Lafarge Aggregates Malaysia’s Kulai quarry is designed to the highest standards of safety, productivity and efficiency With an emphasis on high standards of safe, efficient and productive operations, Lafarge Aggregates Malaysia recently installed new quarry plant. It became operational earlier this year after Sandvik Mining and Construction Malaysia designed and installed a 250tonnes/hour, four-stage crushing and screening plant in Kulai, Johor, some 270km south of the capital Kuala Lumpur. It is now fully
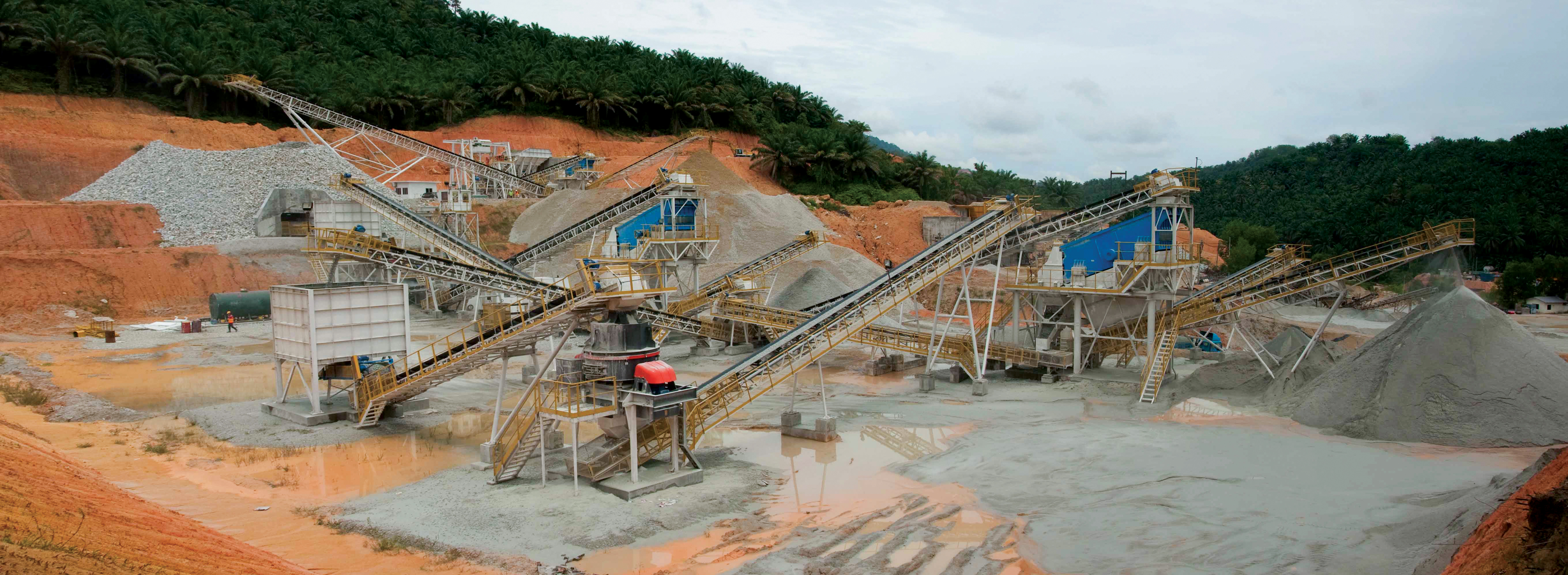
A panoramic view of the Kulai plant in Malaysia
Lafarge Aggregates Malaysia’s Kulai quarry is designed to the highest standards of safety, productivity and efficiency
With an emphasis on high standards of safe, efficient and productive operations,It became operational earlier this year after
Malaysia is proving to be a strategically important market for Lafarge Aggregates, and the new plant will play a key role in providing high quality aggregates for the expansive Malaysian construction industry.
The initial problem for Lafarge however was to not only install an aggregates plant capable of producing high quality end products, at high rates of production, but to be able to combine this required productivity with the highest standards of efficient, safe operation.
The driving force behind the plant design came from Lafarge Aggregates Malaysia’s emphasis in ensuring that the Kulai plant would be able to satisfy market demand for aggregates, and also that operational safety was endemic from the very start.
The initial specification for the plant reflected this commitment that would be continued during the construction and operation, which was carried out with no injuries and which was operational well ahead of schedule.
An example of this is the concrete surge tunnel being extended to facilitate openings from both sides, thus allowing for easier escape on either side should an emergency occur.
“Furthermore, walkways are wider than normal which allows for safer mobility, as well as enabling easier maintenance access,” says Sandvik.
“The finished plant possesses numerous other safety features that have been incorporated from the initial design concept, with many ideas resulting from the innovative thinking of Lafarge Aggregates Malaysia, and specifically the Kulai Quarry project team, with additional invaluable input from the Lafarge Health and Safety Department.”
At the very heart of the operation is a Sandvik CJ412 primary jaw crusher; a CS430 secondary cone crusher; a CH440 tertiary cone crusher and a CV228 quaternary vertical shaft impactor.
This equipment, when combined into the state-of-the-art plant design, has the capability to efficiently produce five different products at the required production rate of 250tonnes/hour.
The five products produced comprises ballast rocks; road base material; 10-20mm aggregates; 5-10mm aggregates, and manufactured sand.
The end products themselves are used throughout the Malaysian construction industry, with specific uses being found in ready-mix production; pre-cast requirements; road construction and general building work.
“What proved to be of particular interest is that although the plant has been designed to be capable of producing a 0-20mm product at 250tonnes/hour, but Lafarge testing of the plant has proved it to be capable of producing a 0-20mm product at a production rate of 291.2tonnes/hour,” says Sandvik.
According to the company its CH440 cone crushers are of advanced design, possessing a high capacity in relation to size, high reduction efficiency and producing excellent product shape.
The crusher has hydraulically adjusted CSS, optional automation, a choice of several different crushing chambers, and other high-performance features.
Another piece of crushing equipment used at the Lafarge Kulai aggregate plant is the CV228 VSI, which is part of the Sandvik CV200 series, developed to ensure that product shape and size are consistent.
“The innovative nature of the design also produces reduced power consumption, increased capacities, reduced maintenance costs, and vitally, requires fewer maintenance services,” says the company.
The CV228 has been primarily designed to operate as a third or fourth stage crusher, which fits in with Lafarge’s manufactured sand application.
Sandvik’s patented autogenous rock-on-rock crushing technique is said to result in several major advantages in the production of manufactured sand, including the consistently cubical product shape, which results from the extremely low flake and elongation values.
“Due to the design of the VSI [vertical shaft impactor] product gradation remains constant even as rotor wear parts wear, thus ensuring that contamination rates are extremely low as no wear parts are used to directly crush the rock. It is worthy of note that the autogenous crushing technique used in the crushing process not only mirrors the work of nature, but provides significant benefits in cement production due to the shape of the final sand product.”
The CV228 and the CV200 series utilise Sandvik’s patented Bi-Flow system and high-performance rotors, which are used in conjunction with the second generation wear parts that are said to have resulted in dramatic power reductions, yet capable of producing higher tonnage throughputs despite this reduction in power.
“The result of this development is that up to 20% of the maximum crusher throughput can be effectively handled through the Bi-Flow system, thus producing a significant saving in electricity costs and lowering of Lafarge’s CO2-emissions per tonne.”
Although the crushing plant is at the heart of Lafarge’s aggregate plant, further Sandvik equipment has been used, including a SGF1260 grizzly feeder; two E8203 vibrating screens and a BR927 hydraulic breaker. There is also an additional Sandvik BR927 hydraulic breaker at the primary production stage of the plant incorporated as an additional safety feature, and a BB285 boom system mounted on the primary opening.
“Malaysia’s ambitious and huge infrastructure development in the south of the country such as the Iskandar Corridor, and Singapore’s insatiable demand for building materials, will surely benefit from Lafarge Aggregates Malaysia’s new plant.”