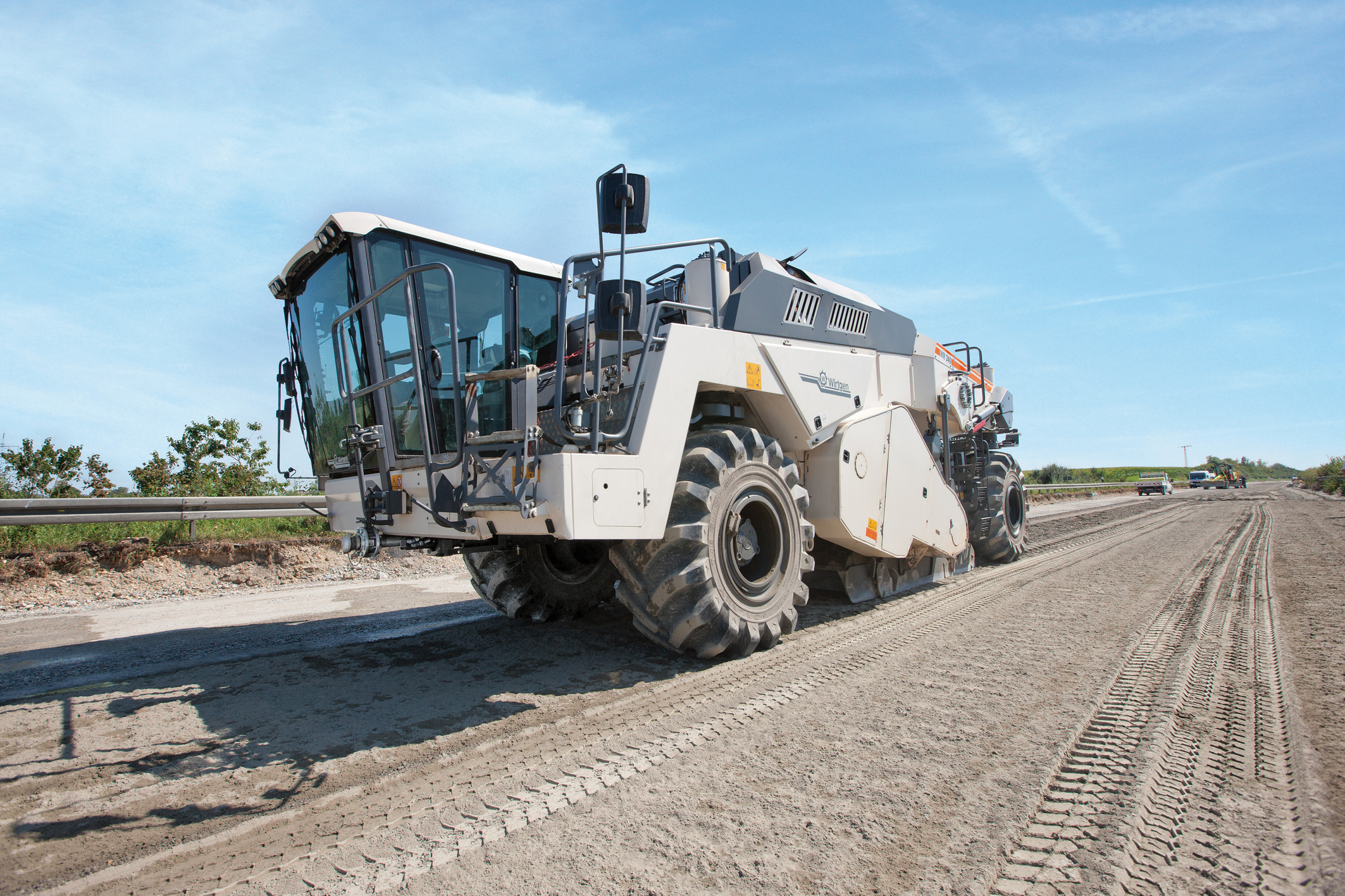
An array of new developments in the market for road recycling and stabilisation machines as well as milling equipment is now on offer - Mike Woof reports
Major new developments are being seen in the sector for road recycling and stabilisation equipment, as well as milling machines. New models are coming to market that benefit from the latest low emission engine technology to meet the increasingly tough European and North American requirements.Perhaps more importantly though, the new machines are also designed to be more efficient and precise and come with a wider range of options for road recycling tasks. In some markets and the US in particular, stabilisation and road recycling is now widely used as a way of rehabilitating roads in need of repairs. Fast and efficient, these machines offer a cost-effective way to replace worn out road surfaces. Incremental developments in the technology over time have also allowed contractors to use the machines to deliver high quality road structures able to carry heavy traffic loads. The equipment is also being used increasingly in emergent territories to recycle old roads productively, and provide a better base for a new surface.
Similarly with milling machines, manufacturers have developed more productive and efficient units that are also more versatile than before. These are able to carry out more road repair and surface recycling tasks than simply milling off a worn-out surface layer. The
This is a major development for Fayat, which has placed these new machines within its
With a transport weight of 25tonnes, the RS-446C is said to be powerful and productive, with drive from a 309kW diesel. Its two-stage engine drive and three-speed cutter transmission is said to maximise break-out forces and allow production rates of up to 47m/minute in optimum conditions. Maximum cutting depth is 508mm and the drum is 2.44m wide, while the machine is driven by four hydrostatic wheel motors, a layout that also offers high manoeuvrability. Direct shifting of the cutter transmission allows operators to select one of the three cutter speeds, which range from 128-209rpm. Contractors can choose between available 2,271litre/minute water only or water/emulsion additive systems for reclamation and stabilisation applications.
The RS series machines have been designed to meet the need of North American customers where there is strong demand for recycling equipment. But with BOMAG taking over this line-up the company may well opt to develop the RS models for sales in wider geographical markets. One potential development would be to offer its FLEXMIX system on the CMI units, although some machine modifications may be required first.
However BOMAG has also been developing its German-designed soil stabiliser range with the launch of the MPH600. This machine replaces the earlier MPH125 and is said to offer increased performance and productivity, along with accurate mixing capabilities. The machine can be equipped with the novel FLEXMIX system, which the company claims optimises mixing performance. The machine also features a new 447kW emissions compliant engine that is said to be highly fuel efficient. The sophisticated FLEXMIX system features a rotor that is infinitely adjustable and can adapt the machine to the requirements of a specific location, providing maximum output with efficient mixing and pulverising.
In addition a novel tooth replacement system has been developed for use on the MPH600. Called the BRS 05, this is also said to provide a more secure mounting while reducing changeover times for worn components. Featuring a permanent connection to the base bracket, this is made of wear-resistant steel to extend service life and reduce servicing requirements. The MPH600 is said to deliver optimum mix quality due to its fully automatic metering computer. This provides continuous monitoring of work and precise metering of water and bitumen additives. The computer records relevant data and this can be printed out for analysis. Other features include an ergonomic cab that offers high visibility, a new control steering system using twin joysticks and ease of transportation due to the height adjustable cab.
From
Highly versatile, the machine is said to be easy to operate with a control station that can be slid 457mm over the right side of the chassis so as to maximise visibility, while the seat and console can be swivelled 90° and for safety the machine is equipped with a reversing camera. Featuring four-wheel-drive and four steering modes for gradeability and manoeuvrability, the machine also has hydraulic suspension control allowing depth of cut to be controlled accurately. Cutting depths of 508mm can be achieved across a width of 254mm, although other cutter drum dimensions are available. The drum is belt-driven and features four speed options, with an air-shifter allowing rpm changes during operation without requiring the machine to be stopped to reset ratios. Serviceability is said to be good and the engine cover is raised hydraulically by 90° allowing access for maintenance. An option available for the SX-4e is an automated water/emulsion system with a capacity of 1,890litre/min. This system has fully automatic controls that moderate flow depending on factors such as cut depth and machine speed and this allows the SX-4e to be used in a much wider array of road recycling applications.
Sharing the performance features is the SX-4ex version of the new stabiliser. This has been developed for markets outside of the EC and North America where there is no need to meet such tight standards on exhaust emissions. The only difference is with the engine however and the SX-4ex variant is able to operate without need for the high quality fuels. The larger SX-6e and SX-6ex and SX-8e and SX-8ex will be available shortly and will share features with the SX-4e and SX-4ex.
From the start of 2014 the firm will also commence launching its Tier 4 Final models, although much of the work on these has already been done for the Tier 4 Interim introductions. Changes to the machines will focus on the new engines and associated after-treatment systems, although the design work necessary has already been carried out and there will be little in the way of external changes.
Meanwhile Roadtec’s latest addition to its milling machine range is the diminutive RX-100e, a compact and manoeuvrable unit aimed at duties in the road repair market. The drum is driven hydraulically by the machine’s 103kW Cummins diesel and the machine can cut a slot 508mm wide and 203mm deep. The small turning circle allows the machine to be steered around access covers in the roadway as well as kerbs and it suits duties on tight sites and for utilities works. Fuel economy is said to be good, helped in part by a cooling system that is demand led with a high efficiency, variable fan. To increase its versatility, the right rear leg tube can be moved from its standard position alongside the cutter housing to a location in front of the cutter housing as this allows the unit to be used in flush cut operations. Visibility is said to be good and the operator seat can be slid out to the right side if required.
The company originally focused on the heavy end of its milling machine line with the RX-900 and RX-700. The range has broadened over time and now includes the RX-600 and RX-400 (all the mills are available in e and ex variants) but further models are due to plug the gap.
Wirtgen is keen to retain its strong market position in the reclaimer stabiliser segment and its improved line-up will reinforce that presence. A new generation of stabilisers is now available from Wirtgen, with this revised line-up following on from the WR240 launched last year. The new WR200 and WR250 models share features with the WR240 and are said to set new standards in cold recycling and soil stabilisation.
The versatile WR240 suits heavy-duty stabilisation of large areas of non-cohesive soil, and for the cold recycling of old asphalt surfaces. This model brought new features to market and despite achieving higher productivity than its predecessor, tests in the field also show it to be more fuel-efficient due largely to its sophisticated engine management system. The machine has also been noted for its large high visibility cab and improved manoeuvrability, with these features all now being carried over into the more compact WR200 and the top-of-the-range WR250. The WR200 is the smallest of the range and is said to be even more manoeuvrable than the WR240, suiting duties on small sites while it offers increased mobility as it requires no special transport permits. In contrast the WR250 is a heavy-duty machine designed for stabilising heavy, swampy soils. In recycling and pulverisation jobs the WR250 can be used to turn roadways up to 250mm thick into homogenous granulate. An important new feature is the ability to control milling drum speed from the cab to suit it to different applications while the milling drum is designed to suit the machine’s high output. This combination of new drum and adjustable speed is said to allow the WR250 to provide high mix quality at a high feed rate.
The company is also keen to retain its dominant position in the milling machine market and is unveiling 11 improved models for its range. The new i variants feature intelligent emission control, benefiting from high efficiency, low exhaust emission technology. Several new features are also available for the milling machine range, such as a new levelling package and improved cutting technologies. The Rapid Slope is a new sensor package, which boosts the effectiveness of the firm’s Level Pro automatic levelling system. Fully integrated into the machine control system, the Level Pro automatic levelling package allows milling depth to be maintained accurately using sensors. The new Rapid Slope cross slope sensor provides fast and accurate recording of measurements and values are processed and forwarded to the machine control system. This allows Wirtgen milling machines to achieve high precision in cross slope profiles as well as considerably higher milling speeds with the same levelling quality. Used with the new telescoping levelling beam for scanning reference points up to 3.5m to the side of the machine, Rapid Slope offers optimum milling results even in challenging terrain.
Successive improvements to Wirtgen’s Flexible Cutter System (FCS) help widen the versatility of the firm’s milling machines. The proven FCS allows contractors to use a single machine for an array of duties, with drum changes taking from just 30 minutes to 1.5 hours (depending on the machine model). A simplified version of the system called FCS Light allows drums of the same width to be changed even more quickly.
Another improved feature is the new HT22 quick-change toolholder system, which offers increased service life for the upper part of the quick-change toolholder system and that of the milling drum. More robust, service intervals for checking the bolt pre-tension can be increased from 250 hours to 500 hours. Simple and reliable, this bolt connection system has been proven over a two-year-plus prototype phase.
And the Generation X point-attack cutting tools are said to deliver greater production at lower costs. These new point-attack cutting tools have been developed by Wirtgen in close cooperation with partner Betek. Increased wear resistance is offered for use at high milling output rates and the company claims the new point-attack cutting tools can be used for up to 20% longer under high milling output rates than conventional point-attack tools. A key feature is the innovative geometry of the carbide tips and optimised guidance in the toolholder system which reduces longitudinal wear.
Recycling product development
Anyway Solutions claims that its new product offers a versatile alternative to conventional cement or lime for recycling applications. This ANSS product is said to combine the performance characteristics of cement and lime, without the negative effects of either. The firm says that the product is composed of a specific type of cement, lime, several pozzolans, reaction rate governing additives and an innovative polypropylene fibre, which is how it achieves its high performance.
The ANSS product is said to offer five main reaction processes, allowing an ionic exchange with clay particles, crystalline formation between soil particles and cementitious gel creation. It also allows a continuation of the cementitious gel phase over an extended period that provides physical stabilisation by the fibre net. According to the company, using ANSS helps reduce the time required to construct a road as well as the direct costs of construction and the maintenance costs over the lifespan of the road. It is also said to offer a positive environmental benefit. The ANSS product is said to have been used in an array of applications worldwide with considerable success.
Tough option
Component specialist
He said that this two part pad system allows the pad to bolt directly onto the track. Long life and durability are claimed, as well as ease of replacement. These pads are in the firm’s trademark blue colour scheme to differentiate them from Wirtgen’s own yellow pads.
The company has also increased its manufacturing capacity to cope with growing demand for its products. The company is also now able to deliver complete undercarriage packages to customers including chains, rollers and sprockets.