Solutions for a reduction in emissions, recycling and more efficiency are being introduced by major asphalt plant manufacturers as Patrick Smith reports. The demand to reduce all types of emissions and increase the use of recycled material has put pressure on industry to come up with answers, and asphalt production is no exception.
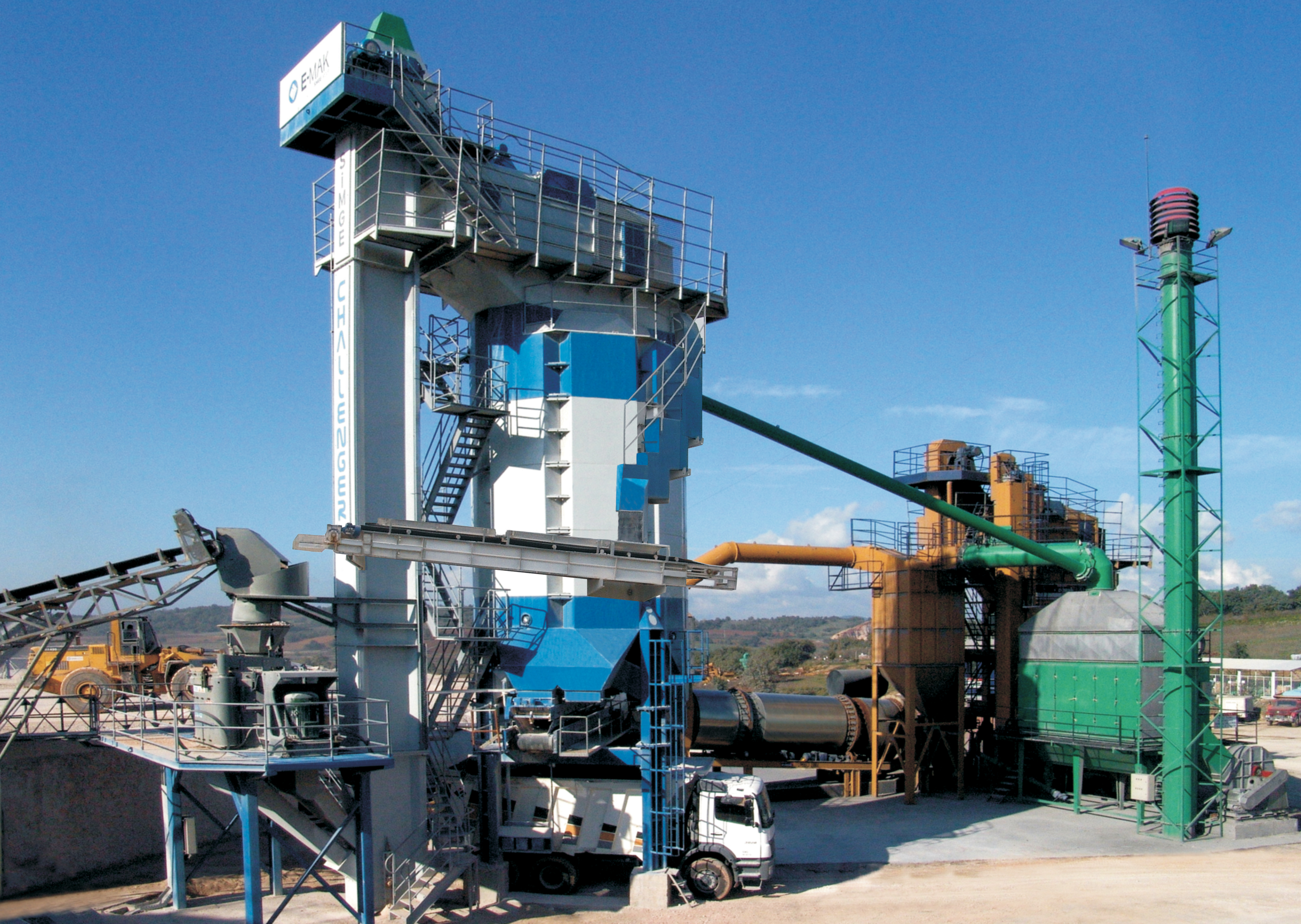
E-MAK has upgraded its Simge Challenger system
Solutions for a reduction in emissions, recycling and more efficiency are being introduced by major asphalt plant manufacturers as Patrick Smith reports
The demand to reduce all types of emissions and increase the use of recycled material has put pressure on industry to come up with answers, and asphalt production is no exception.However, the industry is tackling these issues with innovative solutions, including the increasing use of warm asphalt mixes in Europe (a trend now catching on in the USA and elsewhere); plants that can use high quantities of reclaimed asphalt pavement (RAP, see panel story), and plants that can be retrofitted with the necessary accessories.
For example, warm asphalt can be produced at lower temperatures and this is said to result in a reduction in emissions, dust and fumes, while at the plant during production there is a noticeable reduction of CO2; CO, Nox and dust, and while laying fumes are also reduced.
Other claimed benefits are savings in energy consumption; greater workability offering a longer construction season and an extended workability window; "performance and quality at least equivalent to that of hot mix asphalts", and it is suitable for base and surface layers.
"It is usually possible to lower the mixing temperature by at least 20°C and sometimes by as much as 70°C," said the company.
At the
The plant is also available as a mobile unit, but as a stationary continuous plant its forced twin paddle continuous mixer is said to provide a high quality and highly homogeneous asphalt mix.
"Clearly separating the material heating and mixing processes has reduced emissions and allows for a simple, precise and direct feed into the mixer. Starts and shut-down with no loss of material helps to keep production costs low," says Ammann.
With a plant height of 20m and a horizontal skip, the continuous mixer output ranges from 100-360tonnes/hr (the model on show at Bauma offered up to 300tonnes/hr), and it takes all types of additives such as fibres, powders and liquids.
Low temperature asphalt production is achieved with bitumen foam while the ContiMix can use a variety of fuels such as heavy oil, recycled oil and coal dust.
A SIM-designed dryer for asphalt mixing plants that can handle up to 50% RAP made its first appearance on the Ammann stand. Three of the Italian company's RAH 50 2390 models have already been sold in Italy where they have been tested. Details show that the dryer has an installed thermal power of 17.1MW (maximum installable power is 20.1MW), while the maximum output of asphalt at 3% humidity is 260tonnes/hr.
Meanwhile, Turkish manufacturer
"ÇESAN plants can reduce energy consumption, greenhouse gas emissions and improve efficiencies by reducing fuel consumption with its completely self-designed dryer, which operates on the basic principle of heat transfer to the aggregate. From this point for each 1tonne of asphalt a minimum of 1litre of fuel can be saved," said the company.
The New Top Tower TT4000 model from the
The TT4000 uses some of the features from the Top Tower TT3000 unit launched last year but now offers a throughput of 260tonnes/hour. This new plant comes in addition to existing plants, which have outputs of 180-200tonnes/hour.
According to sales and marketing manager Jacques Bonvallet: "This machine is not only bigger, the design is basically the same as the TT3000 but is now able to facilitate retrofits coming in the next few years." He explained that as asphalt technology is evolving, Fayat is keen for its machines to have capabilities for further modifications as required. The TT 4000 has been designed so that it can meet the needs of customer for the next 20 years and allow changes as they are developed.
Turkish company
"It works like a second asphalt plant," explained Emre Gencer, member of the board at E-MAK. To produce a binder course a percentage of fresh asphalt from the asphalt plant is used and this is mixed with the product from the RATech.
For a wearing course, a higher percentage of the fresh asphalt from the integrated plant is used. In addition, recycled asphalt concrete is added to the mixture through a weighing unit.
Scraper type conveyors inside the RATech carry the material through and prevent any sticking inside the system, while indirect heating to temperatures of 200-400ºC ensures that the material is kept at the correct temperature. Thermocouples inside the system measure the temperatures, "...so we know exactly the temperature inside the plant", Gencer said. The flow of hot materials inside the plant is from top to bottom, while heat loss of batched material is prevented due to a heated storage bin.
Inside the RATech plant the machine holds 17.5tonnes of material at a temperature of 145ºC.
The machine features its own mixer, equipped with bitumen weighing system and anti-ageing additive dosing unit.
The company has also upgraded its Simge Challenger system, which stores aggregates internally thus making major savings in heating and drying materials, cutting energy used in heating as well as CO2 emissions. Using the system can also boost aggregate output by up to 50% and increase asphalt plant efficiency by 15%.
Further benefits on fleet savings are made as the unit reduces the need for stocking and handling.
The Simge Challenger also increases efficiency and reduces bitumen consumption by 10-15%.
Although developed originally for asphalt production applications, it can also be used to provide aggregates into a large concrete batching facility. Two versions are available with stocking capacities of 200tonnes and 250tonnes.
The company claims that with its system an operator can decrease fuel consumption 14% by decreasing the mix temperature while having the ability to run higher percentages of RAP.