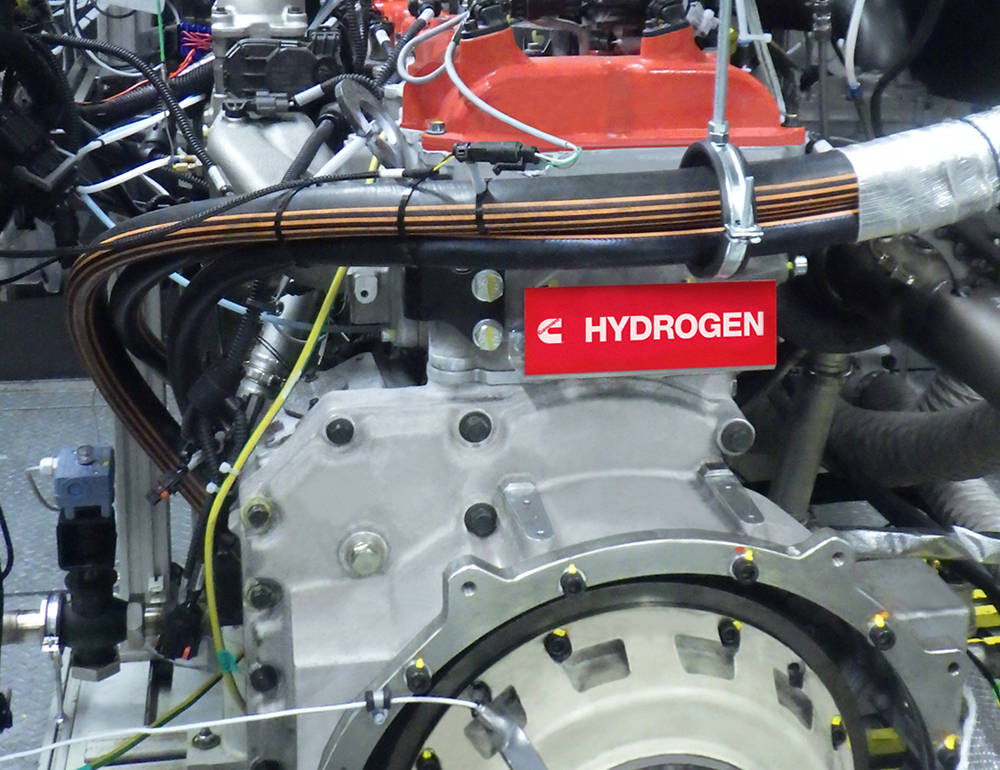
The construction machinery sector has relied on the diesel engine as its primary source of motive power for a century. Early earthmoving machines used steam power and these began to be replaced by equipment using petrol engines at the start of the 1900s. But firms began switching to diesel engines in the 1920s as the performance of these units improved.
However, with the need to address climate change issues, that dominance of the diesel engine for off-highway earthmoving equipment is being challenged and from a number of angles.
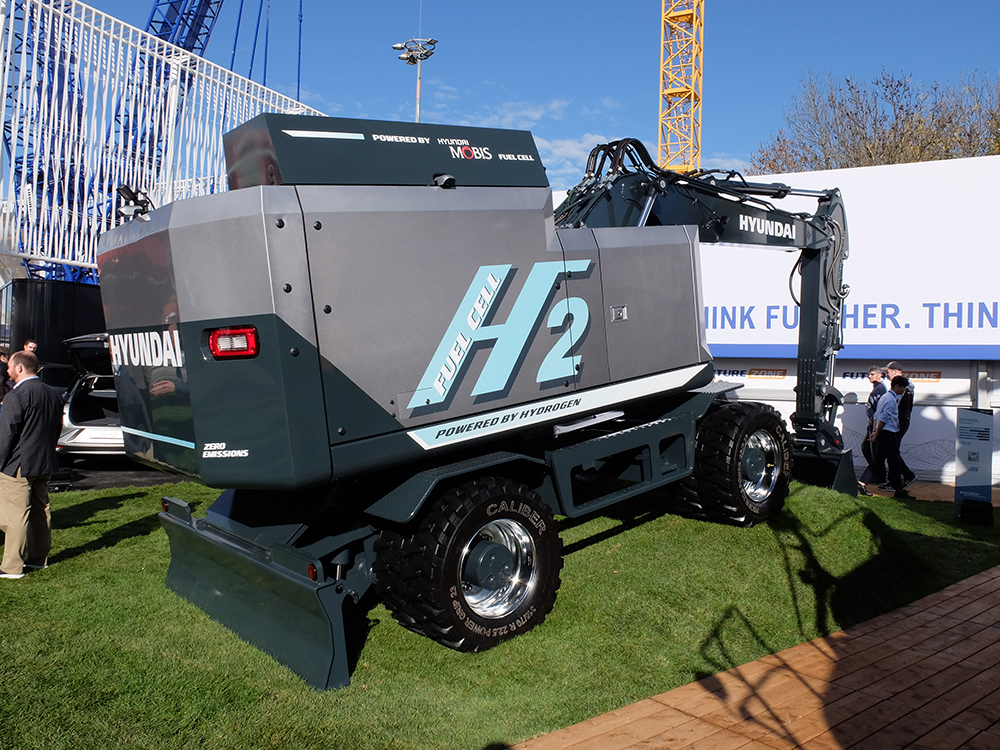
Electric power is now becoming accepted as one alternative but has so far been limited to compact machines. In the last year or so prototypes of larger machines have been unveiled featuring electric power from firms including Caterpillar, Komatsu and Volvo CE for examples.
Meanwhile, hydrogen fuel systems have been unveiled with most using modified internal combustion engines, although there have also been fuel cell systems tested such as a JCB prototype, only Hyundai is preparing to offer a fuel cell excavator at present. Volvo CE has invested heavily in developing fuel cell power units at its Eskilstuna facility in a big step towards commercial introduction of the technology. Several construction machinery firms such as Hyundai Doosan Infracore, JCB and Liebherr as well as the engine maker Cummins have been working on internal combustion (IC) engines fuelled by hydrogen.
Caterpillar says that its 22tonne 320 excavator prototype features five 600V Cat lithium-ion batteries which provide a total of 320kw/h electric power. This allows up to six hours operation before recharging is required, depending on the operation. More demanding operations such as trenching will have a shorter period before recharging is necessary.
The 19.7tonne GC wheeled loader uses four Cat 300V lithium-ion batteries for a total of 256kw/h electric power. It takes around one hour to recharge. Both the 320 medium excavator and 950 GC medium wheeled loader can use DC fast charging.
Komatsu says that its 20tonne class PC210E electric hydraulic excavator is equipped with a Proterra-manufactured lithium-ion battery system. Komatsu and US-based Proterra have been jointly developing electric medium-sized hydraulic excavators and have been conducting PoC (Proof of Concept) tests on advance research machines at construction sites. The PC210E will be available commercially in the Japanese market in due course.
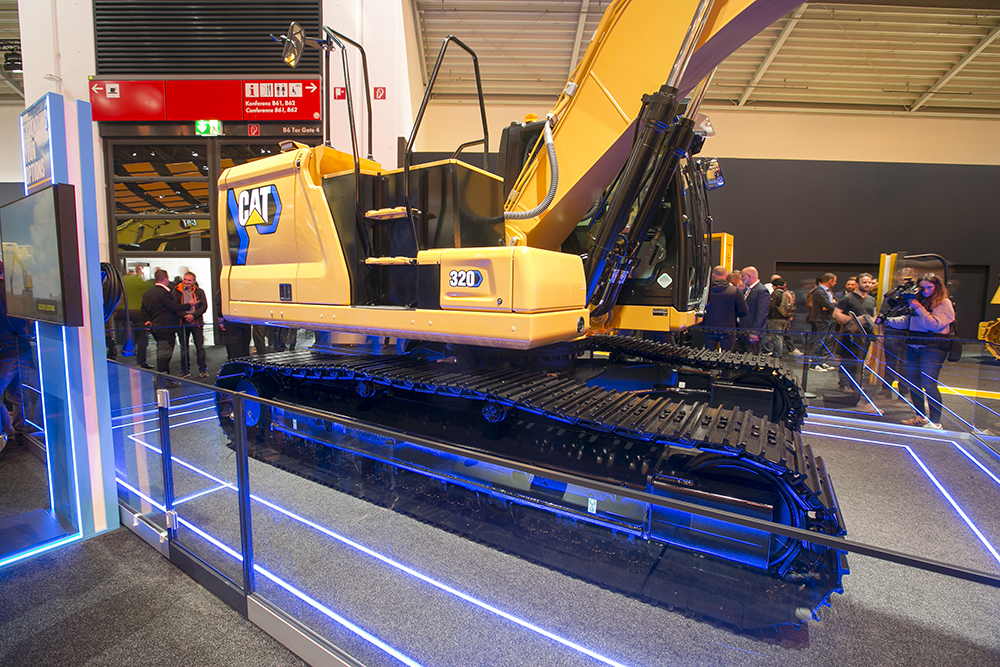
The PC210E model integrates Proterra’s lithium-ion battery technology which is proven in heavy-duty vehicles with Komatsu’s hydraulic pump, controller, and electric motor. In addition, Komatsu has developed a robust structure to protect the batteries. As a result, the company claims performance equivalent to a conventional diesel excavator and eight hours of operation from a full charge.
Volvo CE says that its EC230E excavator will meet demands for electric excavators in the 23tonne class. However, a more radical innovation comes in the shape of an electric power system for its 20tonne class L120 wheeled loader. The system has been developed in conjunction with Parker Hannifin and converted by Volvo Group’s own CE Engineering Solutions. Volvo CE says that it is working with CE Engineering Solutions and selected electromobility partners to accelerate the availability of electric solutions across all segments. This latest collaboration to expand its line of electric wheeled loaders follows Volvo CE’s investment in Dutch manufacturer Limach to broaden the company’s electric excavator portfolio.
The manufacturer says that its partnership approach allows for speedier implementation to the market. It is being carried out in parallel with the company’s continued development of more electric solutions, such as its 23tonne class EC230 electric excavator using the firm’s own technology. Volvo CE says the machine delivers the same performance as its diesel counterpart, but with zero exhaust emissions and near silent operation.
Powered by 240kWh batteries, it provides a runtime of approximately five hours in most medium-duty applications. Consistent with Volvo’s existing charging solutions, it is estimated to charge from 0-100% in just 1.5-2 hours. The L120H Electric Conversion offers features as standard: Comfort Drive Control; Load Assist with Onboard Weighing; plus radar detection with its new Collision Mitigation System. In addition, the L120H Electric Conversion will be supported by dedicated electromobility applications which allow the operator to check battery and charging status and to preheat the cab.
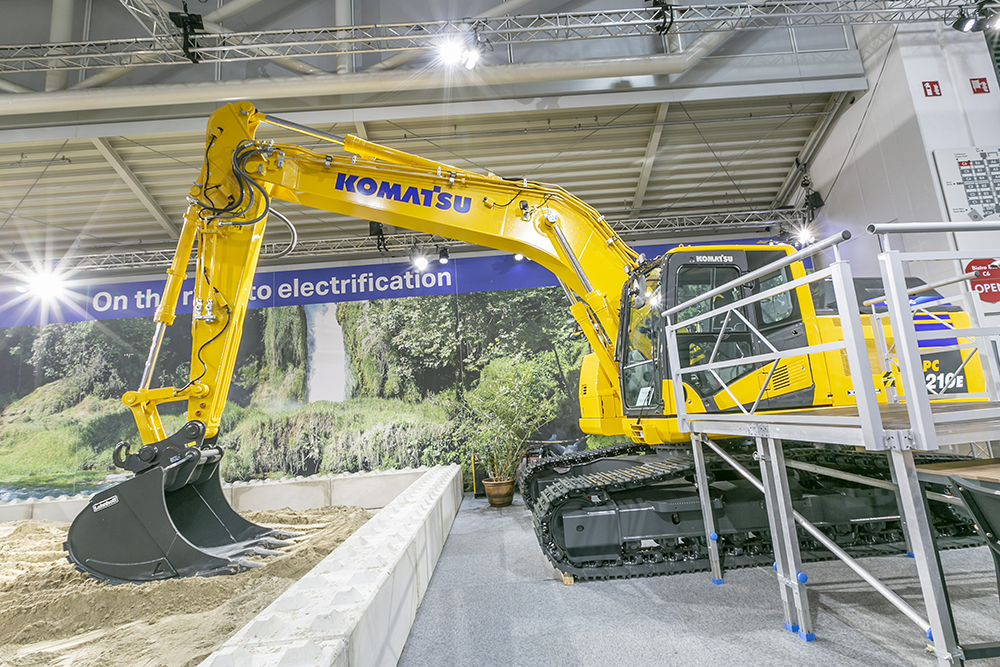
Volvo CE says that, depending on market demand, it brings the possibility to convert existing customers’ L120H wheeled loaders to electric in the future. With a US$7.8 million investment from Volvo Group, a new production facility will be built at the Changwon plant in South Korea. This facility will produce a wide range of common electric storage solutions (battery packs) for Volvo Group and become a core competence centre for electric excavators.
The company also recently announced a plan to upgrade its Arvika factory in Sweden which produces the firm’s medium and large wheeled loaders. The $6.3 million investment from Volvo Group will allow for the production of electric wheel loaders at Arvika, while the firm has plans to build electric haulers at its facility in Braås, Sweden. Arvika will erect a new building, approximately 1,500m2, which will allow the facility to free up areas inside its assembly factory to build electric wheeled loaders. While it has not yet been announced which models will begin their electric transformation and exactly when, production of both electric wheeled loaders and conventional ICE wheeled loaders will continue for now on the same production line. Volvo CE says it will ensure a phased introduction model by model, taking into account all aspects of the electric ecosystem, including infrastructure requirements, charging solutions, battery handling and business models.
Some firms are taking the prospects of hydrogen as a fuel for ICE units very seriously.
Hyundai Doosan Infracore (HDI) is aiming to mass produce internal combustion engines (ICE) that use hydrogen as fuel in 2025. The firm is unveiling its prototype ICE power unit that runs on hydrogen in 2023, with full-scale testing planned for 2024, to be followed by full-scale mass production in 2025.
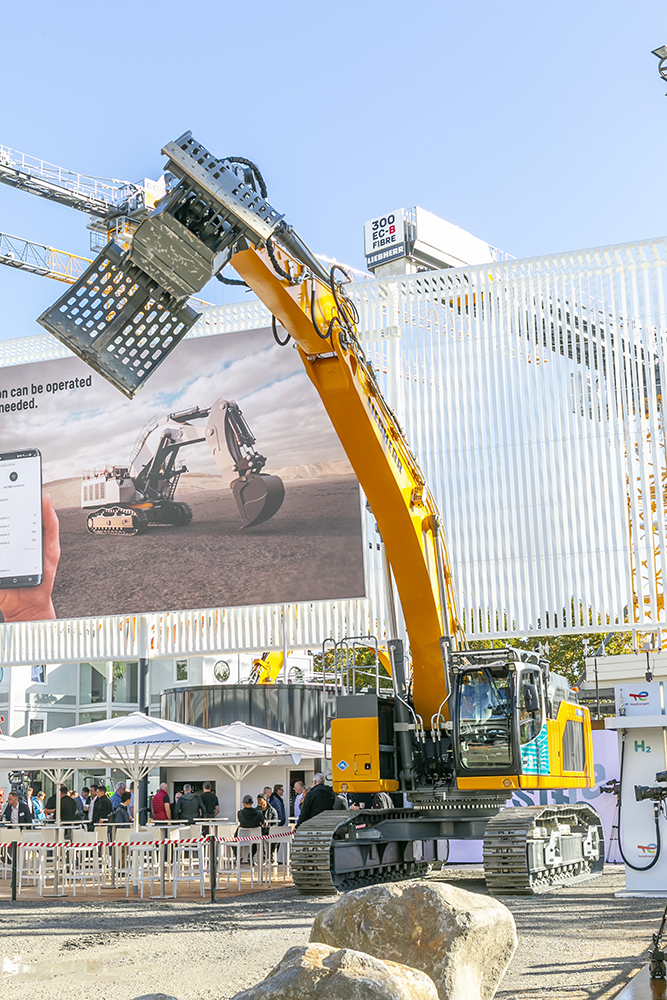
The firm has completed the design of its hydrogen ICE unit, an 11litre class engine that produces a power output of 300kW and a torque of 1700Nm at 2,000rpm. It meets the Tier 5/Stage 5/Euro 7 regulations which require the emissions to be 90% reduced to the current level to meet Zero CO2 (below 1g/kWh) and Zero Impact Emission (Zero Emission in EU).
Liebherr won an innovation award at the bauma exhibition in Germany for its 50tonne R9XX H2 prototype excavator, built at its Colmar facility. The machine is powered by an IC engine modified to run on hydrogen. This clean burning concept produces mostly water vapour from the tailpipe while the CO2 emissions profile of the machine from manufacturing to decommissioning are estimated to be around 70% lower than for a conventional machine.
The special H966 power unit was developed at the firm’s Liebherr Machines engine facility in Switzerland and uses conventional technology adapted for the purpose. The port fuel injection (PFI) and direct injection (DI) systems are said to ensure efficient combustion. Series production of the Liebherr hydrogen-fuelled engines is scheduled to commence in 2025. The H966 engine features six cylinders and a four-cylinder H964 unit is in development.
JCB is investing £100 million on a project to produce efficient hydrogen engines. A team of 100 engineers is already working on the development with the recruitment of up to 50 more engineers under way. The firm has unveiled an IC engine that runs on hydrogen as well as a prototype backhoe loader and telehandler and will be offering construction machines using this as fuel on the market in the near future.
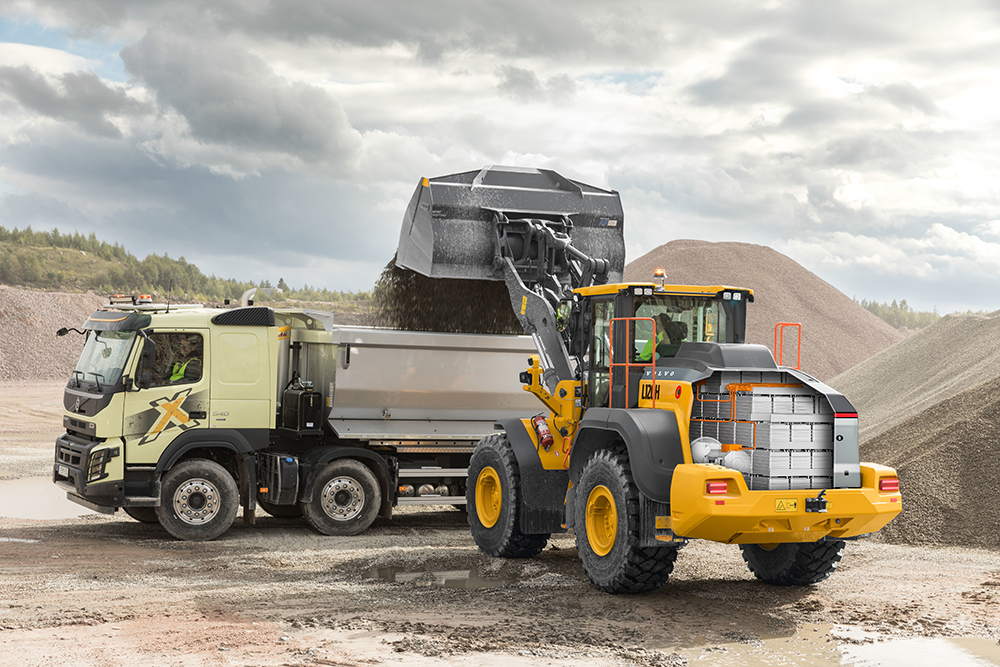
Cummins is now moving ahead with its hydrogen-fuelled, internal combustion engine (H2-ICE) development programme. The firm is working on a medium-duty 6.7litre engine and a heavy-duty 15litre engine that will be fuelled by hydrogen. The new hydrogen engines will be able to operate with zero carbon emissions, while delivering high power density and improved thermal efficiency.
The engine development work will be accelerated after receiving a £7.2 million funding award from the UK Government provided through the Advanced Propulsion Centre (APC). This has recognised the potential for H2-ICE to play a major role in decarbonising commercial trucks and construction equipment from 2025 onward.
Designated as the APC18 BRUNEL Project, the technical readiness work will expand on Cummins’ experience from its existing H2-ICE programme and recent testing. Planned development of the 6.7litre hydrogen engine will focus on medium-duty applications including construction machinery, such as excavators and wheeled loaders.
Cummins partnership with hydrogen storage specialist NPROXX adds an important resource in terms of integrating the hydrogen engine, with the high-pressure gas tanks and supply lines installed on the vehicle or equipment.