Quarry firm Blue Mountain Minerals is improving output quality and productivity following the installation of a new CEMCO crusher. The facility is located in the Sierra Nevada foothills in Northern California, around two hours’ drive to the south east of Sacramento. This quarry has been providing customers in California with a variety of limestone and dolomite products for more than 150 years.
Blue Mountain is the largest producer of limestone products in northern California and provides quality materia
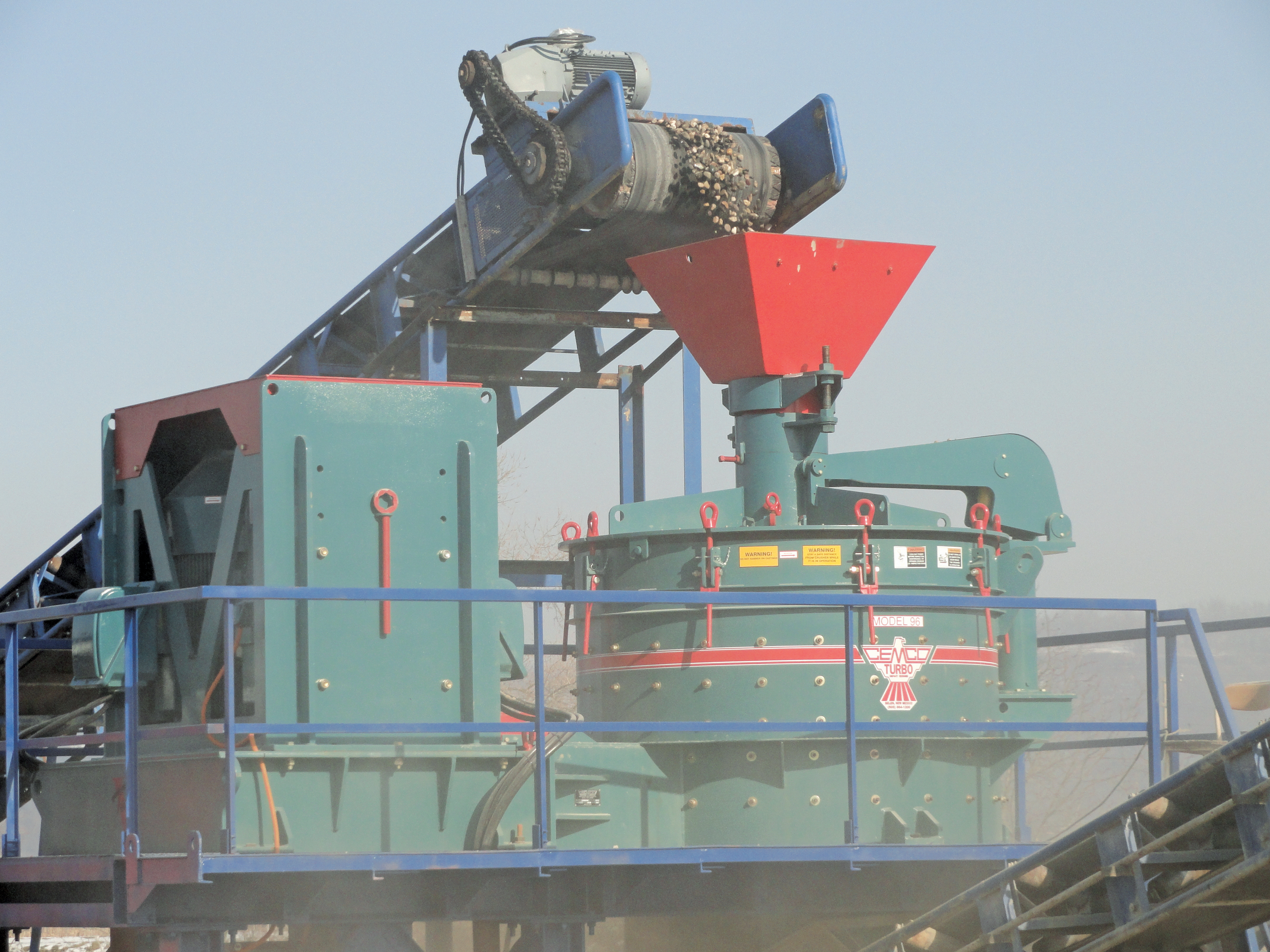
A new CEMCO VSI crusher is helping improve productivity and product quality at a quarry in the US
Quarry firm Blue Mountain Minerals is improving output quality and productivity following the installation of a new 6824 CEMCO crusher. The facility is located in the Sierra Nevada foothills in Northern California, around two hours’ drive to the south east of Sacramento. This quarry has been providing customers in California with a variety of limestone and dolomite products for more than 150 years.
Blue Mountain is the largest producer of limestone products in northern California and provides quality material for a wide range of industries. The company also takes a forward-looking approach to business including comprehensive planning for site reclamation and voluntary adoption of Tier 4 emissions compliance on all of its extraction equipment.
The facility features a large crushing operation with primary and secondary stages as well as a vertical shaft impactor (VSI) for the tertiary stage. This delivers a very narrow band product, with little difference in sizes from the top and bottom grades. The existing VSI had to be replaced as it was no longer able to meet product quality requirements as well as productivity targets. The old VSI was generating a high percentage of fines and had a recirculation load of 45%, making it hugely inefficient. The unit was not sufficiently able to cope with the specific grades of limestone and dolomite it was handling. The marbled limestone of the Blue Mountain site is hard and abrasive and generally results in a smaller natural particle size.
But the old VSI that the facility was using featured a rock shelf type of crushing rotor with little adjustment available to optimise performance and better suit the material grade. The high recirculation rate also increased the quantity of fines, with up to 10% of the material having to go to waste. Because of the high recirculation rate and the high percentage of fines, the old VSI was also using a lot of power and required two motors with a total power rating of over 670kW.
The site management realised that the high percentage of fines and high power requirement meant that the old VSI was inefficient. A newer machine could deliver a better quality product with a higher throughput yet use less power and also reduce the percentage of fines going to waste. The quickest option was to purchase a second VSI to augment production.
CEMCO is able to customise its machines for the operation and the material to be crushed, a process achieved through testing and constructing the crusher based on two key factors. These are the velocity of the rock after leaving the impeller, and time/energy of impact after traveling to an anvil ring or rock shelf. Because there are so many possible combinations of these factors, testing is crucial. The team used material samples from Blue Mountain and investigated different rotation speeds of the motor, rotor designs and throw distance of material from the rotor to the impact point. Speeding up the motor RPM produces smaller material sizes, while slowing it down delivers larger pieces. CEMCO went through dozens of rounds of testing before determining the optimal crusher for Blue Mountain, as well as the settings of that crusher. CEMCO’s recommended solution to Blue Mountain’s challenges was its VSI crusher V-Twin 96, equipped with an anvil ring.
The anvil crushing method used in the CEMCO VSI, features a semi-autogenous design, a rock-lined rotor and crushing chamber with anvils. This method provides a vertical wall that has a greater ability to control the material size based on the motor RPM. For this reason, an anvil ring can be used for harder, more abrasive materials. While CEMCO was able to adjust the speed and throw distances to adapt for the abrasiveness of the material being crushed, the site’s existing current rock shelf method VSI crusher was unable to make the necessary adjustments.
When testing was complete, the operation realised that the CEMCO VSI crusher had less than 10% recirculation rate as opposed to the rock shelf VSI crusher’s 45%. The CEMCO crusher was also able to run on less than half the power.
Blue Mountain is the largest producer of limestone products in northern California and provides quality material for a wide range of industries. The company also takes a forward-looking approach to business including comprehensive planning for site reclamation and voluntary adoption of Tier 4 emissions compliance on all of its extraction equipment.
The facility features a large crushing operation with primary and secondary stages as well as a vertical shaft impactor (VSI) for the tertiary stage. This delivers a very narrow band product, with little difference in sizes from the top and bottom grades. The existing VSI had to be replaced as it was no longer able to meet product quality requirements as well as productivity targets. The old VSI was generating a high percentage of fines and had a recirculation load of 45%, making it hugely inefficient. The unit was not sufficiently able to cope with the specific grades of limestone and dolomite it was handling. The marbled limestone of the Blue Mountain site is hard and abrasive and generally results in a smaller natural particle size.
But the old VSI that the facility was using featured a rock shelf type of crushing rotor with little adjustment available to optimise performance and better suit the material grade. The high recirculation rate also increased the quantity of fines, with up to 10% of the material having to go to waste. Because of the high recirculation rate and the high percentage of fines, the old VSI was also using a lot of power and required two motors with a total power rating of over 670kW.
The site management realised that the high percentage of fines and high power requirement meant that the old VSI was inefficient. A newer machine could deliver a better quality product with a higher throughput yet use less power and also reduce the percentage of fines going to waste. The quickest option was to purchase a second VSI to augment production.
CEMCO is able to customise its machines for the operation and the material to be crushed, a process achieved through testing and constructing the crusher based on two key factors. These are the velocity of the rock after leaving the impeller, and time/energy of impact after traveling to an anvil ring or rock shelf. Because there are so many possible combinations of these factors, testing is crucial. The team used material samples from Blue Mountain and investigated different rotation speeds of the motor, rotor designs and throw distance of material from the rotor to the impact point. Speeding up the motor RPM produces smaller material sizes, while slowing it down delivers larger pieces. CEMCO went through dozens of rounds of testing before determining the optimal crusher for Blue Mountain, as well as the settings of that crusher. CEMCO’s recommended solution to Blue Mountain’s challenges was its VSI crusher V-Twin 96, equipped with an anvil ring.
The anvil crushing method used in the CEMCO VSI, features a semi-autogenous design, a rock-lined rotor and crushing chamber with anvils. This method provides a vertical wall that has a greater ability to control the material size based on the motor RPM. For this reason, an anvil ring can be used for harder, more abrasive materials. While CEMCO was able to adjust the speed and throw distances to adapt for the abrasiveness of the material being crushed, the site’s existing current rock shelf method VSI crusher was unable to make the necessary adjustments.
When testing was complete, the operation realised that the CEMCO VSI crusher had less than 10% recirculation rate as opposed to the rock shelf VSI crusher’s 45%. The CEMCO crusher was also able to run on less than half the power.