German firm Wirtgen is retaining its lead in road recycling technologies – Mike Woof writes Tests on cold recycling with a new layer thickness using Wirtgen's sophisticated WR 4200 machine have shown impressive results according to the firm. The road construction and traffic authority Landesbetrieb Mobilität (LBM) Cochem-Koblenz commissioned a pilot project as part of its plan to optimise the cold in-place recycling process (CIR). The aim was to examine the extent to which the layer thickness can be reduced
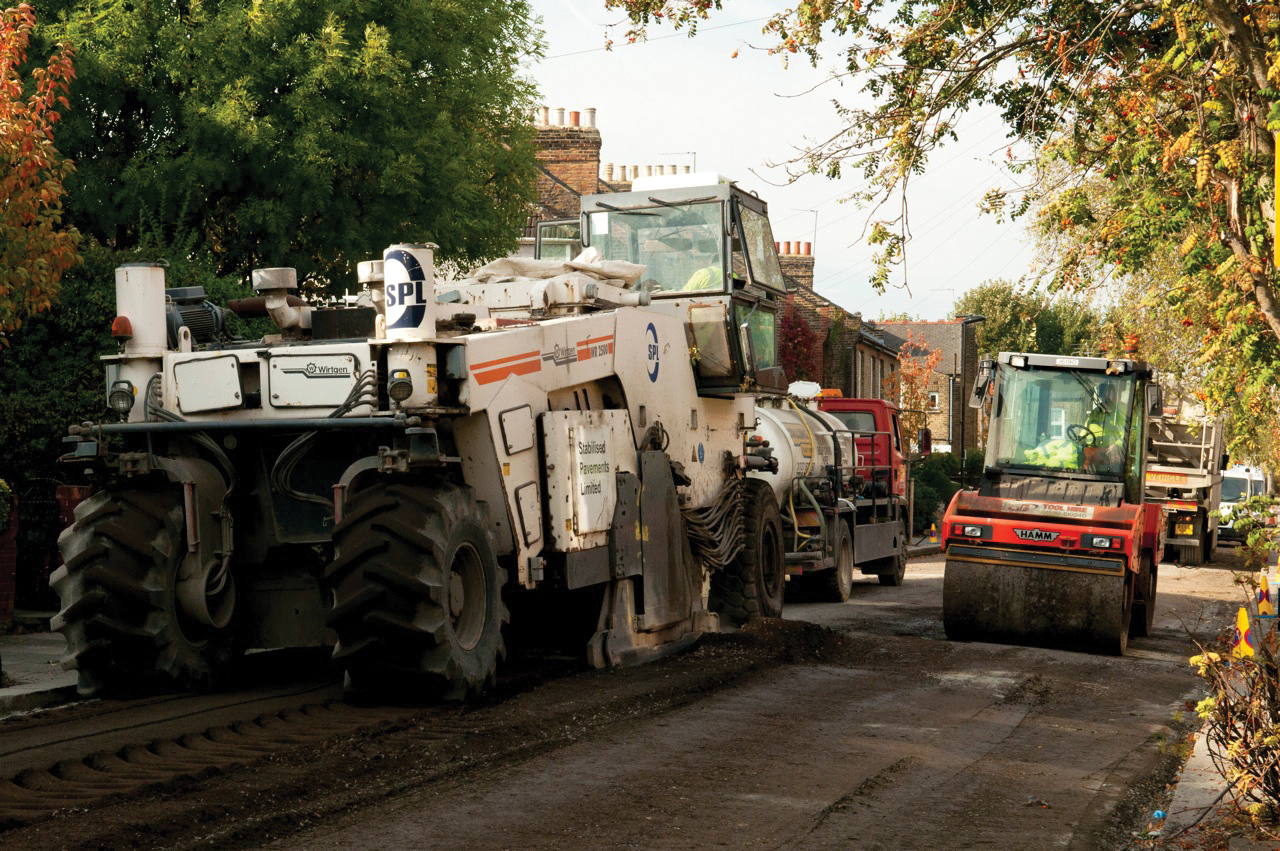
Specialist firm Stabilised Pavements is using its Wirtgen WR 2500 to treat the tar-bound road to a depth of 200mm, while saving an estimated 59tonnes of CO2 emissions
German firm
Cold recycling method is one of the most resource-saving processes in road construction and demand for this technology has climbed sharply in recent years, spurred by rising prices for raw materials and energy. Wirtgen has been developing technologies for the structural rehabilitation of roads for over 20 years and now offers a line-up of nine machines and plants for in-situ or in-plant cold recycling applications.
The WR 4200 is the most powerful machine in Wirtgen's cold recycler fleet and was used on the job site between Weibern and Engeln. The machine was able to mill the 7,200m² road section and process it in a single pass within the space of just three days. The total construction time would normally have been six weeks, but this work only needed three. And unlike the conventional process involving the replacement of the surface and binder course, the cold recycling processes meant that the width of the roadway could be maintained without widening it. Cold recycling saved valuable resources and also saved up to 10% on costs in comparison with ordinary rehabilitation methods. Moreover, construction projects using the two-layer rehabilitation method are eligible for state funding in Germany, while fulfilling all the relevant criteria.
During the construction work, the laboratory sbt implemented an extended quality assurance programme, both on the job site and in the laboratory. All values investigated as part of the check test, both on the job site and in the laboratory, complied with the required specifications and statutory standards. The sbt experts will continue to monitor the project closely over a 10-year period of use and will then pass a judgement on the basis of long-term findings. Wirtgen is optimistic about the outcome though as its projects worldwide have shown that cold recycling is a technically mature and extremely economical process that offers an effective alternative under the right basic conditions.
Meanwhile in UK capital London, Enfield Council has made substantial savings in cost and time and achieved huge environmental benefits on a series of road maintenance projects in the Borough. The council has saved £1.75 million and several weeks work, while reducing traffic disruption and saving an estimated 59tonnes of carbon dioxide emissions. These savings, and the bonus benefit of producing a lower CO2, have been achieved by a decision to reuse the existing material in the eight different roads. The material has been treated, strengthened and recycled in-situ, instead of adopting conventional road reconstruction techniques that are more expensive, slower and more disruptive.
The decision to use in-situ road recycling was influenced by the discovery of tar-bound materials during testing of core samples taken from the eight damaged roads. The council estimated that there was some 2,500tonnes of hazardous tar material in the roads, which would have had to be planed off and taken to a licensed tip about 130km away. The cost of removing the tar-bound material works out at over £100/tonne and would have been around £250,000 in total. The main cost saving was achieved by not having to take the tar-bound cuttings to a licensed tip as hazardous waste.
This is the first local authority in London choosing to partially reconstruct hazardous tar-bound roads by in-situ recycling, instead of using conventional full depth pavement reconstruction techniques with new bituminous materials. Roads built in the UK prior to 1980, or surface dressed prior to the late 1980s may contain tar and programmed maintenance work may involve excavating materials containing tar and disposing of this in landfill, which is both expensive and unsustainable.
According to the Council the cost of conventional reconstruction of the eight tar-bound roads would have been about £2.5 million, just over three and a half times the cost for the in-situ recycling process. Treating the roads in-situ also took about a third of the time needed for traditional reconstruction, considerably minimising disruption to residents and local traffic and saving extended road closure costs.
Cold in-situ recycling helps reduce CO2 emissions, as the technique cuts the need for extraction and transportation of existing in-situ materials to landfill sites. It also reduces the reliance on the production and transportation to site of new materials extracted from natural sources. In-situ recycling is less disruptive to local traffic than conventional reconstruction and for this work the council saved around 300 movements of 20tonne trucks and improved its carbon footprint.
The in-situ recycling process used on the eight Enfield tar-bound roads initially involved the top uncontaminated layer being planed off and disposed of as reusable road cuttings. The underlying damaged sub-base layers of each of the roads were then recycled and stabilised to a depth of 200mm. A layer of cement, blended with pulverised fuel ash, was spread over the surface of the material and the recycling machine was then used to mix the cement and PFA blend to the full 200mm depth, while water was added to produce the required optimum moisture content.
Any excess material was taken off site and mixed with crushed concrete before being used in the Borough’s roads and footways as Type 1 sub-base. The in-situ stabilised and strengthened material was compacted with a roller, reprofiled and rolled again, prior to spraying the surface with a bonding tack coat and gritting so that the road could be opened temporarily for residential traffic. The recycled road was subsequently paved with a new 50mm think surface layer and opened to full traffic.
The mix recipe for the recycled, stabilised and strengthened material was designed and determined from testing and analysing core samples taken from the tar-bound roads. The cement and PFA complement each other as the cement provides an initial gain in strength of the recycled road materials, while the PFA slows hydration and contributes to increasing the strength over time.
The in-situ recycling at Enfield was carried out by the specialist road recycling and stabilisation contractor
For the local council, the technique will allow more roads to be rebuilt using the same funds, as in the past around 10% of its budget has been spent on tar removal. This money can now be used to better purpose for rebuilding more roads overall.