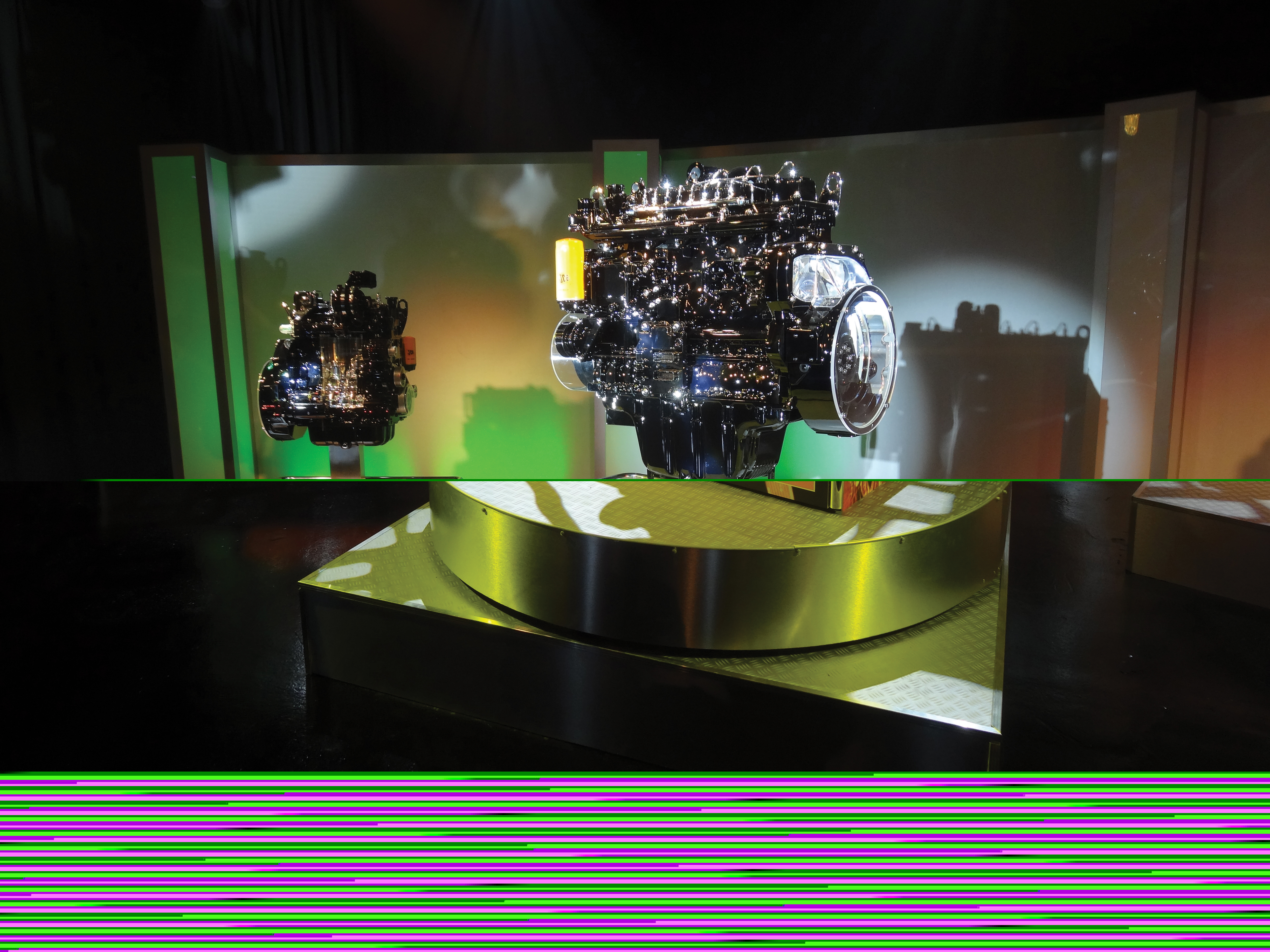
New diesel developments from JCB and Volvo
Innovative diesel technologies are being developed by all the major engine manufacturers at present. New emission requirements have pushed the boundaries in terms of technology, with all the firms working on new systems to ensure their products meet requirements. And companies are also developing new engine sizes to broaden their range of offerings to the market.JCB is starting production of its new six-cylinder diesel, with the addition of the JCB Dieselmax 672 to its engine line-up. This is a significant addition to the range as it broadens the power outputs available from the diesel line-up over the existing four-cylinder design. The company first began producing its own diesels in 2004 when the first engine rolled off the production line in the UK. Engines have also been manufactured at JCB India’s HQ at Ballabgarh since 2011 and the firm has made over 250,000 diesels in all. The introduction of the new six-cylinder engine represents an investment of around US$69.6 million and by the time it goes into full production, its launch will have created more than 50 new jobs.
The JCB Dieselmax 672 is based on the company’s four-cylinder 4.8litre Dieselmax engine, with a high degree of parts commonality across the two engine platforms. In production for more than eight years, with many engines running reliably after more than 20,000 hours of service around the world, the Dieselmax engine features electronic control,
Initially the Dieselmax 672 will be produced to meet Stage II emissions standards, for growth markets including Russia, Brazil and China. The engine will be seen first in JCB’s JS360 crawler excavator for those territories, but will be used in additional machines as time progresses. However, a Tier 4 Final/Stage IV version is in development, which will be offered for use in the US and Europe.
The six-cylinder engine will be offered with ratings of 140kW, 165kW, 190kW and with a maximum output of 225kW. Maximum torque of the JCB Dieselmax 672 is 1,200Nm. JCB claims that its Dieselmax 672 offers high efficiency, with 8% better fuel economy than engines used previously in the JS excavator line. In testing, the 7.2litre engine is said to have recorded a specific fuel consumption of just 189g/kWh, while delivering high performance and rapid response. The six-cylinder engines will be built on a dedicated line at JCB Power Systems’ purpose-built facility in the UK. In development for more than two years, the engines have already completed more than 50,000 hours of testing, 30,000 of which have been in machines working in the field.
The Dieselmax engines have 500-hour service intervals, maintaining low operating costs and maximum uptime for customers. The engines will also be offered as part of the company’s OEM product line, for use in non-JCB machinery.
Meanwhile Volvo CE is looking ahead to the stringent Tier 4 Final/Stage IV diesels emission requirements. Its new diesels new have been tested in a range of operating conditions from sub-zero temperatures to high altitudes and desert heat. These tests will ensure that the firm’s latest generation of engines will perform reliably in all operating conditions.
Meeting these emissions requirements has provided a major engineering challenge for the firm. Extensive testing has been carried out in the north of Sweden for example, with various machines being run at
At the other end of the temperature spectrum Volvo CE also carried out extensive tests in Spain on various test tracks, with the firm monitoring how the technology coped in the extreme heat and demanding applications. The firm looked at how an ADT reacted to being driven up a severely steep hill, with a full load, in high temperatures. To check altitude performance the machines were tested at 3,500m in Les Deux Alpes, France. As the air is thin and atmospheric pressure is low at this altitude it allowed Volvo CE to test and verify machine performance, fuel consumption, engine response and ease of starting. Because of the high altitude there is less oxygen, which impacts on the combustion efficiency of an engine and lowers performance, while also impacting on cooling ability so that engines may also be subject to overheating. To ensure altitude performance for a diesel engine, efficient turbocharging is crucial and electronic control of this can ensure boost remains sufficient to deliver enough air so that com
bustion efficiency remains sufficiently within tolerances. Similarly, electronic controls of cooling fans and systems can ensure engines do not overheat, even when running under load at an altitude close to the maximum ceiling.
All the same, Volvo CE is also offering solutions for other markets and the company is to offer a novel conversion kit that allows customers to sell units that are Tier Interim/Stage IIIB compliant into markets that do have such emission restrictions. The system will be available from the second quarter of 2014. The conversion kit works by protecting the Volvo engines against high sulphur levels, while still meeting Volvo internal design standards.
This kit is important as it will allow the trade of secondhand machines from Europe and the US into developing markets such as in Africa, Latin America and the Middle East. Low sulphur fuel for the European and US machines is rarely available elsewhere but cannot be used in Tier 4 Interim/Stage IIIB compliant machines as it will cause damage, particularly to the fuel system.
With fuel costs increasing, economy has become more important. Sister company Volvo Penta has introduced a new start/stop function for its industrial diesels, which shuts the engine down during extended idle periods and turns it back on when the operator presses the brake or accelerator or pulls a lever in the cab. This helps reduce fuel consumption and emissions but is different from automotive systems, which were not suitable for demanding off-highway applications. Volvo’s engineers quickly discovered that this feature would have to be designed carefully to prevent too frequent stops and starts as this could risk damage to the main bearings and high load on the battery. The firm had to add intelligent functions to ensure that the number of starts and stops would not be excessive while the technology also allows OEMs to tune the system to the application. For safety the system also needed a lock-out to prevent the engine being switched off in the middle of a potentially dangerous job or turn it on during maintenance.
The feature can save from 5-15% in fuel costs, depending on how much idling an operator does in an application. The benefits extend further than that. Because Volvo Penta has thoroughly tested the system, the engine falls under full warranty, even with the system installed. On-site noise is reduced, as are emissions: when the engine is turned off, no emissions are produced. But a reduction in idling also lowers emissions by helping keep the after-treatment system warm while the engine is turned off so that it can burn exhaust fumes more efficiently.
Air cleaning
Cleaner air helps boost engine efficiency and US firm Turbo Filtration claims that its Precleaner PowerRam unit suits use with large machines operating in severe-duty environments. The unit has a directional scoop and a wide-angled air intake, which the firm claims improves engine performance by reducing air-intake restriction and delivering more air, boosting fuel efficiency.
The PowerRam features a louvered screen, which prevents plugging from snow and ice build-up at high speeds, extending filter life by removing dirt and dirt particles along with debris in rain and snow from intake air. It also prevents re-entry of sooty exhaust air. The unit is said to be rugged and lightweight in construction, with a durable powdercoat finish to guard against rust, chemical attack and corrosion. The product has a straight-through flow path so that dirty incoming air enters the top of the unit and flows into guide vanes. The air is directed into a high-velocity air-powered rotor chamber, which is powered by the machine's engine and is rotating at around 5,000rpm. The blades generate centrifugal force, spinning over 85% of contaminants out through special discharge ports and only allowing clean air into the engine. Some of these contaminants can be as small as 1 micron, including dust, dirt and moisture. With reverse axial designs, dirty air enters the bottom of the unit, where it turns and this restricts air flow and reduces engine power. Higher restriction means filters do not last as long so engines cannot work as efficiently and also require more maintenance.