In Kansas, specialist contractor Pavers has carried out important work for the National Guard. The aim of the work was to rehabilitate a WWII era hangar apron for the Kansas National Guard. The project required extensive repair work, including pavement patching, dowel bar retrofitting, partial depth patching and joint sealing. Pavers had to overhaul a 305m x 91.5m apron at Army Aviation Support Facility No 2 that suffered from poor drainage. The project included milling 152mm of old asphalt and concrete and
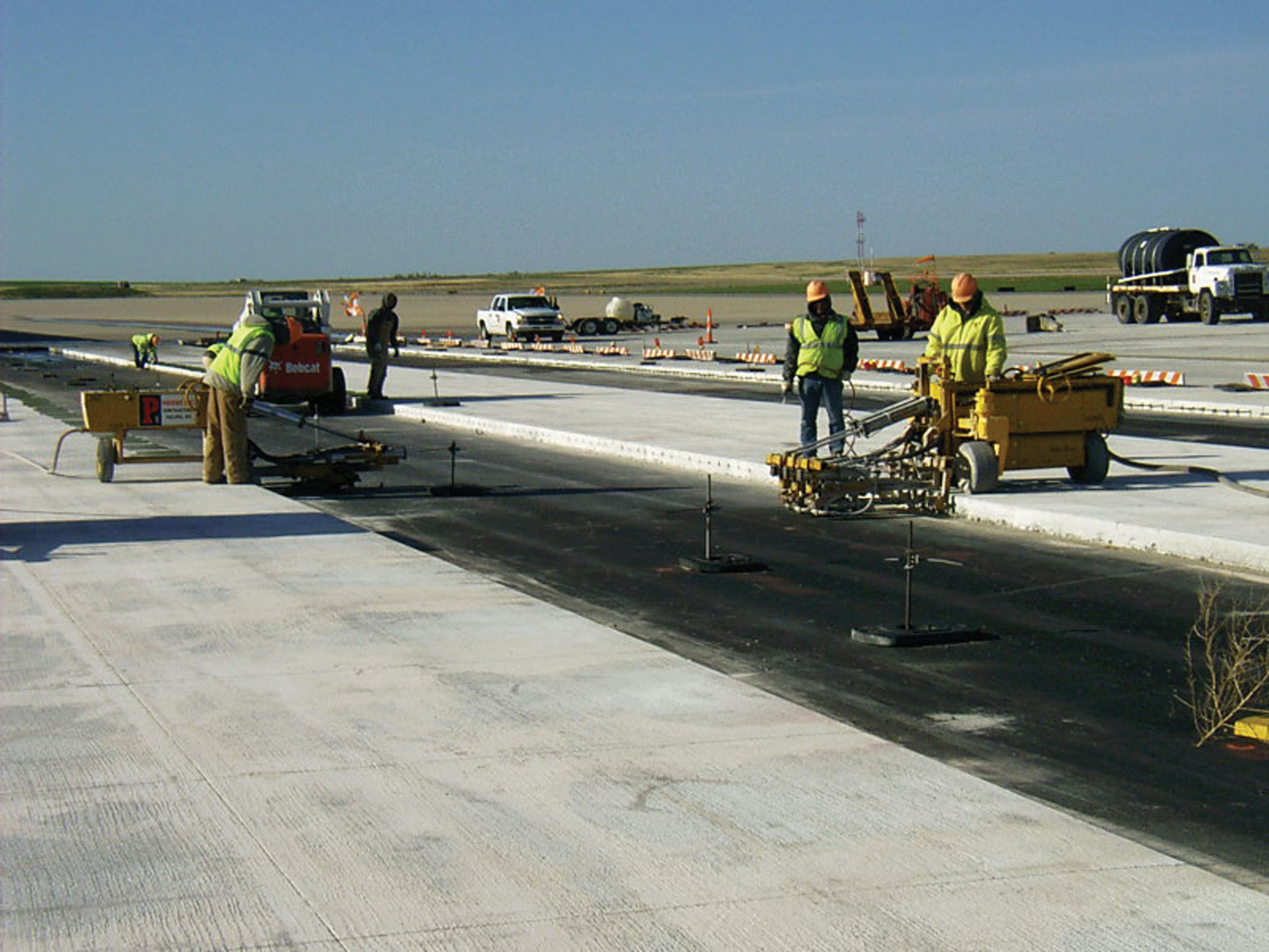
In order to keep on the tight schedule, contractor pavers needed to drill two lanes at a time and more than 32,000 holes were required
In Kansas, specialist contractor Pavers has carried out important work for the National Guard. The aim of the work was to rehabilitate a WWII era hangar apron for the Kansas National Guard. The project required extensive repair work, including pavement patching, dowel bar retrofitting, partial depth patching and joint sealing. Pavers had to overhaul a 305m x 91.5m apron at Army Aviation Support Facility No 2 that suffered from poor drainage. The project included milling 152mm of old asphalt and concrete and replace it with a fresh concrete overlay.
For the dowel drilling work Pavers used pneumatic equipment from Oklahoma-based
Pavers employed the E-Z Drill Model 210B-2 SRA, a two-gang slab rider drill, and the Model 210B-3 SRA, a three-gang version, to drill the thousands of 2.22mm diameter, 457mm deep holes needed for the project. Once Pavers had each lane’s holes drilled, it epoxied the dowels into place and finished off the lane with fresh concrete.
Having the right equipment and experience had Pavers completing the project in time — and getting the Kansas Guard fully operational again. The facility is now used for 10 helicopter pads for the Kansas Army National Guard’s UH-60 Black Hawk helicopters. A thicker concrete area allows heavier transport planes, such as the National Guard’s KC-135 refuelling aircraft when required.