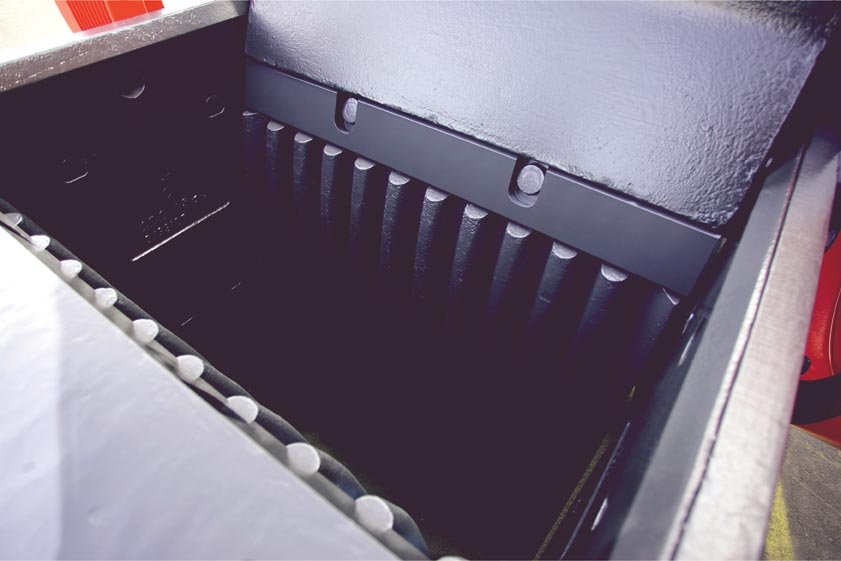
New technology broadens Sandvik's offering for crushing and screening. Mike Woof reports
At the more versatile end of the range is the new CJ208 jaw crusher, the latest addition to the CJ200 series jaw crusher line-up. This crusher is the smallest of the CJ200 Series and offers the performance benefits of heavy-duty equipment in a comparatively compact package, according to the firm. Versatile and productive, the CJ208 is said to be cost efficient as well as compact and robust with high performance.
The unit has an optimised crushing chamber that allows a high reduction ratio and capacity and is able to produce a 0-40mm final product in a single crushing stage. Low running costs and downtime are claimed as the CJ208 is easy to maintain and features a rugged all-welded frame with high durability against shock loads.
Its deep and symmetrical crushing chamber allows a large feed size and capacity while improving reduction capabilities and the unit can be used in both stationary and mobile applications. Its heavy-duty capacity suits it for use in stationary applications while its low-weight means it can also be used in mobile applications. Because the CJ208 has bolted feet it can be used as a stationary unit with 0º inclination or on a mobile unit with 5º inclination.
As with the rest of the CJ200 Series, the CJ208 is offered with an array of options such as automatic bearing lubrication, feed hopper, intermediate protection plate and a drive package, including motor, bracket, pulley, belt and flywheel/belt protection. Low energy and operating are claimed and the CJ208 model only requires a 55kW motor to crush the hardest material with the smallest feed openings.
Developed for high production in-pit crushing and conveying (IPCC), Sandivk's new PF300 can be specified with a sizer, double-roll crusher or hybrid-crusher to suit a range of applications. An integrated IPCC system can be delivered that will meet the customer's needs, according to Sandvik and the system is said to be both compact in design and feature a low weight for high mobility. Stability is also claimed for ease of loading and this helps maximise availability and improves positioning. The PF300 can either work in combination with a belt wagon, mobile transfer conveyors, or load bridges as the connecting downstream link to the face conveyor.
Improved material flow and productivity is claimed with Sandvik's new crusher mantle design. The Sandvik Flexifeed FF mantle features a patented design with a variable intake in the upper section and although the feed opening is narrower at some points in the intake, capacity is maintained. By extending the mantle Sandvik has ensured that more crushing takes place in the upper section of the chamber. This improves utilisation and spreads the wear more evenly throughout, extending the time between service intervals.
The mantle and pockets rotate during crushing, allowing large material through the chamber. According to the firm, on-site testing has shown that the lifetime of liners can be extended by 20-50%, depending on the application, while the reduction ratio is increased by around 5%. Production levels are maintained throughout the mantle's lifetime and material gradation capabilities are maintained. At present, the Flexifeed mantle is only available for the Sandvik CH440 cone crusher in combination with EC, C and MC concaves.
Sandvik's improved range of rubber linings can extend vehicle life, reduce noise and improve operator comfort according to the firm. The linings extend the life of a truck body or feed
bin by preventing much of the abrasive and cutting wear that occurs during loading and unloading, due to impacts or material sliding across a surface.
For such applications Sandvik says its durable WT6000 rubber linings help extend wear life by absorbing energy released on impact. The linings are elastic and return to their initial shape after impact while protecting the steel structure underneath. Apart from reducing noise and extending overall service life of truck bodies and hoppers, these linings minimise the risk of buckles and cracks. During cold weather the linings can reduce risk of fines freezing to the steel sides of a hopper or truck body, boosting productivity and throughput. Because of the reduced maintenance needs, the linings also cut downtime and reduce the need for structural repairs, while helping lower the cost/tonne.
The firm can offer solutions tailored to meet specific applications, complete with rubber elements, bolts and plugs. The linings can be mounted using stud welds or through-bolts for rapid, secure installation while Sandvik can also remove old linings and assemblies.
Clean screening
Increased production capacity and material quality are claimed for the new screening media from Canadian firm Major Wire Industries. The firm's Flex-Mat 3 self-cleaning screen media helps boost throughput and end-product quality while reducing downtime, according to the firm. Wires that resonate independently are said to boost product throughput by up to 40% over conventional woven wire or polyurethane panels by eliminating blinding, pegging and clogging. In addition, this new design is said to offer 30% more open area than woven wire for up to 30% more material throughput. This can boost screening efficiency and deliver material to grade at lower cost than rival systems.
Producers can deliver higher quantities of on-grade product as there is less downtime needed for cleaning or replacing screens. The Flex-Mat 3 products feature lime green polyurethane strips that align to the crown bars in each screen box and hold individual wires in place as they run from hook to hook. The wires vibrate independently to better separate material, minimising blinding, pegging or clogging. Wire configurations include a diamond-shaped Flex-Mat D for standard applications; wave-patterned Flex-Mat S for fines removal; and triangular Flex-Mat T for heavy scalping or fine screening.
Rebuilding and revamping
Indianapolis-based
The company buys used cone crushers and says it rebuilds these units from the ground up, including the chassis on portable units in a special area of its facility. Cone crushers are taken apart, evaluated, remanufactured and then sold to contractors or producers worldwide for around 50% of the cost of a new cone crusher. Any part that is out of specification is replaced including: liners, main frames, bushings, gears, hoppers/bowls, heads, shafts, bearings, seals, housing, springs, motors, pumps, alarms and all other wear parts.
The remanufactured stationary and portable cone crushers are available in size ranges from 0.6-2.1m and these include units configured to crush materials ranging in hardness. The company also says that it can customise cone crushers to suit most operations with production requirements up to 1,500tonnes/hour. The firm offers installation, startup, parts and wear components as well as servicing and can provide six-month or extended warranties if required.