Fayat is aiming its new 6tonne capacity asphalt mixer at a growing market for recycling. This larger capacity asphalt mixer is well-suited to handling mixes containing recycled asphalt according to the firm. To ensure good quality output, mixing times have to be longer when using recycled and virgin feed materials, so as to ensure homogeneity.
This new unit has been developed to meet customer requirements and is said to ensure the best quality of final product when using RAP. The large capacity of the mixe
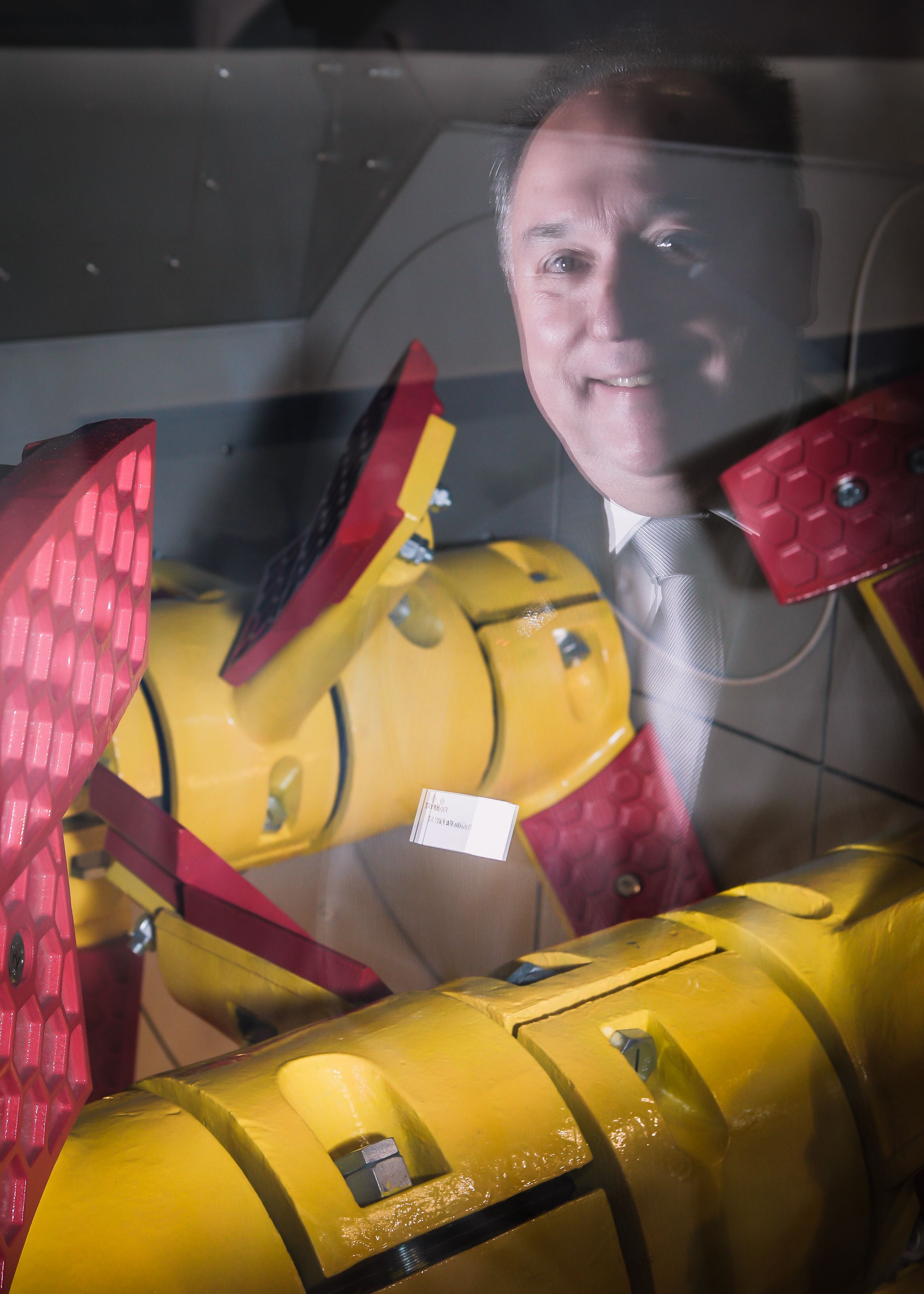
Fayat’s new 6tonne capacity mixer suits recycling use
This new unit has been developed to meet customer requirements and is said to ensure the best quality final product when using RAP. The large capacity of the mixer allows a constant production rate to be achieved despite an increased mixing time. In addition to meeting environmental targets by allowing efficient mixing of recycled materials, the unit also requires only a low energy consumption.
In European plant applications a common way to use RAP is to feed the material into the mixer. But when using higher percentages of RAP, it is necessary to extend the mixing cycle. This is because the RAP gains its heat through over-heating of the other aggregates, prior to spraying of the new bitumen. And this results in a longer mix time.
In the past, RAP was introduced into the mixer in contact with the overheated aggregates and new bitumen was fed into the mixer before the temperature was homogenous. This generated fumes containing high levels of VOC while the quality of the new bitumen was lowered due to oxidisation. High production rates from the plant would result in a low quality output as a result.
However, the new
For example, a Marini Top Tower 4000 plant can produce around 320tonnes/hour with a conventional 45 second cycle. Increasing the mix time by 20 seconds to ensure the temperature gradient is the same across the mix when using feed combining recycled and fresh materials would cut output to 222tonnes/hour with the plant in conventional configuration. But using the 6tonne capacity mixer, maximum output of 320tonnes/hour can be achieved, while also ensuring product quality is optimised.
The unit is as versatile as it is efficient according to the time. Paola Pezzi is in charge of communications at Fayat and said, “It can be retrofitted to existing plants.” The mixer can also be used with a wide variety of products such as liquid additives, solids and fibres. The unit is also suitable for use with cold RAP and in double drum as well as foamed bitumen applications.