Efficient crushing and screening processes help produce quality products, Mike Woof reports. Having an efficient crushing and screening operation is crucial to the cost-effectiveness of a quarry as well as providing the best quality product. The crushing circuit is a key component in any quarry with the right selection of equipment as well as effective maintenance important factors in optimising performance.
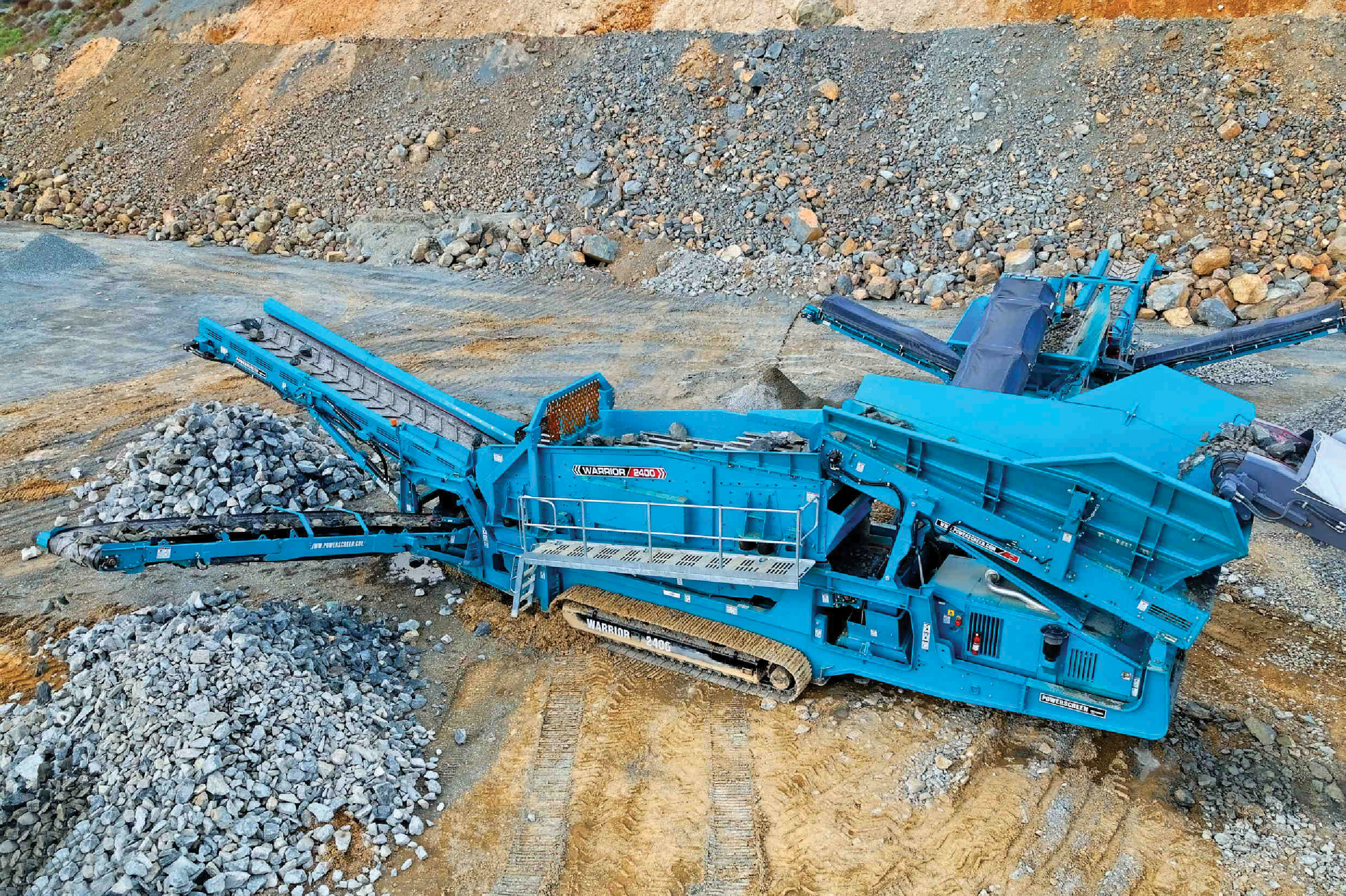
Powerscreen's Warrior 2400 screening plant shares many features with the existing smaller units in the line-up while offering greater throughput capabilities
Efficient crushing and screening processes help produce quality products, Mike Woof reports
Having an efficient crushing and screening operation is crucial to the cost-effectiveness of a quarry as well as providing the best quality product. The crushing circuit is a key component in any quarry with the right selection of equipment as well as effective maintenance important factors in optimising performance. Manufacturers are unveiling innovative solutions to boosting the efficiency of crushing and screening circuits.Sorting the feedstock before it enters the crushing cycle can make major gains in efficiency. This reduces the energy spent in processing undersized fines or contaminants and significantly boost throughput while also reducing unnecessary wear and tear on the crushing and screening plant and maximising finished product quality.
Placed at the start of the reduction cycle, this type of equipment can make major gains in output while cutting running costs and
Customers have a wide array of equipment for the crushing and screening process to choose from, including static and mobile plants. Different types of crushers are also offered to suit specific applications as well as the primary, secondary and tertiary stages in the crushing cycle.
Jaw crushers are typically used in the primary stage and US firm
A key feature of the H2550 is the hydraulic toggle system which features a heavy-duty hydraulic cylinder, custom-engineered for crushing applications. Innovative hydraulic adjustment, relief and clearing systems minimise downtime and prevent component damage, according to the firm. The crusher is said to be ideally suited for the portable contractor and is a low-profile unit while its fast hydraulic adjustment allows operators to cope with different applications and materials. The hydraulic overload relief system prevents crusher damage, downtime and difficult maintenance procedures by opening the crusher and allowing tramp metal and non-crushable materials to pass through, preventing damage, while the system will then automatically return the crusher to its previous setting. The unit offers a 635mm x 1,270mm feed opening and, depending on the conditions is capable of crushing between 145-440tonnes/hour.
Italian crushing specialist
Depending on the material being crushed and the size setting, the GCR100 can produce from 150-300tonnes/hour. The jaws feature hydraulic adjustment and open automatically in the event of tramp metal entering the system. Features include magnetic separation a water spray system to minimise dust emissions, a remote control and a side conveyor as well as a full range of other options. The hydraulics feature load sensing pumps to maximise efficiency and reduce fuel consumption.
Impact crushers suit particular applications and this is a competitive market with various manufacturers offering high performance equipment.
The new SHB series impact crusher has a hydraulically actuated crusher inlet in with a heavy-duty cast design and an optimised, steeper inlet angle to the new blow bar fastening system. The machines also feature a fully hydraulic crushing gap adjustment that can be operated easily and in mere seconds from the operating panel. The crusher bypass has also been redesigned to ensure an optimised flow of material, which is pre-screened and continually moved past the crusher.
According to Kleemann, the improved flow not only increases production rates but also helps to reduce wear. Both machines are powered by direct drives, which Kleemann says improve efficiency along with a loss-free fluid coupling and v-belts connected directly to the flywheel of the crusher. The direct drive means that the rotor speed can be adjusted in four stages, making it suitable for both quarry and recycling applications.
Meanwhile
Although developed for the recycling of construction material, the QI240 is ideal for smaller quarries where space and machine manoeuvrability are at a premium, and superb product shape and high levels of production are essential.
The machine is fitted with a pre-screen to ensure maximum scalping capability to prevent any undersize material passing through the impactor to maximise throughput and reduce wear costs. This also allows a specified sized product to be produced from the natural fines conveyor.
Designed for large fixed plant installations, the new Superior 60-2110E gyratory crusher and the Nordberg MP1250 cone crusher from
Metso's new MP1250 uses the same footprint as the MP1000 but offers greater productivity, with improvements in the mantle locknut to make maintenance quicker and easier. There are also upgrades in the hydraulic tramp protection system, bowl adjustment and removal, and faster. Firms running the MP1000 cone crusher can upgrade their plant using Metso's MP1250 retrofit kit, which includes a new sleeved, high-throw eccentric; large counterweight with bolt-on guard; upper head bushing; head ball; and socket liner. The design also includes an upgraded mainshaft assembly with a patented bearing ring that releases the pressure of the headnut for mantle change-out. This eliminates the risk of damage to the headnut or mantle and allows simple replacement.
Meanwhile a cost effective option to buying a new crushing plant is offered by US firm
Screening the crushed aggregates efficiently provides another key factor in cost-effective production and
Northern Irish firm
Italian company
"The HCS (hydraulic crushing system) continuously checks and adjusts the different parts of the machine, and this means maximum performance in terms of low fuel consumption, low crushing chambers wear, and high production, which means low running costs," says Gasparin Impianti. The 42tonne machine has an output of up to 360tonnes/hour and is powered by a
It has a vibrating grizzly feeder with replaceable double step bars grid; the main belt conveyor's discharge height is 3.2m, and the hydraulic folding hopper is fitted with a with wedge-lock system.