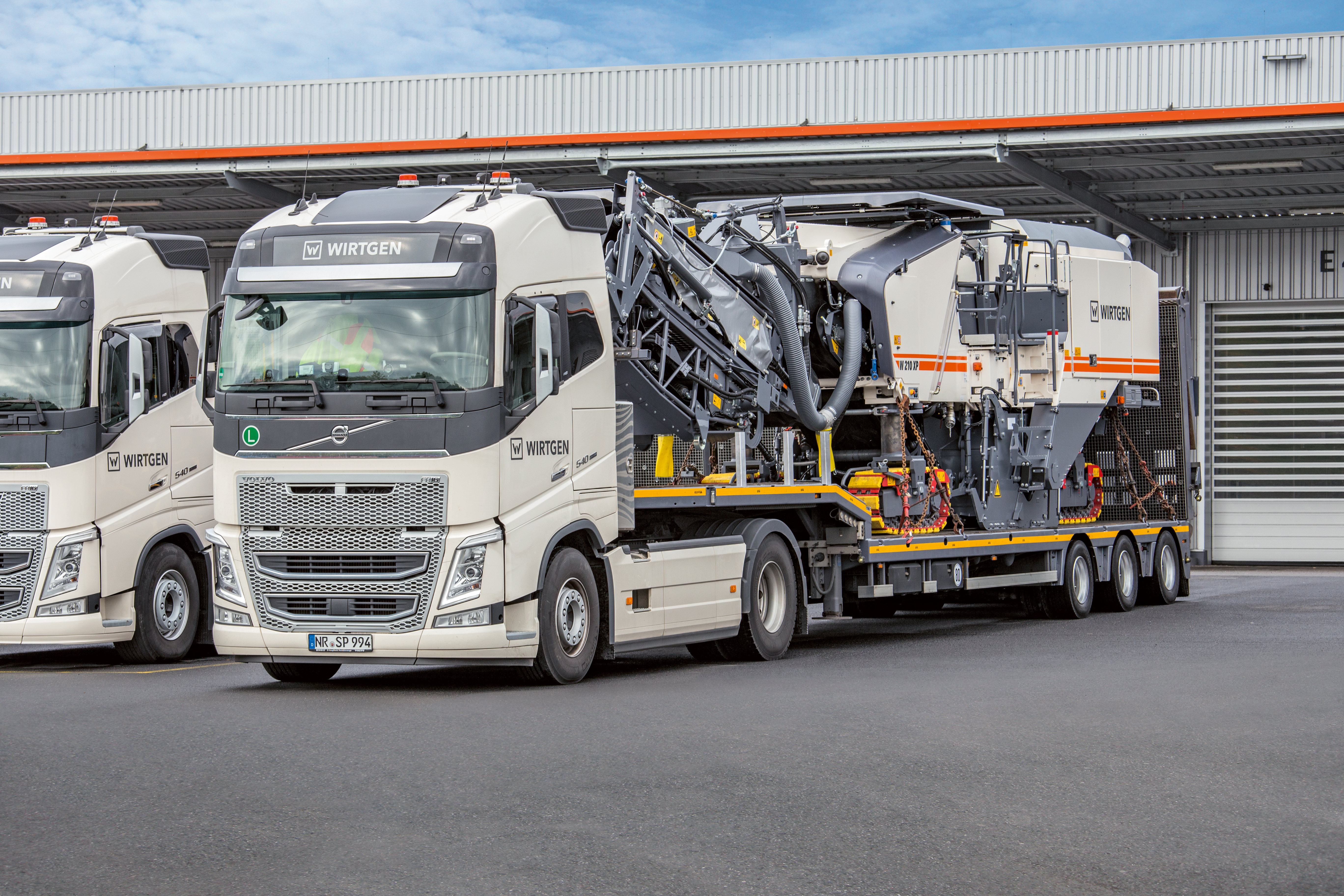
From
The machines are powered by the Cat C18 ACERT diesel, which delivers 563kW and meets the Tier 4 Final/ Stage IV emissions standards. The mounting of the engine is designed to minimise vibration while the machine features a cooling system with an on-demand, variable-speed fan.
The PM820, PM822, and PM825 are hydrostatically driven by two variable-displacement propel pumps. Four-mode steering is standard, with a true-tracking alignment function providing steering precision, smoother cornering, and reduced track wear. The machines use a four-post design, with each leg post featuring an auto-levelling function for precise height adjustment.
The rotor is equipped with three-piece, quick-release tool holders and carbide-tipped cutting bits. Optional rotor systems are available, as are Cat Diamond Bits for precision cutting in specific applications. The cutting chamber has a design that is said to improve material flow, reduce wear on the chamber, and allow flush-cutting.
Chamber side plates move by independent hydraulic cylinders equipped with position sensors, ensuring that the side plates float at the proper level and eliminate binding. The rotor drive is belt-driven and the machine has three cutting settings to match rotor speed/torque with the conditions.
Optional diamond bits last up to 80 times longer than conventional carbide bits, extending intervals between bit maintenance, increasing production and reducing operating costs. These also reduce maintenance needs, improve fuel economy and cut machine vibration.
The PM820, PM822, and PM825 can be equipped with the optional, integrated Cat Grade Control system, which is a 2D-capable/3D-ready grade-and-slope system that automatically controls a preset rotor depth and cross slope. The system can be upgraded for full 3D control with the addition of optional equipment.
Meanwhile,
The W 210 XP comes equipped with a 2m milling drum unit as standard. However units with milling widths of 1.5m and 2.2m are also available as options. The machine has Wirtgen's Flexible Cutter System Light (FCS Light), which is said to increase versatility and utilisation. Both the 2m and 2.2m milling drums are FCS Light-compatible. This allows milling drums of the same width but with different tool spacings to be fitted without difficulty as required for the job at hand. All the milling drums are fitted with Wirtgen's HT22 quick-change toolholder system. The robust upper part of the system can be easily and quickly changed directly on site. This is said to reduce machine downtime and increase the lifespan of the milling drum.
Compact dimensions and comparatively low machine transport weight allow the
W 210 XP to be easily moved from one site to the next. As a result, the high-performance milling machine can be up and running in no time. Without the 29tonnes of water in its tank, transport weight is low so the machine can be moved on a light low-bed truck. Customers can get their large milling machine to its next job at a fraction of the cost.
The machine has an ergonomically designed operator platform. Most functions can be controlled by the multifunctional joystick mounted in the armrest. In this way, the operating concept of the new W 210 XP, devised by the Wirtgen designers with great attention to detail, allows high daily production rates.