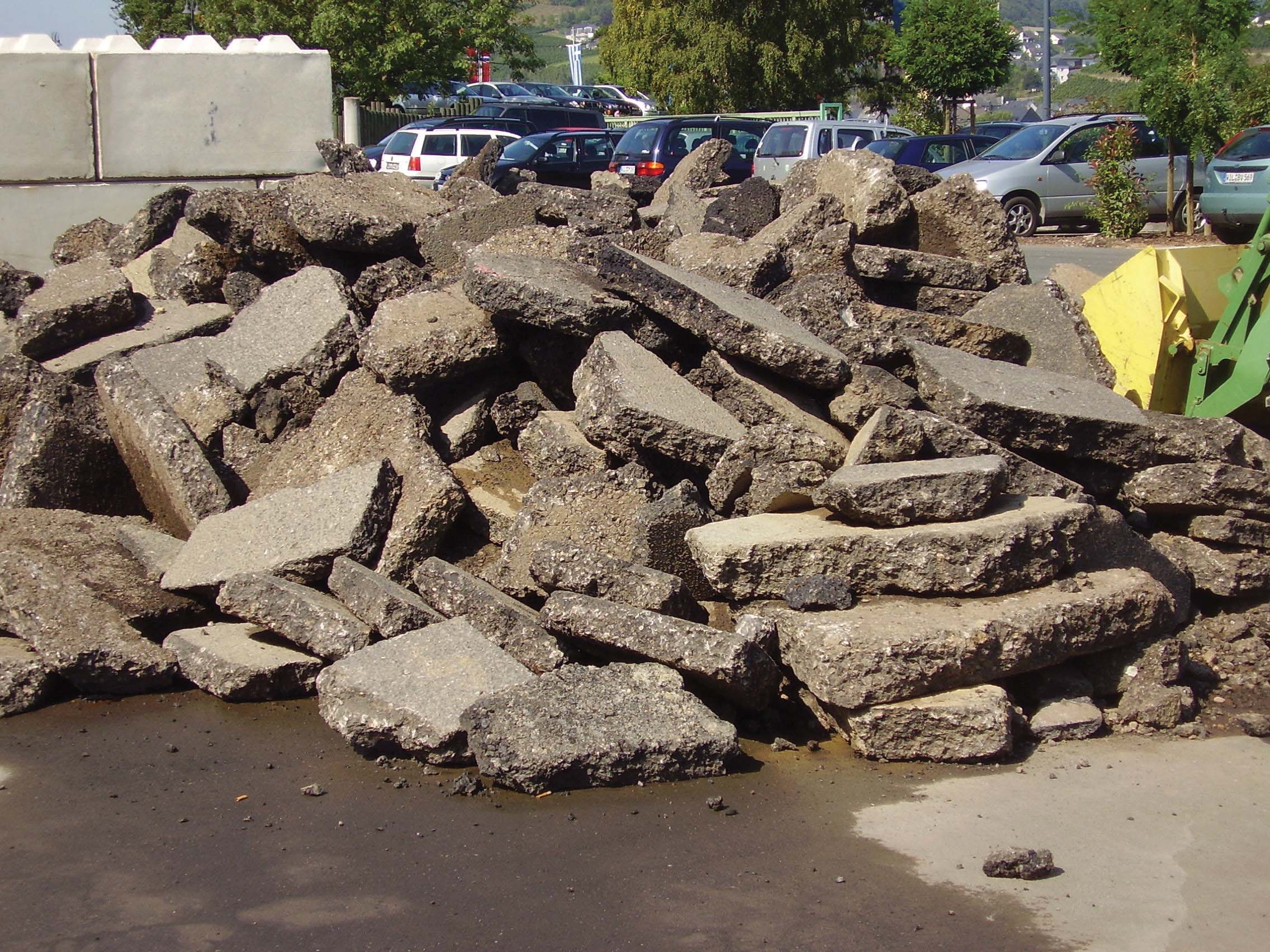
Studies show the asphalt sector has options for materials use that can lower costs and emissions, as well as increasing the use of recycling
One study in the UK led by the Carbon Trust and
However, the trial found that the alternative is able to bond road materials just as effectively at lower temperatures, meaning that it uses less energy. This has led the project team to put together a set of specifications for its use. If the low temperature asphalt market grows to account for 21% of the UK's total asphalt market over the next 10 years, it could save the UK an estimated €55.66 million and approximately 260,000tonnes of CO2 during the manufacturing process.
A survey by the
Information on other recycled materials was also obtained. The most commonly used materials in asphalt mixtures were blast furnace slag, steel slag, and ground tyre rubber. Meanwhile the total tonnage of WMA in the US is estimated at 86.7 million tonnes in 2012. This was a 26% increase over the previous year’s tonnage and in 2012 WMA represented some 24% of the total asphalt mixture market. Plant foaming is used most often in producing WMA, with more than 88% of the market.
In addition, another study in the US has shown that using recycled materials and by-products in pavements is increasingly popular, particularly for hot-mix asphalt (HMA). Reclaimed asphalt pavement (RAP) can contain high-quality, well-graded aggregates that are coated with asphalt cement but may include steel slag, a by-product of steel making. One approach is to incorporate large quantities of RAP into unbound aggregate base and sub-base applications for highway construction.
But steel slag is an expansive aggregate often added when high frictional properties are required, as in HMA surface courses, when good-quality aggregate is scarce. And steel slag may contain free lime (CaO) and magnesia (MgO), which can react with water and cause expansion. Volume changes of up to 10% or more have been attributed to hydration of the calcium and magnesium oxides in the recycled steel slag aggregate base course, caused by water seeping into the pavement base layer. The amount of expansion depends on the origin of the slag, the grain size and gradation, the hydration of UN-slaked lime and magnesia, and the age of the stockpile.
The Illinois Center for Transportation analysed research state highway agency practices. The findings indicated that pavement structures use RAP successfully as a granular base or sub-base material with performance comparable to a crushed stone base. The analysis also revealed that in blending processed RAP materials with virgin aggregates, proper bearing strengths have to be attained. This is because the RAP bearing capacity is usually less than that of conventional granular aggregate bases. As the virgin aggregate content increases, the dry density and strength properties increase.
Steel slag aggregates have good frictional properties, high stability, and good durability, with resistance to stripping and rutting and can perform well as base material. The conventional way to control expansion is to weather the steel slag aggregates in stockpiles until the potentially expansive systems stabilise. The length of time for stocking depends on the local temperature and rainfall and on the degree of air moisture saturation and may range from 3-12 months but after curing, steel slag can serve as a valuable secondary aggregate.
Tests were carried out in laboratory conditions on 17 Illinois RAP materials and virgin aggregates to determine expansive characteristics. Some steel slag aggregates showed a potential for expansion of up to 6.2% and the lower density RAP materials often exhibited more initial settlement or contraction before any kind of expansion. A clear conclusion from the tests was that RAP materials with slag aggregate that was partly coated with asphalt had much lower tendencies to expand than the virgin steel slag aggregates.
Illinois has used steel slag only in HMA surface mixes and never has allowed steel slag or RAP containing steel slag in any other layer of the pavement structure because of concerns about expansion. But the results of this research led to steel slag RAP being allowed in all levels of the HMA mixes, wherever normal RAP is used for aggregate applications.
• Bureau of Materials and Physical Research,
• Department of Civil and Environmental Engineering, University of Illinois at Urbana–Champaign.