A Hanson quarry in Spain is now benefiting from the installation of lining plates in its crushing plant. The J Riera, Llinar del Valles Quarry in Catalonia is using WT6000 linings supplied by Sandvik in the plant's primary hopper. The material was chosen for this tough application as the quarry company wanted to reduce wear and tear on its equipment and cut noise from the site. The hopper is the main intake for feed material in the plant and the rock is blasted granite, with a high abrasive index and a maxi
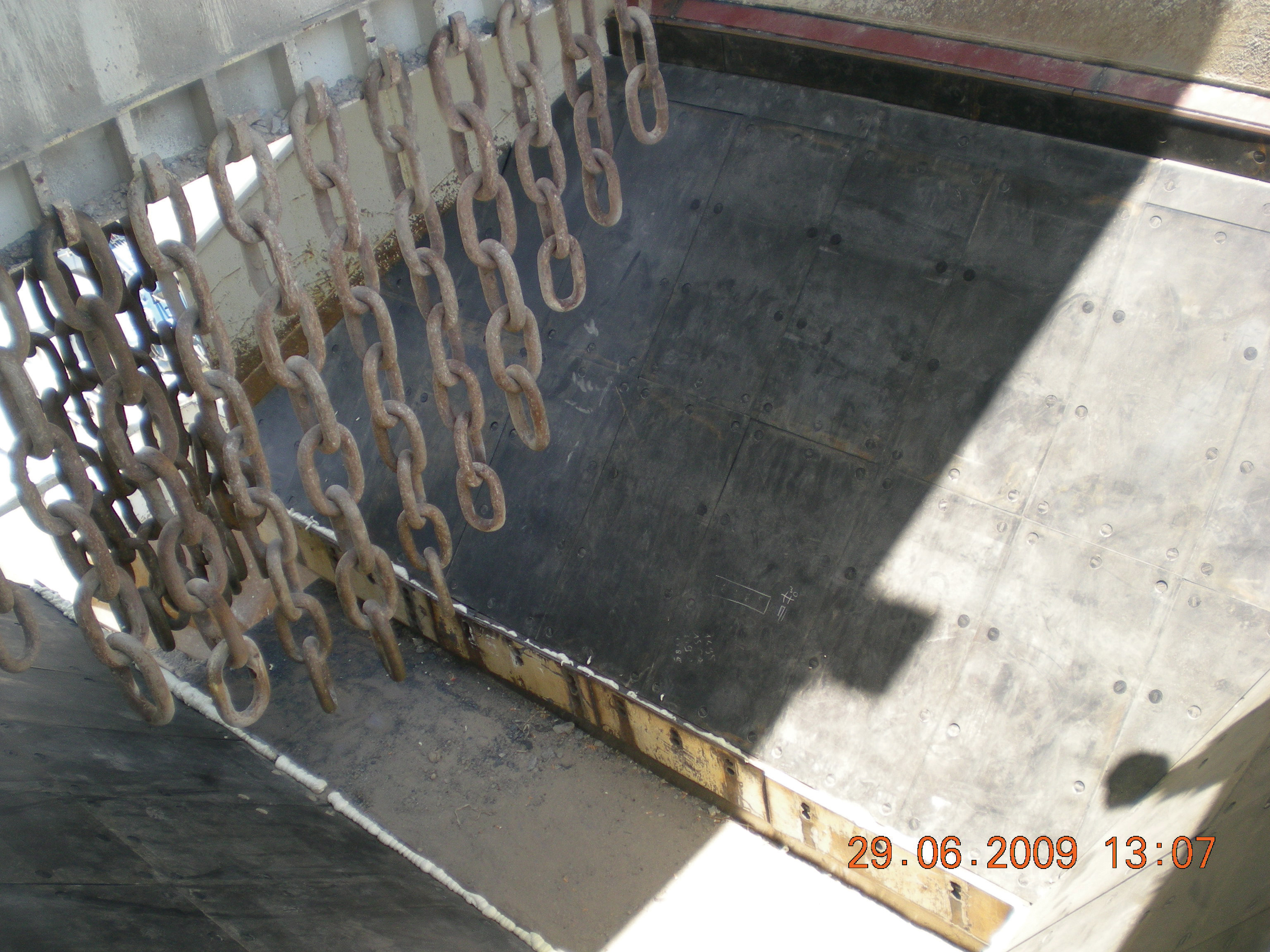
Rubber linings from Sandvik have reduced equipment wear and working noise
A Hanson quarry in Spain is now benefiting from the installation of lining plates in its crushing plant.
The J Riera, Llinar del Valles Quarry in Catalonia is using WT6000 linings supplied by Sandvik in the plant's primary hopper. The material was chosen for this tough application as the quarry company wanted to reduce wear and tear on its equipment and cut noise from the site.
The hopper is the main intake for feed material in the plant and the rock is blasted granite, with a high abrasive index and a maximum size of 2m. The blasted granite is directly discharged by a dump truck into the 90m3 hopper, with the hopper dimensions being 6,623 x 7,575 x 3,887mm.
325 Sandvik selected WT6000 as this suited the arduous application best and designed a layout with 60 shore rubber wear plates featuring full 5mm steel backing, and a total thickness of 125mm while stud welding was used to set up the facilities.
The use of WT6000 will extend equipment life by reducing vibration originating from impact forces on the hopper structure. Since the rubber is corrosion resistant, it offers greater wear life than steel linings. Other advantages include the noise emission reductions offered by the WT6000 lowers as well as the secure stud welding system which means there is no need to drill the hopper.
The lining process began with the set up of the stud weld, which followed the assembly pattern provided by the Sandvik design department. The next step was to install the WT6000 rubber plates, which had been cut and drilled previously following the same pattern. The drilled holes in the rubber plates were covered with a rubber plug to protect the fastening elements against wear and tear.
The J Riera, Llinar del Valles Quarry in Catalonia is using WT6000 linings supplied by Sandvik in the plant's primary hopper. The material was chosen for this tough application as the quarry company wanted to reduce wear and tear on its equipment and cut noise from the site.
The hopper is the main intake for feed material in the plant and the rock is blasted granite, with a high abrasive index and a maximum size of 2m. The blasted granite is directly discharged by a dump truck into the 90m3 hopper, with the hopper dimensions being 6,623 x 7,575 x 3,887mm.
The use of WT6000 will extend equipment life by reducing vibration originating from impact forces on the hopper structure. Since the rubber is corrosion resistant, it offers greater wear life than steel linings. Other advantages include the noise emission reductions offered by the WT6000 lowers as well as the secure stud welding system which means there is no need to drill the hopper.
The lining process began with the set up of the stud weld, which followed the assembly pattern provided by the Sandvik design department. The next step was to install the WT6000 rubber plates, which had been cut and drilled previously following the same pattern. The drilled holes in the rubber plates were covered with a rubber plug to protect the fastening elements against wear and tear.