The evolution of the diesel engine continues as ever more sophisticated technologies come into use - Mike Woof writes
A major focus for diesel engine suppliers is for the development of low emission technologies. Tough regulations are in force in North America and Europe with regard to emissions, a programme introduced to help reduce pollution from off-highway machines. These technologies are also being introduced in stages in other territories, with China now rolling out tougher regulations.
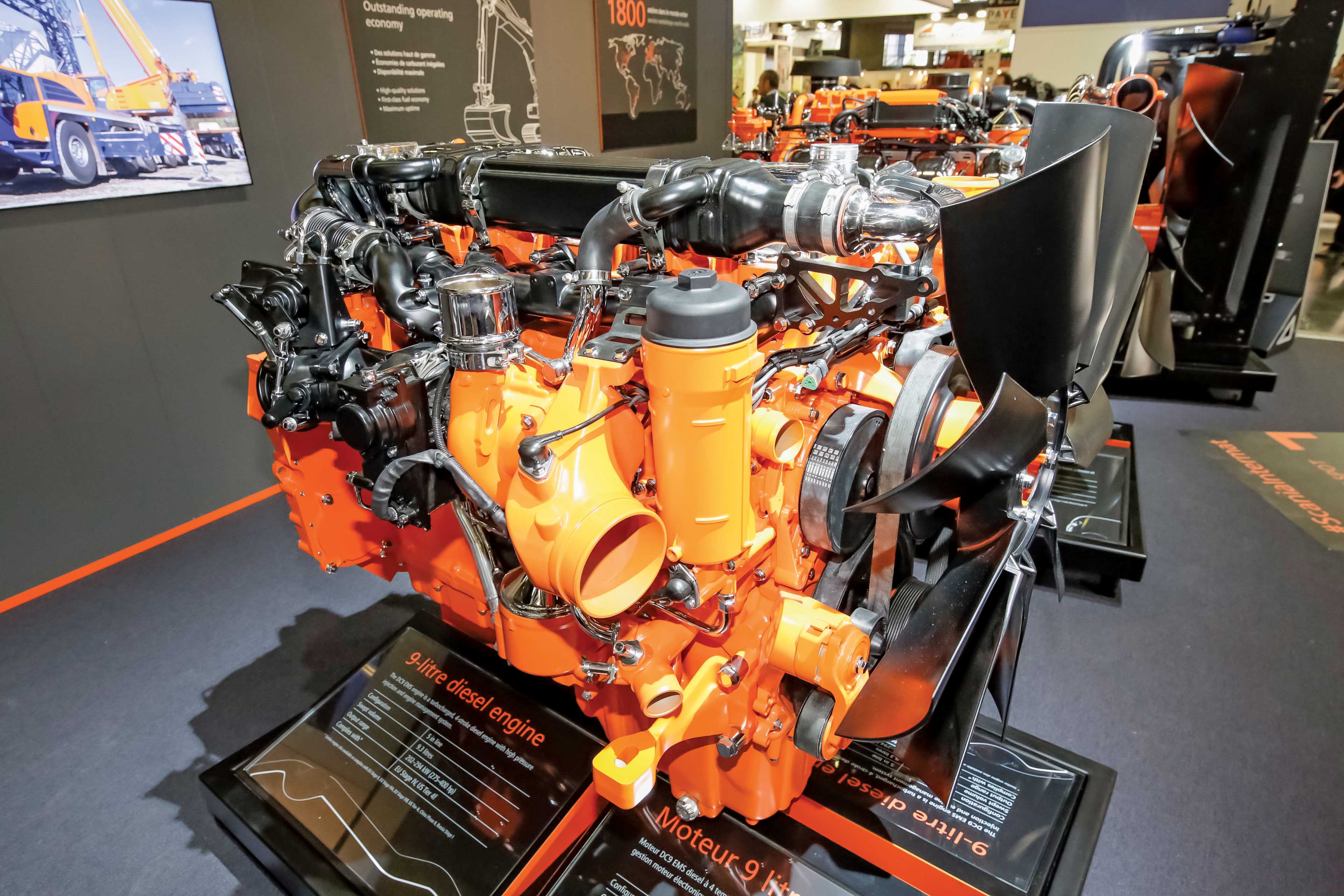
Scania has opted to use EGR in its 9litre diesel for customers in North America and Europe
The evolution of the diesel engine continues as ever more sophisticated technologies come into use - Mike Woof writes
A major focus for diesel engine suppliers is for the development of low emission technologies. Tough regulations are in force in North America and Europe with regard to emissions, a programme introduced to help reduce pollution from off-highway machines. These technologies are also being introduced in stages in other territories, with China now rolling out tougher regulations.
The different manufacturers have developed a wide array of innovative solutions for cutting engine emissions. While addressing the necessary NOx and particulates output, the companies have also managed to extend service schedules and cut fuel consumption, while increasing power and torque. Modular systems have been employed, with the companies combining different separate units to achieve the targets for the varying engine power classes.
However, not all the developments have been for new low emission engines. Some engine manufacturers have been working on systems that will allow customers to remove emission control technologies. This is of key importance for the second-hand construction machine market as it will allow the sale of machines from those markets with strict emissions legislation, North America and Europe, into developing markets where the necessary low sulphur fuels are not available.
255 JCB was one of the first firms to offer this as an option with a comparatively simple system allowing its dealers to remove the emissions kit from its engines. Meanwhile 7659 Volvo Construction Equipment is also offering a system that allows its Stage IIIB/Tier 4 Interim compliant engines to run on high sulphur fuels, without risk of damage.
But minimising emissions from diesels has represented the main focus for research and development for engine manufacturers for the past 15 years. Although developed for the European and North American markets, the technological advances seen in these newer engines will also be of benefit for customers elsewhere and in spreading the investment in research and development. The low emission engines feature sophisticated technology, which makes them more costly. But manufacturers have tried to cut running costs by making the engines more fuel-efficient and also by increasing power densities. This has allowed smaller engines to take the place of larger units seen in older machines.
As one of the world’s major suppliers of off-highway diesels,196 Cummins has understandably invested heavily in meeting the emissions requirements. The company says it has developed a single module that can carry out both diesel particulate filter (DPF) and selective catalytic reduction (SCR) functions. Because both duties are handled by a single unit, this reduces the amount of space required and the system is said to be some 60% more compact than the conventional twin component offering. This innovation is of note as it allows the after-treatment package to be more compact, a key development given the bulk of earlier generation systems and the challenges these have presented for installing the units in machines.
This system will be suitable for use with the firm’s Stage V compliant diesels, which are due to reach the European market in 2019. The firm has also developed its EcoFit UL2 liquid-only urea dosing system to help lower NOx emissions while also reducing both fuel and AdBlue consumption.
Part of the2729 Fiat Group, 7935 FPT Industrial is a major supplier for diesel engines also and the firm is working on an SCR solution to meet the coming Stage V emissions legislation that will commence in 2019. However the company believes it can meet the emissions requirements while avoiding the utilisation of the exhaust gas recirculation (EGR) systems being used by the majority of the suppliers in the market. The firm’s innovative Hi-eSCR package is already available on the Tier 4 Final/Stage IV compliant engines and will be further refined to meet the Stage V requirements. When the Stage V legislation commences, FPT Industrial aims to integrate the DPF unit within the Hi-eSCR package. According to FPT Industrial, its novel emissions control package will be more compact than other systems as a result, as well as being less costly. This package does away with the need for other systems and because the package takes up less space under the engine cover it should be easier to install. As it does not require EGR, it also means there is no need for additional cooling. This is an important point as EGR technology would otherwise further add to the cost and complexity, while increasing the need for noise attenuation to damp down the sound of the larger capacity cooling fans.
Meanwhile FPT Industrial believes that its recently introduced R22 diesel will meet demands from equipment firms for a fuel-efficient, low emission diesel for powering compact machines. This 2.2litre diesel is a three- cylinder engine and meets Tier 4 Final emissions requirements, while offering service intervals of up to 600 hours. Its exhaust emissions are minimised thanks to a combination of diesel oxidation catalyst (DOC) and partial flow filter (PFF) technologies in a single package.
JCB is another engine producer that has decided to avoid using a DPF in its Stage IV/Tier 4 Final compliant diesels, so as to reduce the cost and complexity of its products. The engines achieve the necessary low emissions performance using SCR technologies, a configuration that helps reduce the space needed for the engine installation, as well as optimising fuel consumption. The company says that demand for its engines is also increasing from OEMs due to the combination of fuel-efficient technology and compact diesel design.
John Deere Power Systems is using an array of emissions solutions for its new 2.9litre, 4.5litre, 6.8litre and 13.5litre capacity diesel engines so as to meet the Stage IV/Tier 4 Final requirements. The solutions are suited to the respective engine power classes and the market needs for each segment.
The firm has developed an exhaust filter system that combines DOC and DPF functions for its more compact diesels with power outputs of 36-55kW, but without the need for more complex EGR or SCR technology. The engines with ratings of 56-104kW meanwhile will utilise both cooled EGR and an integrated emissions control (EIC) package comprising both SCR and DOC technologies. The company is using a system comprising cooled EGR, EIC and a DOC for its more powerful engines, with ratings up to the maximum 448kW from the 13.5litre unit.
Modular engine technologies are also being used by759 Scania for its 9litre, 13litre and 16litre engines. The Stage IV/Tier 4 Final compliant diesels feature EGR and SCR systems but do not require a DPF. The low emissions engine technology has been developed in-house, although Scania also offers these diesels for use in non-regulated markets without access to clean, low sulphur fuel. The external dimensions of the engines for non-regulated markets are however the same as the emission complaint units for sale in North America and Europe, a feature that simplifies installation for equipment manufacturers.
The 9litre engine variants are six-cylinder diesels with power ratings from 202-294kW. Also featuring the six-cylinder configuration, the 13litre engines are available with power ratings from 257-405kW. Scania’s 16litre engines use the V8 configuration meanwhile and have power ratings from 405-566kW.
Although best known for its automotive products, the3503 Volkswagen Group is now looking to build market share in the off-highway equipment market. The firm has a broad range of diesels from both its VW and MAN truck brands, with the 2litre engine used in the automotive sector now available in a 44kW variant for off-highway machines also. At the moment this is offered in a Tier 4 Final version but new filters and upgraded electronics will allow it to meet the upcoming Stage V requirements for the EU. A novel continuous regeneration trap (CRT) will help minimise emissions and the engine will be aimed at installations for compact equipment.
Volvo Penta now has the new 5litre D5 and 8litre D8 diesel engines available in a range of variants so as to suit different markets. These are said to be around 2.5% more fuel-efficient than the engines they replace as well as having an increase in torque at low engine speeds. Because the firm is an international player in the off-highway engine market783 Volvo Penta offers the D5 and D8 in a range of variants to suit differing market needs depending on local emissions requirements.
The company has Tier 2, Tier 4 Interim and Tier 4 Final versions of the engines, with this last featuring an SCR package to minimise emissions. The engine does not require either a DPF or diesel oxidation catalyst (DOC) however, which makes the units easier to install.
Volvo CE is introducing a novel high sulphur conversion kit for medium-duty engines. This system will allow customers to resell Tier 4 Interim/Stage IIIB-complaint compliant machines into less regulated markets. When this kit has been used, the engines are able to run on fuel used in countries with lower emissions regulations for off-road vehicles, where fuels typically have higher sulphur levels than in regulated markets.
The conversion kit is available for a range of Volvo CE machines, including wheel loaders, excavators, compactors and pavers. It is compatible with Volvo D4H, D6H and D8H medium-duty engines, and allows the use of fuels with a sulphur content of between 500 ppm and 10000 ppm.
The conversion process involves changes to the hardware and software of the engine. Six hardware kits and 28 new engine part numbers are needed to perform the conversion, and new software will be run separately at a Volvo CE back office to finalise the process when the new components are fitted.
The work can be carried out by a Volvo CE dealer in a country that does not have emissions regulations. Assistance is required by the Volvo CE Global Parts department and approval for the conversion can be given when the work is complete.
The kit works by deactivating the exhaust gas recirculation (EGR) system and replacing the diesel particulate filter and diesel oxidation catalyst with a conventional muffler. This reduces the functionality of the engine and allows it to run on fuels with higher levels of sulphur. Once completed, the conversion is permanent however and the engine can no longer be used in regulated markets.
A major focus for diesel engine suppliers is for the development of low emission technologies. Tough regulations are in force in North America and Europe with regard to emissions, a programme introduced to help reduce pollution from off-highway machines. These technologies are also being introduced in stages in other territories, with China now rolling out tougher regulations.
The different manufacturers have developed a wide array of innovative solutions for cutting engine emissions. While addressing the necessary NOx and particulates output, the companies have also managed to extend service schedules and cut fuel consumption, while increasing power and torque. Modular systems have been employed, with the companies combining different separate units to achieve the targets for the varying engine power classes.
However, not all the developments have been for new low emission engines. Some engine manufacturers have been working on systems that will allow customers to remove emission control technologies. This is of key importance for the second-hand construction machine market as it will allow the sale of machines from those markets with strict emissions legislation, North America and Europe, into developing markets where the necessary low sulphur fuels are not available.
But minimising emissions from diesels has represented the main focus for research and development for engine manufacturers for the past 15 years. Although developed for the European and North American markets, the technological advances seen in these newer engines will also be of benefit for customers elsewhere and in spreading the investment in research and development. The low emission engines feature sophisticated technology, which makes them more costly. But manufacturers have tried to cut running costs by making the engines more fuel-efficient and also by increasing power densities. This has allowed smaller engines to take the place of larger units seen in older machines.
As one of the world’s major suppliers of off-highway diesels,
This system will be suitable for use with the firm’s Stage V compliant diesels, which are due to reach the European market in 2019. The firm has also developed its EcoFit UL2 liquid-only urea dosing system to help lower NOx emissions while also reducing both fuel and AdBlue consumption.
Part of the
Meanwhile FPT Industrial believes that its recently introduced R22 diesel will meet demands from equipment firms for a fuel-efficient, low emission diesel for powering compact machines. This 2.2litre diesel is a three- cylinder engine and meets Tier 4 Final emissions requirements, while offering service intervals of up to 600 hours. Its exhaust emissions are minimised thanks to a combination of diesel oxidation catalyst (DOC) and partial flow filter (PFF) technologies in a single package.
JCB is another engine producer that has decided to avoid using a DPF in its Stage IV/Tier 4 Final compliant diesels, so as to reduce the cost and complexity of its products. The engines achieve the necessary low emissions performance using SCR technologies, a configuration that helps reduce the space needed for the engine installation, as well as optimising fuel consumption. The company says that demand for its engines is also increasing from OEMs due to the combination of fuel-efficient technology and compact diesel design.
John Deere Power Systems is using an array of emissions solutions for its new 2.9litre, 4.5litre, 6.8litre and 13.5litre capacity diesel engines so as to meet the Stage IV/Tier 4 Final requirements. The solutions are suited to the respective engine power classes and the market needs for each segment.
The firm has developed an exhaust filter system that combines DOC and DPF functions for its more compact diesels with power outputs of 36-55kW, but without the need for more complex EGR or SCR technology. The engines with ratings of 56-104kW meanwhile will utilise both cooled EGR and an integrated emissions control (EIC) package comprising both SCR and DOC technologies. The company is using a system comprising cooled EGR, EIC and a DOC for its more powerful engines, with ratings up to the maximum 448kW from the 13.5litre unit.
Modular engine technologies are also being used by
The 9litre engine variants are six-cylinder diesels with power ratings from 202-294kW. Also featuring the six-cylinder configuration, the 13litre engines are available with power ratings from 257-405kW. Scania’s 16litre engines use the V8 configuration meanwhile and have power ratings from 405-566kW.
Although best known for its automotive products, the
Volvo Penta now has the new 5litre D5 and 8litre D8 diesel engines available in a range of variants so as to suit different markets. These are said to be around 2.5% more fuel-efficient than the engines they replace as well as having an increase in torque at low engine speeds. Because the firm is an international player in the off-highway engine market
The company has Tier 2, Tier 4 Interim and Tier 4 Final versions of the engines, with this last featuring an SCR package to minimise emissions. The engine does not require either a DPF or diesel oxidation catalyst (DOC) however, which makes the units easier to install.
Volvo CE is introducing a novel high sulphur conversion kit for medium-duty engines. This system will allow customers to resell Tier 4 Interim/Stage IIIB-complaint compliant machines into less regulated markets. When this kit has been used, the engines are able to run on fuel used in countries with lower emissions regulations for off-road vehicles, where fuels typically have higher sulphur levels than in regulated markets.
The conversion kit is available for a range of Volvo CE machines, including wheel loaders, excavators, compactors and pavers. It is compatible with Volvo D4H, D6H and D8H medium-duty engines, and allows the use of fuels with a sulphur content of between 500 ppm and 10000 ppm.
The conversion process involves changes to the hardware and software of the engine. Six hardware kits and 28 new engine part numbers are needed to perform the conversion, and new software will be run separately at a Volvo CE back office to finalise the process when the new components are fitted.
The work can be carried out by a Volvo CE dealer in a country that does not have emissions regulations. Assistance is required by the Volvo CE Global Parts department and approval for the conversion can be given when the work is complete.
The kit works by deactivating the exhaust gas recirculation (EGR) system and replacing the diesel particulate filter and diesel oxidation catalyst with a conventional muffler. This reduces the functionality of the engine and allows it to run on fuels with higher levels of sulphur. Once completed, the conversion is permanent however and the engine can no longer be used in regulated markets.