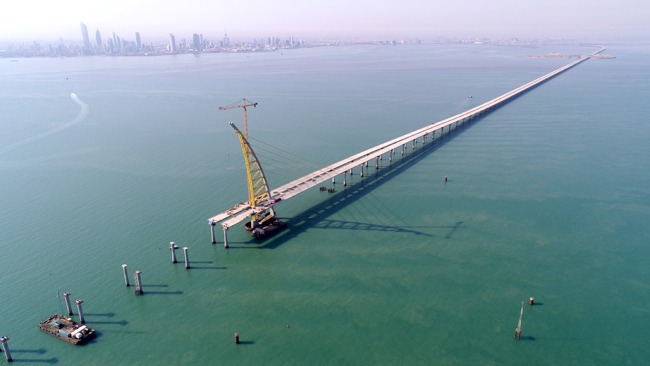
World Highways revisits the world’s fourth longest sea bridge - four years to construct and which has slashed travel time between Kuwait’s largest island and the capital city
Kuwait’s recently opened Sheikh Jaber al-Ahmad Al-Sabah Causeway is a dream come true that the government is hoping will make another dream come true. Kuwaiti media reported in May that the government had inaugurated the US$3.6 billion design-and-build bridge project. It leads from the capital Kuwait City’s free trade zone to an uninhabited area set to become another thriving port - Silk City.
Trade is very important for this oil-rich Arab country of around 4.5 million people on the Persian Gulf – also known as the Arabian Gulf. The tiny country is surrounded by much larger neighbours – not always friendly. The 36km-long Sheikh Jaber Causeway is named after the late 13th Emir of Kuwait to commemorate his contribution to the country’s economic development.
The Madinat al-Hareer - Arabic for Silk City - is a proposed 250km2 urban area in the Subiya region of north-eastern Kuwait, directly north from Kuwait City across Kuwait Bay, also known as Jōn al Kuwayt and at the head of the Persian Gulf. Apart from a free trade zone and seaport, Silk City will have an airport, an Olympic stadium, a tower (taller than Dubai’s Burj Khalifa) and housing for up to 700,000 people. The cost of this long-term mega development is estimated to be more than $100 billion – hence the causeway’s strategic importance to the country.
Local media noted that the Sheikh Jaber al-Ahmad Al-Sabah Causeway, of which 80% is over the waters of Kuwait Bay, is Kuwait’s largest construction project. It also spearheads the country’s economic reform programme entitled Kuwait 2035, whereby the country will move towards a non-oil resource-based economy. Much of the free trade zone development will be done in partnership with China, after the two countries signed memorandums in the past several years. The vision is for the causeway to establish Kuwait as an international trading centre connecting the Middle East with the rest of Asia.
In fact, just before the causeway officially opened, the Kuwaiti government announced in February an $86 billion first phase of construction for the Silk City. The announcement came after a visit to Kuwait by a 35-member high-level Chinese government delegation that included Ning Jizhe, vice chair of the Chinese National Development and Reform Commission,
Causeway
The causeway was designed by Paris-based engineering and consulting group
The overall project has a 100-year service life and entails nearly 49km of road and bridge work. The 36km Subiya Link starts at Kuwait City’s free port area and runs north across the bay to the shore of the Subiya region – costing $2.3 billion. It cuts the 90-minute journey along 104km of coastal roads to around 30 minutes. Works included 3km of onshore bridge structure and roads in Shuwaikh and 6km of onshore bridge work in the Subiya region.
The 12.4km Doha Link runs from the city’s free port westward across a minor bay – 4.5km over the water - to the Doha area of the capital city region, all for $545 million.
The causeway carries dual carriageways, each 17m wide for three traffic lanes, an emergency lane and a hard shoulder. Two artificial islands – one 300,000m² and the other 600,000m² - were constructed to support the causeway across the bay.
The bridge incorporates a supervisory control and data acquisition (SCADA) system that tracks activity on the bridge. It operates with around 600 cameras to observe traffic movements and any emergency issues. The system also has software and sensors to detect cracks in the concrete superstructure and act as a weigh-in-motion system to detect vehicle weights should there be limits for safety reasons. Importantly from a design perspective, many of the electrical substations and equipment for the SCADA systems and other electronics for the bridge are inside the bridge decks' structures. This keeps them away from the highly corrosive environment outside.
Dar Al-Handasah worked as lead consultant on the project working alongside Dar Group sister companies
Main bridge works
The main bridge has the longest span on the project - 177m from pier to pier. Underneath there is a 120m-wide navigation channel with a 23m vertical clearance at high tide. It has a composite concrete-steel truss pylon structure with twin orthotropic slab decks.
The causeway is largely of concrete piles, piers and superstructure. However, the superstructure deck of the main bridge is mainly steel which received layers of waterproofing membrane and asphalt. The 340m of orthotropic slab decks forms a light deck that allows for longer spans than concrete deck slab. A similar steel deck was used in the Bay Bridge in Oakland, California.
The steel deck and the orthotropic deck were manufactured and mostly assembled in South Korea, with additional elements attached in Kuwait. The main bridge deck consists of precast concrete girders, each with a length of 60m; two prefabricated steel girders, each with a length of 82m; and hybrid (steel/concrete) girders with lengths 2x64m and 2x74m. The girders are rigidly attached to the pylon through two connecting cross beams and are free to move longitudinally where guided sliding pot bearings are installed.
Hot, hot, hot
Dar’s brief from for Kuwait’s Public Authority for Roads & Transportation (PART) was to ensure a 100-year service life in a challenging coastal marine environment. This challenging environment – extremely hot and extremely dry - was also an issue during construction, according to Dar. Summer temperatures can rise to dangerous levels - reaching on occasion 50° - for people working on a construction site. High winds and fast approaching powerful storms are also common. Humidity can range from around 60% in the coolest month January to as low as 21% in June, the hottest month.
To avoid health and safety risks to the workforce of nearly 7,000 at times, shifts took place only in the early hours of the morning and at night when temperatures were relatively cooler than mid-day during June to September. Arrays of high-powered lights were used to assist night work and special shields against the sun to create shade were erected when space would warrant it.
Health and safety was also a concern regarding the bay’s world-renowned Green Tiger Shrimp that is collected by local fishermen. Hyundai said that it took the utmost care to preserve the bay’s ecosystem during construction. The company created an alternative breeding area. This entailed 1,000 rock and reef blocks to create a habitat that would draw the shrimp away from construction sites – a very successful strategy that allowed continued harvesting of the delicacy throughout the construction years.
There also was needed some delicate public relations to be done with the extremely curious local fishermen keen to see what was going on. Many would sail perilously close to construction work so they had to be warned of the dangers and kept well back.
The main bridge rests on concrete piles between 33m and 60m long. The piles are connected at their top levels with pile caps cast in dry conditions under sea level using precast reinforced concrete shell forms with circular and square cross sections (PC-houses). Each of the two prefabricated circular PC-houses weighed 1,800tonnes, were 23m in diameter and had a 13m wall height.
Pylon engineering
The pylon design in the form of a 151m-high sail is a reference to the traditional boats used in Kuwait. The arche is already a landmark appearing in the middle of Kuwait Bay. The front section of a the “sail” has a variable section of concrete (half-circle 7.2m diameter at the base) connected by a steel truss to the steel back frame of the pylon.
The pylon itself is constructed of a composite system of concrete column connected to a steel truss by way of steel horizontal and diagonal members. While it is common to have concrete or steel pylons for cable-stayed bridges, what is not common is the composite nature of this pylon. The curved steel yellow members mimic the shape of the old sails.
The main span girders are suspended by eight pairs of stay cables anchored to the concrete leg of the pylon and to the connecting cross beams between the west and east deck girders. The pylon’s structural system is uncommon in that it is not stabilised longitudinally by the traditional back stays. The truss structural system of the pylon enables the omission of traditional back stays.
The longest stay cable on the main span side includes 72 high-strength 7-wire strands with ultimate capacity of 2,000tonnes, a length of 248m and an external diameter of 250mm. The shortest stay cable has 55 strands with a maximum capacity of 1,500tonnes, a length of 38m and an external diameter of 200mm.
There is also a pylon maintenance cradle constructed to give access to the entire outside surface of the pylon. Strain gauges were provided in the pylon legs and pylon foundations. Steel temperature sensors and other impact sensors are provided on the pylon and are part of the overall structural health monitoring system as part of the SCADA installation.
Sail on
The main cable-stayed bridge has a main span of 177m that creates a navigation channel 120m wide and 23m high to enable access to Kuwait’s Doha Port. A 151m-high pylon supports the main bridge - inspired in its shape by a traditional sailboat and which uses hybrid concrete and steel structural trusses. Side and main spans of the superstructure are girders made of precast concrete and prefabricated steel.
The causeway is one of very few bridges in the world that houses electrical rooms inside a bridge box girder. This is so unusual a design that finalising its approval from the Kuwait’s ministry of electricity was “a challenge”.
The main risk to the construction of this type of project is the durability of the equipment used to install girders. Breakdowns and maintenance downtime can cause major headaches in such a hostile working environment. On the causeway project, it was a great achievement not to have any equipment breakdowns which allowed completion of girder installation on schedule. Also, stainless steel reinforcement used for concrete elements is subject to oxidation.
The project was completed on budget. It is rare, notes Dar, that a project of this size is completed without major claims and requests for variation orders. Any claims for adjustment from the contractor during the close out phase are unlikely to be major. The main issue is that there were no claims to derail completion of the project.
Dar Al-Handasah Group
The role of Middle East-based Dar Al-Handasah (Shair and Partners) as lead consultant:
- Construction supervisor;
- Engineer’s representative;
- Led detailed design review on transportation, GIS, environmental, geotechnical and marine works.
Dar Group’ sister companies TY Lin International, Ross & Baruzzini were part of the consultant team:
- TY Lin led the design review of the bridges’ superstructure and substructure and coordinated the design review of the foundations with Dar Al-Handasah;
- Ross and Baruzzini reviewed the design of the systems;
- Dar Al-Handasah along with Ross and Baruzzini are helping PART/MPW to establish the tolling system for the causeway.
Meanwhile, local consultant SSH reviewed the design of the buildings and grade works.
Who’s Who
Client – Kuwait Ministry of Public Works;
Consultants - Dar Al-Handasah Consultants (Shair and Partners), SSH and TY Lin International;
Contractor for Subiya Link – A consortium of Hyundai Engineering & Construction and Combined Group Contracting;
Contractor for Doha Link -
Design for Subiya Link - SYSTRA;
Design for Doha Link - Tony Gee and Partners;
ICE for Subiya Link -
ICE for Doha Link - SYSTRA;
Foundations - TREVI Foundations Kuwait and
Structural and Bridges design review - TY Lin International;
SCADA and intelligent systems review - Ross & Baruzzini;
Also playing major parts were German photonics and light and safety group