The second tube of the Pfänder Tunnel, Bregenz, Austria, where the new main tunnel has been excavated using a tunnel boring machine (TBM), is being constructed by Alpine BeMo Tunnelling.
Tubbings have been installed as the inner tunnel lining, and as part of concreting for the inner shell, the FQ 1 crosscut, suitable for vehicles, is being constructed using a tunnel formwork carriage designed and supplied by PERI.
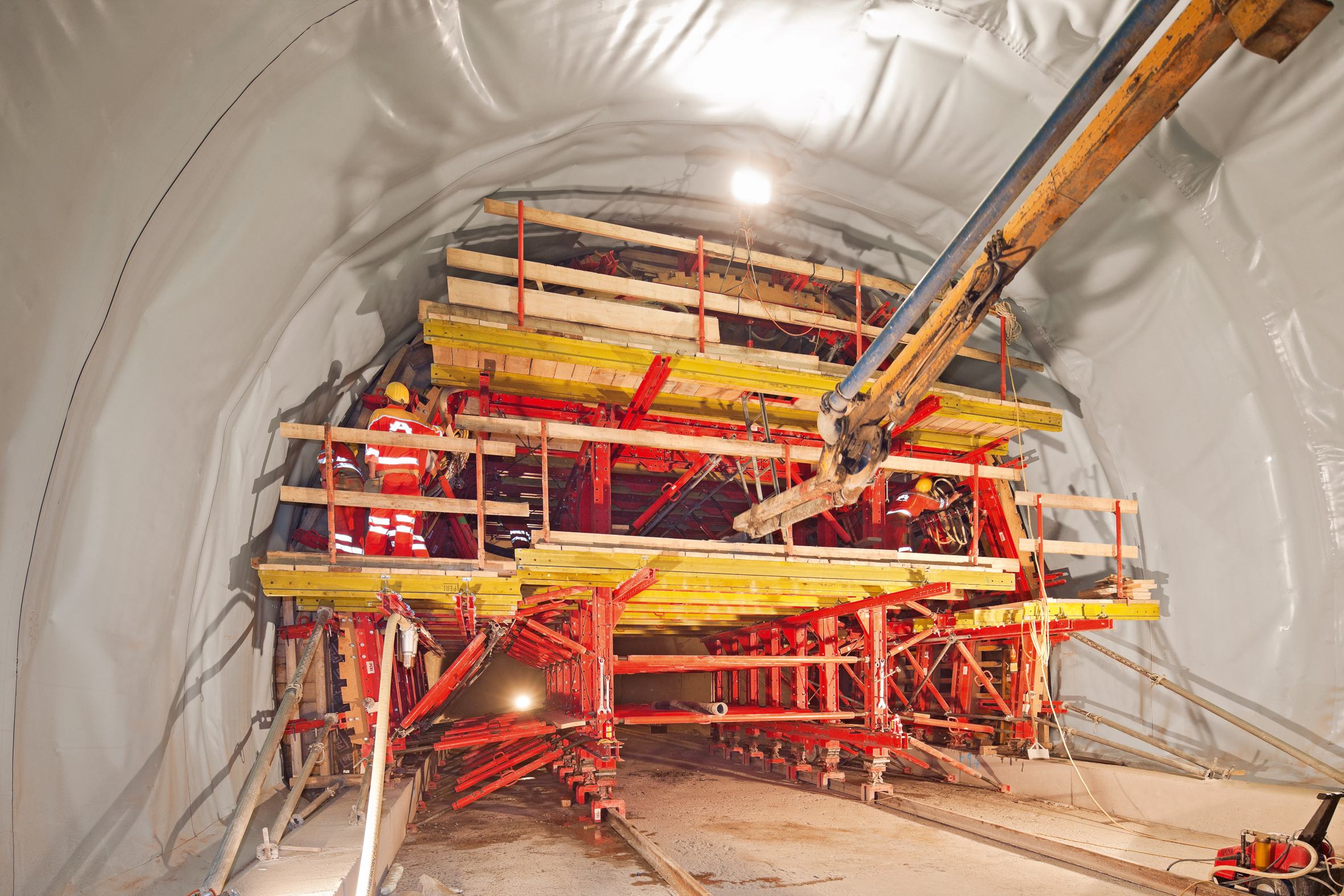
The high proportion of system components provided a cost-effective solution for the short tunnel structure
The second tube of the Pfänder Tunnel, Bregenz, Austria, where the new main tunnel has been excavated using a tunnel boring machine (TBM), is being constructed by Alpine BeMo Tunnelling.
Tubbings have been installed as the inner tunnel lining, and as part of concreting for the inner shell, the FQ 1 crosscut, suitable for vehicles, is being constructed using a tunnel formwork carriage designed and supplied by298 PERI.
The existing Pfänder Tunnel, commissioned some 30 years ago, cannot cope with the increase in the traffic volumes, so the parallel, two-lane tube is being constructed. Over 14 months, the almost-12m diameter TBM drilled 6,600m through the Pfänder Mountains to form the main tunnel, which was lined with precast segments.
In case of fire, 31 connecting passageways between the old and new tunnel tubes for evacuation purposes are planned. For the most important, the 43.1m long FQ 1 crosscut, PERI created a tailored formwork solution consisting mainly of rentable VARIOKIT system components. The other crosscuts will have shotcreted inner shells.
A total of seven round-shaped wall formwork elements were prefabricated by PERI and supplied just-in-time to the construction site, thus minimising assembly time. After only 1.5 weeks of on site assembly, the construction tea
started work on the segments, with standard lengths of 5.9m. After a short period of introduction, a three day cycle could be achieved for these sections. Construction of the last two 3.35m long segments required two days respectively.
Tubbings have been installed as the inner tunnel lining, and as part of concreting for the inner shell, the FQ 1 crosscut, suitable for vehicles, is being constructed using a tunnel formwork carriage designed and supplied by
The existing Pfänder Tunnel, commissioned some 30 years ago, cannot cope with the increase in the traffic volumes, so the parallel, two-lane tube is being constructed. Over 14 months, the almost-12m diameter TBM drilled 6,600m through the Pfänder Mountains to form the main tunnel, which was lined with precast segments.
In case of fire, 31 connecting passageways between the old and new tunnel tubes for evacuation purposes are planned. For the most important, the 43.1m long FQ 1 crosscut, PERI created a tailored formwork solution consisting mainly of rentable VARIOKIT system components. The other crosscuts will have shotcreted inner shells.
A total of seven round-shaped wall formwork elements were prefabricated by PERI and supplied just-in-time to the construction site, thus minimising assembly time. After only 1.5 weeks of on site assembly, the construction tea
started work on the segments, with standard lengths of 5.9m. After a short period of introduction, a three day cycle could be achieved for these sections. Construction of the last two 3.35m long segments required two days respectively.