A series of new advances in asphalt plant design are now coming to market - Mike Woof writes
Key innovations in asphalt plant designs from major manufacturers will offer clients reductions in running costs along with gains in quality control and output. Several of the leading manufacturers are introducing new models that will deliver efficiency gains, as well as options for greater mobility and/or versatility.
Swiss-based Ammann is introducing two new mobile plants, the EcoBatch and QuickBatch models,
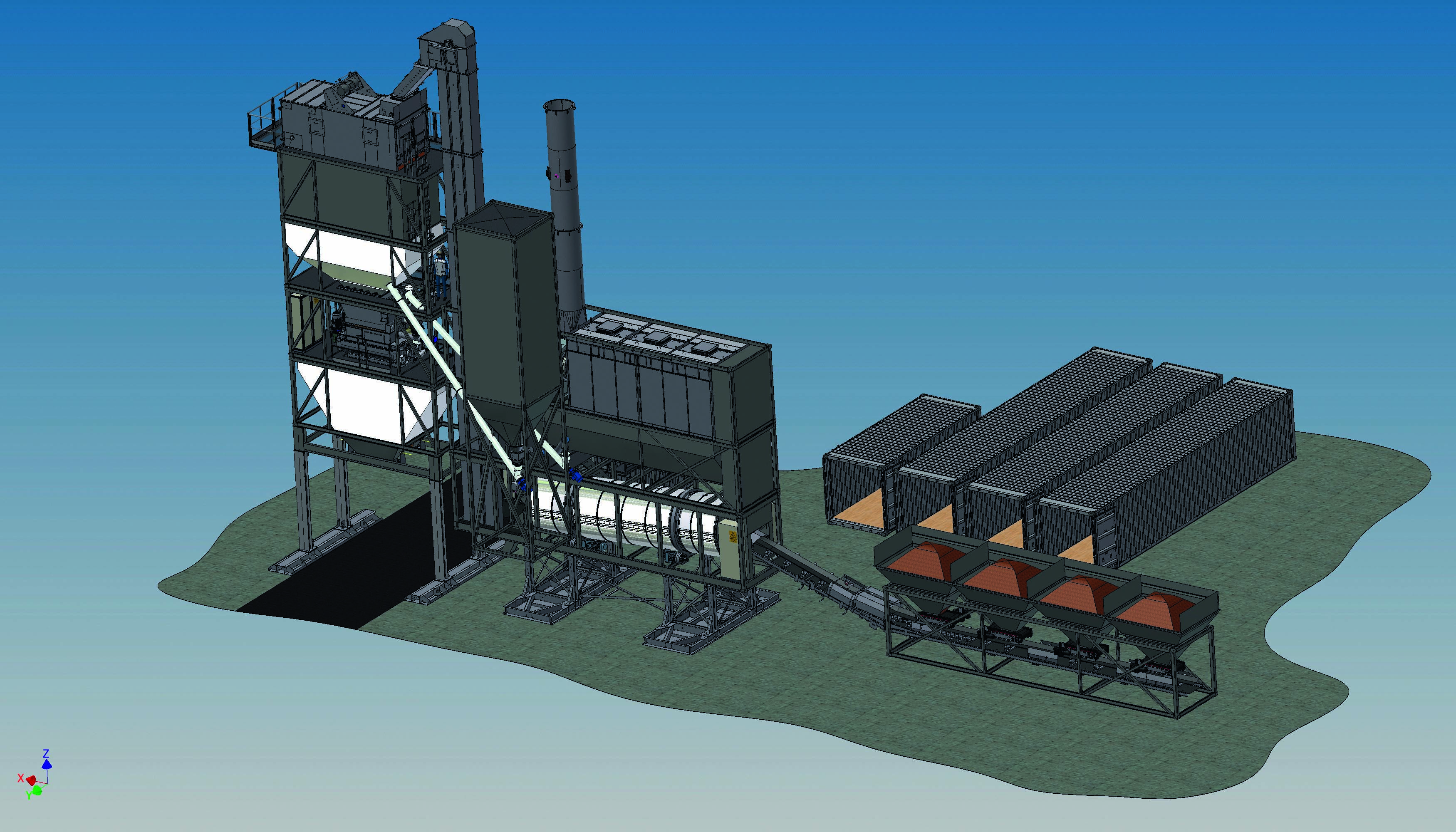
Amman is aiming its new plant at contractors wanting high production and mobility
A series of new advances in asphalt plant design are now coming to market - Mike Woof writes
Key innovations in asphalt plant designs from major manufacturers will offer clients reductions in running costs along with gains in quality control and output. Several of the leading manufacturers are introducing new models that will deliver efficiency gains, as well as options for greater mobility and/or versatility.
Swiss-based6791 Ammann is introducing two new mobile plants, the EcoBatch and QuickBatch models, aimed at capturing a wider share of the market. The smaller EcoBatch unit is designed for high mobility, while the larger Quickbatch is aimed at customers with higher production needs. Both plants are modular and designed for ease of transport, slotting inside standard-sized shipping containers.
The EcoBatch plant can deliver 60-80tonnes/hour of high quality material and is said to be optimised to reduce wear and maintenance needs, with easy access for servicing. Compact dimensions and high quality components are said to maximise performance and its basic layout can be amended with additional features including cold or hot reclaimed asphalt feed, liquid or solid additives and Ammann Foam. It also offers a host of options ranging from a basic plant to more sophisticated advanced versions. A smaller footprint makes it suitable for small level sites, whilst its ductless design eases assembly.
Maximum mixer capacity is 1.2tonnes, while the hot aggregate silo offers 16tonnes capacity and an optional hot mix storage silo has a 50tonne capacity. The plant is said to offer easy transportation due to features such as steel foundations and plug socket cabling, as well as a small footprint for use on sites with space constraints.
Aimed at contractors wanting to install a larger batching plant, the QuickBatch unit is designed for high production. The plant can be carried on eight trucks and fits inside standard 2.5m wide containers, lowering set-up costs but without compromising performance, quality or versatility. The plant delivers high output as well as a high asphalt mix quality. The dryer/filter units, mixing tower modules and add-on components, such as the cold feed and the control cab, all fit in standard containers. The QuickBatch is available with outputs of up to 140tonnes/hour and 180tonnes/hour and the firm says the plant offers the advantages of a stationary mixing plant, but is designed for international operation involving frequent moves for use at different locations.
Transportation infrastructure is geared towards container transport, so the design of this plant helps cut costs when moving it from site to site when this is over large distances, or even internationally. The individual components are placed in containers module by module. All the electrical and mechanical interfaces are pluggable to considerably reduce the time and cost of installation. The QuickBatch is said to provide all the functions and options of conventional plants and can be equipped with Ammann’s range of recycling solutions. The plant features five or six hot aggregate silos of 18m3 capacity, the firm’s 1.7tonne capacity QuickBatch 140 or 2.2tonne capacity QuickBatch 180 mixers and four cold feed bins as a standard, as well as the firm’s sophisticated as1 control system.
167 Benninghoven meanwhile has also developed its BBM 1250 asphalt plant with versatility and mobility in mind. Ease of transport and fast set up times allow mobility while the plant can deliver high quality output due to the use of the latest technology. Key to the plant is the firm’s BBX 1250 screening and mixer unit, which is designed to be transported on one truck while the whole plant can be moved on five trucks. The BBX 1250 section features a four deck screen and a 1.25tonne capacity mixer and can deliver up to 100tones/hour. The plant has four cold feed hoppers with a loading width of 3.6m and the drying drum is mounted on the same chassis for fast and efficient operation, while the hot aggregate bin unit can store up to 20tonnes.
Digital weighing and dosing ensures that the mixer delivers product to the specified formula. In addition, an innovative dust collection system includes a filter and exhauster as well as a 15m³ silo for reclaimed filler and a 25m³ silo for imported filler. And accurate mix control is offered by the BLS 3000 control system.
The innovative273 Marini-211 Ermont RF 160 Neo plant from the 2779 Fayat Group is said to deliver high-quality output at low cost. This, continuous asphalt plant features a modular design, so it can be adapted to customer needs, while also reducing the cost of ownership. The plant can be transported to site by truck, is said to be quick to erect, has low energy consumption and can use up to 50% recycled materials in its feed.
The plant can be set up in a highly sophisticated configuration for use in Europe or used in a more basic layout for emergent market needs. The plant can use recycled feed and key features include stacked filtration and drying units with an extra-short, fully insulated connecting duct and short fines recycling circuit. This layout is said to ensure high precision flow management. The plant is also said to meet the needs of contractors looking to lower carbon emissions.
The plant benefits from the firm’s advanced ECOdry, ECOdrive, ECOenergy, ECOstart, ECOflame and RECYCLEAN technologies, which help to lower energy consumption. Its output range is from 80-160tonnes/hour and the plant incorporates the firm’s Retroflux technology, featuring a counterflow dryer drum mixer. This configuration allows for the recycling of up to 50% RAP, while reducing the environmental impact. The control systems allow the optimisation of drum output, analysing and managing energy consumption ratios, and help reduce material losses.
In addition, Fayat intends to capture sales in additional market segments with its Packliner coldmix plant. The firm says that this plant suits duties in rural or urban road projects for which the use of products such as cold bituminuous mixtures is a major asset. Benefits include low production cost, easy transportation of mixtures and low greenhouse gas or smoke emissions.
This unit is equipped as standard with two feed bins for granular materials, with one volumetric bin and one weighing bin. This allows the production of mixtures based on virgin or recycled materials, and a third feed bin can be added as an option. The plant includes all of the necessary metering units for water, emulsion or cement metering units, in addition to the control and management cabinet, with these components mounted on a single chassis.
The design of the plant is said to optimise mobility and it can be transported in a standard container. This feature also allows for fast set-up times on site, due to pre-wired elements and factory testing prior to delivery. The plant supplements SAE's range of small to medium-output, continuous cold-mix production plants. Its compact installation reduces set up costs, without affecting production versatility or the quality of the mixtures obtained according to the firm.
Meanwhile Fayat is aiming its new 6tonne capacity asphalt mixer at a growing market for recycling. This larger capacity asphalt mixer is well-suited to handling mixes containing recycled asphalt according to the firm. To ensure good quality output, mixing times have to be longer when using recycled and virgin feed materials, so as to ensure homogeneity.
This new unit has been developed to meet customer requirements and is said to ensure the best quality of final product when using RAP. The large capacity of the mixer allows a constant production rate to be achieved despite an increased mixing time. In addition to meeting environmental targets by allowing efficient mixing of recycled materials, the unit also requires only a low energy consumption.
In European plant applications a common way to use RAP is to feed the material into the mixer. But when using higher percentages of RAP, it is necessary to extend the mixing cycle. This is because the RAP gains its heat through overheating of the other aggregates, prior to spraying of the new bitumen. And this results in a longer mix time. The new Marini mixer can use a feed of overheated aggregates and RAP, with its large capacity allowing sufficient time to expel the vapour while new bitumen can be injected precisely when the temperature is homogenous throughout the mix.
For example, a Marini Top Tower 4000 plant can produce around 320tonnes/hour with a conventional 45 second cycle. Increasing the mix time by 20 seconds to ensure the temperature gradient is the same across the mix when using feed combining recycled and fresh materials would cut output to 222tonnes/hour with the plant in conventional configuration. But using the 6tonne capacity mixer, maximum output of 320tonnes/hour can be achieved, while also ensuring product quality is optimised.
Key innovations in asphalt plant designs from major manufacturers will offer clients reductions in running costs along with gains in quality control and output. Several of the leading manufacturers are introducing new models that will deliver efficiency gains, as well as options for greater mobility and/or versatility.
Swiss-based
The EcoBatch plant can deliver 60-80tonnes/hour of high quality material and is said to be optimised to reduce wear and maintenance needs, with easy access for servicing. Compact dimensions and high quality components are said to maximise performance and its basic layout can be amended with additional features including cold or hot reclaimed asphalt feed, liquid or solid additives and Ammann Foam. It also offers a host of options ranging from a basic plant to more sophisticated advanced versions. A smaller footprint makes it suitable for small level sites, whilst its ductless design eases assembly.
Maximum mixer capacity is 1.2tonnes, while the hot aggregate silo offers 16tonnes capacity and an optional hot mix storage silo has a 50tonne capacity. The plant is said to offer easy transportation due to features such as steel foundations and plug socket cabling, as well as a small footprint for use on sites with space constraints.
Aimed at contractors wanting to install a larger batching plant, the QuickBatch unit is designed for high production. The plant can be carried on eight trucks and fits inside standard 2.5m wide containers, lowering set-up costs but without compromising performance, quality or versatility. The plant delivers high output as well as a high asphalt mix quality. The dryer/filter units, mixing tower modules and add-on components, such as the cold feed and the control cab, all fit in standard containers. The QuickBatch is available with outputs of up to 140tonnes/hour and 180tonnes/hour and the firm says the plant offers the advantages of a stationary mixing plant, but is designed for international operation involving frequent moves for use at different locations.
Transportation infrastructure is geared towards container transport, so the design of this plant helps cut costs when moving it from site to site when this is over large distances, or even internationally. The individual components are placed in containers module by module. All the electrical and mechanical interfaces are pluggable to considerably reduce the time and cost of installation. The QuickBatch is said to provide all the functions and options of conventional plants and can be equipped with Ammann’s range of recycling solutions. The plant features five or six hot aggregate silos of 18m3 capacity, the firm’s 1.7tonne capacity QuickBatch 140 or 2.2tonne capacity QuickBatch 180 mixers and four cold feed bins as a standard, as well as the firm’s sophisticated as1 control system.
Digital weighing and dosing ensures that the mixer delivers product to the specified formula. In addition, an innovative dust collection system includes a filter and exhauster as well as a 15m³ silo for reclaimed filler and a 25m³ silo for imported filler. And accurate mix control is offered by the BLS 3000 control system.
The innovative
The plant can be set up in a highly sophisticated configuration for use in Europe or used in a more basic layout for emergent market needs. The plant can use recycled feed and key features include stacked filtration and drying units with an extra-short, fully insulated connecting duct and short fines recycling circuit. This layout is said to ensure high precision flow management. The plant is also said to meet the needs of contractors looking to lower carbon emissions.
The plant benefits from the firm’s advanced ECOdry, ECOdrive, ECOenergy, ECOstart, ECOflame and RECYCLEAN technologies, which help to lower energy consumption. Its output range is from 80-160tonnes/hour and the plant incorporates the firm’s Retroflux technology, featuring a counterflow dryer drum mixer. This configuration allows for the recycling of up to 50% RAP, while reducing the environmental impact. The control systems allow the optimisation of drum output, analysing and managing energy consumption ratios, and help reduce material losses.
In addition, Fayat intends to capture sales in additional market segments with its Packliner coldmix plant. The firm says that this plant suits duties in rural or urban road projects for which the use of products such as cold bituminuous mixtures is a major asset. Benefits include low production cost, easy transportation of mixtures and low greenhouse gas or smoke emissions.
This unit is equipped as standard with two feed bins for granular materials, with one volumetric bin and one weighing bin. This allows the production of mixtures based on virgin or recycled materials, and a third feed bin can be added as an option. The plant includes all of the necessary metering units for water, emulsion or cement metering units, in addition to the control and management cabinet, with these components mounted on a single chassis.
The design of the plant is said to optimise mobility and it can be transported in a standard container. This feature also allows for fast set-up times on site, due to pre-wired elements and factory testing prior to delivery. The plant supplements SAE's range of small to medium-output, continuous cold-mix production plants. Its compact installation reduces set up costs, without affecting production versatility or the quality of the mixtures obtained according to the firm.
Meanwhile Fayat is aiming its new 6tonne capacity asphalt mixer at a growing market for recycling. This larger capacity asphalt mixer is well-suited to handling mixes containing recycled asphalt according to the firm. To ensure good quality output, mixing times have to be longer when using recycled and virgin feed materials, so as to ensure homogeneity.
This new unit has been developed to meet customer requirements and is said to ensure the best quality of final product when using RAP. The large capacity of the mixer allows a constant production rate to be achieved despite an increased mixing time. In addition to meeting environmental targets by allowing efficient mixing of recycled materials, the unit also requires only a low energy consumption.
In European plant applications a common way to use RAP is to feed the material into the mixer. But when using higher percentages of RAP, it is necessary to extend the mixing cycle. This is because the RAP gains its heat through overheating of the other aggregates, prior to spraying of the new bitumen. And this results in a longer mix time. The new Marini mixer can use a feed of overheated aggregates and RAP, with its large capacity allowing sufficient time to expel the vapour while new bitumen can be injected precisely when the temperature is homogenous throughout the mix.
For example, a Marini Top Tower 4000 plant can produce around 320tonnes/hour with a conventional 45 second cycle. Increasing the mix time by 20 seconds to ensure the temperature gradient is the same across the mix when using feed combining recycled and fresh materials would cut output to 222tonnes/hour with the plant in conventional configuration. But using the 6tonne capacity mixer, maximum output of 320tonnes/hour can be achieved, while also ensuring product quality is optimised.