Leading asphalt plant manufacturers have recently unveiled their latest products aimed at customers looking for significant efficiency gains through the use of durable and lasting technology. Guy Woodford looks at some of the new batch Benninghoven showcased a wide variety of its new and innovative asphalt plants and individual plant components during its week-long Open Days event last month at the German firm’s HQ in Mülheim. Launched earlier this year, the MMX80 Continuous Asphalt Plant is capable of prod
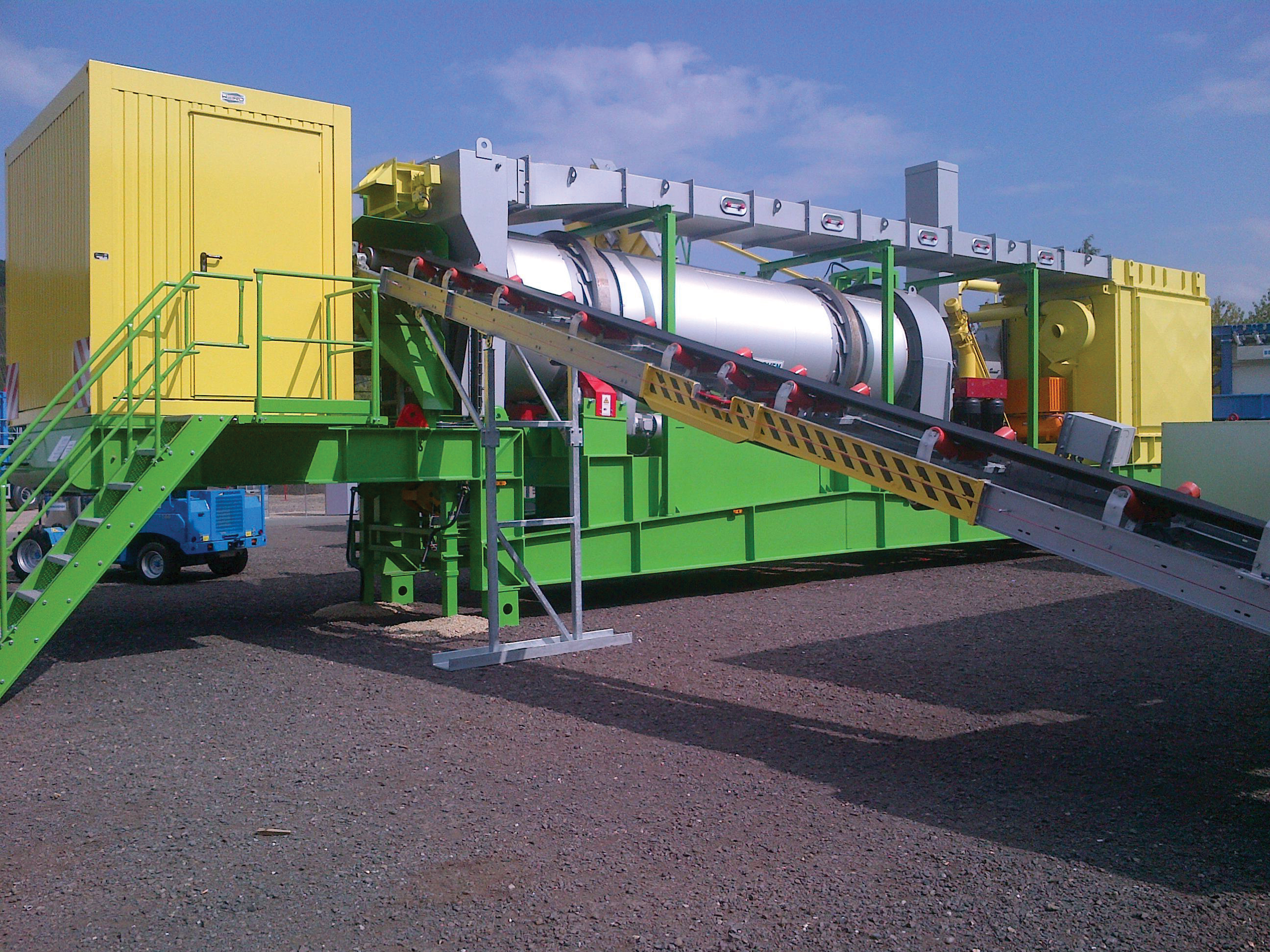
The new MMX80 from Benninghoven
Leading asphalt plant manufacturers have recently unveiled their latest products aimed at customers looking for significant efficiency gains through the use of durable and lasting technology. Guy Woodford looks at some of the new batch
components during its week-long Open Days event last month at the German firm’s HQ in Mülheim.
Launched earlier this year, the MMX80 Continuous Asphalt Plant is capable of producing 80 t/h of asphalt. It has two trailers: the first an aggregate and cold feed system; and the second featuring a continuous mixer, dryer drum, bag filter and bitumen system. In addition to the two trailers, the MMX80 can come with an optional bitumen storage tank.
“The MMX80 is mobile and can get to hard to reach locations,” said Mick Cornish, installation and service manager for Benninghoven UK.
The MMX80 is currently being used by Benninghoven customer JANAR on Reunion Island in the Indian Ocean.
Also on display at the Benninghoven Open Days was a prototype of the Eco Smart 1250 asphalt plant for hot mix asphalt.
Said to be built to a well proven Benninghoven design, highly mobile and quick to install, the containerised Eco Smart 1250 hot mix asphalt plant can be transported by ship or railway. It is designed around 12.19m or 6.09m container sizes, therefore shipping costs are significantly reduced compared to plants transported as bulk cargo.
“The design started with the mixing tower and then moved on to the whole plant,” said Martin Toon, technical manager of Benninghoven UK. “I think export-wise, we are hoping it’s going to be a popular plant. If interest is there good following the show, then we will start production straight away.”
Toon said that more recently, companies in Australia has been showing a lot of interest in Benninghoven plants.
“Due to the scale of the country, the companies involved with them want the capability of moving their asphalt plants around, keeping erection time to a minimum.”
Another Benninghoven prototype on show during the Open Days was a new RAP Recycling Drum using counterflow and indirect heating. The company says the prototype can accommodate up to 70% RAP materials in each mix, giving cost savings by heating much less virgin aggregates material, thus lowering plant operators’ carbon footprint.
A fourth new addition to Benninghoven asphalt plant and asphalt plant component range is the Multi-Variable Recycling Cold RAP (Recycled Asphalt Pavement) System.
With an asphalt and bitumen recycling capacity of 1.5tonnes, two of the systems’ are already said to be being operated successfully by a customer in France. “This has been the first time the system has been displayed at an exhibition,” said Toon. “It stops the build-up of excess steam, so it is more efficient. Too much steam means you have a longer mixing cycle, which means you’re limiting plant production.
“This system means you can increase the amount of cold RAP from 20% to 40% of an individual batch. In the UK there’s a big thirst for doing more and more with RAP material.”
Dirk Auler, of Benninghoven project planning, said the company’s Multi-Variable Recycling Cold RAP System could process up to 50% cold RAP under the right circumstances.
Finally, Benninghoven brand
Meanwhile another leading German firm,
Lintec also offers a new cold recycling system with a maximum of 25% recycled material. The standard system includes a cold feeder with two chambers, the conveyor belt and the RC hopper. The weighing of the recycled material is executed automatically and is said to be fully integrated into the control system.
Swiss firm
Ammann’s parallel drum is said to be best suited for adding larger quantities, up to 60%, of hot asphalt to a mix. In addition, the reclaimed asphalt drum RAH 100 is said by Ammann to be made for adding up to close to 100% to a mix. This is done using adapted blades and process air with no direct flame contact.
According to Ammann, adding near 100% of recycled reclaimed asphalt to a mix can lead to significant project cost savings on building materials. Utilising the company’s counterflow technology is said to realise further savings due to reduced fuel costs.
Meanwhile, claimed lower emissions due to the RAH 100’s asphalt recycling solution is said to allow better augmentation during the approval process. Gentle heating of binding agent contained in reclaimed asphalt is also said by Ammann to retain quality.
Reclaimed asphalt recycling recipes are said by the firm to be more flexible, preventing the need to overheat the minerals, while making work simpler for the mixing engineer.
Ammann claims its as1 plant control system’s new ‘dynamic RAP (Reclaimed Asphalt Pavement) addition’ option makes it easy to modify the RAP ratio according to need, even during production.
The as1 is said to achieve quantitative compensation, as the correction of virgin material is carried out in relation to the quantity and composition of the RAP material. In addition, as1 is also said to provide qualitative compensation, as the correction of virgin material is based on the quantity and composition of the RAP material to Ring and Ball standard (based on the formulae detailed in EN13108).
A prominent Italian firm playing a key role in constructing the new Villesse-Gorizia motorway link in North-East Italy, who were said to be looking for an asphalt plant which could guarantee maximum production levels while, at the same time, offering maximum flexibility and set-up speed, recently chose the
Keen collaboration between Marini’s technical staff and the customer during the project’s design stage is said to have led to the creation of an ideal plant to work on the Villesse-Gorizia project.
The steel base positioning of the aggregate cold feeders, together with other components of the Top Tower 3000 plant, are said by Marini to allow serial location of the plant on any type of suitable compact ground (2.5kg/cm²). In this way, the cost of plant accessories is said to be optimised and Top Tower 3000 can quickly and easily be transferred to subsequent working sites.
With this in mind, the bitumen and fuel tanks are also fitted with an overflow tank to prevent potential pollution in case of plant failure.
Marini says its client has paid a great deal of attention to reducing fume emissions into the atmosphere. As such, the hot mix storage is sheeted, ensuring that the plant components likely to have vapour loss have been duly dealt with.
The quality of materials is also said to have been a top priority for Marini’s client. From the very beginning, Marini says its customer wanted to use Ecogravel, instead of basalt aggregates, to guarantee a better quality of asphalt road pavement.
Ecogravel is said to have high abrasion characteristics. To accommodate this, thicker wearing plates have been required.
Ecogravel is produced as a steel by-product by the transformation of slag from the EAF (Electric Arc Furnace) fusion process. The slag cools slowly, to avoid excessive vitrification which would compromise the characteristics of the final product. Then the product undergoes the subsequent processes of crushing, screening and iron-removal to produce the required sizing.
One of the strengths of Ecogravel is said by Marini to be the reliability of the grading curve, which means it can satisfy highly stringent specifications. This result is said to be achieved because of the consistency of the raw materials produced in the crushing plant and the efficient quality control programme implemented by the Danieli Group (DG), conforming to CE regulations.
The environmental issues associated with the use of this precious steel by-product are described by Marini as “considerable”. It is established that the production of natural aggregate results in a heavy environmental footprint. However, DG is now able to transform a secondary material such as slag from steelworks into an industrial aggregate which can replace natural aggregate, said to result in natural resource and energy savings.
Of similar importance, says Marini, are the economic aspects connected with the use of Ecogravel. The cost of natural aggregates with specific performance rates (basalts and porphyries) is known to be higher in comparison with normal natural aggregates. Consequently, a secondary material like slag, that previously had to be suitably disposed of, can nowadays be considered a rich source of profit for the DG.