Sydney now has a renovated airport runway thanks to contractors Antoun Civil Engineering and Volumetric Concrete Australia. The airport is a major facility as it is the international hub for airlines like Jetstar Airways and Qantas and handles around 37 million travellers each year, with almost 300,000 aircraft movements. Wear was an issue and the decision was made by the Sydney Airport Corporation Limited (SACL) to replace the concrete slabs that make up the runway system. Originally constructed in the 195
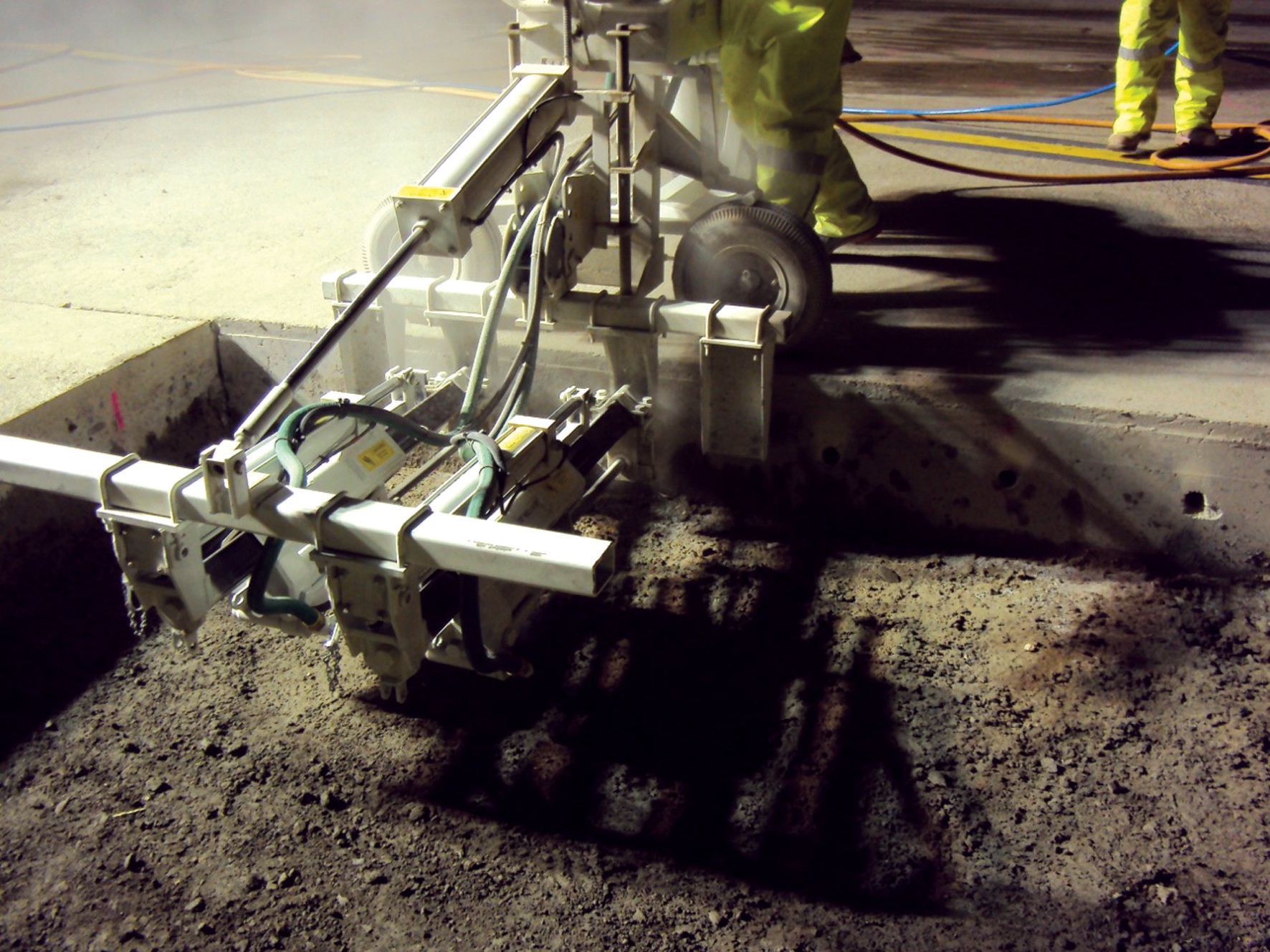
Drilling was carried out at night-time so as not to disturb air traffic
Sydney now has a renovated airport runway thanks to contractors Antoun Civil Engineering and Volumetric Concrete Australia. The airport is a major facility as it is the international hub for airlines like Jetstar Airways and Qantas and handles around 37 million travellers each year, with almost 300,000 aircraft movements. Wear was an issue and the decision was made by the Sydney Airport Corporation Limited (SACL) to replace the concrete slabs that make up the runway system.
Originally constructed in the 1950s, Sydney Airport runways and taxiways are made up of grid-oriented concrete, and a number of concrete pavement slabs at the intersection of the main taxiway and runway 16R were identified as the areas that required immediate replacement. The Plan was to tackle each slab systematically and replace all damaged areas over the course of a few weeks.
7530 Antoun Civil Engineering and 7531 Volumetric Concrete Australia accepted the job, and got to work. Among the list of obstacles along the way were the sheer quantity of work that needed to be done, the fact that the work could only be performed during runway shutdown and curfew hours (between 11:00pm and 4:30am) so as not to disrupt the airport’s scheduled movements. Should the runway be unable to reopen on time, Antoun Civil Engineering would face massive penalties.
“I’m confident enough in my team that I knew we would be able to handle anything the job threw at us,” explained Robert Antoun, of Antoun Civil Engineering. “We just needed a system, so we all sat down, put our heads together and plotted the course of the project.”
Faced with tough time constraints to carry out complex tasks before the airport runway reopened each morning, Antoun Civil Engineering and equipment dealer, Volumetric Concrete Australia, implemented an innovative process that they call the rapid replacement method. The process involves: complete demolition of the area to be replaced; drilling; pouring; and curing. Using this process, Antoun Civil Engineering was able to replace up to three slabs/night, working six nights/week. The project team had to race against the clock every night, hoping that the concrete would achieve complete structural strength before the runways reopened. Methodology and meticulous planning meant that the project remained on track.
Key machines used included two dowel pin drills from Minnich Manufacturing; an A-1C-48, and an A-2C-48 equipped with the optional dust collection system. These were vital to the success of the project. The drills were used for drilling the 36mm diameter holes in the existing slabs for dowel bars to be inserted before pouring the fresh concrete.
Antoun said, “We were able to drill the holes that we needed in existing slabs in about 45 seconds/hole for the single drill unit, and two holes in the same amount of time for the double-gang unit. Safety also came into play for us – we really didn’t want our guys down on the ground manually drilling the dowel-pin holes.”
On each slab to be replaced, Antoun’s crew had to drill approximately 45 holes. It worked out where the operators were able to work through the drilling requirements of a panel in about 35 minutes with the single-gang drill, and about 20 minutes for the double-gang drill. The crew averaged three panels/night and were able to meet the project’s schedule.
The company now plans to apply this same rapid replacement method for similar projects moving forward, due to the success of the operation.
After two and a half weeks of the tough schedule, working six nights/week and facing numerous challenges, Antoun Civil Engineering had completed the project ahead of time and under budget. Sydney Airport now has improved runway surfaces that will better handle the heavy air traffic volumes passing through the facility.
Originally constructed in the 1950s, Sydney Airport runways and taxiways are made up of grid-oriented concrete, and a number of concrete pavement slabs at the intersection of the main taxiway and runway 16R were identified as the areas that required immediate replacement. The Plan was to tackle each slab systematically and replace all damaged areas over the course of a few weeks.
“I’m confident enough in my team that I knew we would be able to handle anything the job threw at us,” explained Robert Antoun, of Antoun Civil Engineering. “We just needed a system, so we all sat down, put our heads together and plotted the course of the project.”
Faced with tough time constraints to carry out complex tasks before the airport runway reopened each morning, Antoun Civil Engineering and equipment dealer, Volumetric Concrete Australia, implemented an innovative process that they call the rapid replacement method. The process involves: complete demolition of the area to be replaced; drilling; pouring; and curing. Using this process, Antoun Civil Engineering was able to replace up to three slabs/night, working six nights/week. The project team had to race against the clock every night, hoping that the concrete would achieve complete structural strength before the runways reopened. Methodology and meticulous planning meant that the project remained on track.
Key machines used included two dowel pin drills from Minnich Manufacturing; an A-1C-48, and an A-2C-48 equipped with the optional dust collection system. These were vital to the success of the project. The drills were used for drilling the 36mm diameter holes in the existing slabs for dowel bars to be inserted before pouring the fresh concrete.
Antoun said, “We were able to drill the holes that we needed in existing slabs in about 45 seconds/hole for the single drill unit, and two holes in the same amount of time for the double-gang unit. Safety also came into play for us – we really didn’t want our guys down on the ground manually drilling the dowel-pin holes.”
On each slab to be replaced, Antoun’s crew had to drill approximately 45 holes. It worked out where the operators were able to work through the drilling requirements of a panel in about 35 minutes with the single-gang drill, and about 20 minutes for the double-gang drill. The crew averaged three panels/night and were able to meet the project’s schedule.
The company now plans to apply this same rapid replacement method for similar projects moving forward, due to the success of the operation.
After two and a half weeks of the tough schedule, working six nights/week and facing numerous challenges, Antoun Civil Engineering had completed the project ahead of time and under budget. Sydney Airport now has improved runway surfaces that will better handle the heavy air traffic volumes passing through the facility.