The Marco Polo Airport, which serves the Italian city of Venice, is in the midst of a major upgrade to boost capacity. The work is being handled by the SAVE Group and involves a €630 million expansion and renovation of the facilities. This will increase capacity with one major phase of the plan being the 2015-16 extension of the apron. This challenging task has been tackled by NORDPAVI, an Italian concrete contractor that specialises in airport work.
The firm is based in Bolzano in Italy’s South Tyrol an
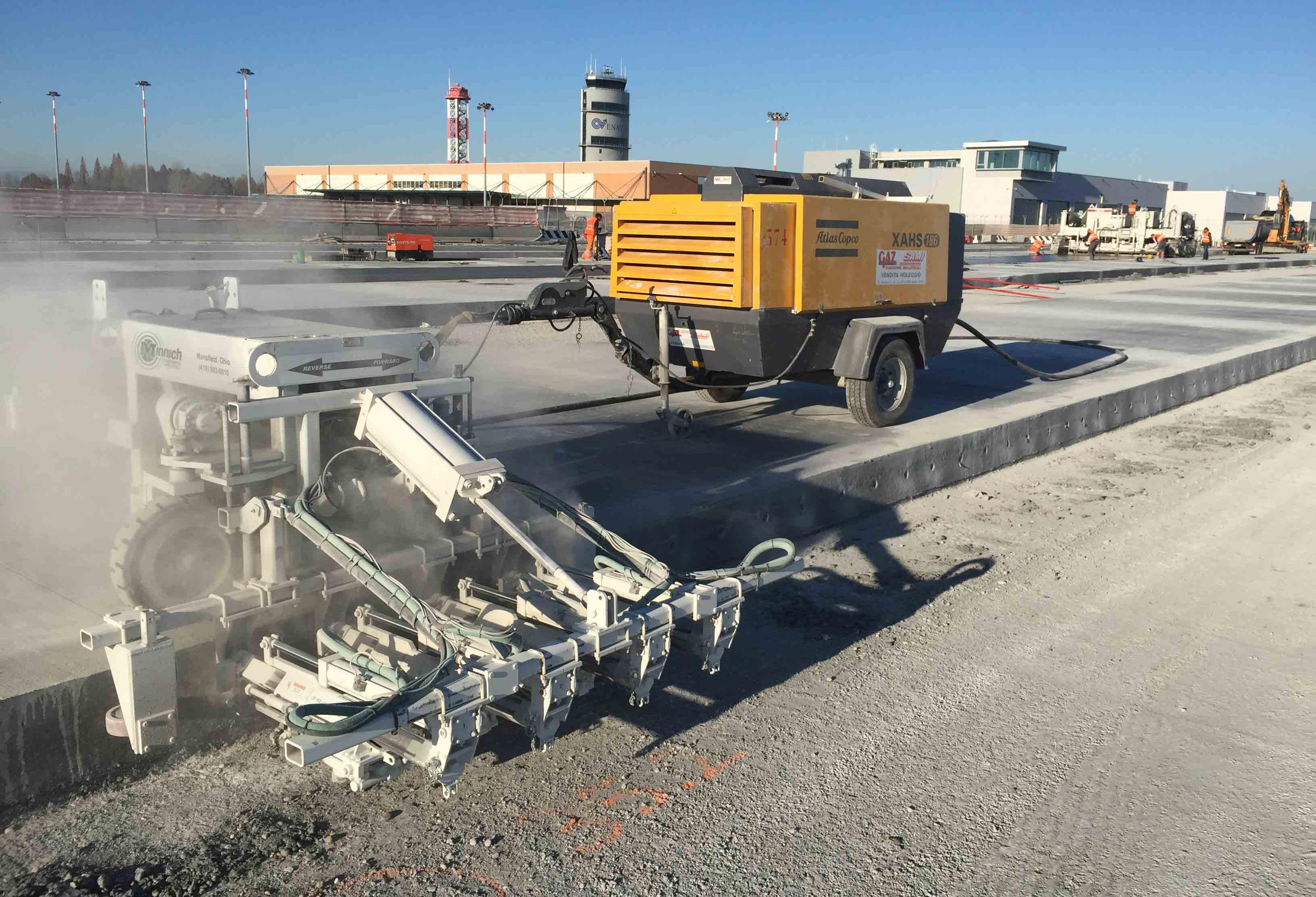
Minnich equipment handled the dowel pin drilling work at Venice airport
The Marco Polo Airport, which serves the Italian city of Venice, is in the midst of a major upgrade to boost capacity. The work is being handled by the SAVE Group and involves a €630 million expansion and renovation of the facilities. This will increase capacity with one major phase of the plan being the 2015-16 extension of the apron. This challenging task has been tackled by NORDPAVI, an Italian concrete contractor that specialises in airport work.
The firm is based in Bolzano in Italy’s South Tyrol and was awarded the job of slipform paving a 45,000m2 concrete apron at the airport. The company runs a218 GOMACO slipformer in its equipment fleet. NORDPAVI airport development manager Enrico Dal Farra said that its key concerns for the work included addressing concrete supply and job-site access during the €562,000 project. Dowel-pin drill selection would be crucial to productivity and profitability.
“Security and traffic safety are critical on airport jobs,” Dal Farra said. “Because we had strict terms to respect, it was very important to have efficient and accurate equipment on the site that could be relied on. For example, it’s a major problem if we have to stop work because a dowel-pin drill doesn’t work or the dowels aren’t aligned.”
The project would require more than 16,000 dowel-pin holes 30mm in diameter to be drilled to depths of 500mm. NORDPAVI wanted to use a dowel-pin drill that delivered more than just superior speed and accuracy. Worker safety is the top priority at NORDPAVI, so operator safety features would also dictate drill selection.
NORDPAVI co-owners, partners and brothers Christian and Luca Da Canal decided to use an A-4SCW on-slab self-propelled wireless unit from286 Minnich Manufacturing, to handle the dowel-pin drilling work.
According to Dal Farra, the Minnich A-4SCW’s wireless remote control technology enabled NORDPAVI operators to drill eight holes/minute and drive down the slab to drill the next set of holes, while standing in the grade away from the equipment. He explained that from that location, operators could drill faster and more accurately while avoiding excess dust and obstacles.
With the help of its Minnich drill, NORDPAVI completed its portion of the project on time in spring 2016.
The firm is based in Bolzano in Italy’s South Tyrol and was awarded the job of slipform paving a 45,000m2 concrete apron at the airport. The company runs a
“Security and traffic safety are critical on airport jobs,” Dal Farra said. “Because we had strict terms to respect, it was very important to have efficient and accurate equipment on the site that could be relied on. For example, it’s a major problem if we have to stop work because a dowel-pin drill doesn’t work or the dowels aren’t aligned.”
The project would require more than 16,000 dowel-pin holes 30mm in diameter to be drilled to depths of 500mm. NORDPAVI wanted to use a dowel-pin drill that delivered more than just superior speed and accuracy. Worker safety is the top priority at NORDPAVI, so operator safety features would also dictate drill selection.
NORDPAVI co-owners, partners and brothers Christian and Luca Da Canal decided to use an A-4SCW on-slab self-propelled wireless unit from
According to Dal Farra, the Minnich A-4SCW’s wireless remote control technology enabled NORDPAVI operators to drill eight holes/minute and drive down the slab to drill the next set of holes, while standing in the grade away from the equipment. He explained that from that location, operators could drill faster and more accurately while avoiding excess dust and obstacles.
With the help of its Minnich drill, NORDPAVI completed its portion of the project on time in spring 2016.