Formwork solutions for the first axial suspension cable stayed bridge in India; and a four-lane road bridge in Germany’s Harz Mountains, are among the latest bridge-based formwork projects analysed by Guy Woodford. RMD Kwikform India has won the contract to design and supply shoring and formwork solutions for the first axial suspension cable stayed bridge ever built in India. The Kota Bridge’s innovative design sees a single 350m span cross the entire width of the Chambal River, with three approach spans on
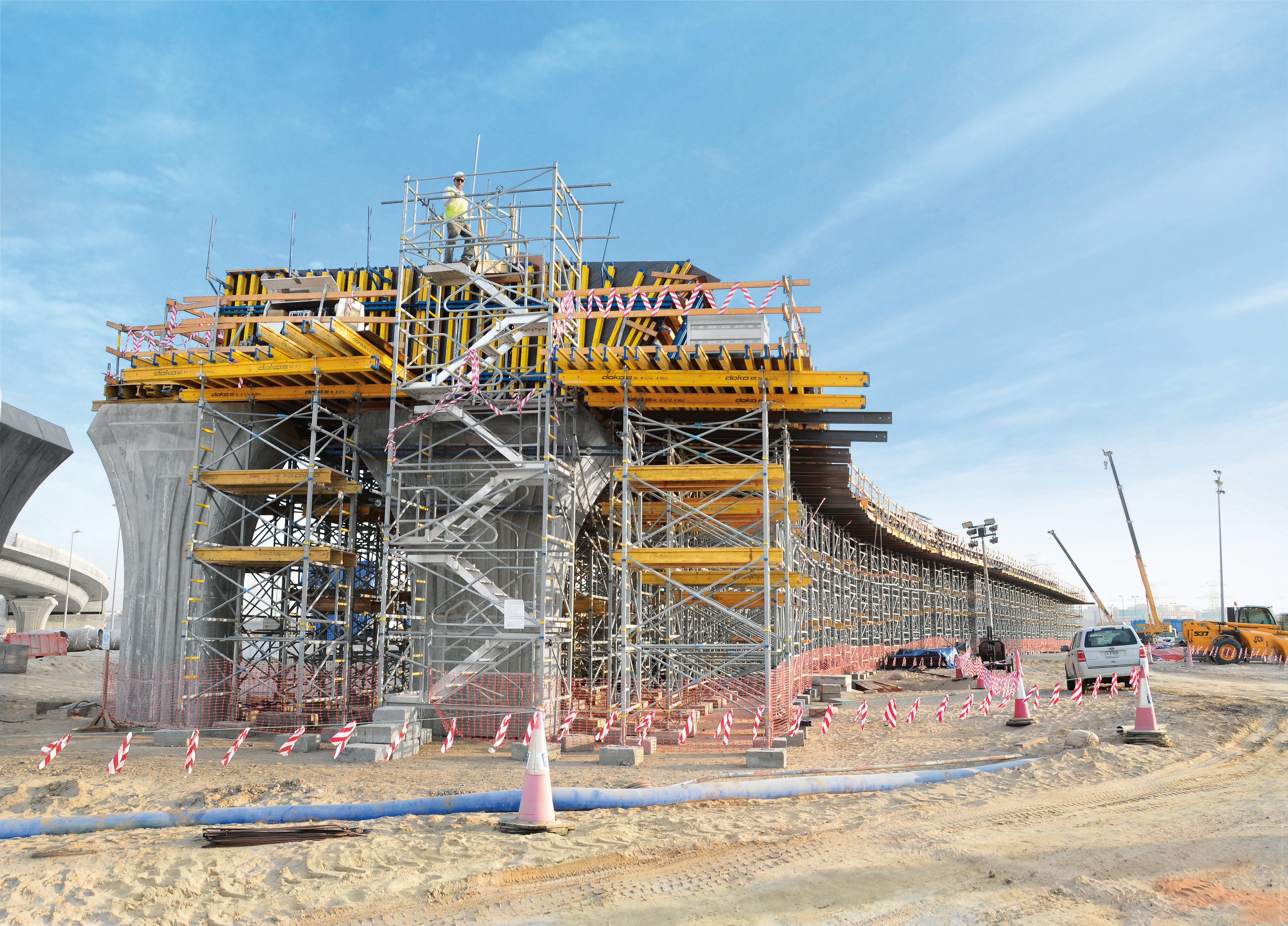
RMD Kwikform India is providing formwork for the Kota Bridge
Formwork solutions for the first axial suspension cable stayed bridge in India; and a four-lane road bridge in Germany’s Harz Mountains, are among the latest bridge-based formwork projects analysed by Guy Woodford
The Kota Bridge’s innovative design sees a single 350m span cross the entire width of the Chambal River, with three approach spans on either side. It is these approach spans that will feature RMD Kwikform shoring solutions.
RMD Kwikform’s ultra-heavy duty Megashor shoring has been chosen as the support system for the 32m high, 32m wide and 60m long main deck of the approach spans. Having to deal with local wind conditions, Megashor is also said to have the ability to cope with the dead weight of the deck itself.
A combination of Superslim, GTX Beams and specially designed crank soldiers are to be employed on the cantilever wing form, while the pier cap will be constructed using a Rapidshor system.
The bridge will be finished by the end of 2014, with RMD Kwikform completing its involvement in August 2013, just 13 months after starting work on the project.
Arul Raja, Vice President at RMD Kwikform India, said: “In supplying formwork and shoring solution to the Kota Bridge we have worked in partnership with construction firms Gammon India and
“RMD Kwikform’s involvement in a project of this significance further demonstrates its ongoing commitment to supporting large scale projects in India.”
This 496m long steel composite bridge is being built with a massive 20.36m wide and up to 58cm thick deck slab. The deck slab has a 6% longitudinal gradient and a transverse gradient of as much as 5%. Meanwhile, the S-shaped roadway has curve radii of 400m and 600m. These extreme specifications, and the fact that the roller-trestle bearing supports are spaced between 3.78m and as much as 4.9m apart, mean that the deployed composite forming carriage has to deal with some unusual and widely varying load conditions.
The first 346m of the bridge roadway, which is being cast in a back-step sequence, takes the form of a right-hand bend with a 400m radius. After this comes a 123m long spiral transition curve into a near 27m long left-hand bend, with a radius of 600m and a corresponding change in the transverse gradient. This section of the structure crosses a designated fauna/flora habitat zone with the only bridge construction of its kind in Germany, consisting of two steel half-arch superstructures with a total length of 130m.
Various different distance-pieces and shims are used on the roller-trestle bearing-supports to compensate for the varying transverse gradient of the structural steelwork and to keep the 25m long composite forming carriage aligned in the horizontal. The 24 casting segments, each a maximum of 23m in length, are being poured in a ‘back-step’ sequence. Doka said that because every single casting segment has a different radius and transverse gradient to the one before it, the carriage was designed to cope with many different load situations. To minimise the work needed for these repeated modifications to the composite forming carriage, its constructional design, consisting almost entirely of rentable system components, has only one type of curve segment per longitudinal beam. This is said by Doka to enable every single modification to the composite forming carriage to be carried out quickly and easily.
Doka formwork instructor Sven Mazalla is assisting site workers with project-related advice and consultation. The job of assembling and dismantling the composite forming carriage has been contracted out to the Doka formwork pre-assembly team.
In Dubai, in the United Arab Emirates (UAE), Jumeirah Lake Towers is a collection of high end residential and office buildings located opposite the Dubai Marina on the other side of the Sheikh Zayed Road.
The development has flourished since the handover of many luxury buildings a few years ago, and this year further local road works have taken place. With the launch of Doka’s new UAE onsite assembly service, commissioned by contractors Ghulam Rasool & Company, the Austrian firm is now heavily involved in a revived project for comprehensive improvement of parallel roads.
The road bridge NW-01 near Dubai Marina comprises four post-tensioned, dual-celled spans with an average support height of 6.5m. Doka’s formwork supply covers the full scope such as shoring, bottom slab, wing and internal walls, intermediate diaphragms, cantilever and top deck slabs.
Doka’s Dubai branch of its onsite assembly service is said to be providing pioneering new services in the scope of work to coordinate onsite formwork erection and assembly and ready to use preassembly. The service is also co-ordinating the use of heavy equipment onsite needed to deploy and manoeuver formwork.
Ghulam Rasool is said to have been highly impressed by the advantages of Doka’s load-bearing tower Staxo 100 in bridge building. Additionally, Doka’s preassembled large-area formwork Top 50 wall shutters with engineered and specially fabricated steel parts greatly were said to have reduced the quantity of fabricated timber elements required to form the road bridge’s shape. Finally, Doka provided a special suspended solution that made the repositioning process faster than conventional de-shuttering sequences.
Khalid Mehmood, road bridge NW-01 project manager at Ghulam Rasool, said: “Since this project was our first entry into the infrastructure market in UAE, we could not take any risks on satisfying the client. Formwork was a big factor, and the combination of Doka’s proximity to the site, onsite assembly, and ready-to-use services thus far have saved us a lot of resources and time.”
The expansion of the Panama Canal is currently the scene of the largest building site in the world with the two lock systems being the key elements in the whole project. The two facilities, on the Atlantic and Pacific sides respectively, are each around 1,800m long and are expected to be completed at the turn of the year 2014/2015.
In three lock chambers positioned one after the other – each 403m long and 55m wide – ships overcome a height difference of around 26m on the Atlantic and Pacific coast. This procedure is controlled by four lock gate installations. Further construction features – each parallel to the locks – are the three huge economising basins. These serve the purpose of reusing about 60% of the water required for individual lock operations.
More than 12 months after the start of construction, the extraordinary dimensions and the massive structural elements are clearly visible. In order that the tight schedule can be maintained, over 4,200 site personnel process 6,300 m³ of concrete on a daily basis in two shifts.
Construction site facilities include 70 cranes and 30 concrete pumping stations. Furthermore, an immense need for formwork and scaffolding material along with a comprehensive overall concept is still required. With an international team of engineers from the PERI subsidiaries in Spain, Panama and Italy as well as PERI headquarters in Weissenhorn/Germany, PERI provides the consortium of building contractors with an ideal combination of formwork know-how together with the efficiency and ability to deliver as well as innovative system equipment.
The largest single order in the 40-year history of PERI is said by the firm to be not only a challenge in terms of know-how together with performance and the ability to deliver, but it is also a matter of real teamwork: PERI Spain and the PERI subsidiary in Panama – founded in 2008 – are responsible for the formwork planning, logistics and on-site assistance, while PERI engineers from Weissenhorn, Germany provide their colleagues with expert support for all tasks. In time for the start of construction work in 2011, the required system equipment was produced within a few months and then shipped to Central America in more than three hundred 12m containers.