A new VSI crushing system is helping Tarmac boost sand production at a key quarry in the UK. Manufactured sand is now being produced at the Tarmac Blashford quarry where a new VSI from Sandvik Mining and Construction is delivering product of high quality, specifically sized and shaped for construction purposes.
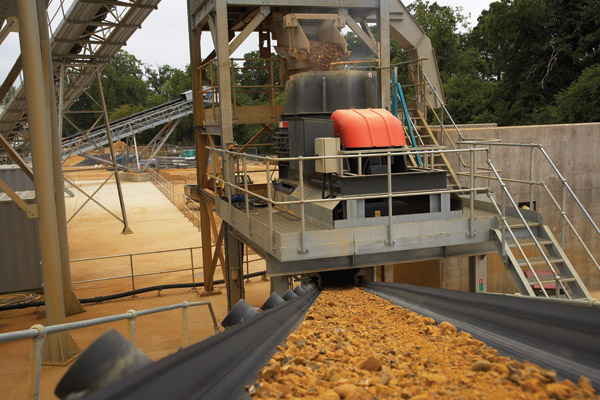
The patented design of the Sandvik VSI crusher is helping Tarmac produce high quality manufactured sand for use in the cement sector at its Blashford quarry
A new VSI crushing system is helping Tarmac boost sand production at a key quarry in the UK. Manufactured sand is now being produced at the Tarmac Blashford quarry where a new VSI from Sandvik Mining and Construction is delivering product of high quality, specifically sized and shaped for construction purposes.
Sand and gravel deposits are commonly found in the south east of the UK, with the fundamental difference between sand and gravel being the particle size. Essentially any material that passes through a 5mm sieve, but retained on a 63 micron sieve, is classed as sand; but all particles retained on the 5mm sieve are classed as gravel. Although Blashford quarry possesses substantial reserves of sand they are not as prevalent as the gravel deposits. But with the current shortage of natural sand due to new environmental legislation, there is now a need for the manufacture of sand from quarried material. As a resultThe design of the VSI means that product gradation remains constant even as rotor wear parts wear, minimising contamination as no wear parts are used to directly crush the rock.
The quarry screens its feed material after primary and secondary crushing in order to eliminate -10mm and +70mm materials. The output is then washed to remove any existing contaminants such as clay or lignite, before the remaining 10-70mm material is fed into the CV216. This ensures that the final sand product possesses the required cubical shape and is also clean and ready to use in the manufacture of cement. Sand manufactured by the CV216 VSI offers consistent quality and cubical shape, which is important for use in the production of concrete products.
A further benefit of this VSI is its low environmental impact as the crusher features Sandvik's patented Bi-Flow system and high performance rotors. These help reduce power requirements, while helping produce higher throughputs. Sandvik claims that up to 20% of the maximum crusher throughput can be handled through the Bi-Flow system producing a significant saving in electricity costs.