An Indian quarry facility has seen increased uptime and gains in overall efficiency due to the installation of new wear components in its crushing system
Installing new distributor plates in this Indian granite quarry has increased its plate operational lifetime by 400-500%. Panchami Stone has fitted the unique HX900 plates to the 85 HP rotor of its Sandvik Construction CV218 VSI, reducing its replacement costs by 50%.
The Panchami Stone granite quarry is located 60km from Bangalore, in the south of I
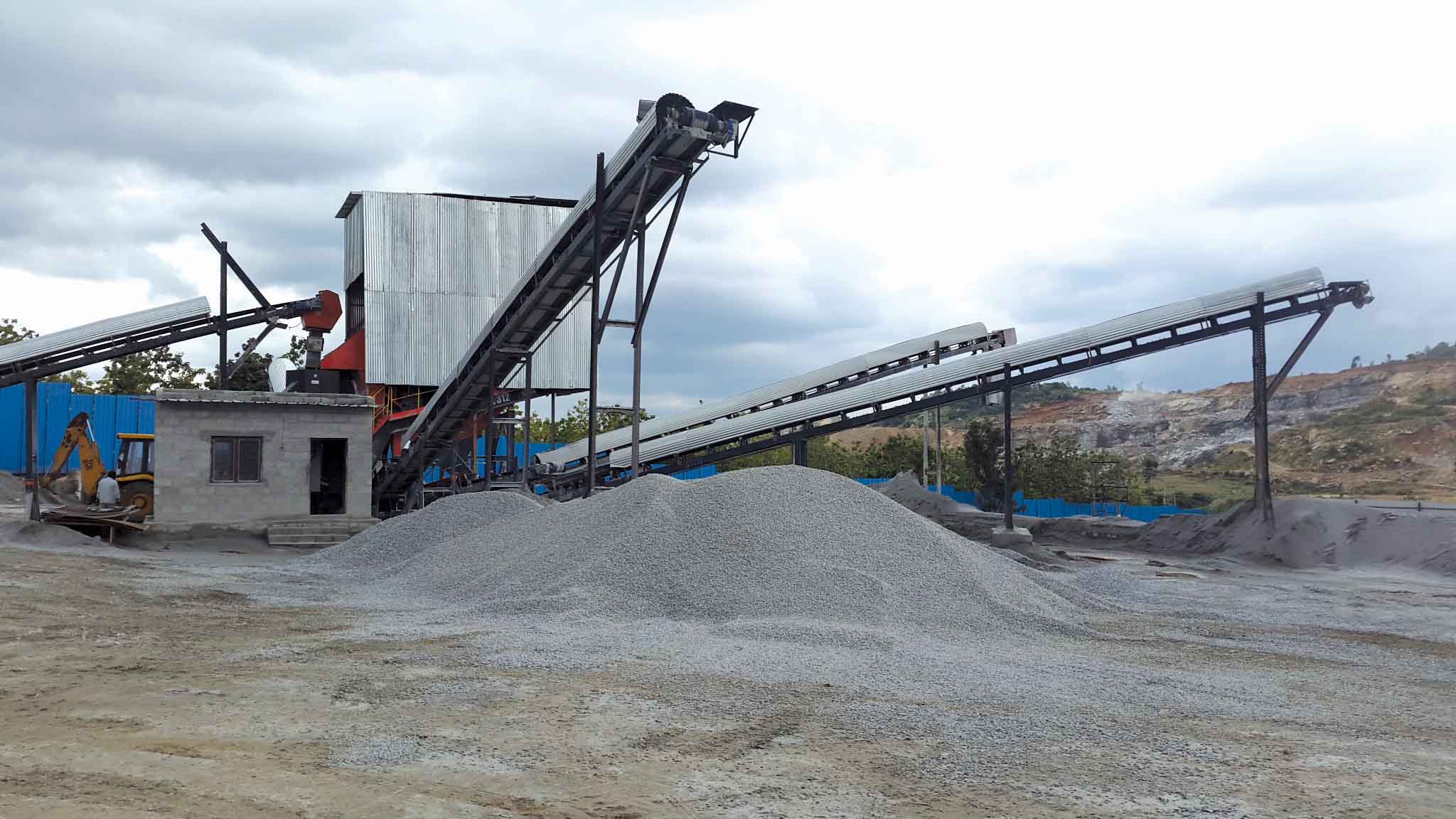
As a result of the new equipment, the cost/tonne has improved substantially
An Indian quarry facility has seen increased uptime and gains in overall efficiency due to the installation of new wear components in its crushing system
Installing new distributor plates in this Indian granite quarry has increased its plate operational lifetime by 400-500%. Panchami Stone has fitted the unique HX900 plates to the 85 HP rotor of its2403 Sandvik Construction CV218 VSI, reducing its replacement costs by 50%.
The Panchami Stone granite quarry is located 60km from Bangalore, in the south of India. The company originally acquired a Sandvik Construction UH311 Cone Crusher and a UV312 Vertical Shaft Impact crusher (VSI) in 2014 and 2015 respectively. The latter is fitted with Sandvik’s state of the art CV218 VSI which has proved ideal for manufacturing a quality sand product. This new plant operation replaced the company’s old jaw to jaw crusher configuration which had proved unable to produce the desired material fractions and end product quality.
The Sandvik wheeled semi-mobile cone and VSI crusher configuration has proved to be suited to manufacturing sand. Panchami Stone has also benefitted from improved production, reduced emissions and a lower cost/tonne operation with the CV218 providing many real benefits over other autogenous VSI crushers. As a result the CV218 and cone crusher plant has delivered optimised production.
The 0-36mm granite feed material at the quarry is fed from the cone into the VSI, from which the manufactured sand product is produced, at a rate of 40,000tonnes/month. Due to its shape the sand product has proved to be superior to naturally occurring sand, providing the local construction industry with a highly valued commodity. The problem for Panchami Stone was that with a work index of 18-20, and an abrasion index of 0.5-0.6, as well as a bulk density of 1.6m3/tonne, meant that the distributor plates on the VSI had to be replaced at regular intervals. This was not only affecting production, but also proving to be costly in both time and money.
The distributor plates Panchami Stone was using for the 85 HP rotor of the VSI had to be replaced after every 18,000tonnes. This meant that 2-3 plates had to be replaced each month, with production being affected due to increased downtime and longer service intervals which were having a negative effect on production costs.
Panchami Stone raised its problem with the Sandvik Construction team in India. Although very happy with the operation of the VSI, the company was becoming increasingly concerned about the effect the feed material was having on the distributor plate, and the number of replacements having to be made each month. The Sandvik India team suggested changing the type of distributor plate to be used, and suggested one of Sandvik Construction’s latest developments – the HX900.
Sandvik’s new HX900 distributor plates are a novel wear protection solution that is said to deliver lower maintenance and operating costs, as well as resulting in fewer maintenance stops. These factors all result in higher capacity over time. In terms of wear protection solutions, HX900 distributor plates deliver the lowest cost per tonne produced and more profit for customers. Additionally ease of fitting is inbuilt into the design, with the new HX900 distributor plates being easily locked onto an adapter plate.
The plates offer a longer wear life than earlier generation designs. This is due to a patented design, which consists of three different wear materials, and results in wear life being about five times longer than with conventional white iron distributor plates. Longer wear life means a minimum of maintenance stops, saving time on changing distributor plates.
A wear indicator clearly shows when it is time to change plates, and when it comes to changing plates, there is no need to lift off the crusher’s upper section. No crane is needed, and no time wasted, resulting in easier and safer installation. This last feature is further aided as the distributor plate is split into three parts, weighing only 5kg each. This makes handling easier and speeds up installation; a more user-friendly design resulting in safer service routines.
Panchami Stone was sceptical at first that the HX900 plates would be the solution to its problem. Sandvik convinced the company to trial the HX900 distributor plates. Following the adoption of the HX900, the distributor plates now only have to be replaced after 80,000tonnes of production; an improvement of up to 500%, with an operational cost saving of 50%.
In addition to the above, the handling of the plates is easier and speeds up their installation. This is due to its lighter, and more user-friendly, weight which also makes routine service safer. Possessing the longest wear life on the market, the HX900 plates require fewer stops, lower maintenance and operating costs, delivering more production. This resulting higher capacity has ensured that now Panchami Stone is able to benefit from the lowest cost/tonne, while benefiting from improved confidence in its production capabilities.
Installing new distributor plates in this Indian granite quarry has increased its plate operational lifetime by 400-500%. Panchami Stone has fitted the unique HX900 plates to the 85 HP rotor of its
The Panchami Stone granite quarry is located 60km from Bangalore, in the south of India. The company originally acquired a Sandvik Construction UH311 Cone Crusher and a UV312 Vertical Shaft Impact crusher (VSI) in 2014 and 2015 respectively. The latter is fitted with Sandvik’s state of the art CV218 VSI which has proved ideal for manufacturing a quality sand product. This new plant operation replaced the company’s old jaw to jaw crusher configuration which had proved unable to produce the desired material fractions and end product quality.
The Sandvik wheeled semi-mobile cone and VSI crusher configuration has proved to be suited to manufacturing sand. Panchami Stone has also benefitted from improved production, reduced emissions and a lower cost/tonne operation with the CV218 providing many real benefits over other autogenous VSI crushers. As a result the CV218 and cone crusher plant has delivered optimised production.
The 0-36mm granite feed material at the quarry is fed from the cone into the VSI, from which the manufactured sand product is produced, at a rate of 40,000tonnes/month. Due to its shape the sand product has proved to be superior to naturally occurring sand, providing the local construction industry with a highly valued commodity. The problem for Panchami Stone was that with a work index of 18-20, and an abrasion index of 0.5-0.6, as well as a bulk density of 1.6m3/tonne, meant that the distributor plates on the VSI had to be replaced at regular intervals. This was not only affecting production, but also proving to be costly in both time and money.
The distributor plates Panchami Stone was using for the 85 HP rotor of the VSI had to be replaced after every 18,000tonnes. This meant that 2-3 plates had to be replaced each month, with production being affected due to increased downtime and longer service intervals which were having a negative effect on production costs.
Panchami Stone raised its problem with the Sandvik Construction team in India. Although very happy with the operation of the VSI, the company was becoming increasingly concerned about the effect the feed material was having on the distributor plate, and the number of replacements having to be made each month. The Sandvik India team suggested changing the type of distributor plate to be used, and suggested one of Sandvik Construction’s latest developments – the HX900.
Sandvik’s new HX900 distributor plates are a novel wear protection solution that is said to deliver lower maintenance and operating costs, as well as resulting in fewer maintenance stops. These factors all result in higher capacity over time. In terms of wear protection solutions, HX900 distributor plates deliver the lowest cost per tonne produced and more profit for customers. Additionally ease of fitting is inbuilt into the design, with the new HX900 distributor plates being easily locked onto an adapter plate.
The plates offer a longer wear life than earlier generation designs. This is due to a patented design, which consists of three different wear materials, and results in wear life being about five times longer than with conventional white iron distributor plates. Longer wear life means a minimum of maintenance stops, saving time on changing distributor plates.
A wear indicator clearly shows when it is time to change plates, and when it comes to changing plates, there is no need to lift off the crusher’s upper section. No crane is needed, and no time wasted, resulting in easier and safer installation. This last feature is further aided as the distributor plate is split into three parts, weighing only 5kg each. This makes handling easier and speeds up installation; a more user-friendly design resulting in safer service routines.
Panchami Stone was sceptical at first that the HX900 plates would be the solution to its problem. Sandvik convinced the company to trial the HX900 distributor plates. Following the adoption of the HX900, the distributor plates now only have to be replaced after 80,000tonnes of production; an improvement of up to 500%, with an operational cost saving of 50%.
In addition to the above, the handling of the plates is easier and speeds up their installation. This is due to its lighter, and more user-friendly, weight which also makes routine service safer. Possessing the longest wear life on the market, the HX900 plates require fewer stops, lower maintenance and operating costs, delivering more production. This resulting higher capacity has ensured that now Panchami Stone is able to benefit from the lowest cost/tonne, while benefiting from improved confidence in its production capabilities.