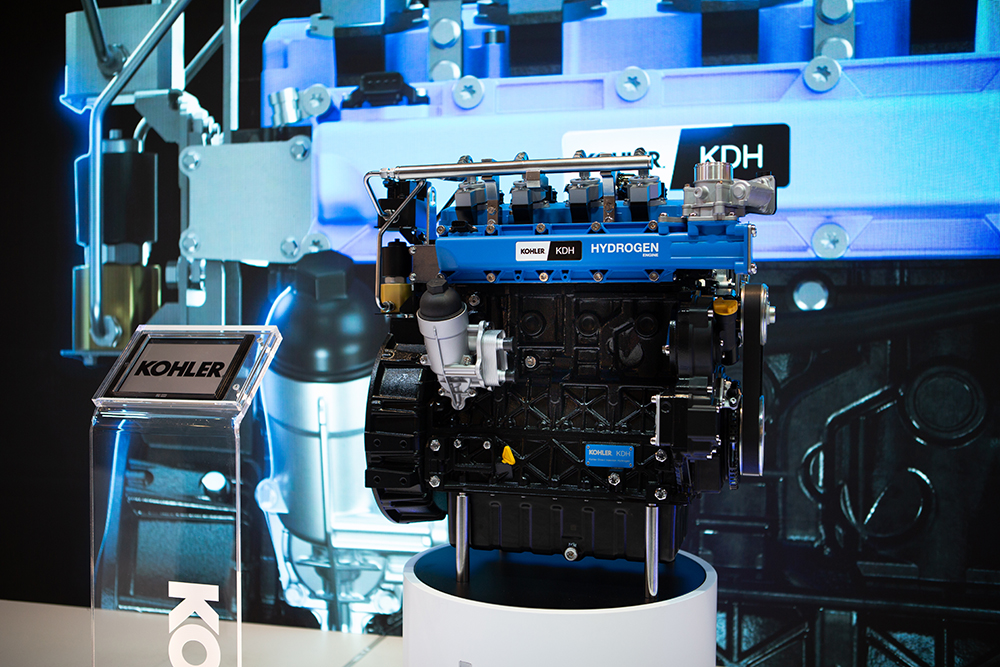
“This marks an exciting moment in the future of our energy company,” says Brian Melka, Group President – Kohler Energy. “As governments, businesses, and individuals look for ways to reduce their carbon footprint, we’re likewise pursuing ways to positively contribute to decarbonization through new technologies and advanced engineering to develop solutions that utilize clean energy sources. We believe we can provide the broadest array of solutions, especially in hydrogen, given our unique footprint across diverse end markets.”
Alongside HVO and e-fuels, Kohler Energy is committed to investing in innovative engine technologies that improve energy efficiency and significantly reduce environmental impact, while still meticulously tailored to the diverse spectrum of machinery requirements. As such, the hydrogen internal combustion engine will be applied to the KDI 2504 TCR, with the ability to provide the same performance and power density as the starting diesel engines but using a carbon-neutral solution.
Additionally, Kohler Energy’s industrial business will launch its first hydrogen fuel cell power system, a 100 kW Solid Polymer Electrolyte Membrane fuel cell, using green hydrogen, for emergency backup, peak shaving and demand response. The system is suitable for a broad range of mission-critical power users including hospitals, data centers, utilities, ports and water treatment plants.
Kohler Engines Introduces Hydrogen Technology with New KDH Engine
Kohler Engines unveiled its new Kohler Direct Injection Hydrogen (KDH) engine, a hydrogen-powered internal combustion engine, during Agritechnica in Hanover, Germany, the world's largest exhibition for the agricultural machinery industry. The KDH presentation was very successful, with a packed audience of industry experts gathered in front of the Kohler booth, and more than 4,500 views of the live broadcast on the company's LinkedIn channel.
The new pioneering hydrogen engine technology is being applied for the first time to the KDI 2504 TCR derivative engine, which takes advantage of conventional combustion engine architecture but replaces diesel with hydrogen. This new engine solution maintains the same in-machine installation, dimensions, PTOs and performance as conventional diesel engines, while using a zero-carbon solution.
Kohler Engines is investing in a range of innovative technologies to enhance energy efficiency, meticulously tailored to meet diverse machinery requirements. Among these solutions, hydrogen has emerged as a versatile, green energy fuel with rapidly evolving technology. Renowned for its wide flammability range, high flame speed, low ignition energy, and high diffusivity, hydrogen holds promise as a cleaner alternate fuel for internal combustion engines.
The choice of direct injection (DI) technology, as opposed to port fuel injection (PFI), allows to preserve diesel performance, including transient response, by avoiding the backfire problem. The design aims to provide the same performance as the original diesel engine, such as max power, peak and low-end torque, as well as transient response and drivability, to ensure and maximize productivity of the equipment.
Hydrogen plays a pivotal role in emissions and GHG reduction due to its capacity to provide clean and highly efficient energy. The most outstanding feature of hydrogen as a fuel is its inherent ability to produce energy through combustion without generating carbon dioxide (CO2). This means that hydrogen as a fuel allows to zero-out the carbon footprint of internal combustion engines.
The combustion of a hydrogen engine is cleaner than a standard diesel engine. Moreover, when an aftertreatment system (ATS) is applied to a hydrogen internal combustion engine, the environmental benefits of using hydrogen are further amplified. Indeed, the addition of the ATS results in a reduction of exhaust emissions to extremely low values, thus making the engine near zero-emission according to the most recent agencies’ definitions. The ATS reduces particulate matter (PM), nitrogen oxides (NOx) and hydrocarbons (HC) to negligeable levels at tail pipe. As a result, this dual approach not only complies with emission standards, but also underscores the commitment to cleaner air quality.
Notably, the hydrogen internal combustion engine is designed to be a drop-in solution, making it potentially adaptable to a wide range of equipment applications.
Kohler Engine’s commitment to providing a convenient solution for OEMs is evident in the fact that no major changes to the engine compartment will be required, as this solution fits the current size of Kohler compact diesel engines: the KDH hydrogen engine has the same engine envelope as the KDI diesel engine. Therefore, OEMs can expect compatibility with existing machine platforms.
Kohler Engines remains aligned with OEMs' development programs, ensuring that the hydrogen engine production schedule aligns with industry demands, and offers support to customers in conducting proof-of-concept evaluations.
“We look forward to unveiling this evolving technology and working closely with our partners to drive innovation, sustainability and decarbonization in the industry,” claims Vincenzo Perrone, President of Kohler Engines.
Content produced in association with Kohler