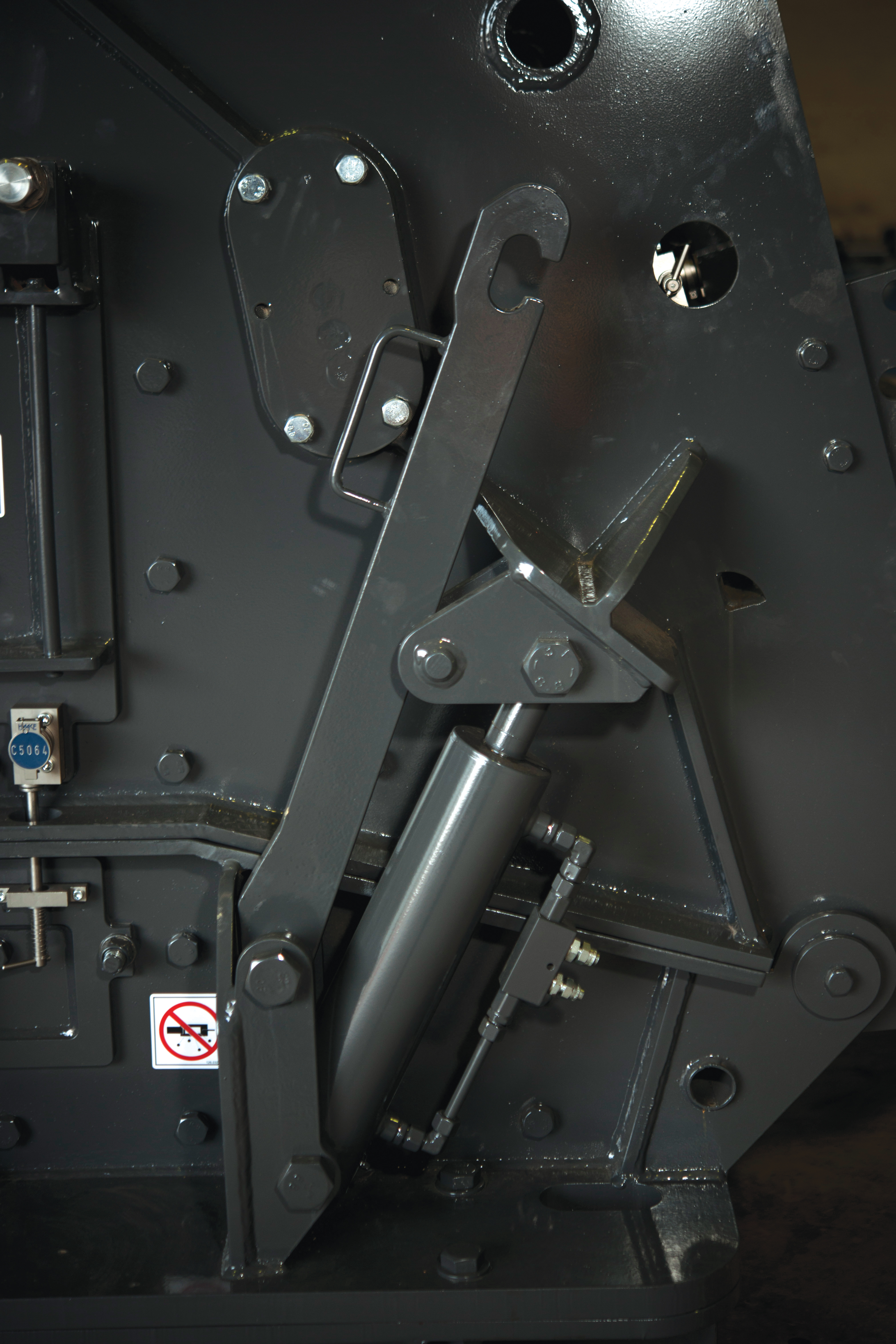
Novel crushing and screening developments are coming to market - Mike Woof reports
A wide array of innovations and market developments are occurring in the sector for quarrying machinery. New technologies are being introduced while business developments are also changing the face of this market segment.There is strong interest in new technology from industry too and this was well highlighted by data from the organisers of the
Several major manufacturers exhibited new crushing and screening technology at the show and several other firms not present at the event have also introduced new systems.
From
The C106 jaw crusher is said to be robust and reliable and now features a new, analogue materials sensor for continuous choked feed and an active setting Control (ASC) for the safe crushing of recycled materials. The C106 has a large feed opening of 1,060x700mm and is said to feature an aggressive cavity cross section, which allows a high reduction ratio. The LT106 offers quick relocation and setup time with a patented turning side conveyor that can be transported with the unit, and hopper walls that can be tilted and opened safely hydraulically. For transport it measures 14.2m long by 2.8m wide and 3.4m high while weighing 40tonnes. For use in urban areas, the LT106 can also be equipped with optional features to minimise dust and noise emissions.
This is the second generation of compact horizontal impact crushers from Sandvik and the firm claims the line offers low capital cost, optimum performance and good cubical shape.
Dallimore explained, “HSI crushers have been around for a long time but this has many new features. It can be adjusted to take a primary feed of 600mm or a secondary 300mm feed. We have full hydraulic adjustment and it is infinitely adjustable.”
The firm has taken out five patents covering the new crushers, which are said to offer low cost/tonne performance as well as the ability to handle an array of materials. The base crusher unit can be mounted on a tracked machine allowing it to be used in mobile primary or secondary configurations, while it can also be used in stationary form for primary or secondary applications. He said, “With one crusher we’re meeting four needs.”
Changing the crusher between primary and secondary configurations is said to be comparatively straightforward and involves moving the feed entrance. For primary applications the entrance is in the side and for secondary use it is on the top, while a removable cover plate can be switched from one to the other as required. The crusher can also be set with a dual feed configuration with the primary side open and oversized material being fed back from the screen and into the top.
The Ci511 primary crusher can deliver 160tonnes/hour throughput and features an 800/980mm feed opening and has a maximum feed size of 600mm. The Ci512 primary crusher features a maximum throughput of 150tonnes/hour with a 400x980mm feed opening and handles a maximum feed size of 300mm.
The innovative design extends to the chamber layout, which is said to deliver better reduction ratios than previous units. The high mass open design rotor is said to ensure stable power consumption and the ability to cope with reinforcing bar in recycling applications.
The infinite hydraulic curtain adjustment is combined with a brake positioning system that relieves pressure and setting when un-crushable objects enter the crusher. In addition, should a large rock wedge in the inlet, the system can move back hydraulically to clear the machine. Safety interlocks are fitted throughout to reduce risks to operators. For example the crusher cannot be opened until the rotor has stopped turning. Oversized bearings and heavy-duty wearparts are said to extend working life and the stationary version comes with a large feed hopper. In stationary configuration the crusher is said to suit use with feed materials such as limestone while in mobile form it can be used for recycling concrete and asphalt. The wear parts can be turned to increase life and the same size of components is used across the whole range of crushers. In addition, the design of the hammer and the materials used in its construction ensure maximum breakage, even as hammers wear.
Dirk Vander Elst is business line manager for wear protection and screening media in the firm’s EMEA region and he said, “We’ve developed a new screen media system.”
The company believes that this system will build sales in the competitive market and the patent-pending WR modular screening media has been developed for use on screens with longitudinal profiles. The system is said to allow aggregate producers to boost production capacity, while delivering efficient screening. The company claims it is easy to install, with no requirement for any screen modification and this helps reduce downtime.
The WR screening media comes with an anti-blinding system allowing the screening of difficult materials at high throughput rates. Cross-mounted flexible screen panels are used that deliver a wave-like effect, which improves stratification and allows undersize material to find a more rapid path to the screening surface according to the firm. Lightweight glass fibre cross members are used.
The fibre reinforced rubber screen membrane allows the use of thinner panels with closer aperture spacing, increasing open screening area by 7-8%. By raising the screen panels from the longitudinal support bars, the screen panels can be fully perforated from side liner to side liner. This ensures maximum material separation, and minimises the amount of undersized particles carried over to the end product.
Vander Elst explained that the material has more time to pass through the screen, while the layout also eliminates blind spots. He added, “There’s no steel inside so the rubber is easier to recycle.”
A wedge fastening system is used and he added, “…also, the adaptor system is reinforced by a glass fibre insert. It is patented and it is revolutionary. We can run with a low stroke compared with our competitors.”
Because the screen products can operate with a stroke of just 4.5mm instead of the 7mm or so required by conventional designs, the inertial forces within the machine are reduced and this helps boost the working life of components.
Haver & Boecker has established Haver & Tyler as its world-wide processing technology alliance. This operation is now a screening and washing technology solutions provider for the worldwide aggregate industry. The alliance comprises Haver & Boecker Latinoamericana in Brazil, Haver Niagara in Germany and
Meanwhile W.S. Tyler says that its Pro-Deck System can help to maximise screening efficiency by allowing users to select the most suitable type of screen media for the application.
This can deliver an optimised screening process for greater efficiency and productivity, as well as reducing the risk of unscheduled maintenance and boosting screen life. The Pro-Deck is said to combine screening expertise with an analytical approach that can determine the most suitable screen media for each operation. The firm’s research suggests that incorporating more than one screen media can improve efficiency and reduce unscheduled maintenance. The company also claims its system helps to eliminate common screening problems such as blinding, pegging and premature wear.
Material traveling over a screen undergoes three different phases, which W.S. Tyler refers to as the layered, basic and sharp screening stages. As each phase of the screening functions differently, customising screen media can take into account the relevant open area and wear life factors and help tailor the screen media to each phase.
This system is also said to evaluate material characteristics, the way the plant is functioning and final output to provide an effective blend of screen media. Adjustments to the screen media are made one section at a time and the results are monitored to ensure output quality and productivity. Analysing material characteristics, the screen media can be adapted to accommodate wet, dry or even abrasive materials.
The first stage is to use the firm’s own vibration analysis tool onsite as this helps determine whether the screen is working within the operational parameters of the application and material. By analysing screen performance and wear on the section and deck, recommendations for any necessary screen media modifications can be made. Once the new media is installed the results can be measured and monitored and the next sections can be tackled until all the necessary changes have been made. This systematic approach can be used with any vibrating screen unit in virtually any application according to the firm.
And the firm is also offering its novel Ty-Wire Screen Media range, which is said to combine the durability and longevity of polyurethane with the greater open area and cost-effective characteristics of woven wire cloth. This is said to offer a highly efficient screening alternative to conventional screen media. The product features a design that delivers up to 80% more open area than modular polyurethane. This minimises blinding and virtually eliminates pegging, according to the firm. Ty-Wire is said to increase screening efficiency and uptime, as well as reducing maintenance costs and increasing product life.
Because materials and applications vary from one operation to another, 100% polyurethane or woven wire screen media may not be the ideal fit for all duties. Polyurethane is resilient and has low-maintenance needs, but can be expensive and heavy, while woven wire is productive and low cost but may not deliver the longevity required. Ty-Wire combines polyurethane and woven wire into an affordable and durable product that helps boost screening efficiency and productivity. The product features high-carbon woven wire encased in an engineered polyurethane grid and can withstand high temperatures and high tonnages, while offering a wear life of up to six times longer than wire cloth.
The product offers a tapered opening design that is said to releases more near-sized material, allowing it to perform as a self-cleaning screen. The top of each opening is narrower than the bottom, preventing plugging. This boosts uptime and profits while eliminating inefficiencies and unnecessary downtime for cleaning of screen media.
The firm says that Ty-Wire is compatible with any vibrating screen and requires no deck conversion before installation. The screens are available with clear openings, ranging from 3.2-38mm, thickness from 8-16mm, and open area from 23.5-56.2%.
Crushing performance from CEMCO
With the ability to process materials up to 152.4mm in diameter, the Turbo 128 V-Twin VSI Crusher is among the largest models in