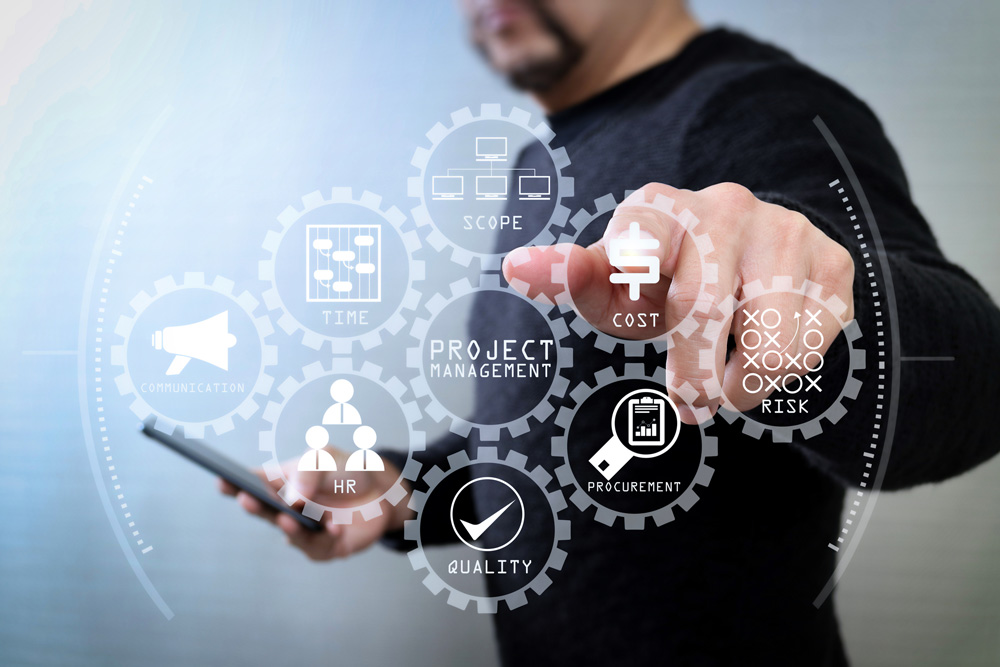
Increasing sustainability and efficiency requirements are challenging construction contractors in meeting their project cost and time commitments. The sector is seeing a changing landscape of machine power sources across the diverse range of equipment onsite, from clean diesel to hybrid, and electric to fuel cell. Coupled with the wide scope of jobs to be done, it is not clear which is the right one to specify. This dynamic set of demands will need to be managed through a diverse range of power options on the worksite of the (near) future.
Whilst there have been impressive advancements in alternative fuels in recent years, construction equipment continues to rely on time-proven diesel as its primary power solution. This is due to the heavy-duty cycles and diverse power applications that are required throughout the industry. The demand therefore for ultra-clean engines that can still provide peak performance is high.
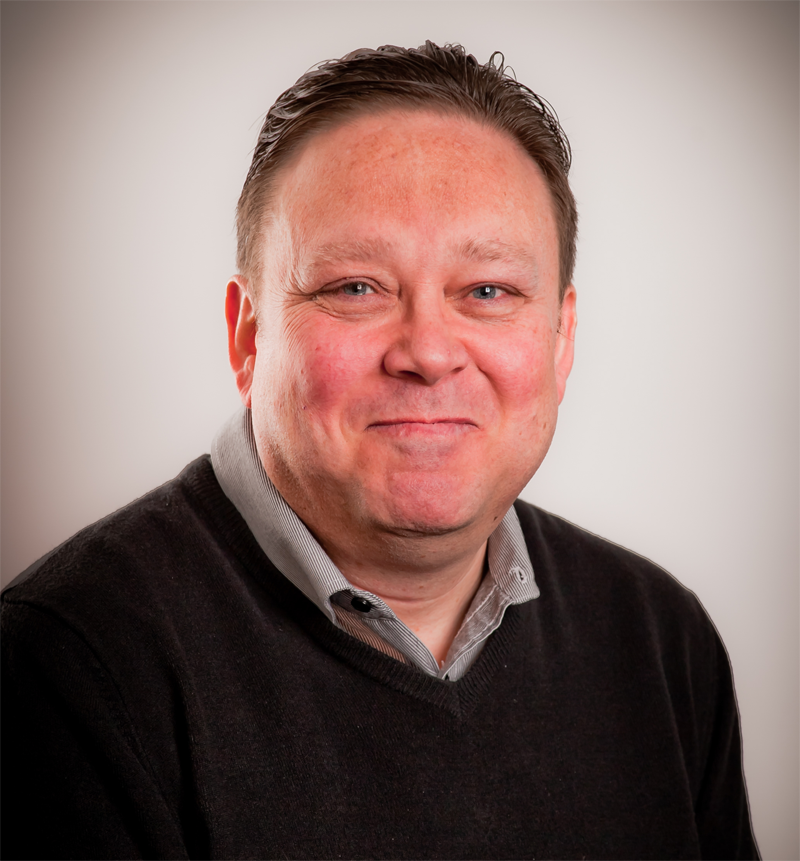
Cummins has been a leader in the global development of Stage V diesel technology. Its Performance Series range delivers on average 10% more power and 20% more torque compared to Stage IV predecessors, while also emitting near-zero NOx and particulate matter (PM) through the use of aftertreatment.
While diesel is more suitable for the heavier duty machine, electric power is starting to gather momentum in compact, light duty cycle equipment such as mini excavators and mini wheeled loaders. These are particularly important on urban sites needing low noise and zero-emissions. The initial investment cost for this adoption of EVs is still higher than others but will gain competitiveness over time.
Cummins has acquired technology companies Brammo, JMBS and EDI to develop capability for electric power. This has led to industrial projects with OEMs Hyundai and XCMG, developing power for electric mini excavators using battery modules connected in a series configuration for a full shift.
It is clear that diesel tankers will not be the only solution for delivering power to the machinery onsite in the future. EVs will require rapid charge stations and fixed charge towers will likely be the preferred option for providing high power and high voltage fleet charging applications. Portable storage solutions will also be essential to any off-grid activity to enable effective charging and ensure longevity of battery life.
Making the most of these charging stations will require smart charge management through improved engine connectivity, monitoring and coordinating the availability of energy, charger proximity, and eventually leading to equipment moving self-directed to platforms that support autonomous machinery.
To ensure that this new generation of infrastructure is used correctly, site managers will need to embrace improved engine connectivity and monitoring to coordinate both refuelling and charging.
Development of the latest generation of digital applications will support the future of construction worksites, allowing customers to maintain peak performance with a range of power and connectivity solutions. Key to managing a diversely powered worksite is the ability to oversee multiple moving parts accurately and efficiently. Planning maintenance schedules for equipment with different duty cycles can be tricky, but this could be exaggerated when adding factors such as refuelling/recharging times and new component parts for repairs caused by the introduction of alternative fuels. Managing downtime in this way is a priority for all site operators which is why diagnostics is playing an increasingly important role to operations.
Unplanned downtime is a major headache for any contractor. Connected diagnostics provides remote fault monitoring through a convenient web portal, mobile app and email service, providing alert notifications on equipped machinery with issue descriptions and service recommendations, along with suggested times to act.
The ability to diagnose a problem is naturally only half the battle, and that is why tools like Connected Solutions have been developed, providing a remote equipment diagnostics service for site operators to support the management of smart worksites. This software combines unique power unit calibrations, electrified charging support and remote connectivity to provide a clear picture of site operations and effective solutions that can be implemented at the push of a button.
In the long term, it is important for software to stay up to date with changes in the engine market, with industry trends and legislation requiring a rapid shift in power applications. To stay on top of the times, customers can benefit from the latest connected software updates. This enables remote, over-the-air programming for engine control module calibrations, facilitating quick installations of new software releases, available anywhere in the world in real time – just like a smartphone.
*Steven Nendick is marketing communications director for Off-Highway at Cummins