In the drilling and hydraulic attachment sectors too, firms are offering novel solutions for the customer. Atlas Copco continues to develop its comprehensive range of drilling solutions in the shape of its latest down-the-hole (DTH) and SmartRig variants, as well as adding new compact rigs and new consumables to the line-up. The firm's latest Roc L630 DTH rig benefits from a new feed as well as improved cooling. The new aluminium feed is said to improve hole straightness and hole quality. It also allows the
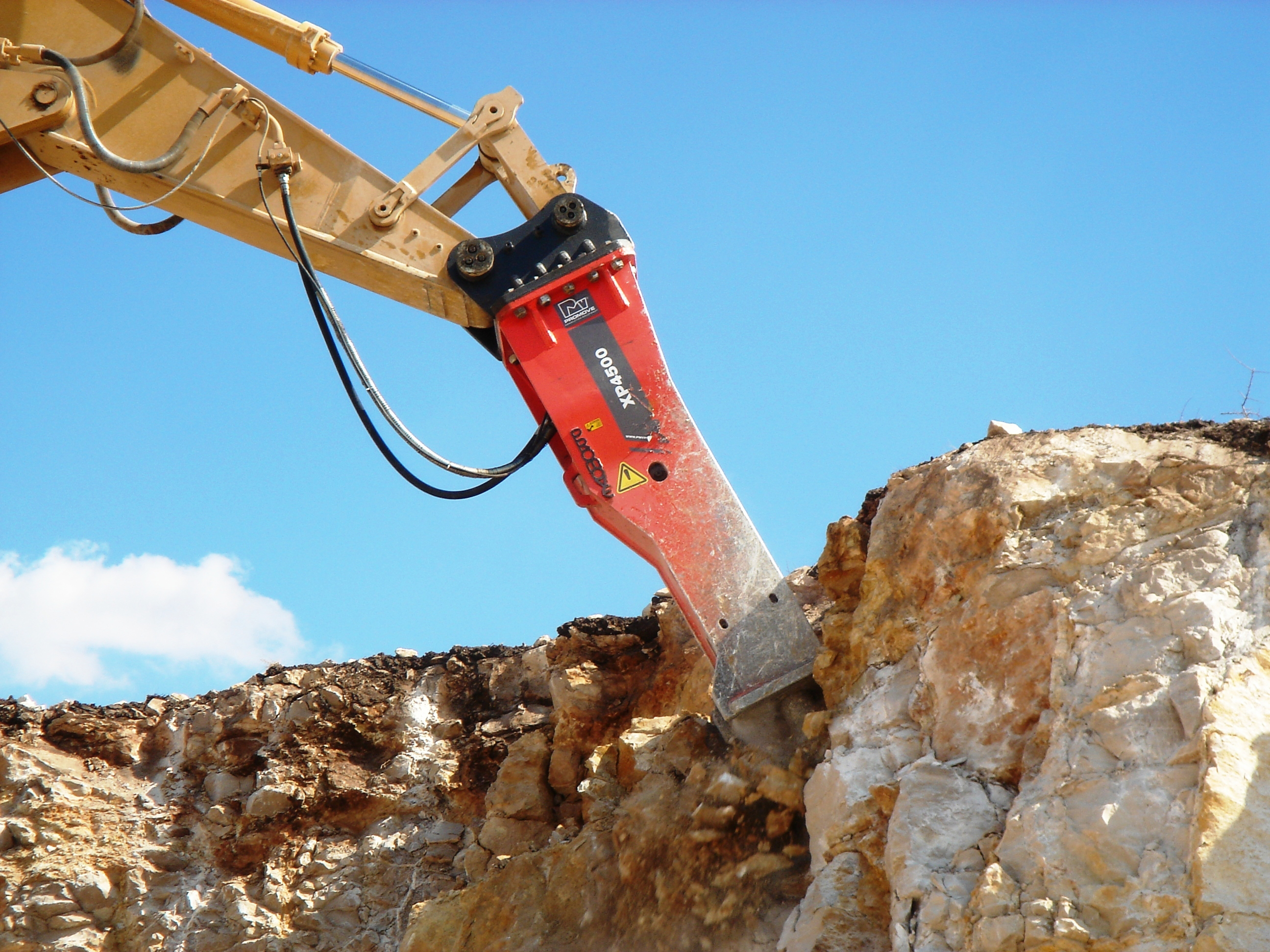
Promove has an extensive range of breakers as well as other attachments
In the drilling and hydraulic attachment sectors too, firms are offering novel solutions for the customer.
The SmartRig offers the benefits of GPS technology that allows for more accurate hole-spotting and provides a better blast pattern. Combined with the latest depth monitoring systems, this technology allows the blast designer and rig operator to improve blasting efficiency. More accurate drilling cuts fines production and results in a higher percentage of the blasted rock meeting size requirements, cutting the need for secondary breaking. In addition this equipment provides a more level quarry floor, reducing wear and tear on loading and hauling equipment.
According to Atlas Copco its SmartRig technology can make a major impact on quarrying costs overall, with major savings in the crushing process in particular due to the improved material size consistency. The machine is also available with the firm's mast shroud, which significantly reduces drilling noise to a projected range of just 350m compared with 1.4km for standard drills and allows the rig to be operated on sites close to housing.
At the compact end of Atlas Copco's drill range is the recently upgraded T15, a wheeled rig that weighs in at 2.5tonnes. This machine can be fitted with the compact but powerful COP 1019HF drifter as well as the proven COP 1022 and COP 1028 drills. Because of its light weight it can be loaded onto a small trailer for transport and yet can be used to drill holes from 22-45mm in diameter while offering a coverage of 18m2.
In terms of consumables Atlas Copco has a new, long-life TD40 DTH tool that can cope with pressure of up to 35bars and is offered in diameters from 110-130mm. For the tophammer drilling market the firm is also offering the T60 ThunderRod, which can be used with the most powerful rockdrills on the market for bench drilling applications and for hole diameters from 102-152mm.
Dutch company Dehaco says it is offering a price-competitive, high-performing alternative for the extraction, recycling and demolition equipment markets in the shape of its growing product line-up. The latest addition to the range is the MS130 Multi Shear, which tips the scales at 13.1tonnes and suits duties on heavy-duty excavators weighing from 70-140tonnes. Also new is the efficient Dust Fighter water cannon unit. This can be used to generate a fine mist spray, which can be used to control dust in minerals extraction operations. The unit is said to be cost-effective to run, with low power consumption and comparatively low water consumption Italian firm
Meanwhile long life is claimed for the CP range of hydraulic multi-processors, which can be fitted to carriers weighing from 2-50tonnes. Made of anti-wear Hardox plating the units are available with mechanical and hydraulic rotation. A similar long operating life is said to be a feature of the SC line of scrap shears, which weigh from 1.9-9.5tonnes. These units offer high cutting power and high cycle speeds of working cycles and long-term reliability. The firm's CR range of rotating concrete pulverisers feature wide jaw openings, high operating speed and high breaking power, as well as replaceable teeth and tips.
Sophisticated technology is a feature of
The high performance BR215 breaker is said to feature an innovative mounting system as well as a slim body design that allows it to be used in tight spaces. Weighing 1.22tonnes it can be used on carriers in the 16-26tonne range, as well as for crusher mounts.
Improved breaker life is claimed for the grease cartridge system from German company Vogel. This can be fitted to all breaker types according to the firm and features a 400gramme capacity cartridge that fits directly onto the breaker. The cartridges last for 4-5 weeks in heavy duty applications and 8-10 weeks in more standard operations but are quick to replace. The type of installation depends on the breaker brand. In addition, the firm is intending to introduce a grease cartridge system for use on cutter crusher attachments early in 2009 and this will feature similar components although the grease pump will be slightly different to suit the application.