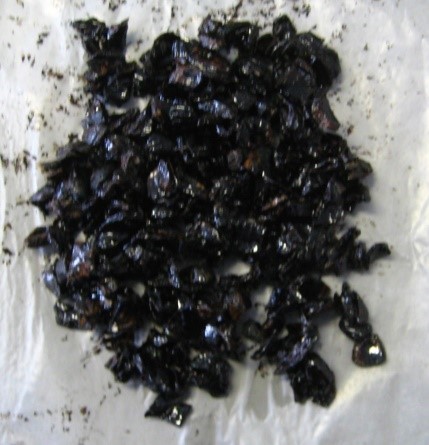
This document discusses how anti-stripping agents can eliminate the possibility of some instabilities in asphalt, such as crumbling and the formation of holes.
Many developments in the past 50 years have improved the performances of bituminous mixtures and allowed the recycling of more materials coming from the demolition of old pavements. This, happily, leads to a reduction of environmental impact through less use of non-renewable first-use raw material.
Increase asphalt concrete performances has often focused on the use of modification polymers, both for bitumen - PMB, Polymer Modified Bitumen – both for mixtures - PMA, Polymer Modified Asphalt. What is often unconsidered is the importance of bitumen-aggregate adhesion which is independent from any polymer modification performed.
Perfect adhesion between the binder and the stone elements prevents water from filtering between the two materials, causing premature aging of the bituminous mixture and leading to the formation of instabilities that decrease the pavement’s performances.
Better adhesion between aggregates and bitumen can be ensured through the usage of anti-stripping agents.
The deteriorations that characterise road pavements are multiple and each one has well-defined causes attributable to the bituminous mixture made and/or to the laying technique and/or to the design and/or to the simple end of useful life.
One of the main triggers of pavement deterioration is the weakening or the detachment of the bitumen film adhering to the surface of the aggregate (stripping). In detail, the factors that affect stripping [1] are:
There has been a lot of research and published case histories regarding stripping and the use of anti-stripping agents.
Adhesion types
- chemical/physical characteristics of the materials used (bitumen and aggregates);
- characteristics of the asphalt concrete, with particular reference to the aggregates and the type of mixture produced (dense graded, porous, SMA, etc.);
- production methodology, hot (HMA), warm (WMA), with the possible use of water (salts, zeolites, wet sands, etc.);
- conditions of use of the pavement such as environmental ones, the loads, the de-icing method, etc..
- As soon as the bitumen film separates, the pavement immediately starts to deteriorate. Typical deteriorations caused by this stripping are:
- surface crumbling, further intensified if bitumen content was less than optimal;
- disaggregation and pothole formation;
- cracking and rutting.
The adhesion of bituminous binders involves physical properties of different origin. The adhesion is influenced by the characteristics of both the bitumen (hydrophobic material) and the aggregate used in the mixture (basically hydrophilic material).
Other factors are the environmental conditions (humidity and temperature), surface characteristics of the pavement (roughness, porosity and coating) and vehicular movements upon the pavement.
Adhesion can be defined generally as the molecular force of attraction between two bodies of different nature in contact with each other. In the context of the asphalt concrete, the contact is liquid (bitumen) and solid (aggregates). With the mixing between aggregates with bitumen, the latter covers the aggregates [2]. That is to say, the aggregates are made "wet" by the binder³.
The bituminous binder creates a superficial film around the aggregate in order to obtain a hydrophobic surface, actually impermeable to the particles of water (figure 1). The main theories of adhesion [1,4,5] developed over the years have been: chemical adhesion theory: charges of equal sign repel, therefore the aggregates have compatibility problems with the bitumen (acid) as their negative charge increases; molecular orientation theory: the contact between binder and aggregates is affected by the orientation of the bitumen molecules that are organised to satisfy the demand for energy of the aggregates, influencing the adhesion resistance; mechanical theory: the adhesion is affected by the surface texture, by the type of coverage, by the size of the coverage area and by the size of the stone elements; surface energy theory: the wettability and the coating of the aggregates depends on the surface tension between the binder-binder and binder-aggregates, as well as the viscosity of the bitumen which limits, for example compared to water, the coating of the aggregates.
With reference to the surface energy theory, the last resistances before internal cracking in the binder film (cohesion) are within the binder-aggregate interface (adhesion). Therefore, adhesion and cohesion have a key role in determining the durability of flexible road pavements.
Stripping occurs when the binder has a greater internal cohesion than the adhesion with the aggregate, resulting in the detachment of the bitumen film from the aggregate. Instead, considering the chemical adhesion theory, the molecular interactions in the maltenic fraction of the bitumen have crucial importance that depends on [6]:
- chemical variation of bitumen due to oxidation, exposure to sunlight and contact with de-icing chlorides;
- chemical reactions between acid compounds of the bitumen (negative charges) and those of the aggregates (limestone ones can free positively charged ions, siliceous ones negative charge);
- presence of moisture contained in the aggregates even after heating after the production phase of the asphalt concretes.
Every time there is a separation of the bitumen layer from the stone surface, there is the interposition of water and a direct reduction in performances of the asphalt concrete. Various studies have shown that water-proofing of pavement is the best solution. The situation is guaranteed both through the correct mix design of the laboratory mixtures and through the use of the necessary anti-stripping agents [7].
If it is not possible to alter the nature of the aggregate constituting the bituminous mixtures, the only controllable factor is the bitumen, through the use of anti-stripping agents. Anti-stripping agents are chemical mixtures containing active functional groups that improve the adhesion of the bitumen film on the surface of the aggregates. Mixed with the binder, they lower the surface tension of the bitumen (figures 2 and 3). There are different types of anti-stripping (amino, polyphosphoric or silane). Choosing one over the other depends substantially on the chemical nature of the aggregates used.
Since the bitumen is acidic in nature, we have that:
- polyphosphoric and the silane are used with porphyry, granite, limestone and basalt (in general, with all the types of aggregates);
- amine is used with porphyry, basalt and granite (aggregates with medium and high silica content)
These correspondences are generated by the chemical actions that take place. For example, the amino portion contributes to improving the adhesive properties. Being basic, the amine additives work better with acid aggregates, where the adhesive power is due partially to the action performed by opposite charges.
The additives also contain functional groups that affect dispersion and the peptisation of the constituents of asphaltene type, with consequent changes as regards cohesive forces [2].
Some of the tests mostly used for the verification of the stripping are:
- thin-layer chromatography test;
- patti test;
- ASTM stripping test (ASTM D1664-80 (1985);
- method of test for film stripping (California Test 302 - 2014)
- effect of Water on Bituminous-Coated Aggregate Using Boiling Water (ASTM D3625 - 96 (2005);
- boiling Test (EN 12697-11).
Since there is a close correlation between the sensitivity to moisture and the degradation of its mechanical properties (such as stiffness modulus and resistance to fatigue), other tests are performed to verify the change in the mechanical properties of the bituminous mixture [8]:
- California Swell test (California Test 305);
- immersion-compression test (AASHTO T165);
- wet-dry indirect tensile (ITSR - UNI EN 12697-12).
Verification of the change of the indirect tensile strength (ITSR) is definitely one of the simplest, faster and more used tests.