower stresses and have been designed with diameters of 2.5m. However the offshore piles have to cope with greater loads and as a result, have diameters of 3m, while also reaching greater depths.
The offshore piling operation has faced particular challenges, having to cope with hydrostatic pressure and buoyancy, underwater currents and waves and swells. The length of the causeway means that the pile furthest from shore is 17km out to sea, while there have been other significant challenges also. The tidal variation is very large around Kuwait’s shores and wind speeds can be high, while storms can also be very powerful. Luckily, cyclones are comparatively rare events for Kuwait and there is also comparatively little shipping using the area close to the route of the causeway.
The project features some 1,200 piles in all, with TREVI boring around 230 offshore and these featuring diameters of 3m and reaching depths of 84m. This piling work has been handled from a barge belonging to
The barge is not a self-elevating jack-up type though and once each pile has been bored, it has to be moved to the next location using the anchor boat and a tug. A Soilmec SC-120 rig has been used for constructing the piles, with assistance from a
In addition to the piling barge carrying the Soilmec rig, the excavator and the Kobelco crawler crane, TREVI is also using a disposal barge, a service barge and a rebar cage barge. The disposal barge plays an important role during the drilling phase, as it is loaded with all of the material removed during excavation. Meanwhile the service barge plays a support role for the piling operations, storing all the necessary tools such as the second bucket, the cleaning bucket and hanging bar. As its name suggests, the rebar cage barge is used to store the rebar and this has to be located next to the piling barge.
The piling work involves seven main tasks; driving the casing, excavating, cleaning, placing the reinforcement, flushing, pumping the concrete and installing the pile head. TREVI says it has been careful to ensure quality throughout each of these stages, using a special polymer mud to support the pile sides during excavation and until the casting portion is carried out for example.
To ensure the polymer works effectively, the level has to be kept 3.05m above the piezometric surface at all times. The slurry is also placed in the borehole prior to the piezometric level being reached as this prevent sloughing or ravelling. TREVI says it has used advanced polymeric technologies, as these limit filtration losses. At the same time, care is being taken to maintain a positive fluid pressure on the borehole sidewalls, providing the essential sidewall stability. When the polymer slurry is pumped into the excavation, there is an initial fluid loss into the formation. It is this penetration of the polymer slurry into the porous formation that allows interaction with the soil particles through chemical adhesion, providing the necessary bonding effect and improving the stability of the pile sidewalls. The strength of adhesion however varies between polymer types and can also be affected by the use of different additives, with a wide performance range depending on the combination used.
TREVI says that to ensure that the polymer slurry meets quality needs, clean water is required with pH values ranging from 10-11. Mixing should be homogenous to avoid agglomerates of polymer powders forming, while the fresh slurry should also meet the necessary target for viscosity. The polymer slurry has to be recirculated without the use of centrifugal pumps and recovered from the pile using progressive cavity pumps, while a filtration tank is employed to minimise the sand content. While excavation work is ongoing, the engineering team also have to maintain constant checks on the viscosity, pH value, density and sand content of the slurry so as to ensure quality is optimised. In addition, there are also strict rules on the handling and disposal of polymer slurries as these are subject to environmental regulations.
Most of the casings measure some 40m long, with these being spaced in pairs 10m apart, at a distance of 60m between each pair. TREVI has been installing one pair at a time; first the pile on the east and then the pile on the west, before moving the barge to its next location.
Once each casing is ready and has been checked for position accuracy by a surveyor, the excavation work is carried out. The configuration of the Soilmec rig allows the 2.96m diameter bucket to be rotated in either direction. The bucket design is crucial to the operation as it has lateral openings that allow the polymer slurry to escape as it fills with the excavated material.
Another important piece of equipment that TREVI is using is the polymer compensation tank, which allows the polymer level to be controlled accurately in the casing. This ensures that the pressure is optimised and helps the stability of the pile when it is open.
The spoil from the bucket is dumped into an empty tank, with the excavator then being used to offload the material into the disposal barge alongside. At the end of each separate piling cycle, the disposal barge carries the excavated material to the jetty for recycling. So far the firm is taking around 15 hours for each of the 65m-deep piles.
Once the excavation work has been carried out, TREVI verifies the pile stability using a Koden test. This uses ultrasonic testing, a well proven technology that can determine if there are any collapsed areas or cavities.
Once the pile has been excavated and checked for quality, TREVI then uses a cleaning bucket with no teeth to remove any material from the bottom before installing the rebar cage.
The firm uses different segments, depending on the depth of the pile, though for most three are sufficient. These have to be installed in a very limited space and TREVI says that this stage is extremely tricky. Logistically complex, the position of the components has to be carefully arranged on the rebar barge and with the lightest segment furthest from the crane for this stage to be carried out correctly. And if the segments measure up to 23m as used for the deeper piles, then two cranes are required to lower the rebar cage into place.
The segments themselves are joined using special couplers but the spacing is critical, as the sections cannot be more than 5mm apart. Cleaning of the pile is also critical, using high-pressure compressed air to flush out debris, particularly at the base of the bore. Ensuring that the toe of the pile is clean is highly important as otherwise the structure would not be able to cope with the necessary loads. This flushing is carried out at seven points inside the bore, with each of these stages taking 20 minutes. A hollow pipe is positioned inside the pile, with a side pipe then connected at the end to allow the air to flow. The upper end of the tube then connects to a discharge tank that holds fluid from the pile base. Because the compressed air mixes with the fluid, this becomes lighter and is forced upwards by hydrostatic pressure into the discharge tanks.
Only once the flushing has been carried out fully and the sand content checked, can the concreting process be initiated for the casting process. A special 1.2m diameter cleaning bucket is also used that fits inside the 2.8m diameter rebar cage. This special bucket is able to slip down inside the cage without touching the sides and is used to remove the extra concrete, which is placed inside a special container and transported back to the main contractor.
With the cleaning process complete, a personnel basket is lowered into the pile so that the inside of the pile can be cleaned and the inner surface of the concrete smoothed over. Using this complex process in the challenging offshore environment, TREVI has been able to install three piles/week on average but the firm hopes to increase productivity as it refines the operation further.
All images provided courtesy of
Kuwait geography
The State of Kuwait is situated at the north-eastern corner of the Arabian Peninsula. It comprises an area of approximately 17,800km2. Kuwait has a hot and dry climate. The summer in Kuwait is very hot, especially in July and August and the mean temperature during this period varies from 30-50°C. The winter is cool however, especially in January when the mean temperature is 12°C.
Rainfall in Kuwait totals just 110mm/year while another prevailing climatological characteristic is the frequent dust storm. The contribution of dust sedimentation of the north-western part of the Arabian Gulf is some 1mm/year. The same thickness of deposition is assumed to be taking place throughout the coastal areas of Kuwait.
Pronounced variations in humidity are also common in Kuwait. Relative humidity varies from 60.9% in January to 21.5% in June. On the other hand, evaporation is very high and is variable within location and seasons, allowing a mean amount of evaporation of 10.3mm/day.
Kuwait lies on the eastern edge of the deep sedimentary basin that forms the Arabian Peninsula and is underlain by a considerable thickness of sedimentary rocks. In the south of Kuwait, relatively young deposits of the Dibdibba formation, which are Upper Miocene to Pleistocene Epochs approximately 2-10 million years old, outcrop at the surface. These deposits are underlain at depth by the Dammam formation of the Upper Eocene Epoch, which are approximately 38-42 million years old. However the normally intervening deposits of the Fars formation are absent except in Northern Kuwait.
The Dibdibba formation typically consists of siliceous sands and gravels, with varying amounts of silt and some thin clay and gypsum bands. Cementation is only partial and relatively poor, consisting of calcium carbonate and gypsum.
In South Kuwait the recent deposits overlying the Dibdibba formation consist chiefly of windblown sand forming sheets and low dune structures. Adjacent to the shoreline, calcareous deposits are present and these generally consist of oolitic and bioclastic sands.
The low seasonal rainfall mostly evaporates or percolates into the ground, so very little runoff drains out to the sea. The influence of evaporation predominates, and the general movement of groundwater is upward. This leads to high concentrations of soluble material near the ground surface, such as calcium carbonate and gypsum. In North Kuwait gypsum predominates, whereas in the South high concentrations of calcium carbonates are encountered near the ground surface.