Carlos Jofré, technical director of the Spanish Institute of Cement and its Applications (IECA), introduces, on behalf of EUPAVE*, a sustainable technique to rehabilitate fatigued pavements Recycling of pavements is a technique whereby an existing degraded pavement is modified and transformed into a homogeneous structure that can support the traffic requirements. More specifically, it involves reusing the materials from the existing pavement for the construction of a new layer, including the pulverisation o
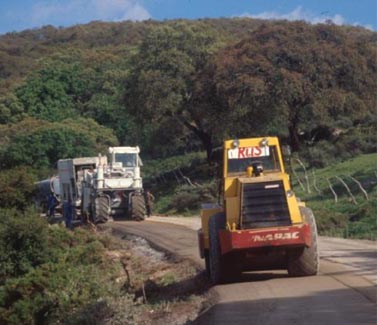
Compaction of a recycled pavement
RSS
More specifically, it involves reusing the materials from the existing pavement for the construction of a new layer, including the pulverisation of the existing pavement up to a certain depth; addition of a binder (cement and/or bituminous emulsion), water (for hydration, mixing and compaction), and the addition of aggregates if necessary (for grading correction or other purposes) and admixtures.
Mix design is based on the results of performance tests on trial mixes. The homogeneous mixture is spread, compacted and cured appropriately, resulting in a base or a layer with a greater structural contribution to a new pavement.
A sealing coat is then applied on the recycled layer to protect it against traffic during the works, with one or two layers of asphalt concrete later applied to ensure the functionality and bearing capacity of the pavement.
In comparison with the conventional technique of overlaying, in situ recycling presents many advantages which make it a much more sustainable option.
These include:
These advantages largely exceed the few drawbacks of the technique, which include, for example, less homogeneity than in a new mixture; possible appearance of longitudinal cracks if adjacent strips are not correctly bonded, and longer rehabilitation time than that required by a simple overlay with bituminous mixtures, where no milling is necessary.
On site recycling of pavements with cement allows the rehabilitation of worn or damaged pavements and their adaptation to support the traffic requirements. If pavements show high deflections, then special studies must be carried out to calculate the required overlay thickness. Cement bound recycling allows a homogeneous and stable layer of an improved thickness to be obtained, with mechanical characteristics similar to those of a soil/cement or cement-bound base.
Thus, with cement bound recycling the bearing capacity is substantially increased and, conversely, pavement deflections and sub-grade stresses and strains are greatly decreased. Moreover, existing ruts can be appropriately corrected if the thickness of the bound layer is increased.
Recycling equipment is currently available that can satisfactorily treat up to 35cm of the existing pavement in a single pass. In most cases, the capacity of the compaction equipment limits the thickness treated.
On the other hand, the target thickness of cement recycled layers should not be less than about 20cm, to avoid the presence of zones with a reduced thickness that could result in a premature fatigue failure.
The criterion for ascertaining the feasibility of recycling a pavement is to identify whether its fatigue comes mainly from the poor quality of the pavement itself (for example, insufficient thickness, or granular layers contaminated with clay, de-bonded bituminous layers) or from problems related to the sub-grade. In the former case, recycling with cement is generally a better option.
A number of Road Administrations (Spain, Belgium, France and the United Kingdom) have recently published specifications or guidelines on these topics.
Good results have been obtained with recycled materials with a design compressive strength not less than 2.5 MPa at seven days. However, some circumstances may require higher strengths, for example to provide resistance to freeze/thaw.
In principle, all types of cement can be used for recycling. However, those that will perform best are those with a content of active additions to increase the setting and workability time.
Based on both laboratory results and experience with cement recycled pavements, it can be concluded that, in many cases, it is possible to recycle with cement without wholly or partially removing the existing bituminous layers.
There are no problems with using cement-recycled layers on high traffic roads, provided they are covered by an adequate thickness of bituminous mix. This is confirmed by the results obtained from roads with a high volume of commercial vehicles, and it should be remembered that the material obtained after recycling with cement is similar to soil cement or a cement-treated base allowed for all traffic categories.
Many countries already have extensive experience in recycling with cement. Available results indicate that the process is satisfactory for low traffic roads/main highways with a high volume of commercial vehicles, and airports.
Spain is one of the countries where this technique is commonly used. In some regions, in situ recycling is the preferred option for rehabilitating existing pavements. Some 1.25 million m² of pavements have been recycled annually over recent years.
One of the most important road works performed in Spain, both in terms of rehabilitated length and volume of commercial traffic, was the recycling of the N-630 National Highway in the province of Cáceres, close to the Portuguese border. Average daily traffic varied between 4,000 and 7,000, with a proportion of trucks of between 18 and 29%.
Existing pavements were composed of asphalt layers on unbound granular materials. They were very distressed, with deflections in the central part between 110- 260 (1/100) mm, and totally broken in the outer strips. There were several causes for this bad condition, including very thin and un-bonded overlays, plastic granular materials and bad drainage, etc.
Depending on the bearing capacity of the sub-grade, the existing pavement was recycled to a depth of between 25 and 30cm. The resulting cement-bound layer was then covered with 10 cm of asphalt concrete.
According to Spanish specifications, between 20 and 25cm of asphalt concrete would have been required for an overlay solution.
Consequently, the recycling approach achieved an economy of more than 300kg of virgin aggregates per sq m.
5% of cement was added in situ to the existing pavement during recycling, in order to obtain a cement-bound material with a compressive strength at 28 days of 3.5 MPa, and a compressive strength at 90 days of between 5 and 5.5 MPa.
Two recyclers, each with a working width of 2m, were used in parallel in order to mill half the width of the carriageway in a single pass. Average output varied between 3.5 and 4m/min. The half-width recycled in the morning was open to traffic in the afternoon, when the remaining half-width was in turn recycled.
Results were very satisfactory, deflections being reduced to one third of the original values. The average compressive strength at 180 days, measured on cores, varied between 4.2-10.4 MPa, depending on the heterogeneity of the existing pavement, but always attaining good values.
Some 36km of pavement were recycled between June and September, 1995. The resulting pavement is still in good condition.
Some 100,000 tonnes of virgin aggregates were spared through the use of recycling rather than conventional overlay. This is clear evidence of the sustainability of this solution. n
*EUPAVE, the European Concrete Paving Association was formed in 2007 with the objective "to promote all cement and concrete products to the transport infrastructure." (www.eupave.eu)
This article is extracted from the2462 IRF Bulletin Special Edition for Europe, to be published shortly.
Carlos Jofré, technical director of the Spanish Institute of Cement and its Applications (IECA), introduces, on behalf of EUPAVE*, a sustainable technique to rehabilitate fatigued pavements
Recycling of pavements is a technique whereby an existing degraded pavement is modified and transformed into a homogeneous structure that can support the traffic requirements.More specifically, it involves reusing the materials from the existing pavement for the construction of a new layer, including the pulverisation of the existing pavement up to a certain depth; addition of a binder (cement and/or bituminous emulsion), water (for hydration, mixing and compaction), and the addition of aggregates if necessary (for grading correction or other purposes) and admixtures.
Mix design is based on the results of performance tests on trial mixes. The homogeneous mixture is spread, compacted and cured appropriately, resulting in a base or a layer with a greater structural contribution to a new pavement.
A sealing coat is then applied on the recycled layer to protect it against traffic during the works, with one or two layers of asphalt concrete later applied to ensure the functionality and bearing capacity of the pavement.
In comparison with the conventional technique of overlaying, in situ recycling presents many advantages which make it a much more sustainable option.
These include:
- Re-use of the aged, polluted or inadequate materials of the existing pavement.
- Homogenisation of the pavement, both in strength and in geometry.
- Reduction in waste and extraction of aggregates from quarries or pits, with the associated environmental advantages.
- The possibility of rehabilitating individual lanes of roads with two or more lanes, where deterioration is frequently restricted to those lanes supporting the heaviest traffic.
- Decrease in nuisance caused by conventional repair work traffic.
- Fewer possibilities of deteriorating the adjacent network of secondary roads, due to the reduced volume of new materials to be transported.
- Lower costs of rehabilitation of worn pavements.
- Maintenance of the surface to a level that does not require the raising of hard shoulders and curbs, and which will not reduce clearance under bridges.
- Opportunities for simultaneously widening the existing road, a frequent situation when upgrading a road. The construction of narrow wedges often associated with widening can be avoided.
These advantages largely exceed the few drawbacks of the technique, which include, for example, less homogeneity than in a new mixture; possible appearance of longitudinal cracks if adjacent strips are not correctly bonded, and longer rehabilitation time than that required by a simple overlay with bituminous mixtures, where no milling is necessary.
On site recycling of pavements with cement allows the rehabilitation of worn or damaged pavements and their adaptation to support the traffic requirements. If pavements show high deflections, then special studies must be carried out to calculate the required overlay thickness. Cement bound recycling allows a homogeneous and stable layer of an improved thickness to be obtained, with mechanical characteristics similar to those of a soil/cement or cement-bound base.
Thus, with cement bound recycling the bearing capacity is substantially increased and, conversely, pavement deflections and sub-grade stresses and strains are greatly decreased. Moreover, existing ruts can be appropriately corrected if the thickness of the bound layer is increased.
Recycling equipment is currently available that can satisfactorily treat up to 35cm of the existing pavement in a single pass. In most cases, the capacity of the compaction equipment limits the thickness treated.
On the other hand, the target thickness of cement recycled layers should not be less than about 20cm, to avoid the presence of zones with a reduced thickness that could result in a premature fatigue failure.
The criterion for ascertaining the feasibility of recycling a pavement is to identify whether its fatigue comes mainly from the poor quality of the pavement itself (for example, insufficient thickness, or granular layers contaminated with clay, de-bonded bituminous layers) or from problems related to the sub-grade. In the former case, recycling with cement is generally a better option.
A number of Road Administrations (Spain, Belgium, France and the United Kingdom) have recently published specifications or guidelines on these topics.
Good results have been obtained with recycled materials with a design compressive strength not less than 2.5 MPa at seven days. However, some circumstances may require higher strengths, for example to provide resistance to freeze/thaw.
In principle, all types of cement can be used for recycling. However, those that will perform best are those with a content of active additions to increase the setting and workability time.
Based on both laboratory results and experience with cement recycled pavements, it can be concluded that, in many cases, it is possible to recycle with cement without wholly or partially removing the existing bituminous layers.
There are no problems with using cement-recycled layers on high traffic roads, provided they are covered by an adequate thickness of bituminous mix. This is confirmed by the results obtained from roads with a high volume of commercial vehicles, and it should be remembered that the material obtained after recycling with cement is similar to soil cement or a cement-treated base allowed for all traffic categories.
Many countries already have extensive experience in recycling with cement. Available results indicate that the process is satisfactory for low traffic roads/main highways with a high volume of commercial vehicles, and airports.
Spain is one of the countries where this technique is commonly used. In some regions, in situ recycling is the preferred option for rehabilitating existing pavements. Some 1.25 million m² of pavements have been recycled annually over recent years.
One of the most important road works performed in Spain, both in terms of rehabilitated length and volume of commercial traffic, was the recycling of the N-630 National Highway in the province of Cáceres, close to the Portuguese border. Average daily traffic varied between 4,000 and 7,000, with a proportion of trucks of between 18 and 29%.
Existing pavements were composed of asphalt layers on unbound granular materials. They were very distressed, with deflections in the central part between 110- 260 (1/100) mm, and totally broken in the outer strips. There were several causes for this bad condition, including very thin and un-bonded overlays, plastic granular materials and bad drainage, etc.
Depending on the bearing capacity of the sub-grade, the existing pavement was recycled to a depth of between 25 and 30cm. The resulting cement-bound layer was then covered with 10 cm of asphalt concrete.
According to Spanish specifications, between 20 and 25cm of asphalt concrete would have been required for an overlay solution.
Consequently, the recycling approach achieved an economy of more than 300kg of virgin aggregates per sq m.
5% of cement was added in situ to the existing pavement during recycling, in order to obtain a cement-bound material with a compressive strength at 28 days of 3.5 MPa, and a compressive strength at 90 days of between 5 and 5.5 MPa.
Two recyclers, each with a working width of 2m, were used in parallel in order to mill half the width of the carriageway in a single pass. Average output varied between 3.5 and 4m/min. The half-width recycled in the morning was open to traffic in the afternoon, when the remaining half-width was in turn recycled.
Results were very satisfactory, deflections being reduced to one third of the original values. The average compressive strength at 180 days, measured on cores, varied between 4.2-10.4 MPa, depending on the heterogeneity of the existing pavement, but always attaining good values.
Some 36km of pavement were recycled between June and September, 1995. The resulting pavement is still in good condition.
Some 100,000 tonnes of virgin aggregates were spared through the use of recycling rather than conventional overlay. This is clear evidence of the sustainability of this solution. n
*EUPAVE, the European Concrete Paving Association was formed in 2007 with the objective "to promote all cement and concrete products to the transport infrastructure." (www.eupave.eu)
This article is extracted from the