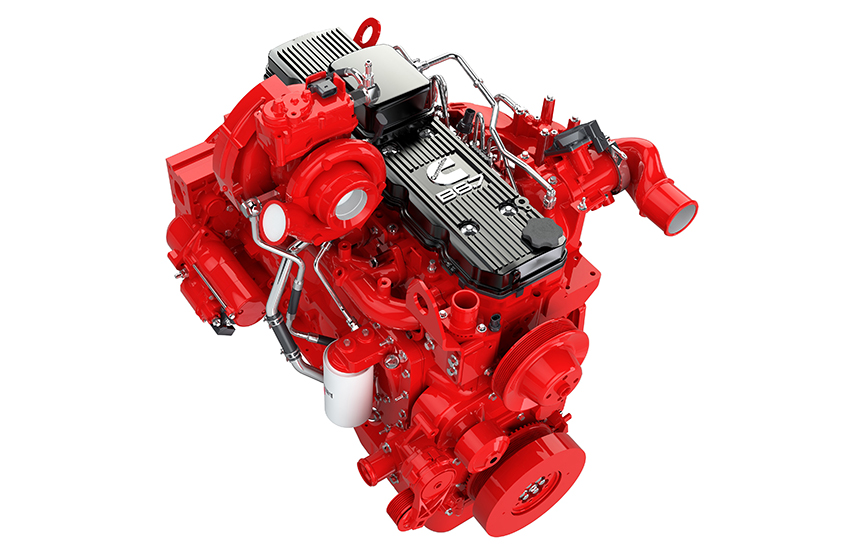
Stage V
Cummins Performance Series range are the latest generation of clean diesel engines that meet EU Stage V and US EPA Tier 4 Final emissions legislation. These products are years ahead of their predecessors in terms of associated technologies and performance capabilities. They are clean, efficient, dependable, and flexible power sources, suitable for the widest range of off-road equipment, from quarrying to urban construction.
Contractors and site managers can make significant improvements by selecting the latest Stage V engined machines in place of older equipment, before having to invest in alternative technologies. The Cummins range of Stage V Performance Series engines are available from 75 – 675 hp / 55-503 kW, with 3.8 to 15 litre displacements and a maximum high peak torque of 2508Nm. They offer elevated levels of power density with low weight to increase machine capability and customer value or offer engine downsizing opportunities to reduce costs with no negative impact on equipment operations.
The higher power density also means that smaller machines can potentially do the job of historically larger ones. Fuel efficiency would be improved, reducing running costs as well as CO2 emissions. The engines’ longer service intervals also lead to reductions in oil and filter usage, lowering costs as well as environmental impact.
Stop-Start
Last year, Cummins announced that its B6.7 Performance Series engine would feature stop-start capabilities.
The B6.7 can be specifically tailored mechanically and electrically with Stop/Start technology for different applications by Cummins’ engineers, with powertrain integration capabilities delivering the best all-round performance to match the required operating cycle whilst reducing emissions and operating costs.

The new stop-start capability is ideal for off-highway applications, with equipment often enduring prolonged periods of engine idling between tasks on site. When installed in equipment, the stop-start capable B6.7 will lower running hours, cut fuel costs by up to 10% and reduce onsite emissions – all without a drop in performance or reliability. Stop-start can be tailored to each installation, with the number of stops and starts limited per hour, maximising efficiency and operation while protecting the durability of the engine.
The B6.7 is combined with the Cummins Single Module™ after-treatment system to meet and exceed the ultra-low emissions levels demanded by Stage V. The efficient selective catalytic reduction (SCR) technology means that cooled exhaust gas recirculation (EGR) is not needed on the engine, allowing for a simpler, more reliable design with a reduced weight.
Correct Maintenance Practices
As well as Stop-Start, there are other ways that site managers can improve fuel efficiency, save costs, and reduce CO2 emissions.
Maintenance: Following recommended maintenance schedules is critical to ensure that equipment produces its optimum performance. Poorly maintained machines will use more fuel for the same amount of work than a well maintained one. Preventive maintenance saves fuel costs and major repairs in the long term, maximising the productivity and life of the engine.
Use the right fuel and oil: Follow the OEM’s recommendations for the correct fluids to be used and keep at the required levels to ensure the performance of the machine stays within its specification. Additional checks on tyre air pressure and air filter cleanliness are also important to maintain optimal fuel efficiency.
Minimise idling: idling wastes fuel, however efficient the engine is. If machines are left idling for a long time, they will produce increased emissions as well as incur additional costs. Idling can also impact the engine life, with unnecessary wear on components. If equipment has timed idle shut-off or stop-start capability, this should be switched on.
Use the right machine for the right job: there are a range of diverse applications within construction that require specific power requirements. Matching duty cycles of equipment appropriately with their application will ensure that engines perform within their specifications for longer, minimising fuel usage and total cost of ownership.
Use trained operators: Having trained people who can operate machinery at their optimal levels will maximise fuel efficiency and reduce potential damage to the unit. Poorly trained staff will likely be more aggressive when using the machine, increasing fuel consumption. As telematics capability develops, the data gathered will be able to help improve operator training.
Monitor your machines: where machines come with monitoring facilities, analysing their data can help reduce fuel consumption. Monitoring also helps to detect potential service problems in advance and reduce repair costs and downtime.
Connectivity

Cummins supplies engines across a wide range of duty cycles to industrial equipment manufacturers throughout the industry, with many of these supplied OEMs developing their own telematics capability. As such, Cummins has developed its digital applications so they can integrate with third party systems connected to the machine network. The benefit of this is having all machine information, including engine performance, in one place via a single interface. All these capabilities result in an improved operational ability for OEMs alongside fleet services, enabling a reduction in fuel usage through improved efficiency. Cummins Connected Solutions are available across the current Performance Series range of engines.
Biofuels
To support decarbonisation efforts, Cummins Stage V Performance Series engines can operate on B20 biodiesel and HVO100. B20 means a mix of 80% diesel with 20% biofuel (that meets European specification EN16709). Using B20 fuel will reflect a CO2 saving of 10%. Hydro-treated Vegetable Oil (HVO) is a synthetic diesel made from waste products, such as frying fat, animal fats or wood pulp, and can be mixed with normal diesel oil to form a blend. This can eliminate up to 85% of net CO2 emissions, depending on the feedstock used in its production.
Utilising biodiesel requires stringent management, as moisture must be kept to a minimum to avoid microbial growth. Due to its poor oxidation stability, biodiesel should be used within six months of manufacture. For this reason, biodiesel is not recommended for low use or seasonal applications.
In Summary
The power industry has made huge strides to significantly reduce engine emissions since regulations began in the 1990’s. Today’s products are producing record low emissions whilst maintaining reliable performance across a range of power requirements and duty cycles. As the industry decarbonises, those looking to make an impact quickly can do so using the latest generation of clean diesel engine. Diesel power will remain a flexible and viable solution for years to come alongside the alternative solutions being developed.
Content produced in association with Cummins