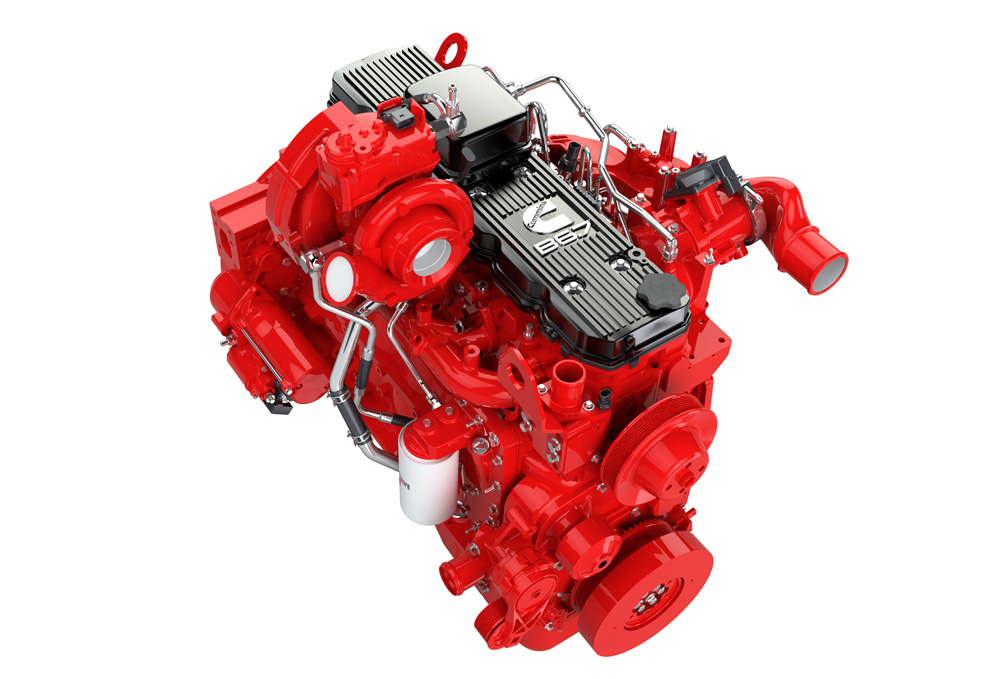
Stop-Start has been integrated into the B6.7 platform with both hardware and software changes. Specially developed bearings in the engine, along with upgrades to the flywheel ring gear and starter motor, ensure long life and reliable performance with frequent starts. The engine system was thoroughly tested to confirm its durability for the rigors of Stop-Start operations.
Cummins engineers work closely with the OEM customer to integrate the engine electronic control module (ECM) software with the OEM’s machine controller software. The OEM controller monitors the machine operation and communicates to the ECM when it is appropriate and safe for the machine to shut off. The ECM monitors engine parameters, such as coolant temperature, intake manifold temperature, engine load, and fan operation, to make sure it is safely able to shut down. When all criteria are met, the engine will stop. The machine controller will then request an engine restart when required, and the ECM automatically restarts the engine to continue working. This Stop-Start feature is essential for machines that sit idling on construction sites for long periods in between tasks. Stop-Start not only reduces running cost - it lowers running hours for the machine, helping maintain higher residual values.
The 6-cylinder B6.7 engine is available from 116-243 kW (155-326 hp) with a high peak torque of 1375 Nm. With a low weight and compact size, it delivers a high power density that enables the B6.7 to replace engines of higher displacement with no impact on machine operation. This supports machines needing higher-speed power delivery, with low-end torque capability for transient performance benefits. Equipment manufacturers can use the B6.7 to improve machine capability and offer more value to their customers.
The B6.7 engine is combined with the Cummins Single Module™ after-treatment system to meet and exceed the ultra-low emissions levels demanded by Stage V. The efficient SCR technology means that cooled exhaust gas recirculation (EGR) is not needed on the engine. Having no EGR means that the engine is lower weight and has a simpler design, allowing for easier installation into equipment; together with lower cooling requirements. The simpler configurations also mean better reliability, reducing the total cost of operation and boosting availability.
This product is ideal for use in a range of off-road equipment including crushers, screeners, wheel loaders, excavators, and empty container handlers. It can be tailored by Cummins’ engineers mechanically and electronically to each machine type. This powertrain integration capability delivers the best all-around performance and running costs to match the required operating cycle.
To find out more about the Cummins B6.7 and full performance range, go to https://www.cummins.com/engines#rfq-title
Content produced in association with Cummins