Wirtgen’s HT22 quick-change toolholder system is said to ensure maximum milling performance and cost -fficient operation.
A longer service life and fewer downtimes are achieved through various HT22 features, such as the significantly enlarged contact areas between the upper and lower parts of the toolholder system.
Consequently, the high cutting forces are reliably transferred to the lower part of the system, substantially increasing the useful life of the milling drum. A larger shank cross-section a
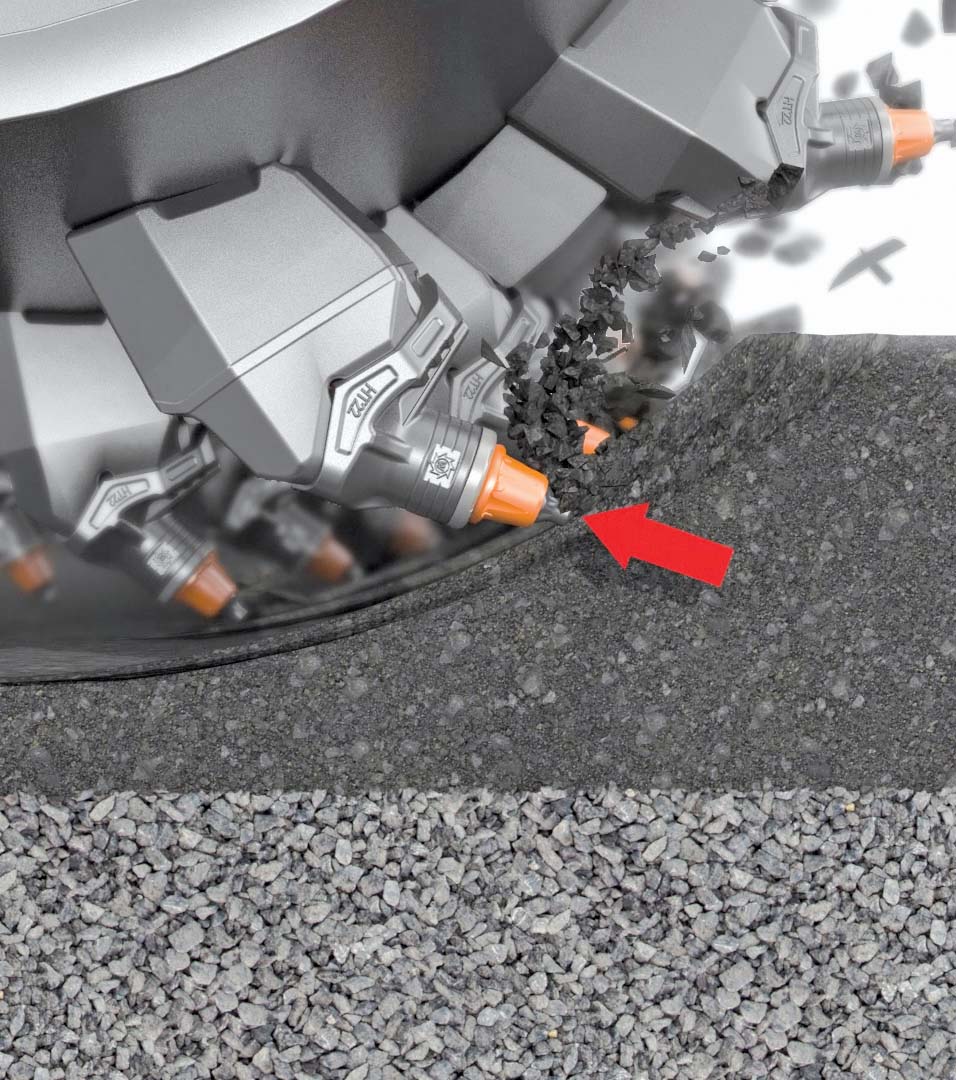
The optimised shank geometry of the upper part of the quick-change toolholder system is extremely strong and provides greater resistance to undesired deformation
A longer service life and fewer downtimes are achieved through various HT22 features, such as the significantly enlarged contact areas between the upper and lower parts of the toolholder system.
Consequently, the high cutting forces are reliably transferred to the lower part of the system, substantially increasing the useful life of the milling drum. A larger shank Cross-section and the optimised shank geometry increase the strength of the shank, thus providing greater resistance to undesired deformation. The maximum longitudinal wear of the upper part of the toolholder is also double that of the conventional version. Service intervals have now been extended from 250 hours to 500 hours thanks to the HT22 quick-change toolhandler system's more robust construction.
All new Wirtgen cold milling machines have been equipped with the new HT22 quick-change toolholder system since October 2013. Machines put into service earlier can easily be retrofitted with the new system, providing customers with the Ideal tools for future milling jobs.