Increasingly, and where possible, roads are being built in tunnels often for environmental reasons, writes Patrick Smith As part of the new M7 motorway development in the southwest of Ireland, the four-lane route crosses the River Shannon near Limerick, before it flows into the Atlantic. Centrepiece of the 10km long Limerick Southern Ring Road is the required tunnelling (675m long), which including the north and south entrance and exit ramps, means it will be 915m long. Completion of the work is planned for
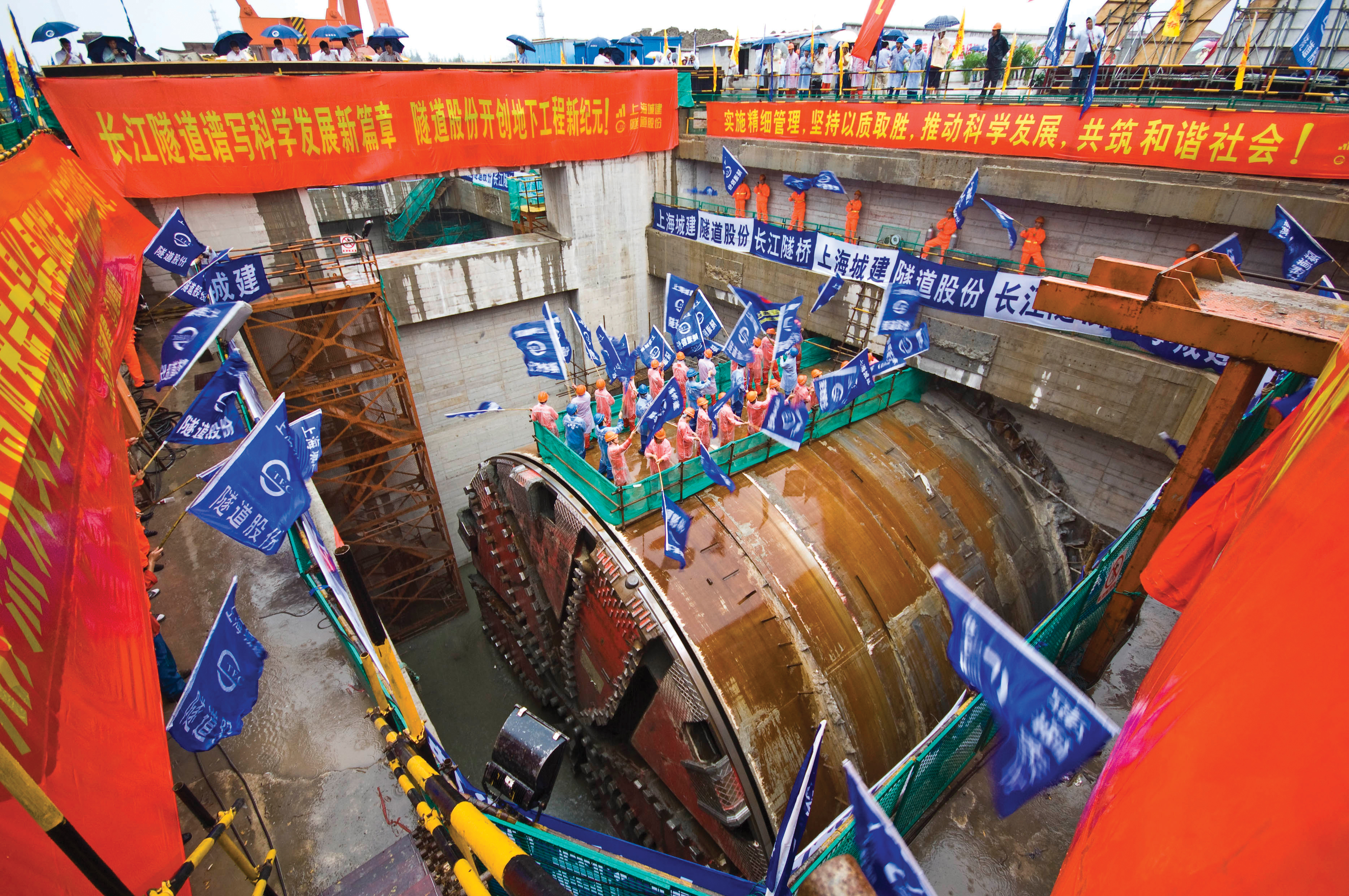
The ceremony on the occasion of the breakthrough of Herrenknecht Mixshield S-3 18
Increasingly, and where possible, roads are being built in tunnels often for environmental reasons, writes Patrick Smith
As part of the new M7 motorway development in the southwest of Ireland, the four-lane route crosses the River Shannon near Limerick, before it flows into the Atlantic.Centrepiece of the 10km long Limerick Southern Ring Road is the required tunnelling (675m long), which including the north and south entrance and exit ramps, means it will be 915m long. Completion of the work is planned for Autumn 2010, and the DirectRoute consortium together with construction company
Formwork and scaffolding specialist,
At the same time, in the area of the south portal, an additional tunnel section is planned, to be completed in six cycles. This takes place using the cut-and-cover method. Due to the few concreting sections to be completed and the short rental period involved, the PERI VARIOKIT modular construction system is selected.
For both solutions, identical double-tube rectangular cross-sections are semi-monolithically constructed in each case, whereby the bottom plate is completed first and then the walls and slabs are concreted in one pour. The two tubes are each 10m wide and 6m high.
For the immersed tunnel, a total of five tunnel elements (each 100m long) are completely prefabricated using a 600m long, 33m wide dry dock positioned at the north portal, and then sealed off by means of bulkheads at the ends. After flooding the dock, the 100m x 25m x 8.5m metre reinforced concrete precast segments, each weighing 20,000tonnes, are floated out and lowered into the exact position in a specially prepared channel on the river bed. The floating and sinking procedures take place by means of a hoisting system and integrated ballast tanks. A hydraulic line and pumping system, which independently fill and empty the eight tanks inside the tunnel tubes with water, provide the required lateral trim during transportation and the lowering process.
With the two PERI tunnel formwork carriages, these elements (five, 20m long concreting cycles) can be manufactured in six-day cycles.
The PERI stopend formwork accommodates the water stops for the casting joints between the individual 20m sections, while with the other version the element joint at the ends of each 100m tunnel element is a solid steel frame for the large-volume sealing profile (a so-called Gina profile) which is integrated into the PERI stopend formwork.
Excavations complete Two
The 7,472m long tunnels connect the Shanghai district of Pudong with Changxiang Island, and have been excavated in only 20 months. A bridge connects Changxing and Chongming, which is currently connected with Jiangsu Province to its north. Located at the Yangtze River mouth, Chongming covers about 20% of Shanghai's total land area, and experts say poor traffic links between Shanghai and Chongming have blocked the development of the island. Construction of the bridge and tunnel will help attract overseas investment and make it a major development area for the Yangtze River Delta.
The tunnel has an inner diameter of 13.7m and it forms part of the US$1.84 billion bridge and tunnel connection. It will house a six-lane expressway and a rail line.
The Herrenknecht Mixshield S-318 reached its target in September having excavated the tunnel tube in highly water-bearing construction ground. Earlier the identical Herrenknecht Mixshield S-317 reached its target shaft "with great precision".
Using the two high-tech giants from Schwanau in Germany, the shell of the two parallel running large diameter tunnels, which are scheduled to be opened for car and subway traffic for the 2010 World Exhibition in Shanghai, could be completed 10 and 12 months ahead of schedule respectively.
"With an overburden of up to 65m, the machines burrowed their way through sand, clay and groundwater with water pressures of up to 6.5 bar. Weekly tunnelling performances of up to 142m of constructed tunnel were reached, performance per day was up to 26m," says Herrenknecht.
"The teams operating the TBMs directed the 2,300tonne and 125m long colossus with highest precision. On a route of 7.5km, they deviated only 2.7cm from the ideal line."
From 2010 onwards, the combined road and subway tunnels will reduce the travelling time between Shanghai and Changxing from 1 hour to 20 minutes and replace the existing ferry.
"The breakthroughs constitute an impressive success for both the Changjiang Tunnel & Bridge Construction and the partnership between Shanghai Tunnel Engineering,
Scheduled to open to traffic in 2010, the new bypass is intended to permanently alleviate traffic congestion in the city centre.
Part of the bypass road will run in a tunnel 10m beneath sea level and 505m long. It is being built by Bilfinger Berger using the separate (non-monolithic) casting method, with two fully rentable travelling tunnel formwork units from Austrian company Doka. These are based on standardised rentable system components, and are fitted with Wall formwork FF 20 and rugged Doka 3-SO formwork sheeting.
The construction trench is inside a sheet pile coffer dam with walls up to 16m high. Following completion of the in situ concrete base slab, the tunnel walls and the cover slab are poured in a single operation using the Doka travelling tunnel-formwork units, in 12.5m long sections cast in a weekly cycle.
After each casting section has been completed, the entire formwork construction is backed off the concrete by hydraulic cylinders and travels on rails to the next casting section. Varying by up to 2m in height and width, the tunnel cross-section makes great demands of the formwork construction in terms of its adaptability.
Interchangeable and compensating elements are incorporated here to ensure precise, rapid adaptation to this varying cross-section. Both tunnel approach ramps are being formed using extra-large elements of Large-area formwork Top 50.