A survey carried out jointly by the National Asphalt Paving Association (NAPA) and the Federal Highway Association (FHWA) shows that asphalt recycling and energy-saving technologies are in increasing use in the US
The increasing adoption of new construction practices in the asphalt pavement industry has saved more than US$2.2 billion during the 2011 paving season through the use of recycled materials and energy-saving warm-mix technologies.
According to a survey conducted by the National Asphalt Pavem
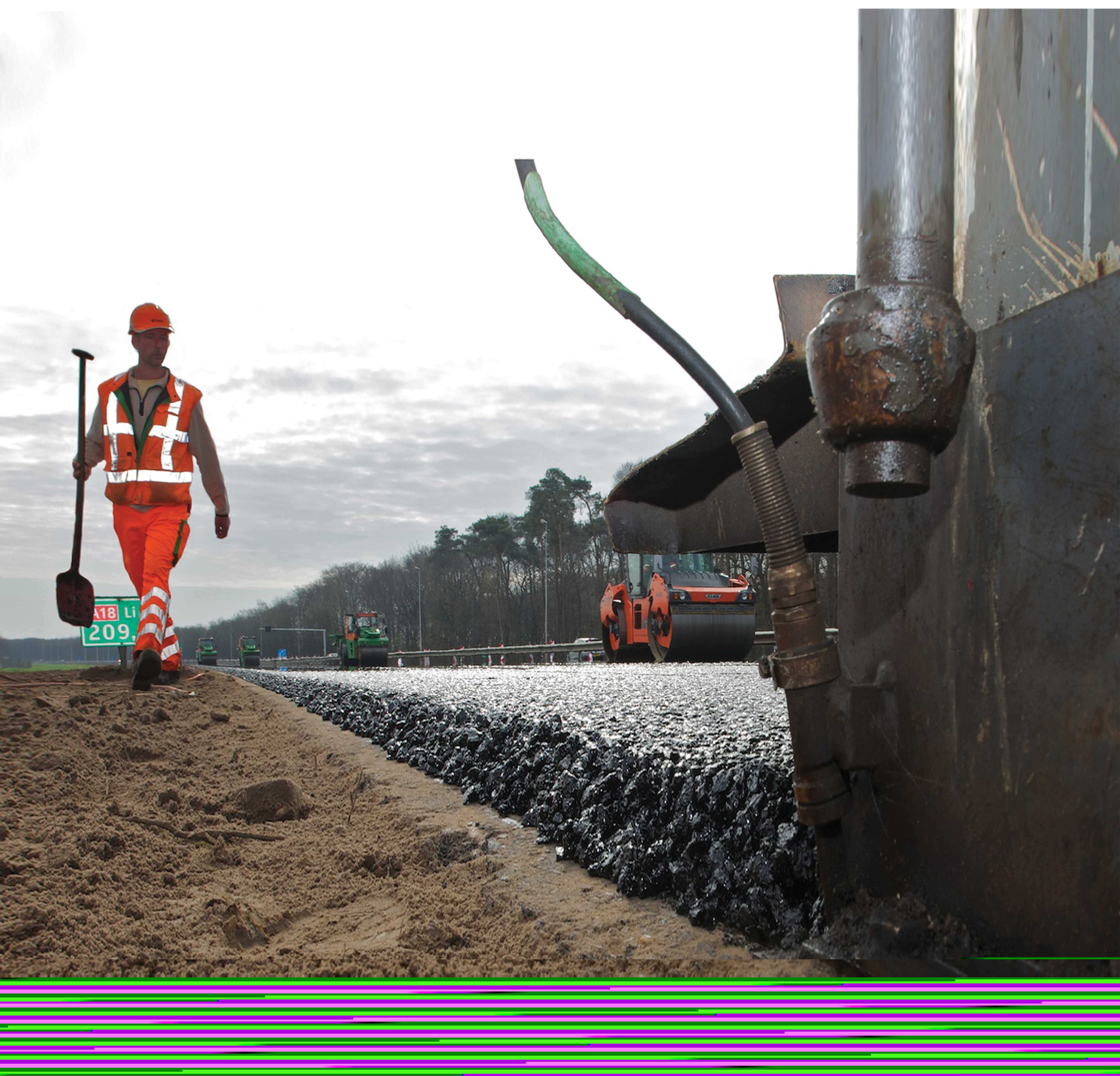
The introduction of warm asphalt technologies has been slower in Europe than in the US, although a 500m trial section of the A18 in the Netherlands has now been paved with the material
A survey carried out jointly by the National Asphalt Paving Association (NAPA) and the Federal Highway Association (FHWA) shows that asphalt recycling and energy-saving technologies are in increasing use in the US
The increasing adoption of new construction practices in the asphalt pavement industry has saved more than US$2.2 billion during the 2011 paving season through the use of recycled materials and energy-saving warm-mix technologies.According to a survey conducted by the
“Asphalt pavements are the sustainable option for paving our nations’ roads and highways. With warm mix, we can use less energy to produce high-quality pavements, and RAP and RAS allow us reuse liquid asphalt, saving costs and preserving natural resources,” said John Keating, NAPA 2013 chairman, president and COO East of Oldcastle Materials. “While use of these technologies has increased dramatically, there is room to do more, and the asphalt pavement industry is ready to reach even higher levels of sustainability in road construction.”
The use of RAP and RAS during the 2011 paving season saved some $2.2 billion. When reclaimed asphalt pavement and shingles are reprocessed into new pavement mixtures, the liquid asphalt binder in the recycled material is reactivated, reducing the need for asphalt binder. Using reclaimed materials also reduces demands on aggregate resources. Warm-mix asphalt technologies allow asphalt pavements to be produced at lower temperatures, reducing energy consumption and lowering emissions during production and paving.
“The asphalt pavement industry has a long history of adapting new technologies and innovations to make a better product,” said NAPA president Mike Acott. “This survey reflects that and demonstrates how asphalt producers are at the forefront of ensuring that our roads are built in an economical and sustainable manner.”
It is clear that the use of RAP and warm asphalt has continued to increase in the US by looking at data for the 2009 and 2010 construction seasons. In 2011, RAP usage reached 60.2 million tonnes, a 7% increase from 2010 and a 19% increase from 2009. More than 99% of asphalt pavement reclaimed from roads went back into new pavements. In the survey, 98% of producers reported using RAP in their mixes for new construction, pavement preservation, rehabilitation, and other projects.
RAS usage also continued to climb, increasing to 1.2 million tons in 2011 — an 8% increase over 2010, and a 52.5% increase since 2009. Since 2009, RAS usage has been reported in 36 states. RAS includes both manufacturers’ scrap shingles and post-consumer roofing shingles.
In 2010, FHWA made warm-mix asphalt part of its Every Day Counts initiative to speed the deployment of technologies that can improve highway projects’ quality, sustainability, and safety. In 2011, total WMA tonnage in the US was estimated at about 62.2 million tonnes, a 67% increase from 2010 and a nearly 309% increase since 2009. Almost all WMA in the US was produced using foaming, injecting a small amount of water into the mix. Warm-mix additive technologies accounted for just over 4% of the market, with this technology having first been demonstrated in the US in 2004.
“Warm mix brings with it so many benefits, reduced energy usage, better compaction in a wider range of temperatures, and more pleasant working conditions. It is fantastic to see how quickly it’s been adopted in such a short period of time,” Acott said.
The survey was based on results from 203 companies with 1,091 plants in 49 states and Puerto Rico. It also included data from 32 State Asphalt Pavement Associations, were used to calculate industry estimates for total tonnage. A slight variation from the previously reported 2010 results is due to changes in survey design to ensure greater accuracy.
For the European market, the use of RAP in a project can assist with achieving sustainability targets. Its use has so far been comparatively limited but this is expected to change, particularly as the cost savings are beneficial at a time when budgets are particularly tight.
But the positive response to warm asphalt in the US is markedly different from Europe, where the paving industry is still comparatively reluctant to use this technology and the introduction of warm mix has been comparatively slow. It is not immediately clear what the reason for this slow uptake of warm asphalt systems could be in Europe, even though much of the technology is home-grown. Specifiers in many European countries are conservative and may not wish to change direction until more data is available, while there may also be some concern over the types of additives warm asphalt requires and the implications these have further down the line.
Using warm asphalt also requires operating changes, with an increased focus on compaction operations and a greater prominence for truck scheduling to reduce the time between a batch being produced and it being tipped into the paver. However there have been some key trials in Europe using warm asphalt and this could herald wider use of the technology in the future.