Innovative technology is use is providing efficient, clean burning engines - Mike Woof reports The development of new diesel engine technology has, for the off-highway equipment sector, been the single most expensive research field for the industry since these machines first started being manufactured. Aimed at reducing the emissions of nitrous oxide as well as particulate matter, in a phased series of stages the engine emission improvements will make major changes to the construction sector. In real world
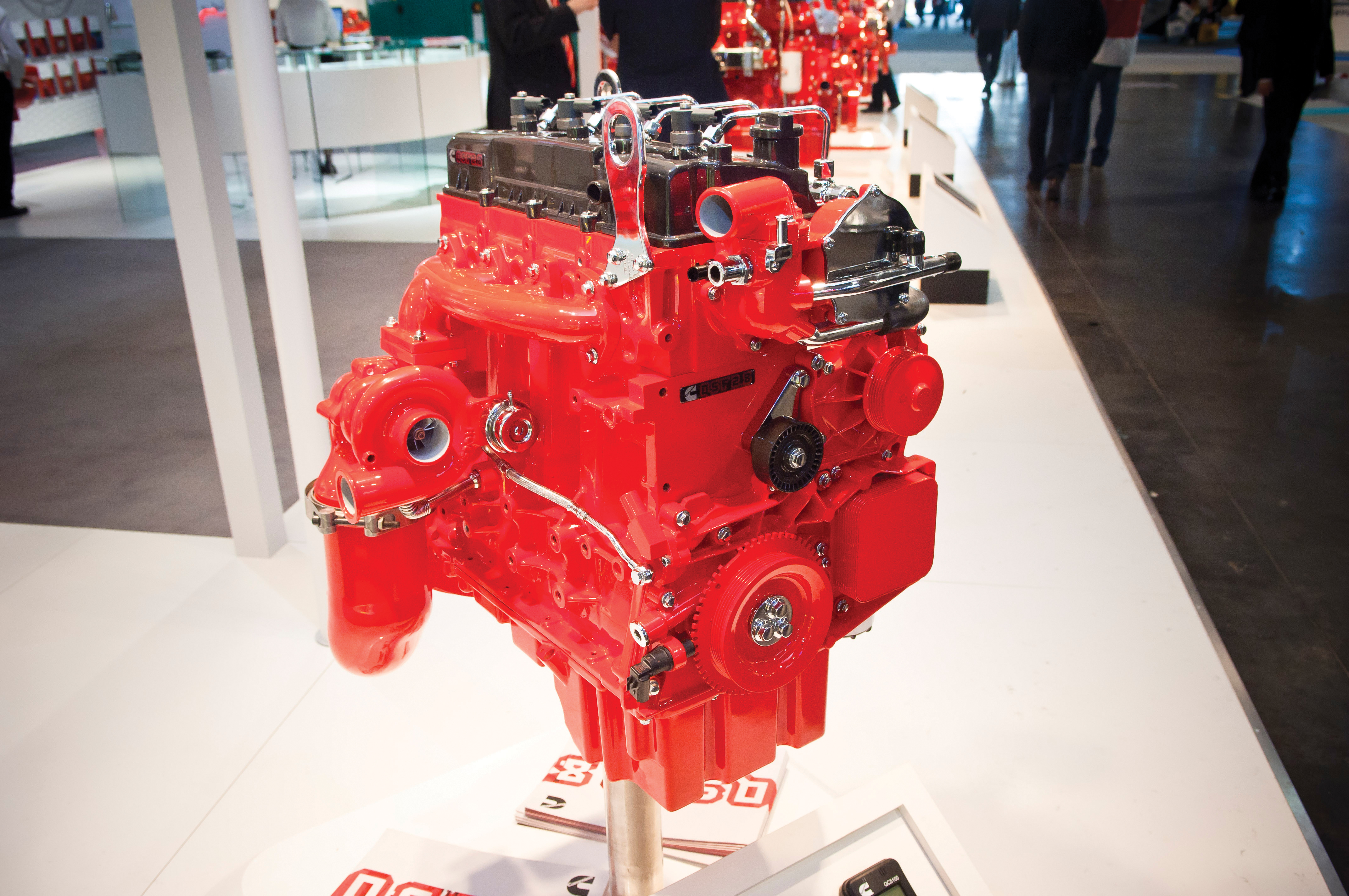
The QSF2.8 engine is the new compact Cummins unit with sophisticated controls
Innovative technology is use is providing efficient, clean burning engines - Mike Woof reports
The development of new diesel engine technology has, for the off-highway equipment sector, been the single most expensive research field for the industry since these machines first started being manufactured. Aimed at reducing the emissions of nitrous oxide as well as particulate matter, in a phased series of stages the engine emission improvements will make major changes to the construction sector. In real world terms, the total quantities of exhaust emissions from construction machines are miniscule when compared with those from the transport sector. Yet legislating bodies have opted to introduce the requirements for North America, the EC and Japan, so engine suppliers and equipment manufacturers have had to comply.This research and development has come at a major financial cost for the engine firms and, combined with the additional cost of the emissions control equipment needed, results in customers having to pay more for the new diesels. Fuel quality is another important issue as the low emission engines can only run on high quality diesel with very low sulphur content. High sulphur fuels used in some countries would cause rapid wear and failure. This in itself has created another issue, as machines in developed countries have traditionally been sold off secondhand to developing countries. Questions remain as to how this will affect secondhand machine sales and resale values, whether engines can have emissions equipment removed, or whether those developing countries will soon have cleaner fuels available.
But there have been benefits for customers. The development of these new generation engines has resulted in diesels that are not only cleaner and quieter in operation, but also deliver better economy with fuel savings ranging generally from 5-10%, and provide overall performance increases. To meet the new emissions regulations many firms have been concentrating on smaller, more compact engines that deliver greater power outputs. This has allowed equipment firms to select diesels with smaller blocks and retain low profile machine designs for operator visibility for instance.
One of the key technologies has been the development of new generation, high pressure fuel systems. Different firms have varying technologies for fuel delivery but these include multiple fuel bursts, combined with optimised inlet and head design to ensure that more efficient combustion occurs. Variable geometry turbochargers have been another development, with several different technologies now in use.
The rival firms have chosen from an array of technologies, using a range of similar concepts but varying the detailed design, system integration and implementation. At the same time, manufacturers have opted for varying solutions in even their own large and small engine ranges. These many different emissions control technologies have spawned an array of acronyms and notably, DOC, DPF, EGR and SCR.
Diesel oxidation catalysts (DOC) have been available for some time and are being employed by a number of engine firms as part of the emissions package. The diesel particulate filter (DPF) is being widely used by engine firms and helps reduce particulate emissions. The DPF units do require regenerating at periodic intervals, using fuel to burn out accumulated particulates as the machine operates, while also needing replacement at set intervals. With exhaust gas recirculation, a portion of the exhaust gas is flowed back into the inlet, which lowers combustion temperature, reducing emissions of nitrogen dioxide. Meanwhile selective catalytic reduction (SCR) is used to convert nitrogen oxides into nitrogen and water, with the aid of a catalyst.
For
At the smaller end of the market, the QSF2.8 from
For the Tier 4 Interim/Stage IIIB emissions requirements,
John Deere has said that it will now use SCR technology in its engines to meet Stage IV/Tier 4 Final compliance. The company originally said it was keen to employ other technologies to achieve the necessary performance but after extensive research, decided SCR was its best option for minimising NOx and particulate emissions. The company will use an SCR catalyst and diesel exhaust fluid dosing unit on diesels in its line-up with power ratings from 56-560kW. The SCR exhaust catalyst and exhaust fluid dosing technology will be integrated with the firm’s existing EGR, DOC and DPF systems used on the Tier 4 Interim/Stage IIIB compliant engines. This new package is called the Integrated Emissions Control system and has been specifically developed for use in rugged off-highway applications.
This will then be followed by engines having lower power outputs, and with the entire Stage 4 Final/Tier IV range being available to markets where compliance is required by 2016.
The 2.5litre and 3.4litre engines also offer greater capacity than the firm’s previous diesels, with the previous range having been topped by a 2.2litre unit. High power densities are claimed for the new engines, the 3.4litre diesel is rated at up to 100kW, allowing machine manufacturers to use a diesel with a smaller block than was possible in the past. Meanwhile fuel consumption has been reduced by some 15%, although the new emissions technology means that the diesels will be up to 20% more costly than previous engines from the firm.
For
In addition, another benefit is that the emissions equipment can be mounted up to 1.8m from the actual engine. Meanwhile, the removal of the previous active regeneration system makes the whole unit some 30kg lighter and the new engine is also said to offer a saving on fuel of up to 8%.
The new diesels from Scania use a compact DOC that is integrated into the SCR package, reducing space requirements and making the engine package easier to install on machines.
This is an important point as the engines will allow machine manufacturers to retain low profile engine covers that help deliver all-round visibility. The technology has been developed along modular lines to suit use on the five and six cylinder engines, as well as the 16litre V8 in the line-up. The firm is also considering adding an exhaust brake to ensure that the SCR system continues operating effectively when the engine is running in light load conditions.
For the Tier 4 Final/Stage IV regulations commencing in 2014, Volvo Construction Equipment’s sister firm
The company says that this will also avoid problems of exhaust gas condensation and any associated corrosion that would require replacement of components. According to Volvo Penta, key benefits include removing the need for DPF regeneration and reducing the need for changes to the engine installation. At the same time, the engines will deliver optimised fuel consumption and low operating costs.
The company intends to offer five basic engines: the 5litre D5; the 8litre D8; the 11litre D11; the 13litre D13; and the 16litre D16. The four larger engines are all six cylinder units, while the all-new D5 is a four cylinder engine offering power outputs from 105-160kW and a maximum torque rating of 900Nm. Like the D5, the D8 is also all-new, with power ratings from 160-235kW and a maximum torque of 1,300Nm. The D11, D13 and D16 have power ratings of 235-285kW, 285-405kW and 405-565kW as well as maximum torque outputs of 1,950Nm, 2,650Nm and 3,200Nm respectively.
Moving back down the engine output scale,
These diesels meet the Tier 4 Interim/Stage IIIB emissions requirements and are based on the earlier TNV units from the firm. A new diagnostic system called Yanmar SA-D, and the firm’s SA-R remote monitoring system also provide real-time engine status and allow pro-active servicing to be carried out. There are 10 new engines from Yanmar in the line-up, with either direct or indirect fuel injection and power outputs from 10-56kW, while some feature three cylinders and others have four cylinders.