A series of developments in the milling machine market will give customers both greater choice and performance – Mike Woof writes.
Competition is heating up in the market for milling machines, which has been dominated for many years by Wirtgen. The German firm still retains a strong share of this market, but is now facing much tougher levels of competition from key rivals, and Atlas Copco, BOMAG, Caterpillar and Roadtec in particular. Meanwhile the market is also seeing the return of another familiar nam
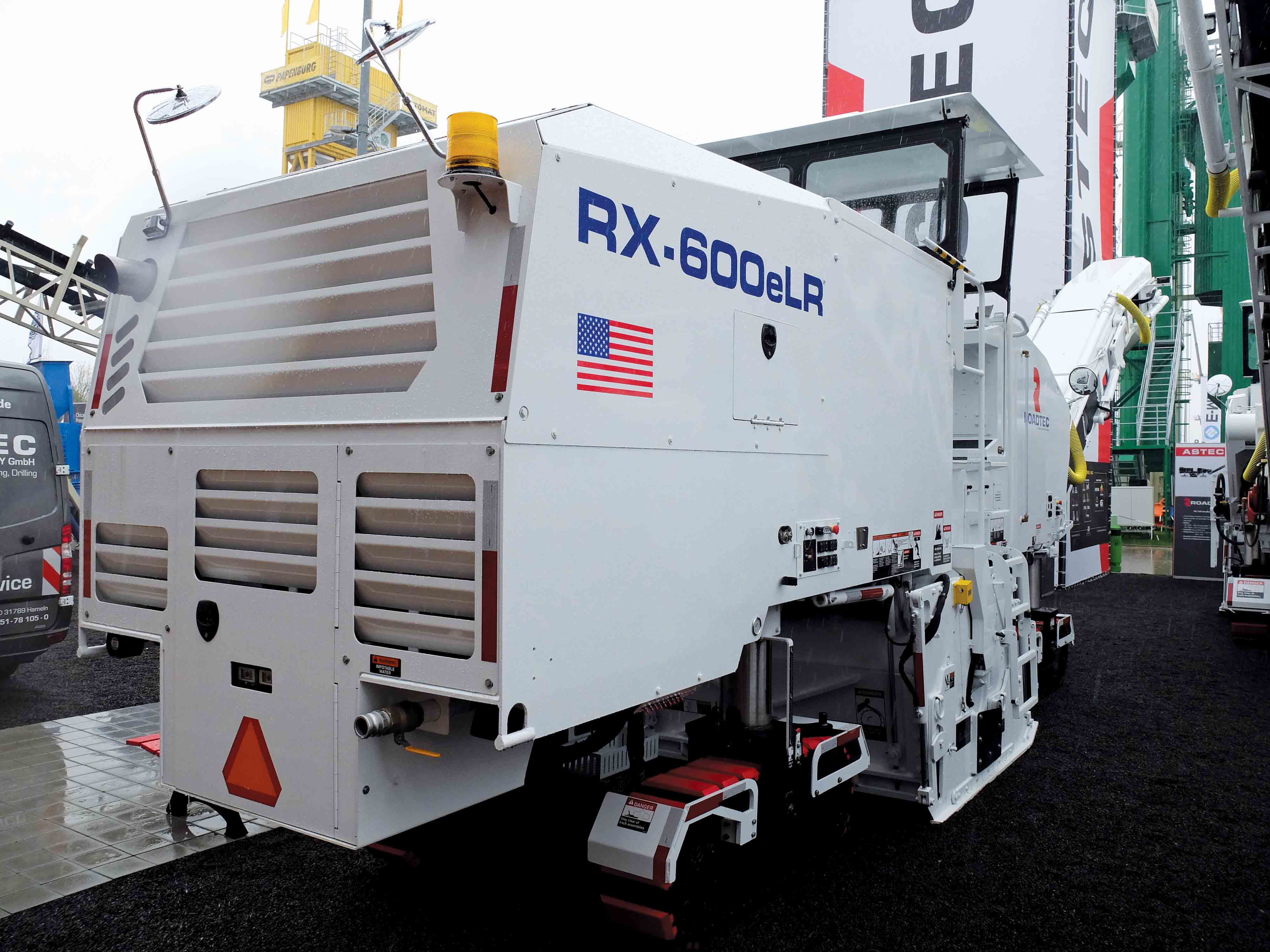
Roadtec’s new RX-600eLR offers a high level of versatility for a machine of its size
A series of developments in the milling machine market will give customers both greater choice and performance – Mike Woof writes.
Competition is heating up in the market for milling machines, which has been dominated for many years by2395 Wirtgen. The German firm still retains a strong share of this market, but is now facing much tougher levels of competition from key rivals, and 161 Atlas Copco, 172 BOMAG, 178 Caterpillar and 1252 Roadtec in particular. Meanwhile the market is also seeing the return of another familiar name to the fold, CMI, although it is still early on in the brand’s relaunch. It is worth noting that much of the innovation in the milling machine market is focussed at the larger end of the market. BOMAG and Wirtgen have developed new compact milling machines in addition to larger units but for the other players, the focus is on bigger equipment and the 2m class in particular.
BOMAG’s revised milling machine line now stretches from compact models up to the large, highway class units. There is a new model for the 500mm class in the shape of the BM500/15 and for the 1m class with the BM1000/35, BM1200/35 and BM1300/35. All of these units are said to be manoeuvrable, versatile and productive. But at the larger end of its range, the company has augmented its existing 2m class model, the BM2000/60, with the addition of the more powerful BM2000/75 and BM2200/75. The BM2000/60 and BM2000/75 have the same basis structure and a cutting width of 2m, but the latter machine has a more powerful engine delivering 567kW, which is said to increase productivity. The same diesel powers the BM2200/75, which also has a 350mm maximum cutting depth and is again based on the same basic chassis, but offers a cutting width of 2.2m.
The206 Dynapac PL2000 milling machine from Atlas Copco Road Construction Equipment can handle milling widths of 2.1m and milling depths of 320mm. Power comes from a 196 Cummins diesel and the firm claims that the PL2000 offers strong traction power, optimised performance and low operating costs. The firm offers the machine in either Tier 3 or Tier 4 versions, depending on the emissions requirements of the local market.
According to the firm the new PL2000 is efficient and offers high milling performance, while being cost-effective for users. The machine runs on four crawlers and has low operating noise, while it is said to be stable in operation and highly durable. Ergonomic controls and a vibration damped operator station make the machine easier to use for longer periods. The two-stage, covered front-loading conveyor belt is said to offer a long working life, while the machine is said to have an efficient levelling system to compensate for uneven ground. Meanwhile it also has a quick-change tool holder system, allowing faster replacement of cutters and reducing downtime.
Caterpillar’s new PM620 milling machine is aimed at the 2m class, with a 2.2m version called the PM622 coming to market soon. The firm says that the 2m class is significant and estimates that this segment represents around 35-40% of the market for milling machines. Power comes from a Cat C18 diesel rated at 470kW, which meets Tier 4 Final emissions requirements and has a mounting designed to minimise working vibration. Operating weight for the PM620 is around 33.33tonnes, while when ready for transport the machine weighs 29.4tonnes. Operating weight for the PM622 is 33.9tonnes and the machine weighs 30tonnes when ready for transport.
Four steering modes are fitted for manoeuvrability and the machine has a turning radius of 2m despite its size. Auto levelling is fitted while there is a hold button that pauses operations during truck changes. The PM620 features an 85mm wide conveyor that can be raised and lowered and can slew 60° to either side. A company representative said, “You can discharge to a truck in the next lane or when rounding a curve.”
The rotor drive offers three cutting speeds while the machine has an automatic load control function that optimises performance during operation, while the machine can use the new Cat diamond cutters. A sideplate is fitted that is moved up and down by smart cylinders and offers an auto-averaging system. The controls, meanwhile, are the same as on Caterpillar’s new F-Series pavers, with tough and durable touch screens. Electronics and various other systems are also shared with the F-Series pavers, as is the Cat Grade Control technology for more accurate working and with a choice of 2D or 3D systems. Smart features include an automatic plunge cut system that eases the rotor into the start of the cut and a cross communication function that allows the operator to view and change the settings of control boxes located on the opposite side of the machine. There is also a cross-coupling system that works when an adjustment is made to the grade or slope of one side of the machine, so that the opposite side will automatically adjust based on the command parameters.
A dust extraction system can be fitted that collects dust from the conveyor and cutting chamber. Water capacity is 3,400litres and a standard water spray system is fitted on the conveyor and inside the cutter drum, while the machine has the option of an additional water spray system if required. The machine also has numerous storage areas for tools, lubricants and cutter bits, a feature requested by customers.
After a long break, the CMI brand is now returning to the milling machine market with a new range aimed primarily at the heavy end of the market. The company is part of the same group as UK-based739 Parker Plant and is building its products in the US state of Iowa. At the moment the RM-7 Roto-Mill is the only milling machine available from the firm, but others models are in development, all of which share novel design of cutter housing geometry that is said to allow efficient discharge of milled materials. Power for the RM-7 comes from a 563kW diesel, driving the cutter drum through conventional belts. Standard cutting width is 2.18m with a maximum cutting depth of 356mm. A three-track version is available that weighs 36.3tonnes, while the four-track variant weighs 38.6tonnes.
The most compact model is the RM-4, which is available with wheels or tracks and weighs 18.4tonnes or 18.9tonnes respectively. It has a maximum cutting width of 1.22m and a maximum cutting depth of 300mm, with power from a 330kW diesel.
The RM-6 model offers a 2.18m cutting width and a maximum 355mm deep cut. Power comes from a 447kW diesel while the machine is offered in three- or four-track variants weighing 34.5tonnes and 36.9tonnes respectively.
The larger RM-9 model, meanwhile, will offer the same 2.18m cutting width as standard but will provide a maximum cutting depth of 381mm, while having options for cutting drum widths of 2.62m, 3.43m and 3.81m. The three-track variant weighs 41.1tonnes while the four-track model tips the scales at 43.7tonnes.
All of the Roto-Mill machines are powered by Cummins diesels apart from the top-of-the-line RM-12, with twin Caterpillar engines. It has a cutting width of 3.81m. This is designed for large highway and airport projects requiring large cutting widths and depths, coupled with high productivity.
A very interesting development in the milling machine sector is the approach being taken by Roadtec and Wirtgen to make large machines more versatile. The two firms are taking very different approaches to this, with Roadtec now developing its RX-600eLR milling machine for the 2m class.
This is not ready for market yet as testing is underway, but the prototype reveals the novel approach Roadtec is taking to increase the machine’s capabilities. Central to the design of the machine is the drum drive, which uses twin hydrostatic motors and with one on each side. This design does away with the need for a bulky belt drive system that sticks out from the chassis. This allows the RX-600eLR to make a milling cut flush with a kerb or New Jersey barrier on either side. And it is an important factor for operations in workzones given that road authorities do not usually allow construction machines to travel in the opposite direction from the flow of traffic.
Having a hydrostatic drive system offers other benefits too, such as fully proportional control of cutter drum speed from standstill to maximum rpm. This means that drum speed can be controlled specifically to the needs of the job and the material being cut, optimising productivity while reducing cutter wear. By comparison, a machine with a belt drive will typically have only a few drum speed options. And Roadtec also says that the system responds quickly in the event of the cutters hitting any obstructions, reducing the risk of damage.
Another important feature of the machine is that the chassis was purposely designed to be narrow, with the end of the cutter drum projecting on each side. This further helps in the machine being able to cut flush with highway barriers, even where the mill is operating on the inside of a gradual curve. With the cutter drum extending past the side of the machine, it also allows a user to cut close to an obstruction such as an inspection cover. The operator can see the end of the cutter drum and use the crab steer function to manoeuvre around the obstruction. More conventional features for the 30tonne RX-600eLR include its 503kW Cummins diesel, which meets Tier 4 Final emissions requirements, as well as dust extraction and optional grade control technology.
Also new from Roadtec is the RX-600e, now equipped with a sophisticated grade and slope control system. This offers automated control of elevation (ACE) and uses a network of grade and slope sensors combined with one central microcontroller.
The machine tips the scales at 26.9tonnes and is powered by a Cummins QSX15 diesel rated at 462kW. It is offered in three- or four-track versions and is designed to be manoeuvrable and versatile for use in urban applications. The machine can cut to depths of 330mm and can be equipped with cutter drums with widths of 1.9m, 2m or 2.2m. Roadtec has designed the cutter housing and drum along modular lines, so that these units can be changed quickly for different applications. Users can also change between drums with different cutter patterns, as well as from different tool suppliers, to better suit differing applications and customer needs. For longer working life, the walls of the cutter housing are also lined with wear plates.
Wirtgen’s answer to increasing versatility for a large milling machine is rather different, however. The firm has devised the W 200 Hi, capable of cutting a width of 2.1m and to a depth of 300mm. A key feature of this machine is the ability for its cutter drum to be shifted hydraulically from one side to the other by up to 400mm. This also allows the machine to cut close to a kerb or New Jersey barrier and on either side, so that it can continue operating in the same direction of travel as the live traffic alongside in the workzone.
This sideshift system again allows the operator to mill close to obstructions, using the steering system to move around them. The sideshift system also means the machine can mill close to a kerb or barrier on a curved section of road, despite the size of this 30.4tonne unit with its 455kW diesel. Machine also benefits from the firm’s sophisticated LEVEL PRO PLUS levelling system, which helps deliver a high quality milling finish.
The company also recently launched its W 120 Ri and W 150 CFi compact machines, with milling widths of 1.2m and 1.5m respectively. The company claims that both models offer high manoeuvrability onsite and high mobility for faster transport between jobsites.
Competition is heating up in the market for milling machines, which has been dominated for many years by
BOMAG’s revised milling machine line now stretches from compact models up to the large, highway class units. There is a new model for the 500mm class in the shape of the BM500/15 and for the 1m class with the BM1000/35, BM1200/35 and BM1300/35. All of these units are said to be manoeuvrable, versatile and productive. But at the larger end of its range, the company has augmented its existing 2m class model, the BM2000/60, with the addition of the more powerful BM2000/75 and BM2200/75. The BM2000/60 and BM2000/75 have the same basis structure and a cutting width of 2m, but the latter machine has a more powerful engine delivering 567kW, which is said to increase productivity. The same diesel powers the BM2200/75, which also has a 350mm maximum cutting depth and is again based on the same basic chassis, but offers a cutting width of 2.2m.
The
According to the firm the new PL2000 is efficient and offers high milling performance, while being cost-effective for users. The machine runs on four crawlers and has low operating noise, while it is said to be stable in operation and highly durable. Ergonomic controls and a vibration damped operator station make the machine easier to use for longer periods. The two-stage, covered front-loading conveyor belt is said to offer a long working life, while the machine is said to have an efficient levelling system to compensate for uneven ground. Meanwhile it also has a quick-change tool holder system, allowing faster replacement of cutters and reducing downtime.
Caterpillar’s new PM620 milling machine is aimed at the 2m class, with a 2.2m version called the PM622 coming to market soon. The firm says that the 2m class is significant and estimates that this segment represents around 35-40% of the market for milling machines. Power comes from a Cat C18 diesel rated at 470kW, which meets Tier 4 Final emissions requirements and has a mounting designed to minimise working vibration. Operating weight for the PM620 is around 33.33tonnes, while when ready for transport the machine weighs 29.4tonnes. Operating weight for the PM622 is 33.9tonnes and the machine weighs 30tonnes when ready for transport.
Four steering modes are fitted for manoeuvrability and the machine has a turning radius of 2m despite its size. Auto levelling is fitted while there is a hold button that pauses operations during truck changes. The PM620 features an 85mm wide conveyor that can be raised and lowered and can slew 60° to either side. A company representative said, “You can discharge to a truck in the next lane or when rounding a curve.”
The rotor drive offers three cutting speeds while the machine has an automatic load control function that optimises performance during operation, while the machine can use the new Cat diamond cutters. A sideplate is fitted that is moved up and down by smart cylinders and offers an auto-averaging system. The controls, meanwhile, are the same as on Caterpillar’s new F-Series pavers, with tough and durable touch screens. Electronics and various other systems are also shared with the F-Series pavers, as is the Cat Grade Control technology for more accurate working and with a choice of 2D or 3D systems. Smart features include an automatic plunge cut system that eases the rotor into the start of the cut and a cross communication function that allows the operator to view and change the settings of control boxes located on the opposite side of the machine. There is also a cross-coupling system that works when an adjustment is made to the grade or slope of one side of the machine, so that the opposite side will automatically adjust based on the command parameters.
A dust extraction system can be fitted that collects dust from the conveyor and cutting chamber. Water capacity is 3,400litres and a standard water spray system is fitted on the conveyor and inside the cutter drum, while the machine has the option of an additional water spray system if required. The machine also has numerous storage areas for tools, lubricants and cutter bits, a feature requested by customers.
After a long break, the CMI brand is now returning to the milling machine market with a new range aimed primarily at the heavy end of the market. The company is part of the same group as UK-based
The most compact model is the RM-4, which is available with wheels or tracks and weighs 18.4tonnes or 18.9tonnes respectively. It has a maximum cutting width of 1.22m and a maximum cutting depth of 300mm, with power from a 330kW diesel.
The RM-6 model offers a 2.18m cutting width and a maximum 355mm deep cut. Power comes from a 447kW diesel while the machine is offered in three- or four-track variants weighing 34.5tonnes and 36.9tonnes respectively.
The larger RM-9 model, meanwhile, will offer the same 2.18m cutting width as standard but will provide a maximum cutting depth of 381mm, while having options for cutting drum widths of 2.62m, 3.43m and 3.81m. The three-track variant weighs 41.1tonnes while the four-track model tips the scales at 43.7tonnes.
All of the Roto-Mill machines are powered by Cummins diesels apart from the top-of-the-line RM-12, with twin Caterpillar engines. It has a cutting width of 3.81m. This is designed for large highway and airport projects requiring large cutting widths and depths, coupled with high productivity.
A very interesting development in the milling machine sector is the approach being taken by Roadtec and Wirtgen to make large machines more versatile. The two firms are taking very different approaches to this, with Roadtec now developing its RX-600eLR milling machine for the 2m class.
This is not ready for market yet as testing is underway, but the prototype reveals the novel approach Roadtec is taking to increase the machine’s capabilities. Central to the design of the machine is the drum drive, which uses twin hydrostatic motors and with one on each side. This design does away with the need for a bulky belt drive system that sticks out from the chassis. This allows the RX-600eLR to make a milling cut flush with a kerb or New Jersey barrier on either side. And it is an important factor for operations in workzones given that road authorities do not usually allow construction machines to travel in the opposite direction from the flow of traffic.
Having a hydrostatic drive system offers other benefits too, such as fully proportional control of cutter drum speed from standstill to maximum rpm. This means that drum speed can be controlled specifically to the needs of the job and the material being cut, optimising productivity while reducing cutter wear. By comparison, a machine with a belt drive will typically have only a few drum speed options. And Roadtec also says that the system responds quickly in the event of the cutters hitting any obstructions, reducing the risk of damage.
Another important feature of the machine is that the chassis was purposely designed to be narrow, with the end of the cutter drum projecting on each side. This further helps in the machine being able to cut flush with highway barriers, even where the mill is operating on the inside of a gradual curve. With the cutter drum extending past the side of the machine, it also allows a user to cut close to an obstruction such as an inspection cover. The operator can see the end of the cutter drum and use the crab steer function to manoeuvre around the obstruction. More conventional features for the 30tonne RX-600eLR include its 503kW Cummins diesel, which meets Tier 4 Final emissions requirements, as well as dust extraction and optional grade control technology.
Also new from Roadtec is the RX-600e, now equipped with a sophisticated grade and slope control system. This offers automated control of elevation (ACE) and uses a network of grade and slope sensors combined with one central microcontroller.
The machine tips the scales at 26.9tonnes and is powered by a Cummins QSX15 diesel rated at 462kW. It is offered in three- or four-track versions and is designed to be manoeuvrable and versatile for use in urban applications. The machine can cut to depths of 330mm and can be equipped with cutter drums with widths of 1.9m, 2m or 2.2m. Roadtec has designed the cutter housing and drum along modular lines, so that these units can be changed quickly for different applications. Users can also change between drums with different cutter patterns, as well as from different tool suppliers, to better suit differing applications and customer needs. For longer working life, the walls of the cutter housing are also lined with wear plates.
Wirtgen’s answer to increasing versatility for a large milling machine is rather different, however. The firm has devised the W 200 Hi, capable of cutting a width of 2.1m and to a depth of 300mm. A key feature of this machine is the ability for its cutter drum to be shifted hydraulically from one side to the other by up to 400mm. This also allows the machine to cut close to a kerb or New Jersey barrier and on either side, so that it can continue operating in the same direction of travel as the live traffic alongside in the workzone.
This sideshift system again allows the operator to mill close to obstructions, using the steering system to move around them. The sideshift system also means the machine can mill close to a kerb or barrier on a curved section of road, despite the size of this 30.4tonne unit with its 455kW diesel. Machine also benefits from the firm’s sophisticated LEVEL PRO PLUS levelling system, which helps deliver a high quality milling finish.
The company also recently launched its W 120 Ri and W 150 CFi compact machines, with milling widths of 1.2m and 1.5m respectively. The company claims that both models offer high manoeuvrability onsite and high mobility for faster transport between jobsites.