Varna Airport in north-east Bulgaria provides an important international link for the country, with a runway rebuild helping improve capacity.
The airport is of particular importance for Bulgaria’s tourist trade as it provides a major connection for visitors to the Black Sea coast. And the reconstruction work at Varna Airport’s only runway will ensure the facility is able to handle the area’s increasing visitor numbers.
The project had to be carried out quickly and efficiently to prevent delays to f
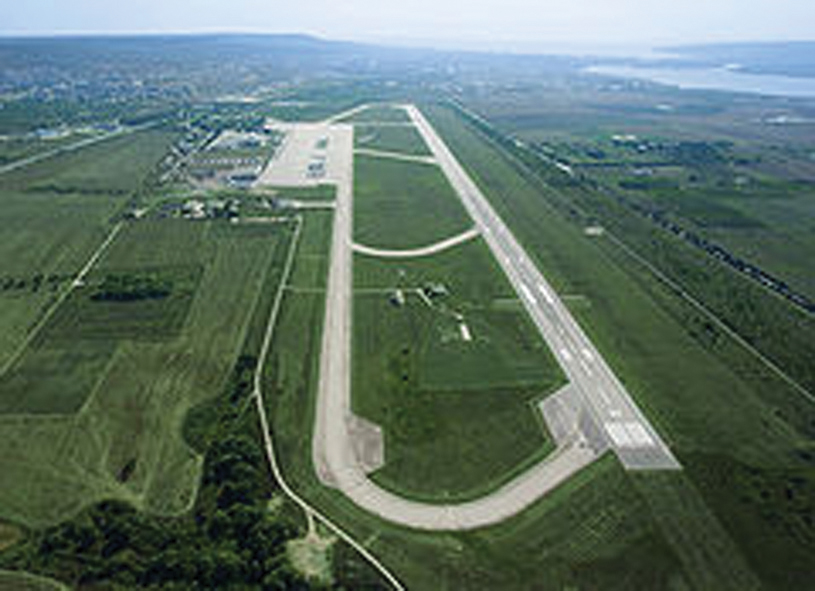
Varna Airport in Bulgaria is now benefiting from a new asphalt surface over the original concrete runway
Varna Airport in north-east Bulgaria provides an important international link for the country, with a runway rebuild helping improve capacity.
The airport is of particular importance for Bulgaria’s tourist trade as it provides a major connection for visitors to the Black Sea coast. And the reconstruction work at Varna Airport’s only runway will ensure the facility is able to handle the area’s increasing visitor numbers.The project had to be carried out quickly and efficiently to prevent delays to flights and the work was organised by the concessionaire of the Varna Airport, Fraport, which also operates Frankfurt Airport. The company commissioned a consortium comprising German firm Max Bögl and Bulgarian company Ingstroyengineering to carry out the construction work. The airport was closed from mid-October 2011 to end-February 2012 and work was then able to start.
The project required covering the existing concrete runway with a 300mm thick asphalt layer, as well as extending the shoulders. This used a total production of 150,000tonnes of asphalt within a six-week period, with work carrying on at the site seven days/week and 24 hours/day.
The quality and consistency of the asphalt used was crucial and the contractor opted to use two ECO 4000 semi-mobile asphalt mixing plants from
For the project each plant was equipped with six cold bin feeders of 12m² each, multi-fuel burners fired by gas or oil, five deck screens, 55tonne capacity hot bins and 4tonne capacity mixers.
The bitumen supply for the two asphalt plants had a total volume of 480m³, using eight high-efficiency, vertical bitumen tanks of 60m³ apiece. Three of the tanks were also equipped with vertical agitators to allow the storage of polymer modified bitumen (PMB).
The job required some 60,000tonnes of asphalt with PMB for use in the binder and wearing course. The PMB was itself produced using a Benninghoven polymer plant. The bitumen storage systems of the two plants were connected, so that the material could be pumped at any time and asphalt production could run continuously.