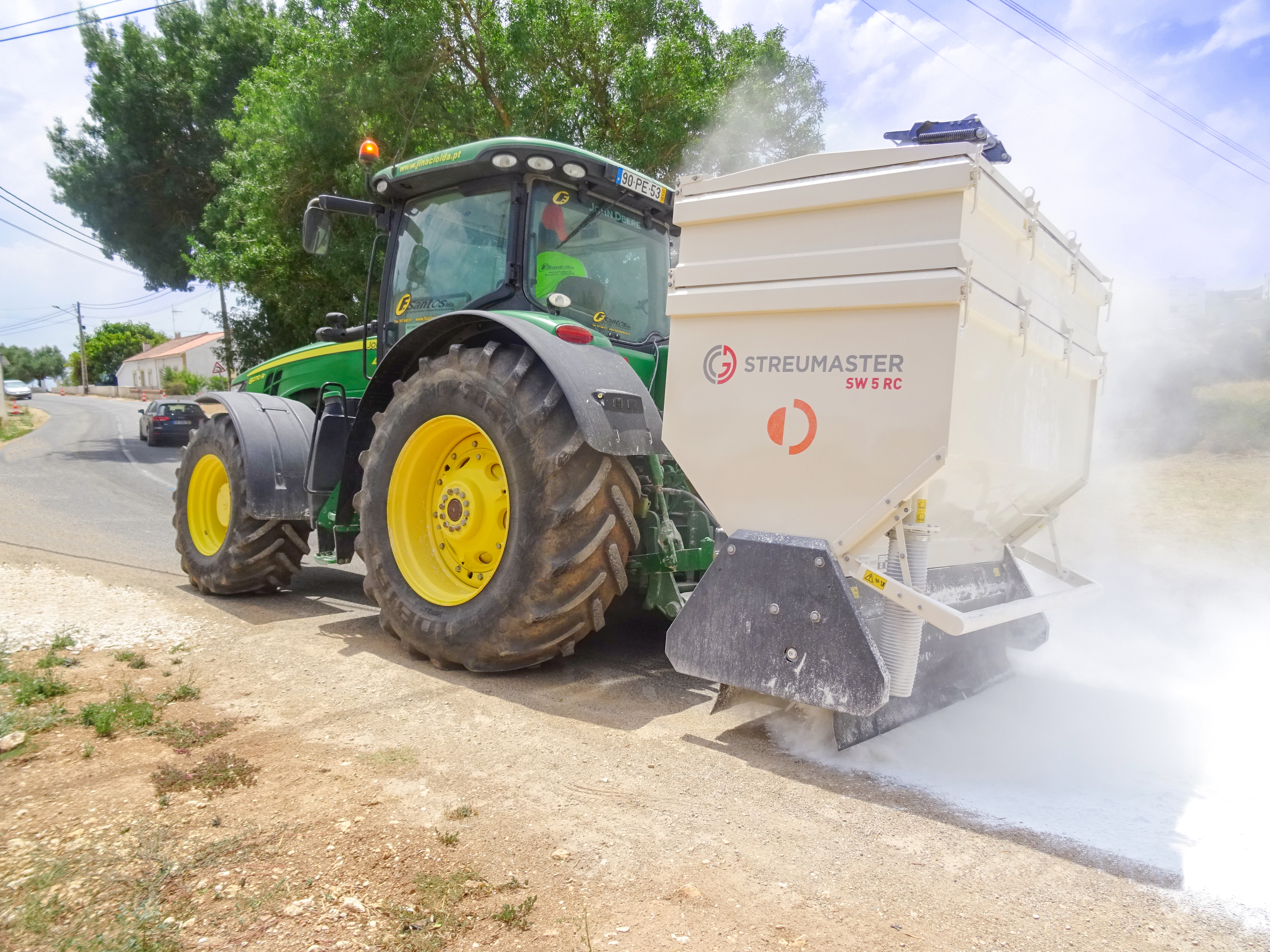
A road rehabilitation job is Portugal has been carried out using the latest cold recycling train technology. Trunk road ER 361 runs through the town of Monsanto, around 100km north of Lisbon and a 2.7km stretch of the route required structural rehabilitation in both directions. The authority awarding the contract, Infrastructuras de Portugal, had planned 12 weeks for the repair works. However, a road construction team from Pragosa used the cold recycling process to complete the job in just four days.
A key machine used for the cold recycling train was the new Wirtgen W 380 CR, which made its debut for Pragosa on this construction site. This unit is capable of recycling the old layers of the road in just one pass. A Vögele paver was then used for the paving work, with several Hamm road rollers then carrying out final compaction.
Time was a key factor in the success of cold in-place recycling for this job. Shortening the duration of the project from 12 weeks to four days was possible as almost no material had to be transported to the project. The actual construction site planning had envisaged that both lanes would be excavated to a depth of 540mm and rehabilitated from scratch. This would have resulted in around 7,500m³ of material being transported from the construction site, and then replaced with new material. Bringing in new material, as well as the associated work, resulted in the planned construction duration of 12 weeks.
However, using cold in-place recycling eliminates the need to replace existing material. By adding lime and foamed bitumen as binding agents and using the existing materials from the old road surface, a high-quality construction material can be produced. The new bitumen-stabilised material (BSM) serves as the new base structure for the road and is fit for traffic again after completion of a construction section.
The width of the lane varied between 2.75m and 3.25m on the construction site. To allow for this variance, the W 380 CR cold recycler was equipped with a milling drum unit with a working width of 3.2m instead of its standard unit with a working width of 3.8m. The firm’s MCS system also made it possible to switch the milling drums on the construction site.
The University of Minho was responsible for designing the mix for the new BSM layer and collecting samples of the existing road structure. In the process, the university determined that the roadbed still had sufficient bearing capacity so a BSM layer plus a new asphalt surface layer represented a long-lasting alternative to the conventional, cost-intensive process of building a new road.
To produce the new BSM layer, 7kg of lime/m2 needed to be added to the mix. The lime was applied directly to the old road surface before the mixing process. A Streumaster SW 5 RC spreading units mounted on a John Deere tractor ensured that the lime was evenly distributed. By carefully discharging the material at the right spreading width, the crew achieved a high degree of spreading accuracy, which kept costs as low.
The W 380 CR then milled 160mm deep through the damaged asphalt surface layer into the binder course. “The working depth of the cold recycler was set to 16cm in order to produce a BSM layer with sufficient bearing capacity,” explained Mike Marshall, Wirtgen recycling expert. After adding only 2.6% foamed bitumen and water, the lime was mixed in directly.
Using the down-cut method, the new road bed was mixed from the existing material consisting of the surface course and parts of the binding agent with the aggregates. The recycling machine delivered productivity and was able to advance at 5m/minute. In the process, the CR produced around 320tonnes of high-quality BSM mix/hour. “Foamed bitumen was selected as the binding agent. This offers numerous benefits in terms of processing capabilities and cost-effectiveness. In addition, cold processing significantly reduces carbon emissions,” explained Marshall.
The adjustable conveyor of the W 380 CR transported the 320tonnes of BSM into the hopper of the Vögele SUPER 1900-3i following behind it. The paver was followed by three Hamm road rollers to complete the construction project. An HD+ 110i tandem roller with a smooth drum was used to first seal and stabilise the paved layer. Two GRW 18 pneumatic tyre rollers were then used for final compaction.
According to Pragosa, it saved around 98% of the carbon emissions compared to the conventional construction method. This was primarily due to the construction material being reused on site. With conventional methods material would have had to be transported to and from this site by truck, around 1,500 separate trips. In addition, there were no landfill costs for disposal or extraction costs for the new material.