The crushing and screening phase is a crucial component in aggregate production and new development will help optimise performance - Mike Woof reports Crushing and screening is a key part of the quarrying cycle and has a huge impact on overall operating performance. Optimising operations will cut running costs, reduce materials wastage and also provide a more consistent product quality, boosting cost-effectiveness dramatically. An array of innovations were revealed to the market at the recent INTERMAT 2012
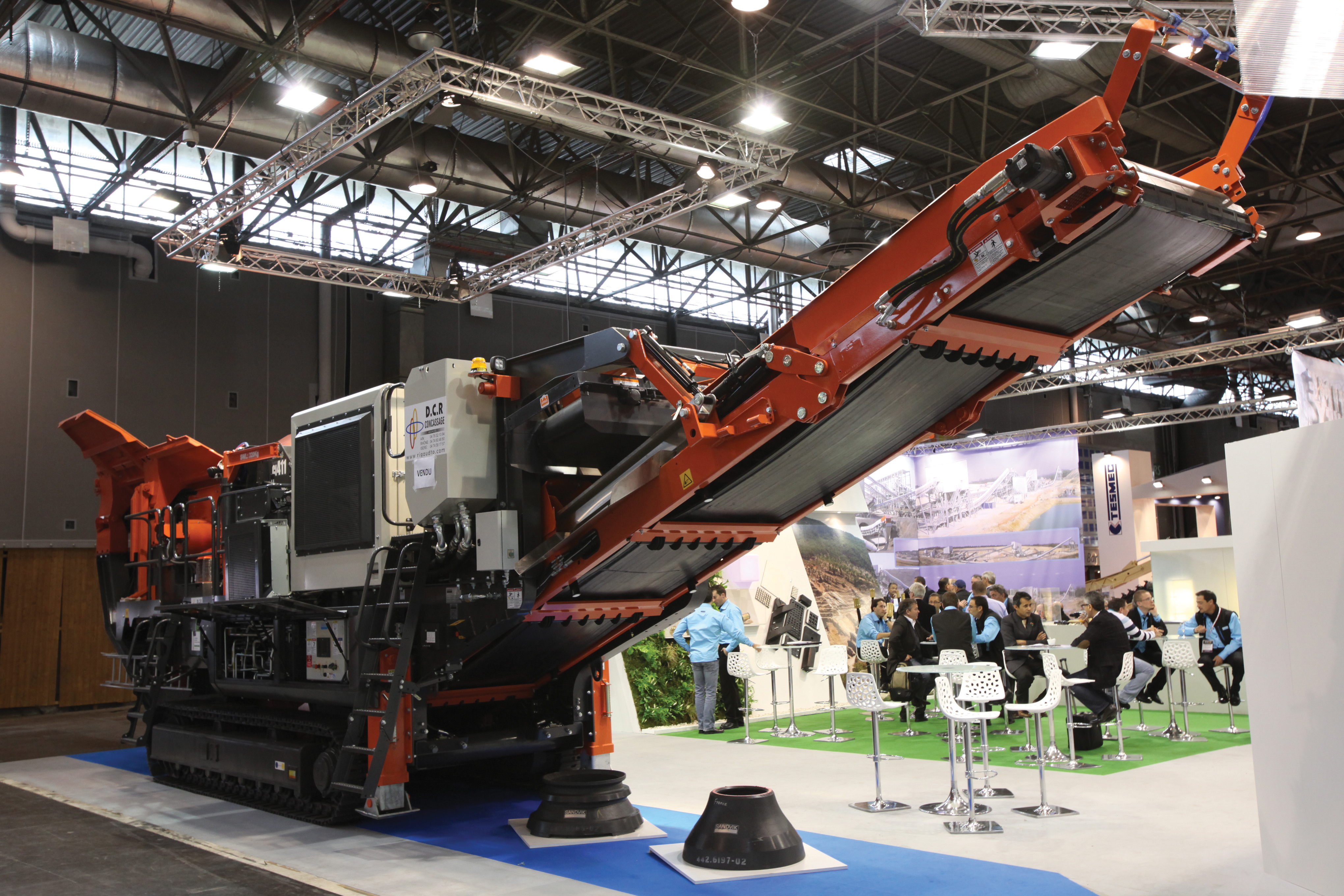
Sandvik’s versatile QI 240 can be used in both primary and secondary impact crushing duties
The crushing and screening phase is a crucial component in aggregate production and new development will help optimise performance - Mike Woof reports
Crushing and screening is a key part of the quarrying cycle and has a huge impact on overall operating performance.Optimising operations will cut running costs, reduce materials wastage and also provide a more consistent product quality, boosting cost-effectiveness dramatically. An array of innovations were revealed to the market at the recent
New machine developments now coming to market stand to increase working efficiency, with an array of new technologies becoming available. One notable development in recent years has been for mobile equipment, with these more versatile plants offering far greater throughput than in the past, as well as longer service intervals and lower downtime due to improved design and the use of the latest materials technology.
Control systems have become more sophisticated for the mobile machines, allowing much higher production capabilities while also delivering high operating efficiency.
Feeding materials
Ensuring a steady flow of materials into a crushing circuit can help optimise throughput, boosting operating efficiency and productivity, while also reducing wear and tear caused by discontinuous working. New mobile equipment is coming to market for this segment, which will help mobile plants achieve far higher performance.From
Versatility is claimed also as the machine can be fitted with a grid and a screen for use as a scalping/screening unit.
The Edge-Loader TL220 features a conventional belt design and large, wide track-mounted receiving hopper to all it to be filled by a large wheeled loader filling. It is also offered with a discharge conveyor featuring 180° radial swing that moves hydraulically and allows the operator to feed the output in the direction required without stopping production.
The firm says that key advantages of the TL220 are fast set-up time on site and ease of transportation, while it can handle an array of different materials and can be used in a huge variety of applications.
The new design offers customers the option to radial the track conveyor without stopping production or repositioning the conveyor from its in-line arrangement after the crusher or screener. This radial automatic function enables operations to automatically process and build a stockpile of up to 15,122tonnes (9,452m3).
Jaw jaw
Jaw crushers are typically used in primary application and can cope with tough materials, suiting them to a wide array of duties.The
In addition, the MC 100 R has sufficient power reserves to operate the crusher when the crushing jaw is full. The reversible drive enables blockages in the mouth to be removed quickly and easily. The powerful 228kW diesel engine ensures maximum feed capacity of up to 200tonnes per hour, claims Kleemann.
Italian crusher manufacturer
Impacting design
Advances seem to be particularly strong in the market for impact crushers, with a very wide array of new machines being introduced.German manufacturer
Kleemann's MR 110 ZS mobile impact crusher is from the new Mobirex EVO series. The firm’s new EVO plants are said to offer more in diverse customer applications. The new material flow concept, which enlarges the system widths in the direction of the material flow, ensures enhanced performance, less wear and optimum values in terms of consumption/tonne of broken material.
The MR 110 ZS EVO features the stand-alone double-deck grizzly along with high-performance electromagnets while the screening unit includes oversize grain return conveyor whose screen surface is 40% larger than its predecessor model.
Kleemann says that huge importance was attached to flexibility in the development of the EVO series, and this started with the new feeding unit with a fully automatic hopper locking mechanism. This was followed by the new touch panel control system with status displays in clear text format, and then the completely redeveloped crusher. The in-feed geometry has been redefined for better penetration of the material in the impact range of the rotor. The new C-Shape rotor ledges are said to remain sharp for longer due to their C-shape and are characterised by a clamping system which makes change-overs much easier.
A key feature is the fully hydraulic and automatic gap setting, which allows the crusher gap to be adjusted to the exact millimetre using the touch panel when the rotor is running. All this not only increases the quality of the final grain, but also the availability of the plant. The new, overload protection system also boosts availability.
Meanwhile
This removes the need for a secondary crusher or screen, saving money for the operator and cutting the number of machines on site.
Powerscreen’s XH500 horizontal shaft impact crusher is said to represent the latest generation of highly versatile track mobile crusher, designed for processing large volumes of soft to medium-hard primary and secondary materials such as natural rock and construction derived materials including asphalt, recycling and demolition waste. It has been designed for high reduction and maximum throughput of up to 500tonnes/hour.
The firm says that the machine is ideally suited to contract crushing due to its high productivity and ease of set-up, operation and maintenance. Key features include vibrating pan feeder, double deck live pre-screen, feeder load management system, under pan feeder, efficient crusher direct-drive system, crusher hydraulic overload protection, hydraulic raise and lower product conveyor for rebar removal, new PLC control system and class leading stockpiling capacities.
Rockster Recycler has developed its smallest and most compact mobile crusher to date, the R700S impact crusher. Weighing in at 22tonnes when equipped with a screen box, or 19.3tonnes without, the crusher can be transported as a single unit by truck. The machine is powered by a 129kW FPT engine, driving a 930mm rotor while it has an inlet opening of 710mm by 650mm.
Production capacity is 150tonnes/hour and it measures 9m long by 2.41m wide and 3.1m high, allowing it to be transported easily from one site to another.
Sandvik Construction is introducing its new QI240 mobile impact crusher. According to the firm the QI240 is a fully mobile, compact impact crusher and features a patented design that allows it to work in primary or secondary roles. The machine is said to produce high quality materials due to its Sandvik PriSec impactor. The company claims that this is the most versatile impactor currently available on the market and is designed to meet high quality end product specifications. Two hydraulically adjustable apron curtains can be positioned to allow the machine to be used as a primary impactor. These can be repositioned to allow the machine to operate as a secondary impactor to produce smaller end products.
The QI 240 is fitted with a pre-screen as standard to maximise scalping capability and throughput, while reducing wear costs. In addition, an underpan feeder is fitted as standard for maximum belt protection. The machine offers variable tip speed from 30-37m/s and is said to be designed for optimum fuel economy and low operating costs. It also has a hydraulically adjustable main conveyor for relieving wire blockages in recycle applications. Maximum feed size for the CI411 impactor fitted is 500mm while the machine can produce up to 500tonnes/hour.
Operating weight varies from 39.4-43.4tonnes depending on specification while it measures 14.65m long by 5.65m wide and 4.13m high. Folded down for transport it is 14.16m long by 2.5m wide and 3.4m high.
Cream of the cones
McCloskey says it is now offer a recirculating screen box on its C38 cone crusher. This new model is called the C38R and is said to offer the same high throughput and reliability of the existing C38, along with greater efficiency.Additional features include hydraulically adjustable closed side setting, easy manganese changes, and a weather protected control panel with user-friendly controls.
According to the firm set up time and ease of operation is aided by the simplicity of the Modular Product range. It is designed to fit and work together interchangeably. The modular product line bolts together on site with little onsite wiring. Designed with logistics in mind, each module, including all its components, can be transported in one container.
Terex MPS says the cone model has a capacity of 125-220tonnes/hour (70-125tonnes/hour for sand) and the basic crusher weighs 10,000kg. The sand version has a 160kW motor while for other uses it is 185kw.
Screening advances
Finally, screening material efficiently is a key issue to ensure product quality and new machines can offer economies of scale as a well as adaptability.The Warrior 2400 is the largest machine in
The new
The aggressive forward-facing inclined modular configuration screenbox has a 2,755mm x 1,200mm top deck and a 2,755mm x 1,200mm bottom deck. Depending on the working application of the machine, the screen box angle can be adjusted hydraulically.
The top deck of screenbox can be fitted with a variety of screening media including; tines, bofor bars, punched plate and mesh.
The bottom deck can be fitted with mesh or cascade fingers. A high performance 1,000mm four-ply belt feeder, with hydraulic gearbox drive, is fitted to the machine as standard and has proven performance and versatility in demanding and varied working environments. The hopper has a 5m³ capacity as standard. The machine is equipped with three hydraulically folding discharge conveyors allowing for maximum stockpiling capacity and associated benefits of rapid set up and tear down times.
A
Terex Finlay says that its new 684 inclined screen can also be used in an array of applications. Fully self-contained, this plant can be hydraulically folded and ready for transport in less than 30 minutes, suiting it to contract screening. The new screenbox on the Finlay 684 features three full size 4.3m x 1.7m inclined decks giving a large screening area of 21.9m2. This layout provides efficient screening and high capacity, as well as quick wedge tensioning, access holes and bottom deck hydraulic tensioning system to reduce the time required for mesh changes. The fourth product oversize plus conveyor can work at varying angles to discharge material for recirculation and stockpiling.
A 1,050mm belt feeder, with hydraulic gearbox drive, is fitted to the machine as standard, and the hopper has an 8m³ capacity as standard and can be fitted with a 4.26m tipping grid or 3.65m vibrating grid. A Caterpillar C4 82kW engine is used to power the machine. The machine also features heavy duty crawler tracks, and an optional radio remote control unit.