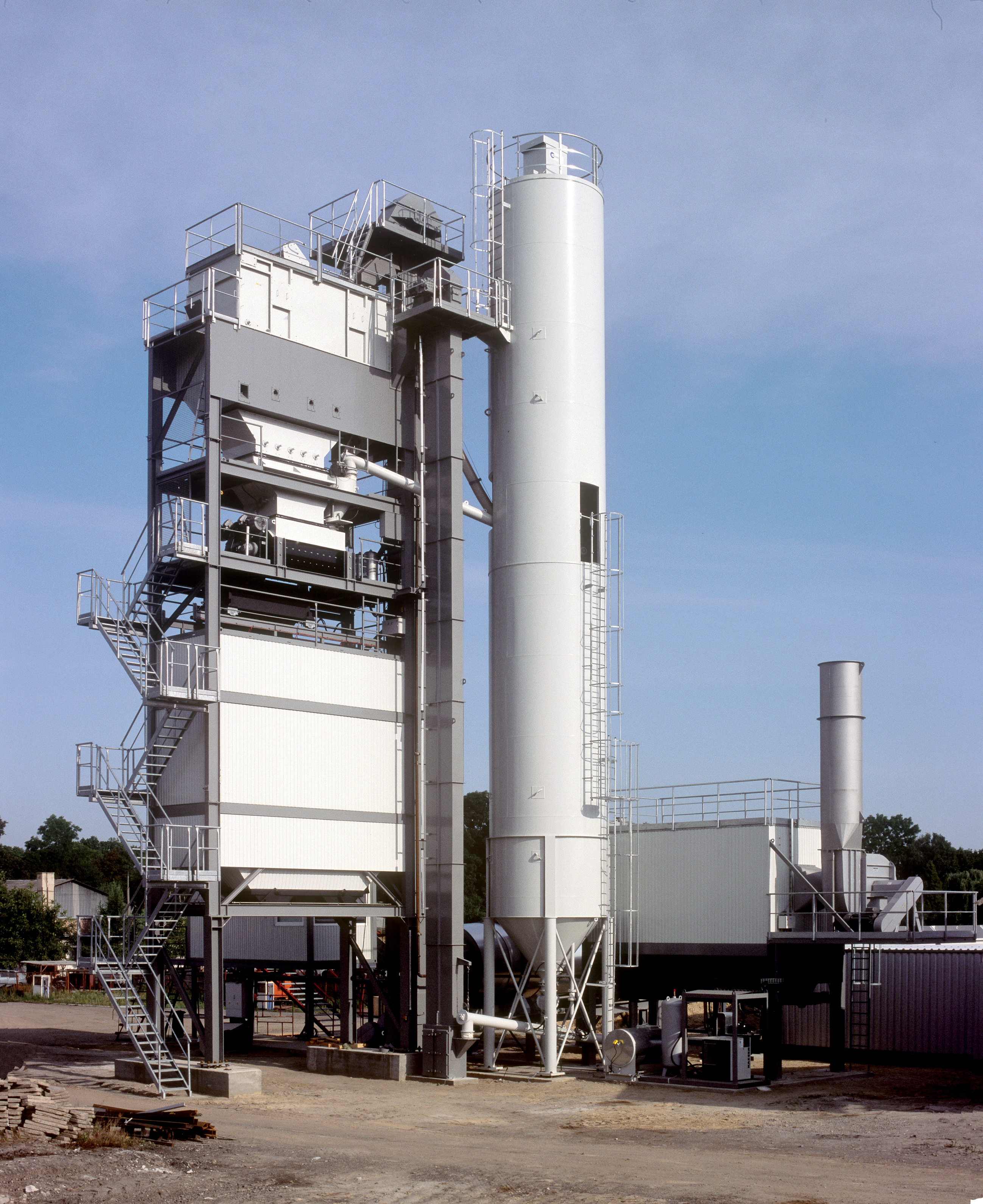
Modern asphalt plants are a far cry from the early models, and are capable of producing a wide variety of mixes at the touch of a button. Patrick Smith reports
Cutting-edge software-based control technology makes today's asphalt mixing plants simple and efficient to operate. The tightening of clean air regulations is reducing the emissions from the plants, and the current focus is on the goal of raising the processed portion of reclaimed asphalt (RA) towards 100%, saysOn reclaimed materials, it is also interesting to note that on remedial work on the A4 autoroute, near Paris, France, used as an experiment for 'carbon counting,' French toll road operator.
An innovative asphalt recycling technique at a rate of 50% was used for the scheduled heavy maintenance applications on the A28 motorway north of Le Mans, France.
A high-rate recycling kit, adapted to fit an existing TSR
Lasting nine weeks, the project involved 40,000tonnes of hot mix asphalts (HMA) with recycled aggregates and 34,000tonnes of traditional HMA. Conditions were excellent for the project, and the results were technically equivalent to those achieved on conventional projects, but the overall energy balance improved by 17.7%, greenhouse gas emissions were reduced by 15.6%, and the solution was more economical.
Ammann adds that the "challenges of the future are as fascinating as they are ambitious: CO² emissions are being reduced still further and ultramodern mixing processes will enhance production and encourage the use of low-temperature asphalt." Like many other companies in the industry, Ammann produces a range of fixed and mobile asphalt plants including the Global Uniglobe (80-300tonnes/hr); Universal/S/NG (160-320tonnes/hr); the City (240-340tonnes/hr and ContiMix (200tonnes/hr), while its mobile plants include JustBlack (120-160tonnes/hr); BlackMove (200tonnes/hr); SuperQuick (up to 280tonnes/hr) and the SpeedyBatch (up to 150tonnes/hr). The SpeedyBatch 150, introduced earlier this year, is one of a number of asphalt mixing plants from Ammann Group company SIM, and it has a nominal production capacity of 150tonnes/hr, while the features are identical to the other SpeedyBatch types, but the modules have a maximum width of 2.5m for easier plant transportation. SpeedyBatch is asphalt batching plant designed to offer maximum installation and dismantling speed, while maintaining the performance and possibilities of a fixed traditional system.
Only recently Ammann's UK branch, based in County Warwickshire, sold three asphalt mixing plants to Scotland at once. Ennstone Thistle opted for a Global 160 at Elgin on the north coast of Scotland, and for a Universal 240 and Global 120 at Orrick and Oban (both on the west coast).
MET: mobile and modular
Meanwhile, Italian manufacturer
The company says that while answering demands from producers of hot mix asphalt (HMA) for productive capacity and quality, some current asphalt plants can be improved further, particularly concerning wear resistance; simplification and cost reduction of technical maintenance as well as ecological aspects like the reduction of the energy consumption and "the dangerous escapes of undesirable substances into the external environment." It says it has achieved these targets by introducing MET technololgy over the past few years: the innovation mainly concerns the tower of batch asphalt plants.
At the
"MET is a new and different method of ensiling and dosing the hot aggregates, to be used with the same advantages whether the plant is fitted with a screen or not." The shape of the storage bin for hot aggregates from the dryer has been completely changed and compared to the traditional hopper is replaced by independent cylindrical silos (six at most). This with the dimensions fixes the volume and quantity of the different aggregates' storage capacity (over 200m3). The aggregates level inside the silos is constantly radar monitored and the plant is always ready to produce the requested asphalt formula.
Aggregates coming from the dryer are directed to the selected silo (for instance 0-4mm in the first bin, 4-8mm in the second until all the bins are full). It is possible to stock in two silos two different asphalts already mixed, taking from each feeder the quantity requested by the formula.
The continuous quantity aggregates measurements will give a linear signal and the plant software controls the feeder's speed output. This avoids wasting material already processed in the dryer, offering flexibility to make easier the manufacture management and to increase profit, says Bernardi.
Under each silo there is a weighing hopper, and with the MET method, the weighing of the single size material is done for deduction, while for mixing, the MET method can be used both on the small plant and on the 'hot stock type.' It can be fitted with small or big mixer to produce from 1.2-6 tonnes/batch, and discharge can be done directly into the truck, avoiding storage that could cause the mixture disaggregation, the bitumen oxidation and the aggregates exfoliation.
From the mixer the asphalt falls into the anti-segregation hopper: if fitted with certificated instruments this would be used for delivery notes.
The silos and weighing hoppers are enclosed in a single electrically heated shell, insulated and protected from the outside where only the mechanical devices and control instruments are placed.
"This allows users to stock the hot aggregates for a long time and they are always ready to use. This insulation also offers respect of the environment because all the dusts and steams produced during the screening and the mixing of the aggregates develop inside this shell of wide volumetric capacity," says Bernardi.
The MET-MT (MET Modular Type) batch type plant has MET technology built with pre-assembled modules. With this new plant, Bernardi has joined all the MET's typical advantages with a modular frame construction for faster and easier installation on site.
The tower is divided into five easily bolted together modules (3m x 6m x 3m), and the base frame, assembled on site, is the portal on which the modules are placed (all electric, pneumatic parts and oil diathermic heating systems are prewired in factory).
While all the modules are standard dimensions, they can be fitted out differently according to the requested output per hour. For example, in the MET-MT 30 tower shown at Samoter, from the base frame the sequence from bottom to top is the mixing module fitted with a 3 tonne capacity mixer ensuring 220tonnes/hr production and the weighing module made using six cylindrical 3m3 capacity hoppers, each fitted with a loading cell and with pneumatic opening, thus keeping in tune with the typical MET technology.
Continuing up the plant, the storage bins module has six 4m3 capacity cylindrical bins for hot aggregates. With hoppers and bins there is 7m3 capacity for each aggregate: total aggregates storage is 42m3 (an optional module increases storage capacity).
The conveyors module contains all the equipment to convey the aggregates from the screen to the storage bins while the screen module is fitted with 12° inclined high output screen (five selections plus direct line).
The tower of the MET-MT can be equipped to use recovery and commercial filler, each one with its own weighing hopper.
The MET Mobile batch plant, subdivided in semi-trailers, is towed by normal two axle tractors. Two new semi-trailers are coupled to the other standard semi-trailers forming the plan including feeders, dryer and filter.
The first is the MET tower and the second is fitted with the hot aggregates elevator and the filler elevator with two silos for recovery and commercial filler (40m3 and 16m3).
At Samoter, the tower presented was the MET 19M offering four selections and an output of 170tonnes/hr with a batch of 1,900kg. It weighs 36tonnes and has transport dimensions of 13.7m x 3m x 4.2m.
According to Bernardi, tower installation is easy and fast: from the transport position the two modules are separated, the part containing the hot storage and mixer is vertically placed, and the screening is put on the top by a crane. The tower is ready to work.
"After the great success of MET idea, with these two new models, the modular and the mobile, Bernardi Impianti International gives clients an answer to their different needs, completing the application range of this new technology," says the company.
'Firsts' for Astec
The first
YoungJong Industry of Ul-San, in the south-east of the country, bought the 180tonne/hr facility and is currently working with government regulators to study the sustainability of paving with reclaimed asphalt pavement (RAP).
To test the performance of RAP, YoungJong operators paved the road into its facility with asphalt pavement that included 20-50% recycled material, and with the South Korean officials will be monitoring the sustainability and quality of RAP.
In July YoungJong organised a seminar for contractors, government officials and academics, at which Astec chief engineer Greg Renegar spoke on running RAP with the Astec Double Barrel Drum dryer/mixer and about maximising RAP usage, to support YoungJong's efforts.
Meanwhile, further to the west, BMT Construction and Transport Company of Ho Chi Minh City began operating the first Astec facility in Vietnam early in 2008. The relocatable facility, including the 2.1m Double Barrel dryer/mixer, is rated to produce 270tonnes/hr. Commissioned in April the facility is now producing up to 35,000tonnes/month, making BMT Construction and Transport Company a major supplier of hot mix asphalt in the region.
The Asian successes come as Astec announced that its parent company, Astec Industries, is to expand its asphalt plant manufacturing business with the acquisition of Wisconsin, US-based Dillman Equipment, which produces asphalt plant equipment.
Astec president Ben Brock said: "This is a great move for both companies. As we looked ahead, we felt like our international business would only increase over the life of our division. Given that growth potential, we were considering two options: build more factory space at our Chattanooga location or buy more factory space. As we were considering our options we were fortunate to be able to partner with Dillman. It is a good fit and we will work to grow all of our facilities long term. As our international growth continues and we work to grow our market share in North America, we now have the manufacturing capacity we need for both markets for the next five to ten years."
ÇESAN's expansion plans
Turkish manufacturer ÇESAN, founded in 1989, says it is becoming a global brand having started to produce asphalt plants in 1995.
Its modern production facility covers 24,000m² at Sincan Industrial Zone, Ankara, where it employs 130 staff.
The company is about to complete a new production facility at the same industrial zone, and plans to expand its production range with products such as concrete batching plants and bulk trailers, while research and development studies are also continuing to manufacture batch type and drum mix-type mobile asphalt plants on a single chassis.
ÇESAN is certified by the ISO 9001:2000 Quality System Certificate, and its production range includes drum mix type stationary and mobile plants from 60tonnes/hr to 300tonnes/hr capacity in standard versions, although if there is demand higher capacity plants can be produced. The company also produces related products and components such as thermal oil heater, high pressure burners, dryers, screens, filters, bitumen and fuel tanks, along with batch type stationary and mobile plants.
ÇESAN says it sets high standards and applies advanced technology developing its business providing engineering know-how, assembling, technical, maintenance and spare parts services.
"ÇESAN, aiming to be a world brand, has increased export volume in recent years and added to its portfolio Iraq, Algeria, Sudan, Kazakhistan, Bulgaria, and new countries such as Afghanistan and Albania in 2008. The company is improving commercial operations by marketing studies, frequently participating in domestic and international sectoral fairs," says Turgay Üçbudak of "ÇESAN.
Looks familiar, but...
Kalottikone of Finland says that at first glance very little has changed externally on its mobile Hot-Mix 30M asphalt plant since the first unit of Hot-Mix series was made in 1982.
"Actually, the concept used to put up a very mobile and compact plant has shown its viability so forcefully that the mechanical setup has remained much the same," says the company.
"Similarity, though, is misleading. Almost everything has been revised thoroughly: materials, components and the automation." The Hot-Mix series of mobile plants was developed to respond to the specific requirements of Northern European road construction companies: short asphalting season; lots of small contracts scattered over the region; long daylight time in summer and, sometimes in sparsely populated areas, bad quality roads for moving the plant to a new spot.
"Possessing a highly mobile plant, a contractor was able to fulfill a number of contracts with a good total asphalt production record. In Sweden, a 200tonnes/hr capacity Hot-Mix plant is relocated typically in three days (from the end of the asphalting job to the beginning of a new one). As every single day used for dismantling, transporting and erection is a day out of generating revenues, an easy relocation without problems is highly appreciated," says Kalottikone.
Since their introduction, Hot-Mix asphalt plants have been exported to more than ten countries from Scandinavia to China.
"Russia has been one of the most interesting markets since the beginning of 1990s. Kalottikone has supplied Hot-Mix 30M and 45M asphalt plants to Russian customers along with cold asphalt plants, asphalt remixers and pavement preheaters."
In 2006, GUP Spetsdorstroi, a Murmansk City-owned road construction and maintenance company, bought a 250tonnes/hr Hot-Mix 45M plant. It covers the demand for asphalt in the city and still has capacity to provide outside areas with high-quality asphalt.
Race against time
With October 2009 fixed as the date for the Abu Dhabi Formula One Grand Prix, a Linnhoff asphalt batching plant is being used in a race against time to complete the new circuit.
Linnhoff Technologies of Singapore won a contract to supply the Linnhoff tower plant LH3000 to the International Grand Prix circuit now under construction in Abu Dhabi. It will be the sole unit supplying asphalt for the 5.6km circuit, having been commissioned in June.
The Linnhoff LH3000 has an integrated hot storage silo that can hold 150tonnes of hot mix asphalt and which is placed below the twin-shaft mixer in a heat-economising design.
The plant, which will be producing up to 240tonnes of asphalt/hr for the construction of the track surface, has been delivered to the joint Malaysian and Bahrain construction firm CEBARCO-WCT Engineering, which is handling the asphalting part of the contract.
Linnhoff Technologies is a division of
The double screen drum system designed and patented by Lintec features the heating and screening components in a single elevated unit.
"As demand for asphalt continues to boom on extended 'out of town' highways, transportation is becoming more of a problem (in terms of transportation, costs and traffic restrictions) in locating the asphalt plant along the new routes," says Lintec.
"One solution is for containerised asphalt batching plant which can be quickly and easily dismantled, moved and re-erected as work on the new highway progresses, reducing transportation costs ensuring reduced delivery times." The Lintec CSD range features four models to offer production capacities of 120-270tonnes/hr.
KVM Viking for Ireland
Michael Cronin (Readymix), based in Killarney, Ireland, which supplies aggregate products, saw the potential of turning the Millstreet Quarry in County Cork into asphalt, and in late 2006 chose Danish company KVM to supply a new asphalt plant. The smallest KVM Viking plant was ideally suited for the business and the location.
The Viking plant is rated for 160tonnes/hr based on a 2,000kg mixer. The KVM drying plant is powered by a 13.4 MW KVM-CBS dual fuel burner for light fuel and preheated fuel. The mixing tower holds 64tonnes in six bins and the hot storage holds 200tonnes in three silos.
KVM batching equipment for fibre pellets was part of the installation as well as the KVM 3000 Control System.
Congress hears about E-MAK innovation
Another innovation in asphalt production was highlighted at the recent
S. Emre Gencer, a member of the board of The
The presentation was selected from papers by renowned specialists from the asphalt and bitumen industry, and was one of three oral presentations during the Innovation Showcases.
According to Simge, the "European scientific field was astounded with the technology Turkey presented to the world," and the company expects the new invention will spread faster in Europe than Turkey.
In his presentation, S. Emre Gencer explained that the Simge Challenger is a cost-reducing, asphalt quality-increasing, stocking area-decreasing, environmentally friendly, closed-system crushing, sieving, stocking, feeding unit that can be integrated in all asphalt plants.
The Challenger is fed with 25-70mm material. The percentage of the humidity is reduced to only 0.2% in aggregates which come from the Challenger system, says the company.
"In other words, the relative humidity of aggregates coming from the Simge Challenger system is 25 times less than that of aggregates stored in open areas in conventional crushing and sieving systems. As a result, all the disadvantages arising from high moisture content are removed." Often a wide area is needed to stock the raw material during conventional asphalt production.
"In this mainly open-air stocking area, mainly fine aggregates of 0-5mm in size, which comprise 50% of the mixture, gets wet from rain and are scattered around the air by wind. Consequently, these micro-granular fine aggregates are wasted. The environment is polluted and the rest of the material gets dirty and starts to oxidise.
"Such microscopic dust particles of stone formed as a result of crushing and sieving of aggregates in the Challenger system, are absorbed and collected in the asphalt plant's filter unit. This filler material, a vital part of asphalt production, is added into the system at no extra cost. Aggregate which has gained temperature during the crushing process is transferred to the dryer. The reduced humidity and emissions protects the environment and the asphalt plant burns less fuel/money," says the company.