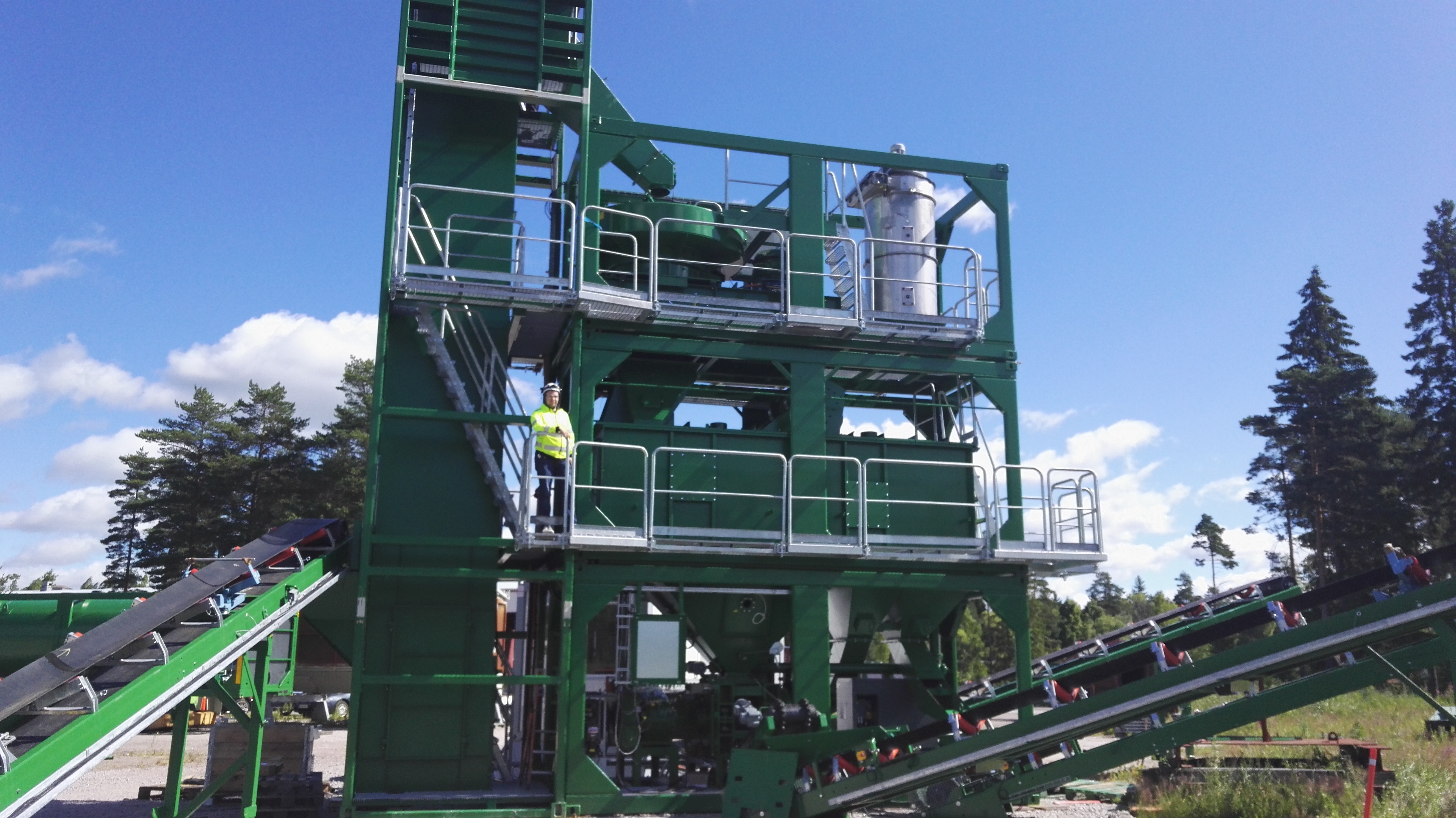
The new AMOPEPPER plant is now being tested at the
The way the system works is that the plant can be moved to an area where RAP material is available or material can be transported to the plant area.
Once these two are ready, RAP material is fed into the process and the end result is hard stones of two different sizes as well as bitumen pellets. These are squeezed so hard that nearly all moisture is eliminated. It has already been tested that these pellets can then easily be stored and won't absorb any more water. Stones can be used wherever, for the production of new asphalt or in other places, where good quality aggregates are needed.
"We will perform the last fine-tunings during week 29 and we will then be ready to start production,” said Casimir Kasvi.
“We appreciate the big amount of test material coming from our big customers. Once we are ready for production testing, we are going to study the results in a laboratory. We will also send the end material forward to asphalt plant owners for further studies. We have high hopes for this product and there has been a tremendous interest regarding this. According to our plans, we will be ready for testing at the end of September, after which we can start taking orders.
“We made some late design changes and now all modules of the AMOPEPPER plant are in CSC approved containers. This was because of the good feedback from customers that have purchased our Container Model (CM) plants."
AMOMATIC has been delivering these CM plants to different continents and reports very favourable feedback regarding this new product. "Customers are saying that this was actually the only available solution for them since they have narrow roads and that transportation is needed several times within a season,” said product manager Heikki Tiinanen. "When there is a possibility to transport the whole plant in CSC approved containers and that erection can be done within one day, there is already so much benefit coming out of this that the choice was easy to make."